It has been demonstrated through examples that metal and plastic can be effectively “connected” using laser welding.
It should be noted that the term “soldier” is not entirely accurate and should be replaced with “connected”.
As shown in Figure 1, the car door is reinforced with fiberglass plastic.
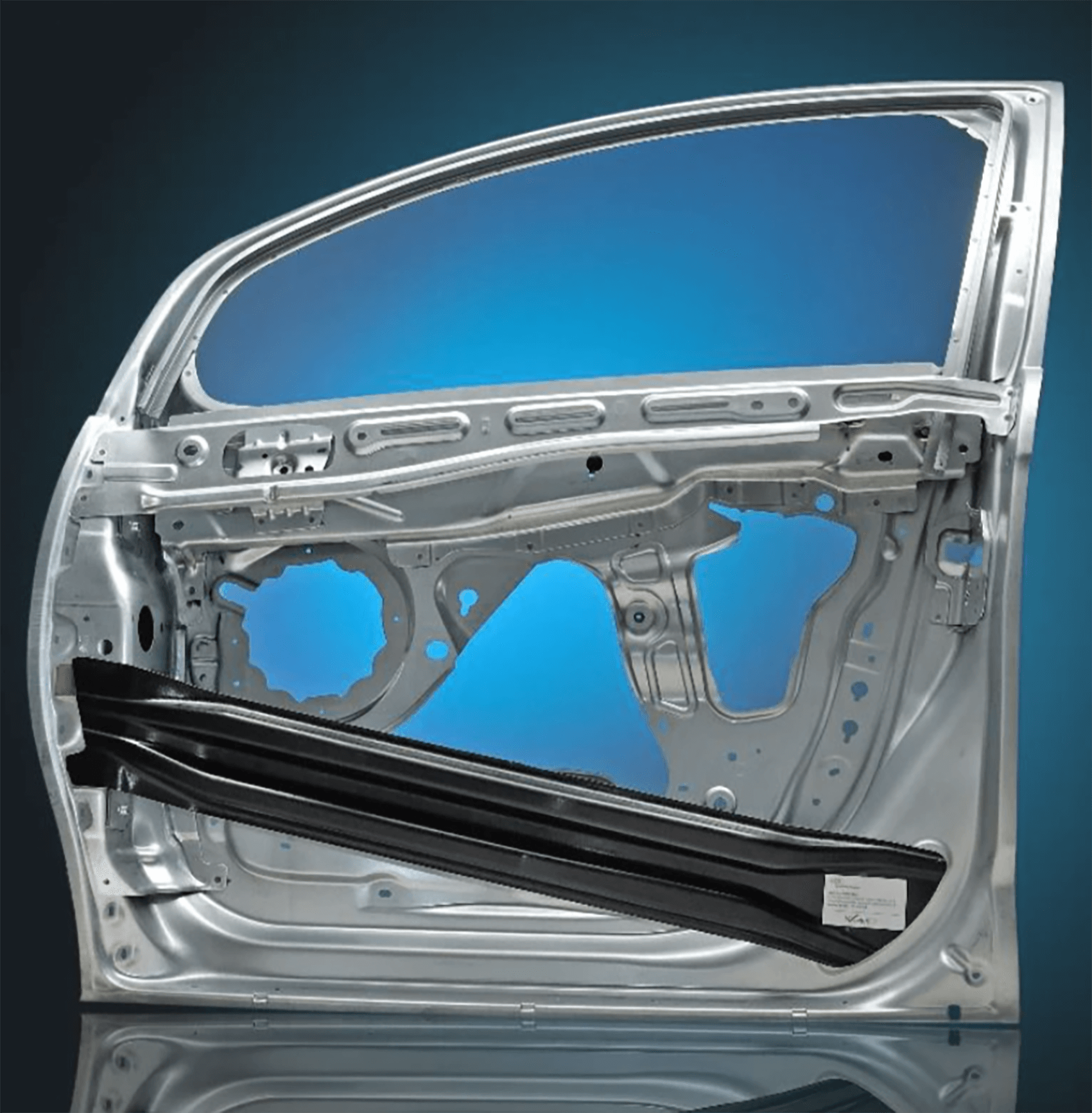
Fig. 1 Car door reinforced with fiberglass plastic
With the increasing focus on weight reduction in the automotive industry, there is a growing need for effective connections between metal and plastic components, particularly those containing reinforced carbon fiber or glass fiber.
To meet the demands of fast-paced assembly line operations in the automotive industry, a solution for fast, reliable and automated connections between these materials is needed.
The following are three of the most commonly used methods for joining composite and metal parts in industry: (list the methods).
Of these, laser-based connection technology is the most recent advancement. However, despite its potential, there are still several challenges that must be faced with this technology, including issues related to efficiency, joint resistance and aging. This article will provide an in-depth examination of these challenges.
(1) Mechanical Connection: This method is fast, economical and provides a stable connection. However, the process of creating holes in the composite material can disrupt the fiber distribution and weaken the overall strength of the composite. Additionally, using connectors like screws adds weight to the assembly.
(2) Bonding: There is a wide variety of adhesives available to connect various materials. However, the surface must be pre-treated, the bonding process takes longer, adhesive must be used, which increases the overall bonding cost.
(3) Laser Connection: The laser connection is fast, reliable and provides a strong connection without the need for auxiliary materials. However, it is currently limited to use with thermoplastics only.
1. Basics of laser connection technology
The laser connection process of thermoplastic and metallic parts involves two steps.
In the first step, a microstructure is formed on the surface of metal parts through laser processing. This is typically accomplished using a 1 kW fiber laser.
The laser scans the surface and creates a regular pattern of grooves and indentations (as shown in Fig. 2).
