Laser welding principle
Laser welding involves directing a high-intensity laser beam onto a metal surface. The laser interacts with the metal, causing it to absorb the laser energy and convert it into heat. This heat causes the metal to melt and eventually cool and solidify, resulting in a welded joint.
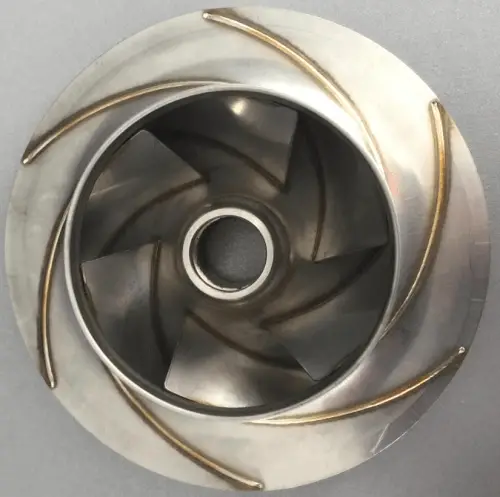
There are two laser welding mechanisms:
1. Heat conduction welding:
When a laser is directed at a material surface, part of the laser energy is reflected while the remainder is absorbed by the material. This absorbed energy is converted into heat, which causes the material to heat up and melt.
Heat from the surface layer of the material continues to be transferred through heat conduction to the deeper layers of the material until the two welded parts are joined.
Pulsed laser welding machines are commonly used for this process, and the depth-to-width ratio is typically less than 1.
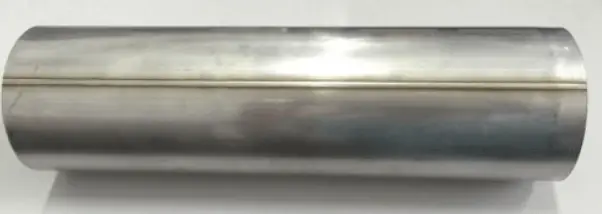
Stretch pipe welding – continuous welding
2. Laser deep penetration welding
When a high power density laser beam is directed at the surface of a material, the material absorbs light energy and converts it to heat energy. As a result, the material heats up, melts and vaporizes, producing a large amount of metallic vapor.
The reaction force of the escaping steam pushes the molten metal, creating holes. With continuous laser irradiation, the wells penetrate deeper into the material.
When the laser is turned off, the molten metal around the wells flows back and solidifies, resulting in the two parts being welded together.
This process is commonly used in continuous laser welding machines and the depth to width ratio is typically greater than 1.
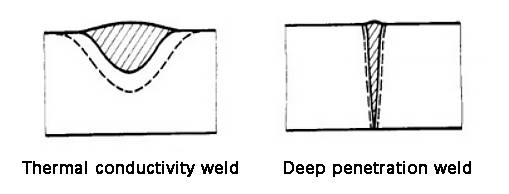
Features of laser welding
- Laser welding is known for its fast welding speed, large welding depth and minimal deformation of the materials to be welded.
- Laser welding can be performed at room temperature or under specific conditions, and the equipment required is relatively simple. For example, when a laser passes through an electromagnetic field, the beam does not move. Additionally, laser welding can be performed in vacuum, air and some gas environments, and can even weld through transparent materials such as glass.
- Laser welding can weld refractory materials such as titanium and quartz as well as different materials with excellent results.
- With high-power laser welding machines, the power density is very high and the depth-to-width ratio can reach 5:1.
- Laser welding is capable of microwelding due to its ability to produce a small, focused spot that can be precisely positioned. This characteristic makes it ideal for assembling and welding micro and small parts produced in large quantities.
- Laser welding can reach parts inaccessible for long-distance non-contact welding, providing greater flexibility to welding operations.
- Laser beams can be divided in terms of energy and time, enabling simultaneous multi-station welding and time-sharing welding, which greatly improves production efficiency and equipment utilization.
Laser welding classification
There are two types of laser welding: pulsed laser welding and continuous fiber laser welding, which are classified based on the type of laser used.
