The consumer electronics and automotive industries play a crucial role in increasing the use of copper in industrial processing and product manufacturing.
As new battery technology with improved capacity is developed, the need for compatible connection technology also increases.
Although soft soldering is still the main technology for low-power electronic applications, it must be used in situations where high transmission currents or high loads and dynamic stresses are present at the joints.
This trend is particularly influenced by the electric vehicle industry and its suppliers, who are looking for robust and efficient processes for mass production operations, such as energy storage and in-line transmission.
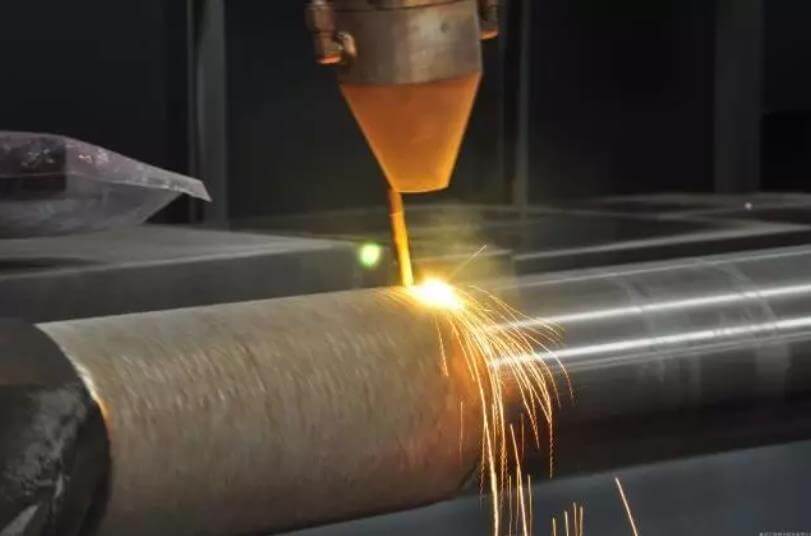
In the past, the physical properties of copper and copper alloys limited the use of laser technology for welding.
However, the advent of high-power, high-brightness fiber lasers has overcome these limitations.
With the development of new and appropriate processing technologies, stable and defect-free joints can be produced through an efficient welding process.
Near infrared laser, copper welding challenge
Difficulties in laser welding of copper arise from two of its physical properties: low absorption of most high-power industrial lasers and high thermal conductivity during the process.
The absorption of copper increases as the wavelength decreases, making visible band lasers, such as green lasers with a wavelength of 532 nm, suitable for welding copper. However, these lasers are not available or have not been extensively tested for the power range required for most welding applications.

Fig. 1: Defect-free copper welding via high-speed beam oscillation process
Infrared lasers face absorption issues when working with solid materials.
During deep penetration welding, if the material melts or evaporates, its absorption rate increases greatly.
The absorption rate of solid copper is less than 4%, but the absorption rate of copper vapor (generated during deep penetration welding) is more than 60% (see table below).
This absorption problem can be solved by using a very high power density, which accelerates the melting and evaporation of copper and therefore increases its absorption.
Table: absorptivity of copper to infrared laser radiation under different states.
state | Absorption rate (%) |
Solid | 40 |
Liquid | 10 |
Keyhole penetration | >60 |
High-speed video analysis demonstrates that a stable process can be established in less than 1 millisecond.
For continuous wave (CW) welding, this challenge must be overcome early in the welding process. Once the keyhole welding process is established, it provides a consistent high absorption rate. In pulsed operation, this obstacle must be overcome at the beginning of each pulse.
The high power density required for welding can be achieved using a single-mode fiber laser. This type of laser has superior beam quality and focusing performance compared to other solid-state lasers.
IPG offers high-power single-mode lasers up to 10 kW and high-brightness multimode lasers greater than 10 kW, with solid, industrially tested designs.
By using these single-mode fiber lasers and high-brightness lasers in low-order mode, intensities greater than 108W/cm² can be achieved. Reliable coupling can be achieved even at power levels of hundreds of watts.
Compared to ordinary multimode lasers with the same power, the intensity of these lasers is up to 50 times greater.
IPG offers the YLR series of single-mode fiber lasers with a power range of 100W to 1000W, housed in a compact 19″ housing. The company also provides the YLS series of fiber lasers with power up to 10 kW (Figure 2).
