The 5-axis machining concept
5 Axis Machine Fundamentals
5-axis machining refers to the use of CNC systems to simultaneously move cutting tools or workpieces along five different axes. These machines allow the cutting tool to approach the part from virtually any direction, resulting in more precise and complex parts.
The five axes of movement are:
- X axis: left and right along the table
- Y axis: forward and backward along the table
- Z axis: up and down perpendicular to the table
- A axis: rotation around the X axis
- B axis: rotation around the Y axis
By incorporating rotations along the A and B axes, 5-axis machines achieve higher levels of precision and allow for the creation of more complex shapes. This added flexibility can reduce setup times, improve surface quality and produce parts with tighter tolerances.
5-Axis Simultaneous Machining
5-axis simultaneous machining is a specific method that involves moving all five axes at the same time during the machining process. Unlike traditional 3-axis or 5-axis indexed machining methods, 5-axis simultaneous machining offers continuous multi-axis motion, resulting in a smooth, continuous cutting path.
This approach allows for even more complex part geometries and tighter tolerances, while always controlling the angular position of the cutting tool relative to the workpiece. Simultaneous 5-axis machining significantly reduces the risk of tool collisions, eliminates the need for multiple setups and allows for shorter, stiffer tools, which reduces vibrations and leads to better surface finishes.
In summary, 5-axis machining offers numerous benefits such as greater precision, flexibility and efficiency. The inclusion of 5-axis simultaneous machining techniques pushes the boundaries even further, allowing manufacturers to produce more complex and intricate parts with higher levels of precision.
5-axis machining processes
Court Processes
5-axis machining involves cutting processes that use multidirectional movements, which allow for greater flexibility and precision. Cutting tools are operated in five axes instead of the traditional three, which includes not only linear movements along the X, Y, and Z axes, but also rotation around the A and B axes. This greater freedom of movement allows complex geometries are machined with more efficiency and precision.
Important aspects of cutting processes in 5-axis machining include:
- Tool path optimization: reduces machining time and improves tool life by avoiding unnecessary movements.
- Continuous cutting: By continuously adjusting the tool orientation, better surface quality can be achieved and tool life can be extended.
- Collision Prevention: Advanced software ensures that the cutting tool and workpiece do not collide, minimizing potential damage to the machine or part being machined.
Milling processes
Milling processes in 5-axis machining centers include several techniques that allow the creation of complex and precise geometries. These processes are often carried out on computer numerical controlled (CNC) machines, which ensure high levels of precision, repeatability and efficiency. Some of the most common milling processes in 5-axis machining include:
- Contour milling : This process involves cutting along the desired geometric path, creating smooth surfaces and reducing the need for post-process finishing.
- Indexed milling : Allows you to position the cutting tool at specific intervals, enabling the machining of complex geometries with high precision.
- 5-axis simultaneous milling : In this process, the cutting tool and the workpiece are moved simultaneously, which allows the milling of complex and detailed parts.
Machining Settings
The complexity of 5-axis machining requires advanced settings to ensure the part is accurately positioned and held during processes. There are several types of configurations commonly used in 5-axis machining centers, including:
- 3+2 axis configuration: This configuration involves positioning the part in a stationary manner while the cutting tool moves along the desired axes. While not a true 5-axis configuration, it offers adequate flexibility for most applications.
- Swivel head configuration: In this configuration, the cutting tool can be rotated around the A and B axes, which allows you to machine a wider range of geometries.
- Trunnion table configuration: This configuration has a rotating table that holds the part, allowing better access to its various surfaces by the cutting tool.
Choosing the correct configuration for a specific machining operation depends on several factors, such as the complexity of the part, the equipment available, and the desired level of precision. Proper configuration selection can greatly impact the quality of the finished product, as well as reduce machining time and resource utilization.
5-axis machining
To truly understand 5-axis machining, we first need to understand what a 5-axis machine tool is. 5-axis machining, as the name suggests, involves adding two rotary axes to the common three linear axes of X, Y, and Z.
The two rotary axes (A, B and C axes) have different movement modes to meet the technical requirements of various products.
Machine tool manufacturers continually strive to develop new motion modes to meet various requirements in the mechanical design of 5-axis machining tools.