Here are the differences between the two methods:
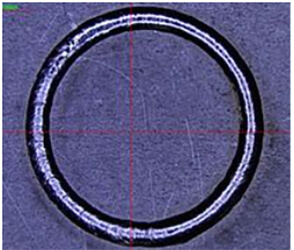
Continuous Welding Standard
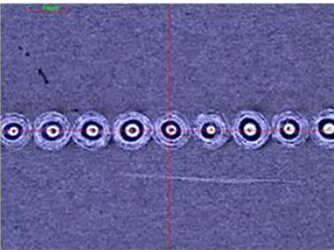
Pulse welding
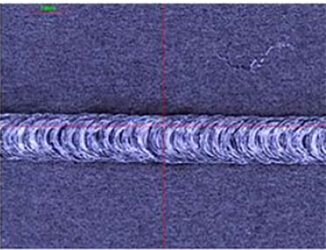
Pulse Welding Spot Superposition
Welding mode | Pulse welding | Continuous welding |
---|---|---|
Penetration | Small | Big |
Energy consumption | Big | Small |
Weld quality and appearance | Normal | Good |
Laser welding classified by laser welding method
According to the product combination, it is divided into:
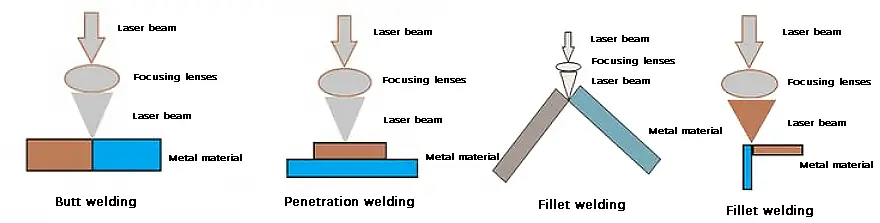
Butt welding typically requires no gap or, if necessary, a gap of less than 0.05 mm. The thinner the product to be welded, the more stringent the clearance requirements.
In the case of penetration welding, it is important to ensure a firm connection between the upper and lower layers. As the top layer material becomes thinner, a tighter fit is required to achieve the desired result.
Comparison between laser welding and other welding methods
Welding mode | laser welding | Argon Arc Welding | Resistance welding | Brazing | Electron beam welding |
Heat affected zone | Minimum | More | Generally | More | Any less |
Thermal deformation | Any less | More | Generally | More | Any less |
Welding point | Any less | More | Generally | More | Any less |
Weld quality and appearance | Good | Generally | Generally | Generally | Preferably |
If you add solder | No | No | No | Yes | No |
Welding environment | No requirements | No requirements | No requirements | No requirements | Vacuum |
Consumables | / | Welding Wire or Tungsten Electrode Replacement | copper electrode | Welding | Faster |
Welding speed | Faster | Slow | / | / | / |
Degree of automation | High | Generally | Generally | Generally | Generally |
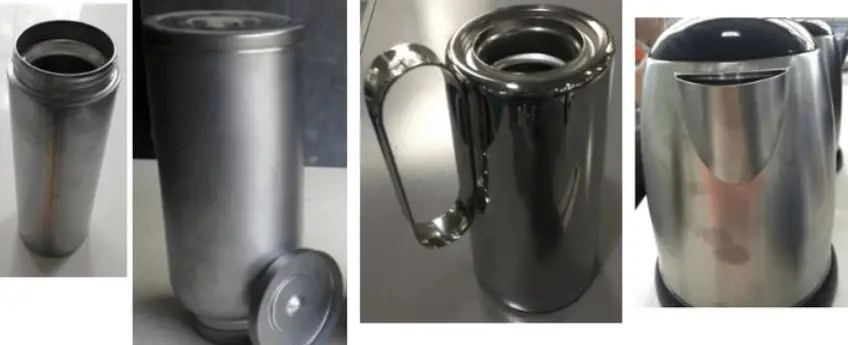
Pulsed/continuous welding
Features of welding metal materials
Difficulty | Stainless steel | Die steel | Carbon steel | steel alloy | Nickel | Zinc | Aluminum | Gold | Silver | Copper |
Stainless steel | easy | |||||||||
Die steel | easy | easy | ||||||||
Carbon steel | easy | easy | easy | |||||||
steel alloy | easy | easy | easy | easy | ||||||
Nickel | easy | easy | easy | easy | easy | |||||
Zinc | easy | easy | easy | easy | easy | easy | ||||
Aluminum | hard | hard | hard | hard | a little hard | hard | easy | |||
Gold | hard | hard | hard | hard | hard | hard | hard | a little hard | ||
Silver | hard | hard | hard | hard | hard | hard | hard | hard | hard | |
Copper | a little hard | hard | hard | hard | a little hard | hard | a little hard | hard | hard | easy |
Steel welding characteristics
Steel is an alloy of iron and carbon, with carbon content varying between 0.04% and 2.3%. To ensure the toughness and plasticity of steel, the carbon content normally does not exceed 1.7%.
