P redo
With the increasing use of fiber lasers in various fields, their reliability has become an important concern. This includes the performance reliability of the laser output, electronic components, optical devices and systems, all of which are closely related to the thermal characteristics of the laser itself.
Temperature has a significant impact on laser performance, especially output power and stability. The heat generated by a fiber laser comes mainly from the pump source and gain cavity.
The pump source conversion efficiency is about 50%, which means that heat is generated in the form of energy equivalent to the output optical power. If this heat is not dissipated quickly enough, the temperature of the internal chip will rise rapidly, causing the center wavelength of the laser to shift.
In the gain cavity, only part of the pump light is converted into laser output and the rest is converted into thermal energy. This thermal energy increases the temperature of the gain medium, causing the fluorescence spectrum to broaden and the spontaneous emission lifetime to decrease, ultimately reducing power conversion efficiency.
Therefore, effective heat management is crucial for fiber lasers. Currently, air cooling and water cooling are the two most commonly used heat management technologies.
Air cooling is suitable for low-power pulse and continuous wave lasers, while water cooling is the main heat dissipation method used in medium- and high-power fiber lasers.
Two main ways of heat dissipation
1. Water cooling and heat dissipation
As the name suggests, water cooling is a method that uses water to dissipate heat through a heat exchanger, such as a water cooling plate.
The principle behind water cooling is simple: cold water from a chiller flows through a water pipe and enters the heat exchanger, then exits through the other heat exchanger port and returns to the chiller through the water pipe. This continuous circulation helps to dissipate heat from inside the laser.
Water cooling and heat dissipation are simple in structure and easy to maintain. By using a chiller with higher cooling capacity, the cooling performance of the laser can be improved due to the strong heat dissipation capacity and good temperature uniformity.
Currently, on the market, more than 500 manufacturers integrate and sell portable laser welding machines that generally use water cooling.
However, in addition to the laser itself, a portable laser welding machine with water cooling and heat dissipation requires a separate water and water cooler, which significantly increases the overall volume and weight of the equipment and limits its use environment.
2. Air cooling and heat dissipation
In a broad sense, air cooling refers to the use of fans to improve air convection and facilitate heat exchange within the machine.
Thanks to technological advancements, leading laser manufacturers have now ventured into the realm of air cooling and heat dissipation.
Last June, global fiber laser giant Company I launched the air-cooled LightWELD 1500W portable laser welding product.
In August, the first air-cooled A1500W intelligent laser welder was launched in China.
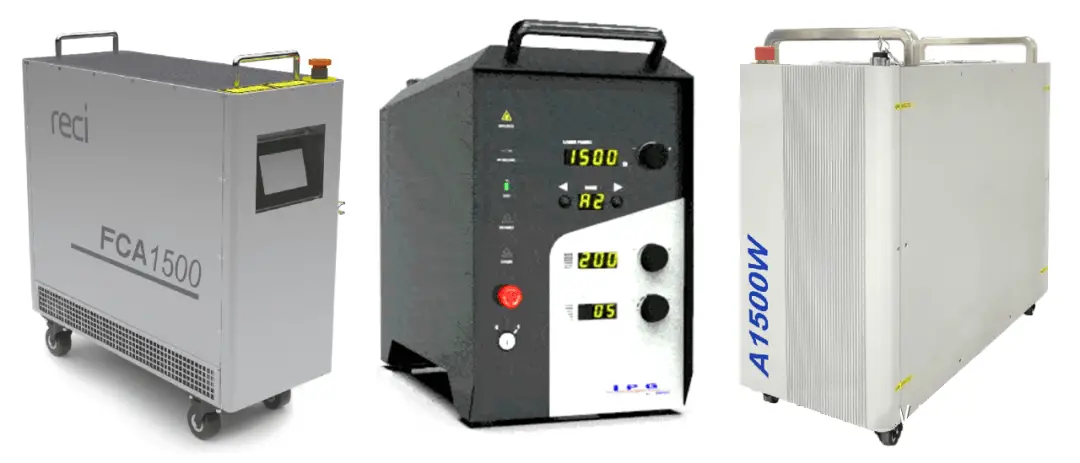
Air-cooled fiber laser: reci, IPG, GW
These three lasers are primarily designed for the portable laser welding market segment.
Air-cooled lasers provide greater flexibility and portability in work environments.