In conclusion, there are several types of 5-axis machine tools currently available on the market. Although their mechanical structures vary, the main forms include:
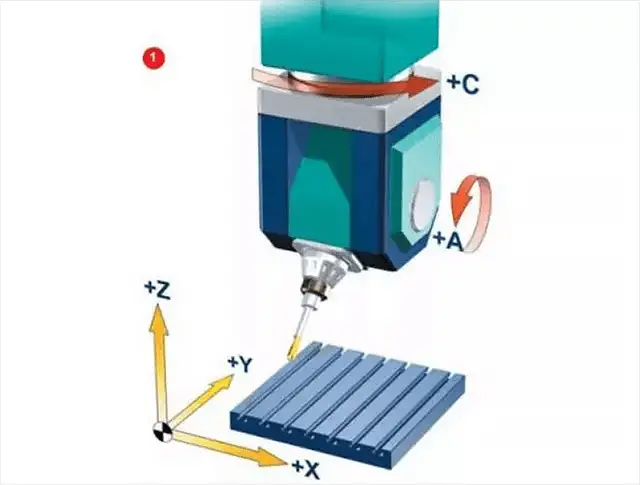
Two rotary coordinates directly control the tool axis direction (double pendulum head shape)
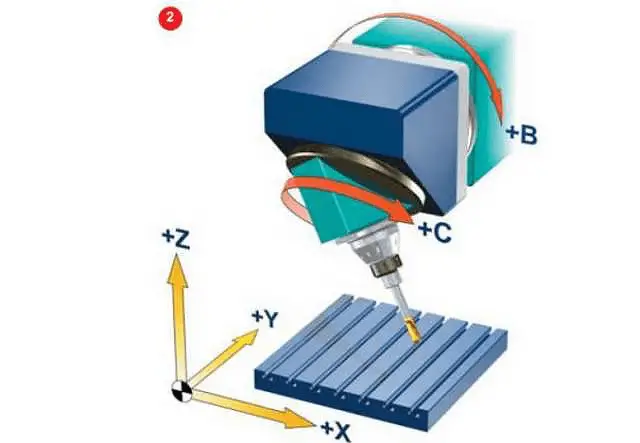
The two coordinate axes are at the top of the tool, but the rotation axis is not perpendicular to the linear axis (Nutate oscillating head shape)
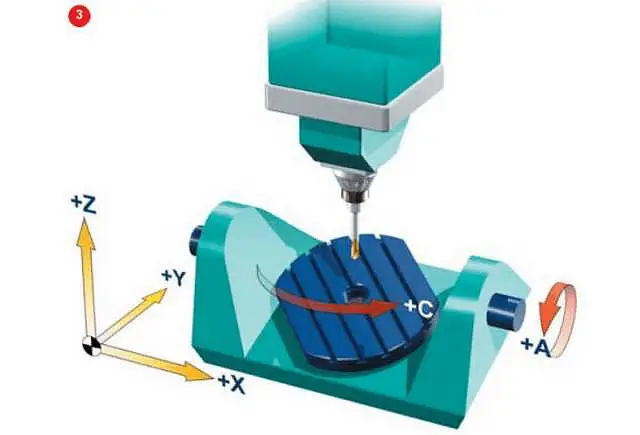
Two rotating coordinates directly control the rotation of space (double turntable format)
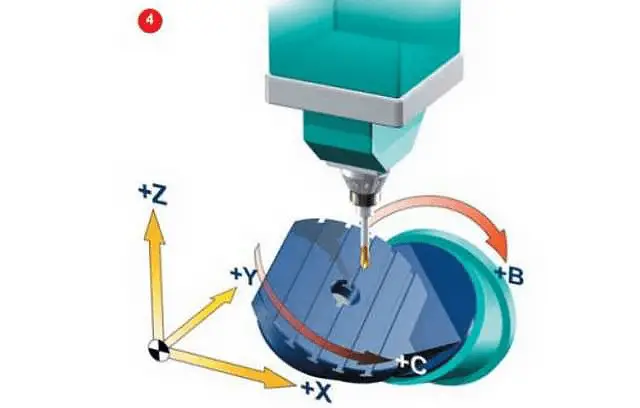
The two coordinate axes are on the work table, but the rotation axis is not perpendicular to the linear axis (Nutate bench shape)
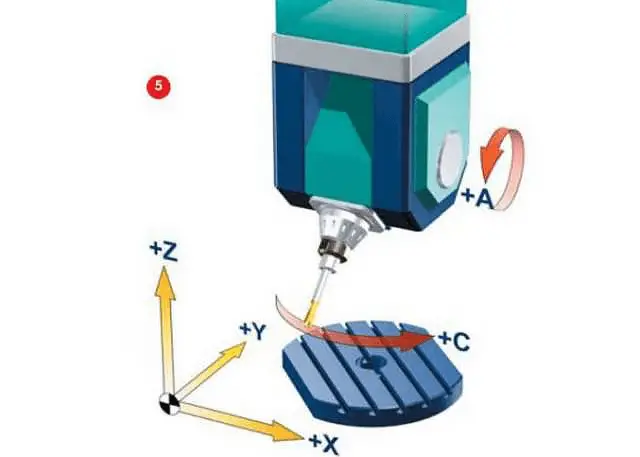
Two rotary coordinates, one acting on the tool and the other acting on the workpiece (one way of turning and one of rotation)
*Terms: If the axis of rotation is not perpendicular to the linear axis, it is considered a “nutated shape” axis.