Alloy steel is produced by intentionally adding alloying elements such as Mn, Si, Cr, Ni, Mo, W, V, Ti, etc. during the casting process. These alloying elements can be used to improve the mechanical properties, process properties or other special properties of steel such as corrosion resistance, heat resistance and wear resistance.
Classification by chemical composition:
(1) Carbon steel:
The. Low carbon steel (C ≤ 0.25%);
B. Medium carbon steel (C ≤ 0.25 ~ 0.60%);
w. High carbon steel (C ≤ 0.60% ~ 2.11%).
The higher the carbon content, the easier it is to produce blast holes in the weld pool.
(2) Alloy steel:
The. Low alloy steel (total alloy content ≤ 5%);
B. Medium alloy steel (total alloying element content > 5 ~ 10%);
w. High alloy steel (total alloy content > 10%).
The weldability of alloy steel depends on the alloy elements, and the weldability similar to the melting point characteristics of stainless steel is good.
(3) Stainless steel
Stainless steel refers to a type of steel that is resistant to weak corrosive media such as air, steam, water and chemically corrosive media such as acid, alkali and salt. It is divided into different types, including martensitic steel, ferritic steel and austenitic steel.
Martensitic stainless steel is typically a low or high carbon steel with a chromium content ranging between 12% and 18%, and the main alloying elements are iron, chromium and carbon. However, it has the worst weldability of all stainless steels. Welded joints are often hard and brittle, prone to cold cracking. To reduce the likelihood of cracking and embrittlement, preheating and tempering are recommended when welding stainless steel with a carbon content greater than 0.1%, such as 403, 410, 414, 416, 420, 440A, 440B and 440C.
Austenitic stainless steel, on the other hand, refers to stainless steel with an austenitic structure at room temperature. This type of steel contains about 18% chromium and nickel and has a stable austenite structure when the chromium content is between 8% and 10% and the carbon content is about 0.1%. It generally has good laser welding performance. However, the addition of sulfur and selenium to improve its mechanical properties increases the tendency of solidification cracking.
Austenitic stainless steel has lower thermal conductivity than carbon steel, with a slightly higher absorption rate than carbon steel. The welding penetration depth is only about 5-10% of that of ordinary carbon steel. However, laser welding, which has a small heat input and high welding speed, is suitable for welding Cr Ni series stainless steel. Some common types of austenitic stainless steel include 201, 301, 302, 303, and 304.
In general, stainless steel has good weldability, with a well-formed weld puddle.
(4) 200 Series – Cr Ni Mn
Austenitic stainless steel, 300 series – chromium-nickel
The meaning of each letter:
- CR stands for chrome
- Ni means nickel
- Mn means manganese
- 1 indicates carbon content (0 in 304 is not carbon-free, but the carbon content is less than 0.1%, belonging to low carbon)
- 201: 1Cr17Mn6Ni5N, indicating austenitic stainless steel 201 containing 1% carbon, 17% manganese, 17% chromium and 6% nickel;
- 304: 0Cr19Ni9 (0Cr18Ni9), indicating 304 austenitic stainless steel containing less than 0.1% carbon, 18%/19% chromium and 9% nickel;
201 stainless steel contains manganese, which makes it prone to oxidation and rust in humid, salty, and poorly maintained environments (although it is still much better than iron products and can be treated with wire drawing or polishing after oxidation and rust).
