The laser welding process, mainly for sheet metal welding, can be divided into two categories: continuous fiber laser welding and pulsed YAG laser welding.
Based on the principle of laser welding, it can be divided into heat conduction welding and laser deep penetration welding. When the power density is less than 104 to 105 W/cm², heat conduction welding is considered. This results in shallow penetration and slower welding speed.
On the other hand, when the power density is greater than 105 to 107 W/cm², the metal surface will form “holes” due to heating and result in laser deep penetration welding. This method is characterized by its fast welding speed and large depth/width ratio.
The principle of heat conduction laser welding involves heating the surface to be processed by means of laser radiation, guiding the surface heat through internal transfer and diffusion, and melting the workpiece to form a specific molten pool by controlling parameters of the laser, such as pulse width, energy, peak power and repetition frequency. This method is suitable for welding thin plates.
Laser deep penetration welding is mainly used for gear welding and metallurgical sheet welding, and the focus of this article is on the principle of laser deep penetration welding.
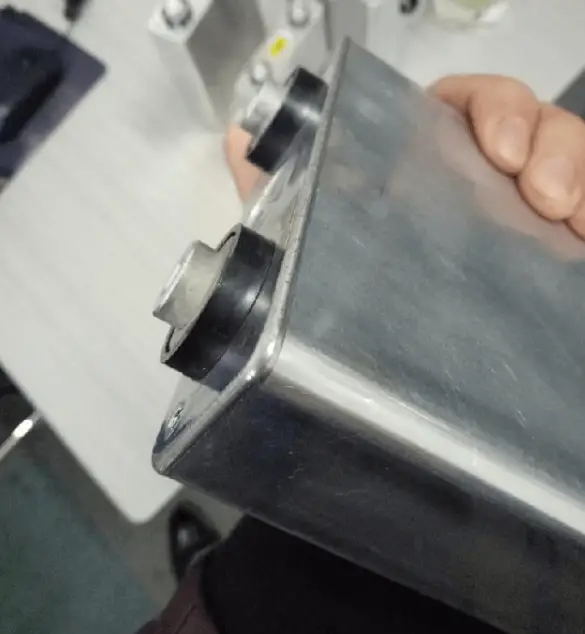
Lithium battery top cover welding with aluminum shell – continuous fiber laser (new energy vehicle cell, mainly 3 series aluminum)
1. Principle of laser deep penetration welding
Laser deep penetration welding typically uses a continuous fiber-optic laser beam to join materials. The metallurgical process of this method is similar to electron beam welding and is carried out through a “keyhole” structure.
When the material is exposed to a high power density laser, it evaporates and creates tiny holes. The small holes, filled with vapor, behave like black bodies and absorb almost all of the energy from the incident beam.
The temperature inside the holes reaches approximately 2,500℃ and heat is transferred from the outer walls of the high-temperature holes to melt the surrounding metal.
The small holes are filled with high-temperature vapor generated by the continuous evaporation of the wall material under laser irradiation. The four walls of the holes are surrounded by molten metal, and the liquid metal is surrounded by solid materials.
In most conventional welding processes and laser conduction welding, energy is first deposited on the surface of the part and then transmitted inward through conduction.
Liquid flow and wall surface tension outside the hole walls are in dynamic equilibrium with the continuous vapor pressure inside the hole cavity. The laser beam continuously enters the small holes, and the material outside the holes continuously flows out.
The movement of the laser beam keeps the small holes and the molten metal around the holes in a stable flowing state.
This means that the small holes and molten metal will advance with the speed of the main beam, filling the gap left behind and solidifying to form the weld.
All these processes occur so quickly that the welding speed can easily reach several meters per minute.

6 series aluminum fiber CW laser welding (this is high speed rail tread)
2. Main parameters of laser deep penetration welding process
(1) Laser power
There is a limit to laser energy density in laser welding. If the laser energy density is below this value, the penetration will be superficial. However, if it reaches or exceeds this value, penetration is greatly improved.
Plasma generation, which means the progress of stable deep penetration welding, only occurs when the laser power density on the workpiece exceeds the limit, which depends on the material.
When the laser power density is below the limit, only melting of the workpiece surface occurs, resulting in stable heat conduction welding.