Having understood 5-axis machine tools, we must now delve into their movements.
However, with such a diverse range of machine tool structures, what unique properties can they exhibit during machining?
Compared with traditional 3-axis machine tools, what are the benefits?
Let us now examine the highlights of the 5-axis machine tool.
Features of 5-axis machine tools
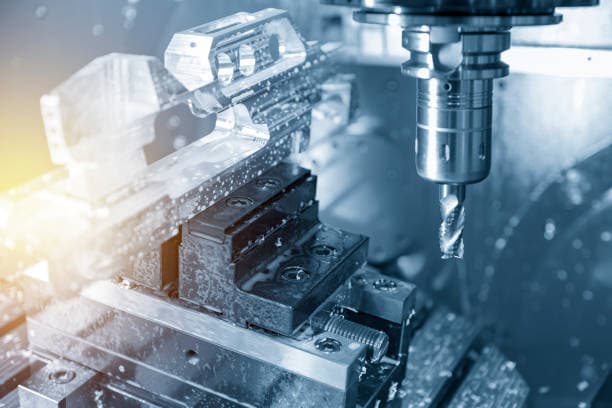
Speaking about the characteristics of 5-axis machine tools, it is important to compare them with traditional 3-axis machines.
3-axis processing equipment is most common in production, and there are various shapes such as vertical, horizontal and gantry.
Common processing methods include end cutting and side cutting with an end mill and profile processing with a ball end mill, among others.
However, regardless of the form or method, a common feature is that the direction of the tool axis remains unchanged during the machining process.
The machine tool can only realize tool movement in the rectangular spatial coordinate system through the interpolation of the three linear axes X, Y and Z.
Therefore, when faced with certain products, the disadvantages of the 3-axis machine tool are exposed, such as low efficiency, poor surface quality and even the inability to process the product.
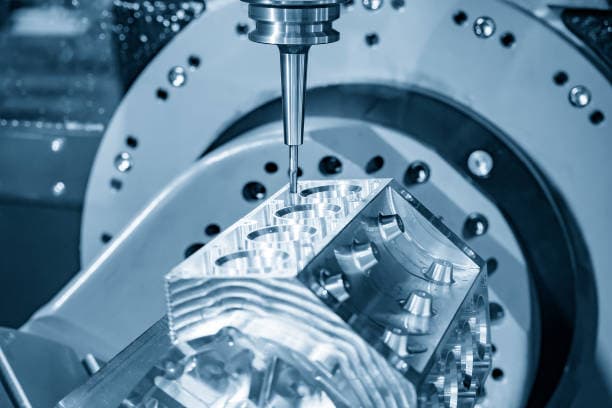
Compared to 3-axis CNC machining equipment, 5-axis machining centers offer the following benefits:
- Maintain the best cutting condition of the tool and improve cutting conditions
As shown in the figure, in the left 3-axis cutting mode, when the cutting tool moves to the tip or edge of the workpiece, the cutting conditions gradually deteriorate.
To maintain the best cutting condition, the table must be rotated.
To fully process an irregular plane, the work table must be rotated several times in different directions.
It can be seen that the five-axis machine tool can also avoid the situation where the linear speed of the ball mill center point is zero, resulting in better surface quality.