All three lasers use air-cooled heat dissipation, eliminating the need for additional water-cooling equipment. This reduces equipment costs and significantly reduces equipment volume and weight.
Despite sharing the “air-cooled” classification, each laser uses a different heat dissipation scheme. This includes fan heat dissipation, heat pipe radiator heat dissipation, and compressor refrigeration heat dissipation.
(1) Fan cooling
In lasers, substrates with good thermal conductivity, such as copper, aluminum nitride, etc., are used to export the heat generated in the pump source and gain cavity, and then dissipate it by convection. This method is known as convective heat dissipation.
Convection heat transfer is classified into two types based on the different driving forces of fluid flow – natural convection and forced convection heat dissipation.
When the fluid flows spontaneously and conducts heat transfer only by the temperature difference of the fluid, it is called natural convection and occurs without any external force.
On the other hand, forced convection occurs when there is an external driving force that causes fluid to flow quickly through fans, pumps, or other components to remove heat.
Because natural convection has a slow heat dissipation rate and weak effect, it cannot fully meet the heat dissipation requirements of the laser.
Therefore, it is essential to add fans to the entire cooling system to accelerate airflow and convert natural convection into forced convection.
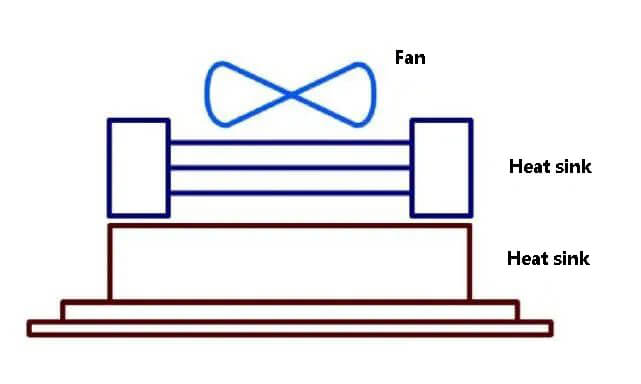
Fan cooling principle
(2) Heat pipe radiator
Heat dissipation in a heat pipe radiator is achieved by transferring heat through the phase change of its internal working liquid. The liquid has a low boiling point and is highly volatile.
One end of the heat pipe is the evaporation end, which is connected to the heat sink inside the laser, while the other end is the condensing end, which is connected to an external heat sink and fan. The tube wall is equipped with a liquid absorption core made of capillary porous materials.
When the laser generates heat, the evaporation end is heated, causing the working liquid to evaporate quickly. The resulting vapor flows to the condensing end under a pressure difference and releases heat, which is then discharged through the fan.
At the same time, the vapor recondenses into liquid, which flows back to the evaporation section through the suction core. (In a gravity heat pipe, there is no suction core and the liquid sticks to the pipe wall and flows back to the lower evaporation section due to gravity).
This cycle continues, allowing heat to transfer from the inside of the laser to the outside.
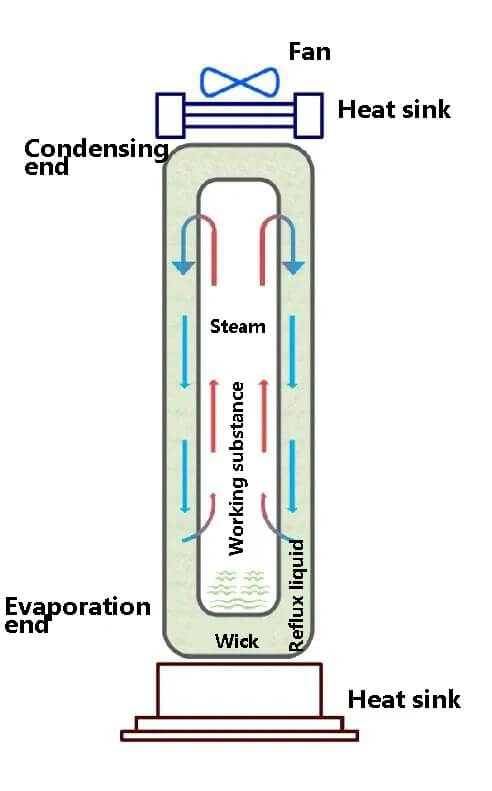
Heat pipe radiator heat dissipation principle
IPG company's lightWELD 1500 portable laser welding system incorporates a heat pipe radiator for heat dissipation.
lightWELD's design and manufacturing are characterized by its compact size and light weight, leading to a new generation of portable laser welding machines.