If the laser power density is close to the critical condition for keyhole formation, the welding process becomes unstable, with alternation of deep penetration welding and conduction welding, resulting in significant fluctuations in the penetration depth.
During laser deep penetration welding, the laser power simultaneously controls the penetration depth and welding speed. Penetration depth is directly related to beam power density and is a function of incident beam power and beam focal point.
In general, for a laser beam of a given diameter, penetration increases as the beam power increases.

Kettle horse – YAG pulse laser welding (can directly make surface appearance)
(2) Beam focal point
Beam spot size is a critical variable in laser welding as it determines power density. However, measuring spot size for high-power lasers is a challenging task despite the availability of several indirect measurement technologies.
The limit of the beam focusing diffraction spot size can be calculated using the theory of light diffraction, but the actual spot size is larger due to the presence of aberrations in the focusing lens.
The simplest measurement method is the equal temperature profile method, which involves measuring the focal point and perforation diameter after burning thick paper and penetrating a polypropylene plate.
This method requires mastery of laser power and beam action time, which can be achieved through practice and measurement.
(3) Material absorption value
The laser absorption of materials depends on several important material properties, such as absorptivity, reflectivity, thermal conductivity, melting temperature, evaporation temperature and so on.
There are two factors that affect the absorptivity of materials to the laser beam:
First, the resistance coefficient of the material. After measuring the absorptivity of the polished surface of the material, it was found that the absorptivity of the material is directly proportional to the square root of the resistance coefficient, which changes with temperature.
Secondly, the surface state or finish of the material, which has a significant impact on the absorptivity of the beam and therefore the welding effect.
Materials with high purity and general conductivity, such as stainless steel and nickel, are best for soldering.
On the other hand, high conductivity materials such as copper and aluminum are difficult to weld. Welding aluminum series 6 and above is prone to cracking and pores.
Copper welding generally depends on application requirements and can be done with pulsed YAG laser and continuous fiber laser.
In the jewelry industry, gold and silver are usually spot welded. However, there are few industrial applications for welding these materials. The focus here is on industrial applications.
The output wavelength of CO 2 lasers is typically 10.6 μm. At room temperature, the absorption rate of non-metallic materials such as ceramics, glass, rubber and plastics is very high, while the absorption rate of metallic materials is low.
However, once the material is melted or even vaporized, its absorption increases dramatically.
The method of surface coating or forming an oxide film on the surface is highly effective in improving the absorption of light beams.
(4) Welding speed
Welding speed has a significant impact on penetration depth. Increasing the speed will result in shallower penetration, but too low a speed will cause excessive melting of the material and result in excessive penetration into the workpiece.
Therefore, there is a suitable range of welding speeds for a specific material with a given laser power and thickness, and maximum penetration can be achieved at the corresponding speed value.

Stainless steel YGA pulse laser wire filler welding (can overcome the problem of large butt joints and appearance surface treatment in the later stage)
(5) Shielding gas
Inert gas is often used in laser welding to protect the weld pool. In some cases, protection may not be necessary if the material can be welded without surface oxidation.
However, most applications use helium, argon, nitrogen or other gases to protect the part from oxidation during welding.
Helium is an effective shielding gas due to its high ionization energy, which allows the laser beam to pass smoothly and reach the part surface without any hindrances. However, it is relatively expensive.
Argon is relatively cheap and has a high density, providing good protection. However, it is prone to high-temperature metal plasma ionization, which reduces effective laser power and welding speed, as well as penetration.
The argon-protected welding surface is smoother compared to the helium-protected surface.
Nitrogen is the cheapest shielding gas, but it is not suitable for some types of stainless steel welding due to metallurgical problems such as absorption, which can sometimes cause pores in the neck area.
The second purpose of using shielding gas is to protect the focusing lens from metal vapor pollution and liquid droplet sputtering, which is especially important in high-power laser welding where the ejected material becomes more powerful.
The third function of shielding gas is to disperse the plasma shielding produced by high-power laser welding. The metal vapor absorbs the laser beam, ionizing it into a plasma cloud, and the shielding gas around the metal vapor also ionizes due to heating.
If there is too much plasma, it will consume the laser beam to some extent. The plasma on the work surface acts as a second energy source, making the penetration shallower and the weld pool surface wider.
The rate of electron recombination can be increased by increasing the collision of electrons with ions and neutral atoms, reducing the electron density in the plasma.