Unlike iron products, the electroplating surface layer cannot be treated after corrosion.
On the other hand, 304 stainless steel does not contain manganese, but has a higher chromium and nickel content, which makes it more resistant to oxidation and rust.
The price of 201 stainless steel is 3-4 times that of iron-based furniture materials (chrome plated or sprayed), while the price of 304 stainless steel is more than half or almost double the price of 201 stainless steel.
The surface of 304 stainless steel is white with a metallic luster, similar to a plastic plate.
Ferritic stainless steel, with a body-centered cubic crystal structure, typically contains 11% to 30% chromium and does not contain nickel (although it may contain small amounts of Mo, Ti, Nb, and other elements).
This type of steel has high thermal conductivity, low expansion coefficient, good oxidation resistance and excellent resistance to stress corrosion cracking.
An example is 430 stainless steel.
Compared to austenitic and martensitic stainless steels, ferritic stainless steels are less likely to produce hot and cold cracks when laser welded.
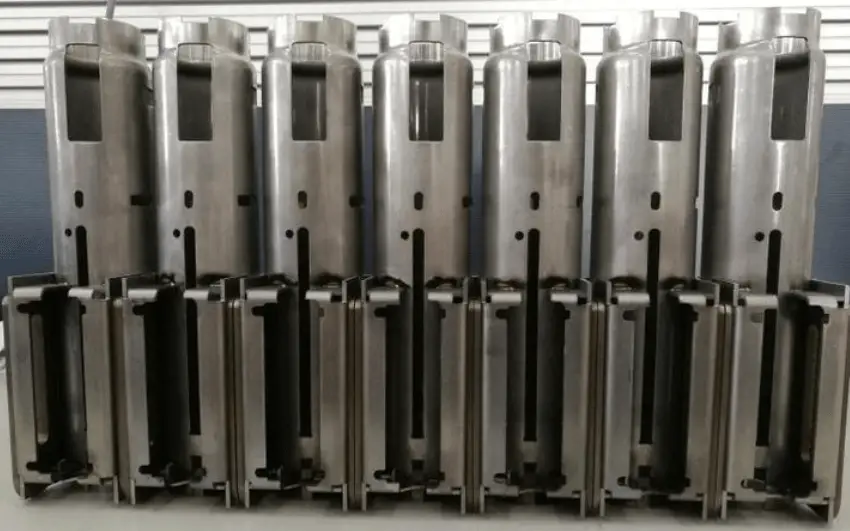
Welding of the automotive steering system structure – continuous welding
Aluminum alloy welding characteristics
Due to high surface reflectivity and high thermal conductivity, aluminum welding requires high power density, which makes it difficult to form a stable molten pool.
Many aluminum alloys contain volatile elements such as silicon and magnesium, leading to the formation of many pores in the weld.
The low viscosity and surface tension of liquid aluminum facilitate the overflow of liquid metal into the weld pool, affecting weld formation.
Some aluminum alloys may experience hot cracking during solidification, which is related to cooling time and weld protection.
The higher the purity of the aluminum, the better the welding quality.
Welding on Series 3 aluminum is generally acceptable, while welding on low-purity aluminum can produce blast holes and cracks.
Features of the laser welding process
There are several process parameters that affect the quality of laser welding, including power density, beam characteristics, defocus, welding speed, laser pulse waveform, and auxiliary gas flow.
1. Power density
Power density is a critical parameter in laser welding.
A high power density can quickly heat the metal to its melting point in microseconds, resulting in a high-quality weld.
Power density is determined by peak power and solder joint area.
Power density = peak power ÷ solder joint area
When welding highly reflective materials such as aluminum and copper, it is necessary to increase the power density. This can be achieved by using a higher current or power and welding as close to the focal point as possible.
2. Laser pulse waveform
The waveform of the laser pulse is a critical factor in laser welding, especially in sheet metal welding.
When the high-intensity laser beam interacts with the surface of the material, 60% to 90% of the laser energy is lost due to reflection, and the reflectivity changes with the surface temperature.
The reflectivity of the metal changes significantly during a laser pulse.
When the metal is in a solid state, the reflectivity of the laser is high.