In addition to welding, it also offers a dual function of portable laser welding and cleaning.
The lightWELD portable laser welding machine employs an air-cooled mechanism, eliminating the need for additional cooling water equipment and associated energy consumption.
Eliminates the need for chiller piping, components, controls and maintenance connections, reducing costs, improving portability and improving overall system reliability.
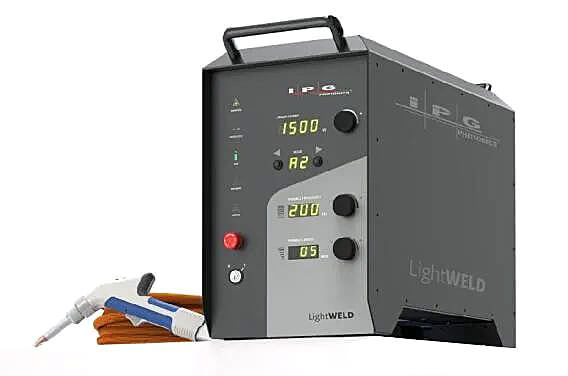
LightWELD 1500 Portable Laser Welding System
(3) Compressor cooling and heat dissipation
Compressor refrigeration and heat dissipation principle: the compressor compresses the refrigerant to turn it into high-temperature and high-pressure gas and flow to the external condenser.
High temperature and high pressure gas condenses into low temperature and high pressure liquid. The heat generated by liquefaction is discharged from the machine with the help of a fan.
The low temperature and high pressure liquid refrigerant changes to a low temperature and low pressure state after depressurization through the expansion valve and then flows into the indoor evaporator.
The evaporator absorbs heat to reduce the internal temperature of the laser, achieving the cooling effect. Subsequently, the refrigerant vaporizes into a gas with high temperature and low pressure.
The refrigerant gas evaporated by the evaporator is compressed again by the compressor and circulates back and forth to dissipate the heat inside the machine.
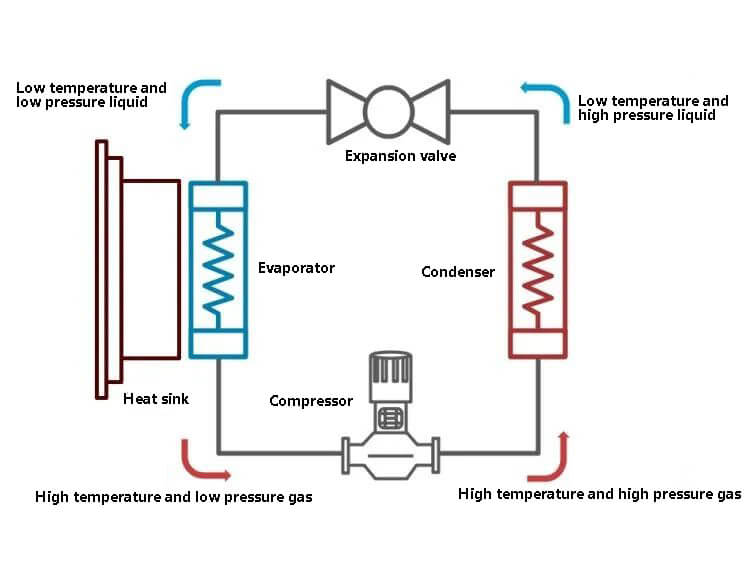
Compressor refrigeration and heat dissipation principle
A1500w intelligent air-cooled portable welding machine uses compressor refrigeration and heat dissipation scheme.