- Effectively avoid tool interference
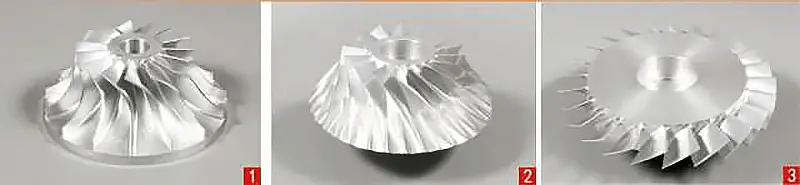
As shown in the figure above, for aerospace field components such as impellers, blades and blisks, 3-axis equipment does not meet the processing requirements due to interference.
5 axis machining tool can meet this requirement.
In addition, the 5-axis machine tool can also use shorter tools for processing, which increases the rigidity of the system, reduces the number of tools required, and eliminates the need for special tools.
For business owners, this translates into cost savings in terms of tooling expenses by using 5-axis machine tools.
- Reduce the number of fixtures and complete five-sided processing in a single fixture
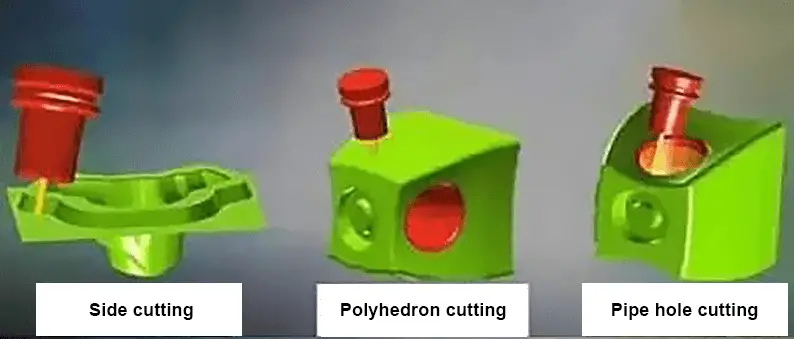
As can be seen from the figure above, the 5-axis machining center can also reduce bench conversion and improve machining accuracy.
In actual processing, only one fixture is required, making it easier to guarantee accuracy.
Furthermore, due to the shortening of the processing chain and the reduction of the number of equipment for the 5-axis machining center, the number of fixtures, workshop area and maintenance costs have also been reduced.
This means you can use fewer attachments, less workshop space and incur lower maintenance costs for more efficient, higher quality processing!
- Improve quality and processing efficiency
As shown in the figure, the 5-axis machine tool can perform cuts through the side edge of the tool, resulting in higher processing efficiency.
- Shorten the production process chain and simplify production management
The full machining capability of the 5-axis CNC machine tool significantly shortens the production process and streamlines production management and planning.
Its advantages become increasingly evident for more complex parts compared to traditional methods with dispersed processes.
- Shorten the new product development cycle
For companies in the aerospace and automotive sectors, new product development often involves complex shapes and high-precision requirements.
In these cases, the use of a 5-axis CNC machining center, with its high flexibility, precision and complete processing capability, can effectively solve the precision and cycle problems in processing complex parts.
This, in turn, significantly shortens the development cycle and improves the success rate in new product development.
It is important to note, however, that 5-axis machines are more complex than their 3-axis counterparts when it comes to tool attitude control, CNC, CAM programming, and post-processing.
Additionally, there are 5-axis true and false questions to consider. The distinction between true and false 5-axis lies in the presence or absence of the RTCP function.
To better understand RTCP and how it is produced and applied, let's delve deeper into the machine tool structure and programming post-processing.
About RTCP
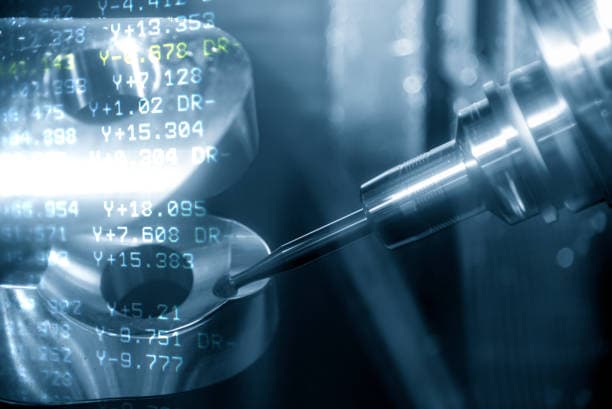
RTCP, which stands for Rotated Tool Center Point, is a crucial aspect of high-quality 5-axis CNC systems. It is also known as tooltip tracking function.