The overall efficiency of both series is 40%.
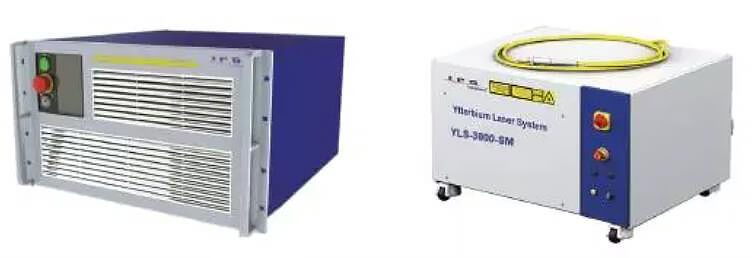
2: High power single-mode fiber laser: air-cooled rack type YLR-1000-SM (left) and 3KW system type YLS-3000-SM (right).
Another problem with the copper welding process is the instability that occurs at low welding speeds.
Typically, welding speeds below 5 meters per minute face instability problems such as spatter, porosity and uneven weld surfaces.
However, as the welding speed increases, these instabilities gradually disappear.
At welding speeds between 5 and 15 meters per minute, the quality reaches an acceptable level.
If the welding speed exceeds 15 meters per minute, the resulting weld will be virtually free of defects (Figure 3).
This suggests that ideal welding parameters are within the capabilities of traditional motion systems such as robots.

Fig. 3: Effect of processing speed on weld quality and depth.
New research has shown that process stability can be achieved not only by increasing welding speed, but also by dynamically changing the position of the beam guide lens.
This oscillating technology allows the formation of stable solder joints at relatively low welding speeds and significantly reduces the depth of the weld.
Through this technology, a high-quality copper weld with a depth of up to 1.5 mm can be obtained using just a single-mode fiber laser with a power of 1KW.
The same technology can be applied to high-brightness multimode lasers.
A 6 kW fiber laser with a beam quality of 2 mm mrad was used in the tests and it was found that it was possible to obtain high quality welding with a weld depth of 5 mm.

Fig. 4: Oscillating welded joints of the FLW-D30 and FLW-D50 series launched by IPG
Dynamic beam control can be achieved through the use of a traditional sweeping galvanometer or a new oscillating head, which combines the benefits of a proven welded joint and a sweeping galvanometer.
These galvanometers can easily incorporate pre-programmed shapes such as circles, lines, or a “figure 8” as well as freely programmable shapes within a certain size.
One of its main advantages is that it can use a standard focus lens instead of an f-theta field mirror and can handle higher power density at a lower focus shift level.
Furthermore, the use of conventional transverse air curtain and protective window reduces the cost of consumables.
The FLW-D50 and FLW-D30 series of oscillating welded joints launched by IPG can operate at oscillating frequencies up to 1 kHz and can be seamlessly integrated into various processing systems (Figure 4). These welded joints can withstand laser powers of up to 12 kW.
And experimental result
When welding a complex path with changes in welding direction, the circular oscillating motion produces the best results.
The final beam speed can be precisely controlled via the oscillation frequency and the oscillation diameter (VC = πD f).
In most cases, the impact of the welding speed vector (VW) on the dynamic positioning of the circular beam speed (VC) is minimal, as the beam speed is much faster than the welding speed (VW).

Fig. 5: Effect of oscillation amplitude on weld width and quality
The ideal frequency setting depends on the spot size, the oscillation diameter (and the resulting circular beam velocity, VC), and the linear welding speed.
Figure 5 illustrates the welding surface under constant power, frequency and welding speed, but with varying oscillation diameters.
The spot size is approximately 30 μm at a focal length of 300 mm. The laser power is kept constant at 1kW and the linear welding speed is set at 1 meter per minute.
Without oscillating motion, these parameters would result in an unstable process such as weld pools and overheated pores.
As the turning diameter increases and the circular beam speed improves, the surface quality becomes more and more stable.
Depending on the oscillation parameters and spot size, the beam and keyhole can move both in the metal bath and in solid and resolid materials, and the process can still achieve stability in both cases.
The weld cross section shows another advantage of this technology: the turning diameter can be used to shape the weld cross section.