The lighter the neutral atom, the higher the collision frequency and the higher the recombination rate.
On the other hand, only shielding gas with high ionization energy will not increase the electron density due to its own ionization.
Atomic (molecular) weight and ionization energy of common gases and metals
Material | He | Air | N | Al | mg | Faith |
Atomic (molecular) weight | 4 | 40 | 28 | 27 | 24 | 56 |
Ionization energy (eV) | 24:46 | 15.68 | 14.5 | 5.96 | 7.61 | 7.83 |
As shown in the table, the size of the plasma cloud depends on the type of shielding gas used. Helium produces the smallest plasma cloud, nitrogen produces the second smallest, and argon produces the largest. The larger the plasma size, the smaller the penetration depth.
This difference is not only due to the different ionization levels of the gas molecules, but also to the difference in the diffusion of the metal vapor caused by the different densities of the shielding gas.
Helium has the lowest ionization and density and can quickly clear the rising metal vapor from the molten metal pool.
As a result, using helium as a shielding gas can effectively inhibit plasma and increase penetration and welding speed. Furthermore, it is lightweight and hardly causes pores.
However, in actual welding, using argon as a shield gives good results. The effect of the plasma cloud on penetration is most noticeable at low welding speeds, and as welding speed increases, its impact decreases.
The shielding gas is released onto the surface of the part through a nozzle at a certain pressure. The nozzle shape and exit diameter are critical, as the nozzle must be large enough to cover the welding surface with the shielding gas, but it must also be limited in size to effectively protect the lens and prevent metal vapor pollution or metal splashes. of damaging the lens.
The flow rate must also be controlled, otherwise the laminar flow of the shielding gas will become turbulent and air will be drawn into the molten pool, forming pores.
To improve the protective effect, side blowing can also be used, where the shielding gas is injected into the small hole of deep penetration welding at a certain angle through a small diameter nozzle.
This not only reduces the plasma cloud on the surface of the part, but also affects the plasma in the hole and the formation of small holes, resulting in greater penetration depth and an ideal weld with a high depth-to-width ratio.
However, this method requires precise control of the size and direction of the gas flow, as turbulence and damage to the molten pool can easily occur, making it difficult to stabilize the welding process.
(6) Lens focal length
The laser beam is usually focused during welding and a lens with a focal length of 63mm to 254mm (2.5″ to 10″) is typically selected. The size of the focus spot is directly proportional to the focal length; a shorter focal length results in a smaller spot.
However, focal length also affects focal depth, which increases with focal length. This means that a short focal length improves power density, but requires precise maintenance of the distance between the lens and the workpiece for adequate penetration.
In actual welding, the smallest focal depth used is generally 126mm (5″). When a larger joint or greater welding is required, a lens with a focal length of 254 mm (10″) can be selected, but this requires a higher laser output power for the desired deep penetration keyhole effect.
For laser powers greater than 2 kW, especially for 10.6 μm CO2 lasers, the reflection focusing method is often used, with polished copper mirrors as mirrors, to avoid the risk of optical damage to the focusing lens.
Copper mirrors are often recommended for high power laser beam focusing due to effective cooling.
(7) Focus position
In laser welding, the focus position is crucial to ensure adequate power density. The variation in the relative position between the focus and the part surface significantly impacts the depth and width of the weld.
In most laser welding applications, the focus is usually set at about one-quarter of the required penetration below the surface of the workpiece.
(8) Laser beam position
The final weld quality during laser welding of different materials is largely controlled by the position of the laser beam, with butt joints being more sensitive than lap joints.
For example, when welding a hardened steel gear to a low carbon steel drum, proper control of the laser beam position will result in a weld composed primarily of low carbon components, which have excellent crack resistance.
In certain situations, the geometry of the part to be welded requires a deflection angle for the laser beam. When the deflection angle between the beam axis and the joint plane is less than 100 degrees, the absorption of laser energy by the part remains unchanged.
(9) Control of the gradual increase and decrease of laser power at the starting and ending points of welding
In laser deep penetration welding, small holes are present regardless of the depth of the weld. When the welding process is completed and the power switch is turned off, dots will appear at the end of welding.
Furthermore, if the new laser welding layer covers the previous weld, excessive absorption of the laser beam may occur, leading to overheating or porosity in the weldment.