In 5-axis machining, the rotary motion of the tool produces additional motion of the tool tip, which affects the cusp location and the attitude between the tool and the workpiece.
To ensure that the tool tip follows the prescribed trajectory, the CNC system must automatically correct the control point, which often does not coincide with the tool tip.
The same technology can be referred to as TCPM, TCPC or RPCP. These names have a similar meaning to RTCP, the main difference being the way the technology is applied.
RTCP specifically refers to the application of the center point of rotation of the pendulum head to compensate in the structure of the double pendulum head.
On the other hand, functions such as RPCP are mainly used in dual rotary table machines to compensate for the change in linear axis coordinates caused by the rotation of the workpiece.
In essence, these functions aim to keep the center point of the tool and the actual point of contact between the tool and the part surface unchanged.
For the purposes of this article, such techniques will be collectively referred to as RTCP technology.
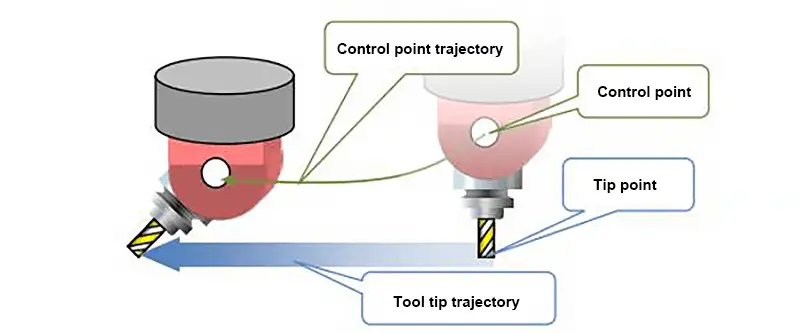
The origin of the RTCP function
Years ago, when five-axis machine tools were becoming popular in the market, the RTCP concept was highly praised by machine tool manufacturers.
At that time, the RTCP function was more of a technology for technology's sake and more of a marketing tool.
However, in reality, the RTCP function is not only a good technology, but also a valuable tool that can bring benefits and create value for customers.
With a machine tool equipped with RTCP technology (also known as a true 5-axis machine tool), operators do not need to carefully align the workpiece with the turntable axis.
Instead, they can simply clamp it and the machine tool will automatically compensate for the offset, which significantly reduces setup time and improves machining accuracy.
Additionally, post-processing is easier because tooltip coordinates and vectors are easily generated.
As mentioned earlier, five-axis CNC machine tools mainly come in the form of double rotating heads, double turntables, or pivoting and rotating frames.
In the following section, we will use a high-tech 5-axis CNC system with dual rotary table as an example to provide a detailed explanation of the RTCP function.
Define the fourth and fifth axes on a 5-axis machine tool:
In the double rotation table structure, the rotation of the fourth axis affects the attitude of the fifth axis, and the fifth axis is the rotational coordinate on the fourth axis.
However, the rotation of the fifth axis does not affect the attitude of the fourth axis.
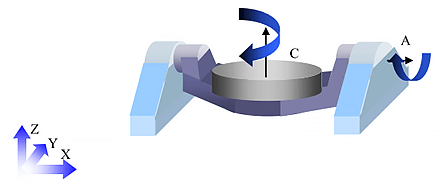
Okay, let's explain after understanding the definition.
As shown in the figure, the fourth axis of the machine tool is called the A axis and the fifth axis is the C axis.
The workpiece is positioned on the C-axis turntable. When the 4th axis, the A-axis, rotates, the attitude of the C-axis will be impacted as it is installed on the A-axis.
When programming the center cut of the tool for the part placed on the rotary table, any change in the rotation coordinate will result in a change in the X, Y and Z coordinates of the linear axis, leading to a relative displacement.
To resolve this displacement, the machine tool must perform compensation, and that is where the RTCP function comes in.
So how does the machine tool compensate for displacement?
To answer this, we first need to analyze the origin of the displacement. As discussed earlier, the change in linear axis coordinate is caused by the change in rotary coordinate. Therefore, it is crucial to analyze the center of rotation of the rotary shaft.
On a machine tool with a double rotary table structure, the C-axis control point, or fifth axis, is normally located at the center of rotation of the machine table.
The fourth axis generally chooses the midpoint of the fourth axis as the control point.