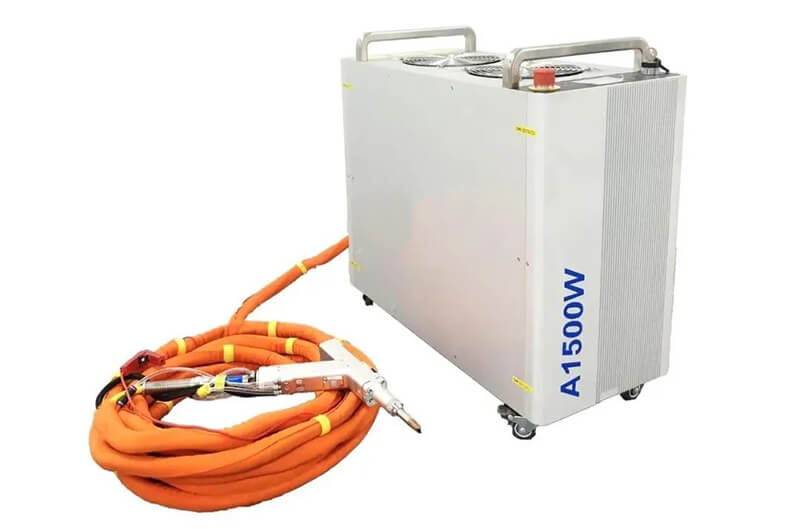
1500W Air-cooled Intelligent Portable Welder
Comparison of heat dissipation methods
The structure of fan cooling is relatively simple, as it diffuses heat from the heat sink to the ambient air using the temperature difference between the heat sink and the surrounding air through fan-forced convection.
However, in summer, when the ambient temperature is high, the temperature difference between the heat sink and the air decreases, resulting in a reduction in heat dissipation capacity. This limits its ability to dissipate heat and makes it sensitive to environmental factors, making temperature control difficult.
Despite its limitations, fan cooling has the advantage of being simple in the overall equipment and control system.
On the other hand, a heat pipe radiator has a more complex structure with multiple heat pipes. It relies on evaporation and condensation of the working material to quickly transfer heat from the heat sink to the ambient air through the fan, making it more efficient than simple fan cooling.
Passive heat dissipation is unable to accurately control the temperature and is greatly affected by the ambient temperature, and is also a part of it.
On the other hand, the refrigeration and heat dissipation scheme of the compressor falls under active heat dissipation. The existence of the compressor and expansion valve allows precise temperature control, regulating the flow and pressure of the refrigerant.
Furthermore, the temperature of the refrigerant in the condenser is higher than that of the heat sink, allowing rapid heat transfer to the air. As a result, your control system must be more complex.
However, due to its significantly more complicated design than the previous two schemes, the size and weight of the equipment also increase correspondingly.
Traditional fiber lasers typically use water cooling to dissipate heat. The water is first cooled by a compression mechanism and then used to cool the laser.
In contrast, air-cooled heat dissipation directly utilizes the compression mechanism to cool the laser, eliminating the need for water and reducing the intermediate heat transfer link. This results in higher heat dissipation efficiency and lower volume and weight.
In our laboratory, we use a constant temperature and humidity test chamber to simulate a high-temperature service environment in summer by adjusting the temperature to 35℃.
We tested the fiber internal gain temperature change in a laser operating at full power (1500W) using different air cooling schemes over time. Experimental data showed that the temperature of the optical fiber increased exponentially in the first few minutes and stabilized after about 10 minutes.
Due to the compressor refrigeration function, the laser can be actively cooled and the temperature can be controlled below 60℃ with relatively stable temperature changes.
On the other hand, the other two schemes are based on passive heat dissipation, resulting in slightly higher internal temperatures than the compressor refrigeration scheme. The heat pipe has higher heat transfer efficiency and can export heat from inside the laser efficiently, resulting in a lower internal temperature than the pure fan and a smoother temperature rise.
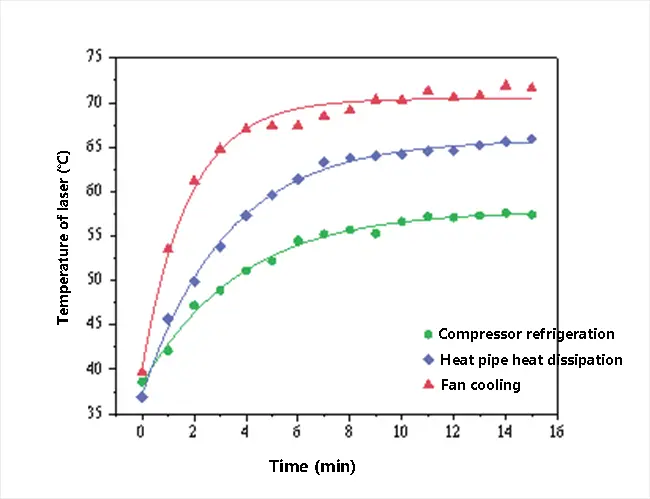
Temperature variation with time when laser with different air cooling schemes produces 1.5KW laser
(lab data may differ from actual field use)