However, when the surface of the material melts, reflectivity decreases and absorption increases, allowing a gradual reduction in current or power.
Therefore, the pulse waveform is usually designed to accommodate these changes, such as:
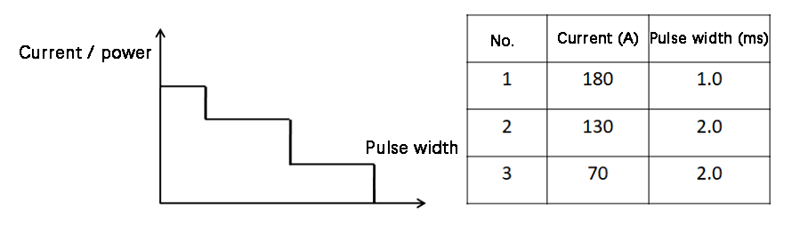
3. Blur Amount
The term “defocus amount” refers to the deviation of the workpiece surface from the focal plane.
The position of the defocus directly impacts the keyhole effect during custom welding.
There are two blurring modes: positive and negative.
If the focal plane is located above the workpiece, it is considered positive blur, and if it is located below the workpiece, it is considered negative blur.
When the positive and negative defocus are equal, the power density of the corresponding plane is approximately the same, but the shape of the molten pool is different.
Negative defocus can result in greater penetration, which is related to molten pool formation.
Experimental results show that when laser heating reaches 50 to 200 μS, the material begins to melt, forming metal in liquid phase and partially vaporizing to form high-pressure vapor. This results in a high-speed spray of dazzling white light.
At the same time, the high concentration gas moves the liquid metal to the edge of the weld pool, creating a depression in the center of the pool.
During negative defocus, the internal power density of the material is higher than that of the surface, leading to stronger melting and gasification. This allows light energy to be transmitted to the deepest part of the material.
Therefore, in practical applications, negative defocus should be used when deep penetration is required, and positive defocus should be used when welding thin materials.
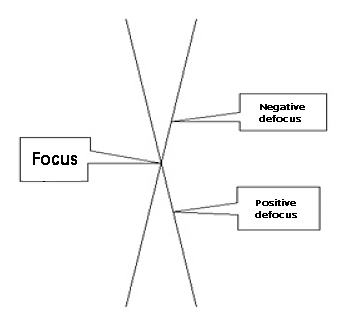
Focus position:
The smallest point with the highest energy can be achieved through spot welding. On the other hand, when a small spot is needed and power is low, spot welding can also be used.
Negative blur position:
A slightly larger spot is suitable for continuous deep penetration welding and deep penetration spot welding. As the focus distance increases, the spot size increases.
Positive defocus position:
A slightly larger spot is suitable for continuous surface seal welding or situations where low penetration is required. As the focus distance increases, the spot size also increases.
4. Welding speed
The welding surface quality, penetration, heat affected zone and other factors are determined by the welding speed.
Penetration can be improved by reducing the welding speed or increasing the welding current.
Reducing welding speed is commonly used to improve penetration and increase equipment life.
5. Auxiliary blow
Auxiliary blowing is a crucial process in high-power laser welding.
First, it helps prevent metal spray from contaminating the focusing mirror through the use of coaxial shielding gas.
Secondly, it prevents the accumulation of high-temperature plasma generated during the welding process and prevents the laser from reaching the material surface through side blowing.
Thirdly, it uses shielding gas to isolate the air and protect the welding puddle from oxidation.
The choice of auxiliary gas and volume of air blown greatly influence welding results, and different blowing methods can also have a significant impact on welding quality.
6. Fiber Optic Configuration and Welding Joint
For example, if the diameter of the optical fiber is 0.6mm and the focusing focal length is 120mm with a collimation focusing of 150mm, the focus diameter can be calculated as follows:
Focus diameter = 0.6 x 120/150 = 0.48 mm
The specific configuration is determined based on the material, thickness, penetration and adjustment clearance of the product.
Long Focus Features:
- The working distance is considerable, which allows interference from the device to be avoided, reduces the impact of product height fluctuations and minimizes contamination from splashes on the protective lenses.
- To achieve the same level of penetration, equipment power requirements will be greater.