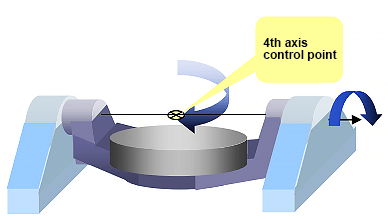
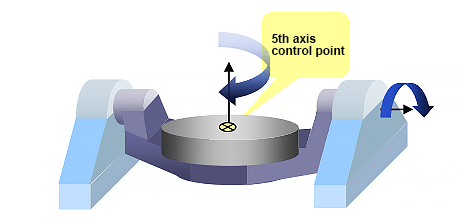
To achieve five-axis control, the CNC system must be aware of the relationship between the fourth and fifth axis control points.
In the initial state, when the A and C axes are at position 0, the control point of the fourth axis is the origin in the rotation coordinate system of the fourth axis, and the control point of the fifth axis is represented by the position vector (U , V, W).
The CNC system also needs to be aware of the distance between the A and C axes.
For double rotary table machine tools, an example can be seen in the attached figure.
It can be seen that for machines with RTCP capability, the control system is designed to always keep the center of the tool in the position specified in the programming. This means that programming is not affected by machine movement.
When programming on the machine, you will not need to consider machine movement or tool length. Simply focus on the relative motion between the tool and the workpiece. The job control system will take care of the rest for you.
For example:
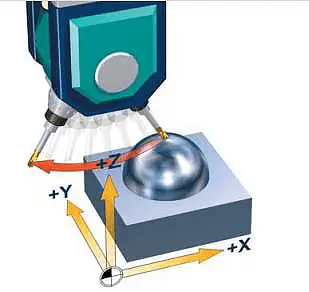
As shown in the figure, when the RTCP function is absent, the control system disregards the tool length.
As a result, the tool rotates around the center of its axis, causing the tip to deviate from its position and become loose.
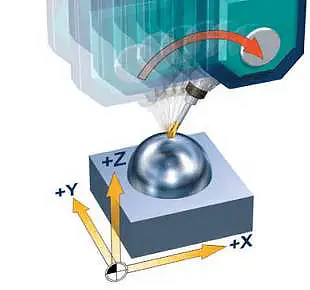
As shown in the figure, when the RTCP function is activated, the control system only adjusts the tool direction, while the tool tip position remains constant.
The necessary offsets along the X, Y and Z axes were automatically calculated.
Regarding the issue of shifting linear axis coordinates in 5-axis machine tools and CNC systems that do not have RTCP, it is important to note that many five-axis machine tools and CNC systems in China are considered “false 5-axis”.
This term refers to machine tools without the RTCP function. It is not determined by appearance or whether the 5-axis is linked, as the false five-axis can still be used for 5-axis linkage.
The main distinction between dummy 5-axis is the absence of a real 5-axis RTCP algorithm, which means that programming for dummy 5-axis must take into account spindle swing length and rotary table position.
This implies that when using dummy five-axis CNC systems and machine tools in programming, it is necessary to utilize CAM programming and post-processing technology to pre-plan the tool path.
If the machine tool or tool is changed for the same part, CAM programming and post-processing must be carried out again.
The 5-axis dummy machine tool must also ensure that the workpiece is positioned at the center of rotation of the worktable during clamping.
This results in a considerable amount of time spent on clamping and alignment for the operator, and accuracy cannot be guaranteed.
Even for index processing, false 5-axis is problematic.
On the other hand, true 5-axis only requires setting up a coordinate system and only one tool calibration to complete the machining process.
The following figure uses the NX post-processing editor settings as an illustration to demonstrate the dummy 5-axis coordinate transformation.
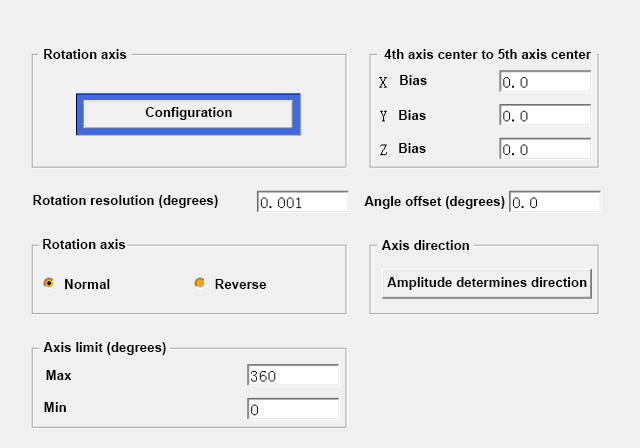
As depicted in the figure, the false axis 5 relies on post-processing technology to compensate for the displacement of the rotary axis to the linear axis coordinate, showing the center position relationship between the fourth and fifth axes of the machine tool.