A small oscillation diameter forms a V-shaped cross section typical of laser welding, while a larger diameter can transform the weld from a V shape to a U shape or a regular rectangle (Figure 6).
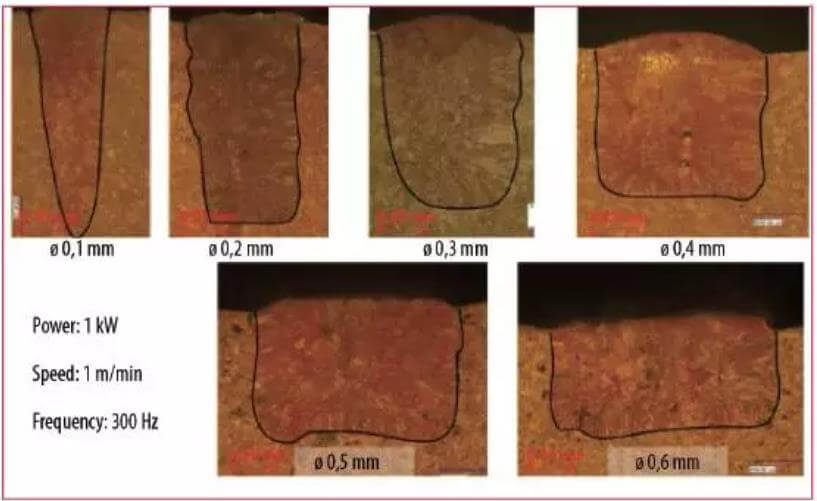
Fig. 6: Effect of oscillation amplitude on the weld cross section
When the energy input per unit length of the weld remains constant (E = P vw), the cross section of the weld remains almost unchanged. This technology makes it possible to meet specific cross-section requirements for various applications.
In the case of overlap welding for electrical contacts, resistance can be decreased by increasing the contact area and properly controlling the welding depth and heat input.
When welding different materials such as copper and aluminum, the melting rate of the materials can be regulated by controlling the depth of welding. By superficially melting the bottom metal plate, the amount of molten material can be kept to a minimum and the formation of intermetallic compounds can be reduced by controlling the dilution ratio.
Pulse, continuous or both?
In recent years, long-pulse fiber lasers with pulse durations of several milliseconds have been introduced to the market, replacing traditional flash lamp-pumped Nd:YAG lasers in a wide range of applications. These lasers include single-mode lasers with average power of 250 W and peak power of up to 2.5 kW.
Previously, the issue of copper pulse welding was discussed. It is crucial to resolve the problem of weak absorption at the start of the pulse and subsequent difficulties in controlling energy input due to sudden changes in absorptivity and heat conduction.
Using a single-mode laser to reduce spot size can overcome the absorption problem, but at the same time, the concentrated energy input can result in small, weak solder joints and overheating of the casting.
The solution to this problem is simple and similar to the process used for continuous lasers. The same swing technology can be applied to quasi-continuous (QCW) lasers.
The movement of the high-frequency beam causes the laser beam to move a relatively long distance in a relatively short pulse time, effectively performing nearly continuous welding during one pulse. For example, a long pulse of 20 ms at an oscillation frequency of 600 Hz can produce circular solder joints or short wire welding consisting of twelve rotating beams.
By adding pulses one by one to linear welds, high-quality copper welding can be achieved with low average power and a corresponding low investment cost. Solidification and remelting between pulses will not lead to welding defects such as pores, heavy spatter or uneven penetration depth.
The turning diameter determines the size and depth of the weld, and the heat input is much less, making it easier to weld important electrical components with a pulsed fiber laser.
Summary
Experiments have shown that high-brightness fiber lasers can effectively solve all known problems in copper welding applications. The high power density of these lasers allows the instantaneous formation of keyholes and guarantees stability and high absorptivity, even at the wavelength of 1070nm.
Through dynamic beam oscillation, the welding process is highly stable, reducing or eliminating porosity and spatter to produce high quality welds. Beam oscillation parameters can also be adjusted to control welding geometry, resulting in shallow welds in deep penetration welding processes.
Using a long-pulse, quasi-continuous fiber laser, spot welding can be performed in a single pulse through high-speed dynamic movement of the beam. By gradually increasing the number of pulses, high quality welds can be achieved at a low average power.