To avoid these problems, the power start and end points can be programmed to allow adjustable start and end times. This is achieved by electronically increasing the initial power from zero to the set power value quickly and adjusting the welding time.
Finally, the power is gradually decreased from the set value to zero at the end of welding.
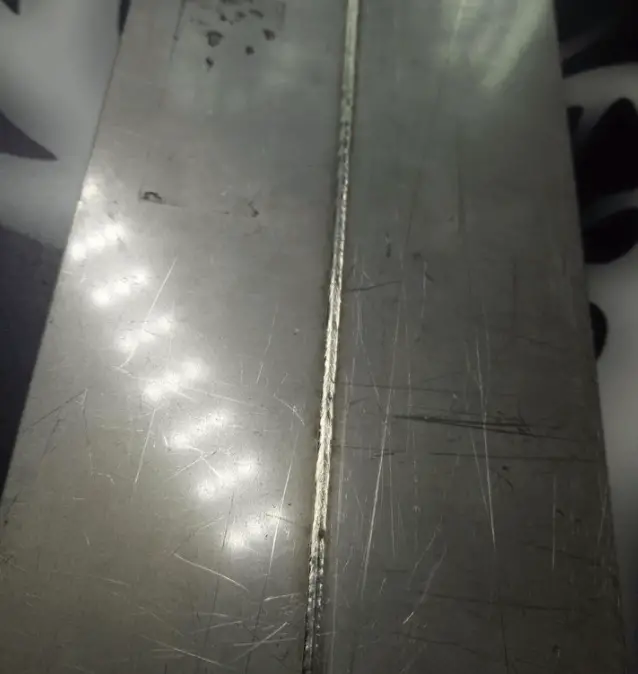
Continuous optical fiber laser welding of stainless steel (suitable for butt welding of small plates with a thickness of 0.2-3mm)
3. Features, advantages and disadvantages of laser deep penetration welding
(1) Characteristics of laser deep penetration welding
- High aspect ratio welding
The high aspect ratio welding process is characterized by deep, narrow welds, which are formed by directing a cylindrical cavity of high-temperature steam around the workpiece. This results in molten metal forming around the cavity and extending into the workpiece.
- Minimum Heat Input
The welding process requires minimal heat input due to the high temperature inside the small hole. This results in a fast melting process and low heat input into the workpiece, leading to minimal thermal deformation and a small heat-affected zone.
- High density welds
The high-temperature steam inside the small hole promotes agitation of the welding puddle and gas escape, resulting in a dense, pore-free penetration weld. The rapid cooling rate after welding helps refine the weld structure.
- Strong Welds
The welding process does not require electrodes or filler wires, and the heat source is hot, leading to a reduction in impurity content and a change in the size and distribution of inclusion in the molten pool. This results in a strong, tenacious weld that is at least equal to or even stronger than the parent metal.
- Precise Control
The laser's small focus point allows for high precision in weld positioning. The laser output has no “inertia” and can be stopped and restarted quickly, making it ideal for welding complex parts with NC beam motion technology.
- Non-contact atmosphere welding
The non-contact atmosphere welding process involves a beam of photons that delivers energy to the part without any physical contact. This means that no external force is applied to the workpiece and the laser is not affected by magnetism or air.
(2) Advantages of laser deep penetration welding
- High welding speed and minimum deformation
The focused laser used in laser welding has a much higher power density compared to conventional methods, allowing for fast welding speeds and minimal heat-affected zones and deformations. This makes it possible to weld even difficult materials such as titanium.
- Efficient and Low Maintenance
The beam is easy to transmit and control, leading to less frequent replacement of the welding gun and nozzle, and no vacuum pumping is required for electron beam welding. This significantly reduces auxiliary downtime and increases load factor and production efficiency.
- High strength and resistance
Purification and high cooling rate during laser welding result in high strength, toughness and comprehensive properties of the weld.
- Cost benefit
The low average heat input and high machining precision of laser welding help reduce the cost of reprocessing. Furthermore, the low operating cost of laser welding also helps reduce the overall cost of processing the part.
- Easy to Automate
Laser welding allows effective control of beam intensity and precise positioning, facilitating the automation of the welding process.
(3) Disadvantages of laser deep penetration welding
- Limited welding depth
- Strict requirements for assembly of parts
- Significant initial investment in laser system