The CNC programs generated for the X, Y and Z axes include not only the approach points, but also the necessary compensations in these axes.
This method leads to reduced processing accuracy, low efficiency, non-universal programs and high labor costs.
Furthermore, each machine tool has different rotation parameters, requiring a separate post-processing file, causing disruption to production.
False five-axis programming cannot be changed, and manual 5-axis programming is almost impossible.
The lack of RTCP function also limits your ability to use advanced 5-axis derived functions such as compensation.
In conclusion, the choice of 5-axis machine tool is not about true or false, but about the method used to obtain processing results. In terms of cost-benefit, true 5-axis machine tools are a more viable option.
Technologies in 5-axis machining
CNC technology
5-axis CNC machining relies on computer numerical control (CNC) technology, which allows for precise machine movements and production of complex parts. This technology allows 5-axis machines to perform simultaneous movements along five different axes, increasing the flexibility and efficiency of machining processes. CNC technology also reduces human intervention and the need for manual adjustments, resulting in greater repeatability and reduced errors.
Machining precision
One of the main advantages of 5-axis machining is its high machining precision. These machines can achieve tight tolerances, typically ranging from +/- 0.001 inches to +/- 0.0001 inches. This precision ensures parts meet exact specifications, making them suitable for industries that require complex geometries and high-quality finishes, such as aerospace, automotive and medical device manufacturing. Improved accuracy also reduces the need for additional post-processing or finishing operations, minimizing production time and costs.
Tool center point
In 5-axis CNC machining, the Tool Center Point (TCP) is a critical aspect of the process. TCP refers to the point where the cutting tool meets the part. During machining, the machine constantly adjusts the TCP to maintain contact with the part as it moves along the path. This consistent and precise control of tool position and orientation allows 5-axis machines to produce complex shaped, curved or angular components with a high level of accuracy. By accurately controlling TCP, 5-axis machines can increase the overall quality of the final product while reducing the risk of errors and costly rework.
5-Axis Machining in Different Industries
aerospace industry
5-axis machining plays a critical role in the aerospace industry due to the need for precision and the complexity of components used in aircraft and spacecraft. Complex shapes such as turbine blades and fuselages require a high level of precision and surface finish that can be achieved with 5-axis machining. Additionally, the aerospace industry often uses exotic materials such as titanium and Inconel, which require advanced machining techniques to achieve successful results.
Defense Industry
The defense industry relies heavily on 5-axis machining to produce complex parts and components used in military equipment. These components generally require a high level of precision and durability to withstand harsh operating conditions. 5-axis machining is crucial for the production of:
- Weapon systems
- Missiles and guidance systems
- Military vehicles and aircraft components
The ability to machine complex shapes with a high degree of precision is essential to the functionality and performance of defense industry products.
Transport Industry
5-axis machining has a significant impact on the transportation industry, particularly in the automotive and high-performance vehicle sectors. It enables the production of complex, lightweight components that can improve fuel efficiency and vehicle performance. Some important applications in the transportation industry include:
- Engine components such as pistons and cylinder heads
- Complex suspension and chassis parts
- Manufacture of molds and dies for body panels
The precision offered by 5-axis machining also ensures excellent surface finishes, reducing the need for additional finishing processes and improving the overall efficiency of the manufacturing process.
Materials and tools in 5-axis machining
Cutting tools
In 5-axis machining, cutting tools are critical components for efficient and accurate manufacturing. Various cutting tool materials are available to meet specific machining requirements. For example, carbide and high-speed steel (HSS) are popular choices for their durability and high-performance characteristics.
For machining aluminum and titanium , ideal cutting tools must have excellent wear resistance and thermal stability. Polycrystalline diamond (PCD) and cubic boron nitride (CBN) tools are often preferred for these materials due to their properties. However, they may not be suitable for all parts, so it is essential to consider the intended application.
Another aspect to consider is the Coating on cutting tools, which can significantly improve tool performance by reducing friction and improving wear resistance. Common coatings include titanium nitride (TiN) and titanium aluminum nitride (TiAlN).
Material Profile
When it comes to 5-axis machining, precision material profiling is essential to providing consistent results on complex shapes. One of the common applications of 5-axis machining is the creation of impellers that require a precise geometric profile for optimal operation.
- For aluminum , a lightweight and highly machinable material, 5-axis machining can provide excellent surface finishes and intricate details. It is commonly used in parts in the aerospace and automotive industries due to its strength and corrosion resistance.
- In contrast, titanium is known for its high strength-to-weight ratio and excellent corrosion resistance, making it an ideal choice for aerospace and medical applications. However, titanium's low thermal conductivity can cause heat build-up during machining, so proper cutting tools and cooling systems are essential to prevent premature wear.
In summary, the right combination of cutting tools and material profiling, along with adequate knowledge of the workpiece material, is crucial to achieving successful results in 5-axis machining. Careful consideration of these factors will ensure that even the most complex components can be produced accurately, efficiently and reliably.
Quality and Productivity in 5-Axis Machining
Improving surface quality
5-axis machining offers many advantages when it comes to improving surface quality. Firstly, this technique can produce complex parts with minimal configurations, reducing the risk of errors and ensuring higher part quality. Additionally, the use of 5-axis continuous motion allows for better cutting tool angle management. This ensures even wear, resulting in smoother surface finishes.
The use of probe systems plays a vital role in achieving excellent surface quality in 5-axis machining. Assists in monitoring the surface, identifying any discrepancies and making necessary adjustments to improve accuracy. This, in turn, leads to better surface finishes and reduces scrap rates.
Increasing productivity
In terms of productivity, 5-axis machining offers numerous advantages over traditional 3-axis machining:
- Shorter machining times: By incorporating simultaneous motion in all five axes, 5-axis machines can perform complex operations in a single setup. This reduces the time spent on setups and minimizes the overall duration of the machining process.
- Greater machine versatility: 5-axis machines handle different types of operations with ease, such as milling, drilling, and turning. This means a single machine can perform multiple functions, reducing the need for specialized machines or additional setups.
- Reduced tooling costs: The ability to maintain constant contact with the workpiece in 5-axis machining means tool wear is more evenly distributed. This extends tool life, reducing overall tooling expenses.
- Improved part quality: By using 5-axis motion, machining can be performed closer to the part geometry without repositioning, which reduces the chance of errors and improves part quality.
In conclusion, 5-axis machining greatly improves the quality and productivity aspects of manufacturing processes. Through the use of advanced probing systems, versatile machines and more efficient operations, 5-axis machining achieves higher surface quality and greater productivity in modern manufacturing.
Advances and Trends in 5-Axis Machining
Innovation in Fixing
In the world of 5-axis machining, advances in clamping have played a vital role in improving the production process. Clamping refers to the system of holding, supporting and positioning a part while it is being machined. With the help of innovative clamping systems, machinists can now work on complex shapes and surfaces more efficiently.
A notable innovation in fastening is the integration of vacuum systems. This allows the workpiece to be securely clamped without traditional clamps, significantly improving cutting tool access. Additionally, advances in materials and design allow manufacturers to develop lighter yet more robust accessories. This reduces setup time and facilitates faster production cycles.
Cutting condition trends
In 5-axis machining, cutting conditions greatly influence the quality of the final product. Over the years, machinists have identified key approaches to optimizing the cutting process, enabling smoother, more precise results.
Some cutting condition trends that are shaping the 5-axis machining industry include:
- Adaptive cutting strategies : These strategies take into account the cutting tool load and automatically adjust the cutting parameters. These approaches reduce tool wear, minimize vibrations and improve surface finish.
- High Speed Machining (HSM) : This method involves operating the cutting tool at higher speeds and feed rates while maintaining a shallower depth of cut. As a result, it improves productivity and improves surface quality.
- Spline interpolation : Spline interpolation is a technique that allows for smoother transitions between tool paths during the cutting process. In 5-axis machining, this method helps produce more precise and complex parts without sacrificing efficiency.
By incorporating these advancements and trends, 5-axis machining continues to push the limits of what is possible in manufacturing highly complex parts. Through innovation in clamping trends and cutting conditions, this field is opening up new opportunities for efficiency and precision in modern manufacturing.