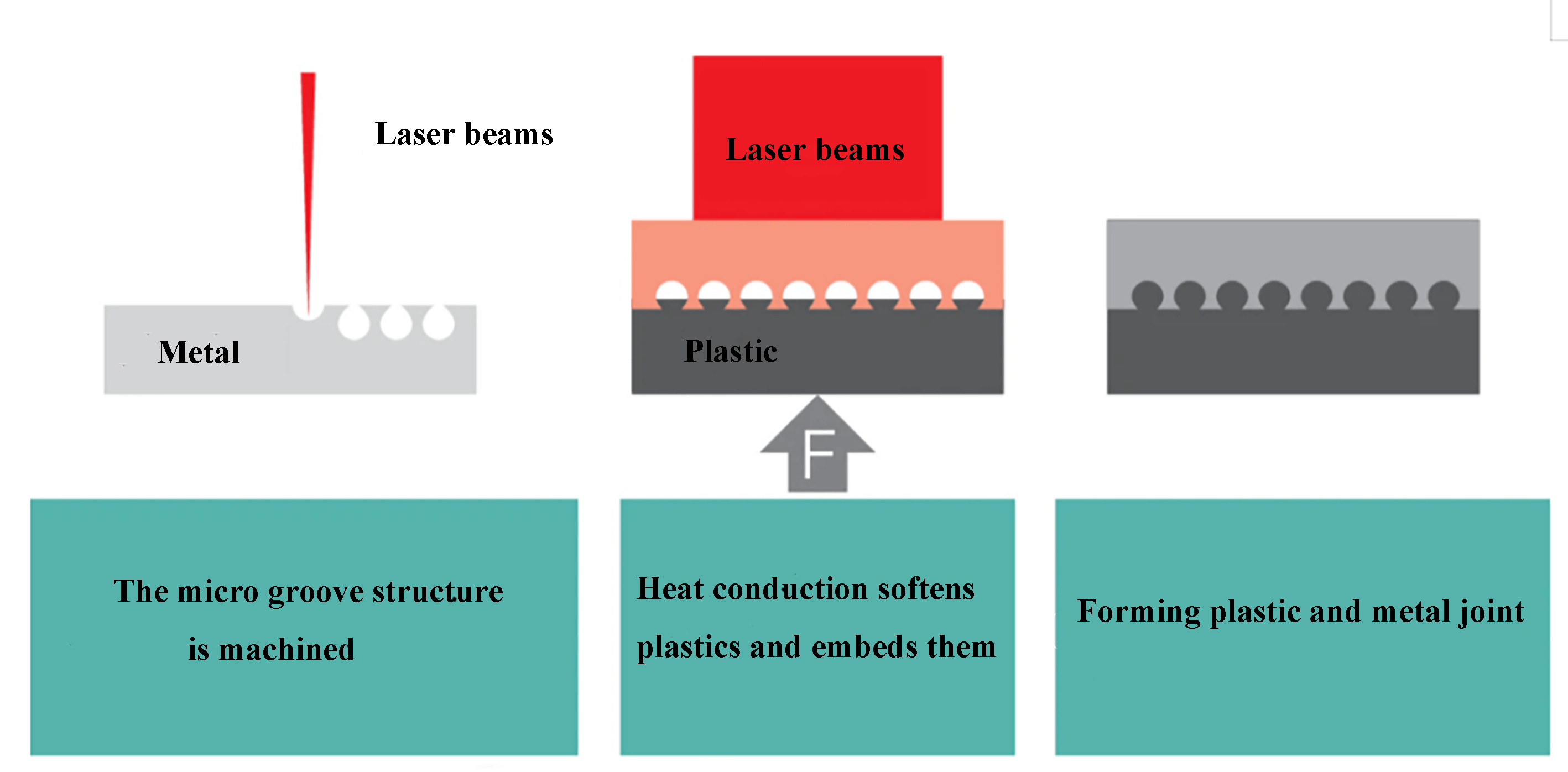
Fig. 2 Plastic and metal laser bonding process
The high power density of the laser beam causes partial melting and evaporation of the metal during ablation. The molten metal is expelled by high-pressure evaporation and solidifies at the edge of the grooves to form the scalloped structure.
To increase the adhesion of the plastic to this surface, the number and density of grooves can be increased, as shown in figure 3.

Fig. 3 Multiple laser beam scans to obtain a good groove shape
An alternative method involves using a special ultrashort pulse (USP) laser to create a spongy surface with conical protrusions. This technique can be applied to steel, aluminum, silicon and titanium surfaces, resulting in improved bond strength for plastics compared to surfaces processed with fiber lasers. However, the only challenge is that the USP laser operates at a slower speed.
In the second stage, the plastic is heated until it melts and then pressed onto the metal surface. After cooling, the plastic is firmly bonded to the metal.
There are several methods for heating plastics, such as using a hot plate, infrared radiation or other processes to directly heat the plastic, or heating metal parts and pressing them onto cold plastic, causing the plastic to melt and flow into small structures through heat conduction.
The first step of laser micromachining is fast and contactless, making it ideal for integration into existing production processes and mass production.
2. Connection strength test
In practical applications, the joint between metal and plastic will be subjected to loads. What is the maximum pressure this type of composite connection can withstand and where will it fail?
The Hoff Laser Technology Research Institute in Germany conducted a series of stress tests on various materials to answer these questions (Figure 4).
One of the test contents is as follows:
- The shear test was carried out on a 1.5mm stainless steel plate and a 3mm PP plastic connector with fiberglass.
- A tensile test was performed on a 1.5mm stainless steel plate and a 3mm PP plastic connector (excluding fiberglass).
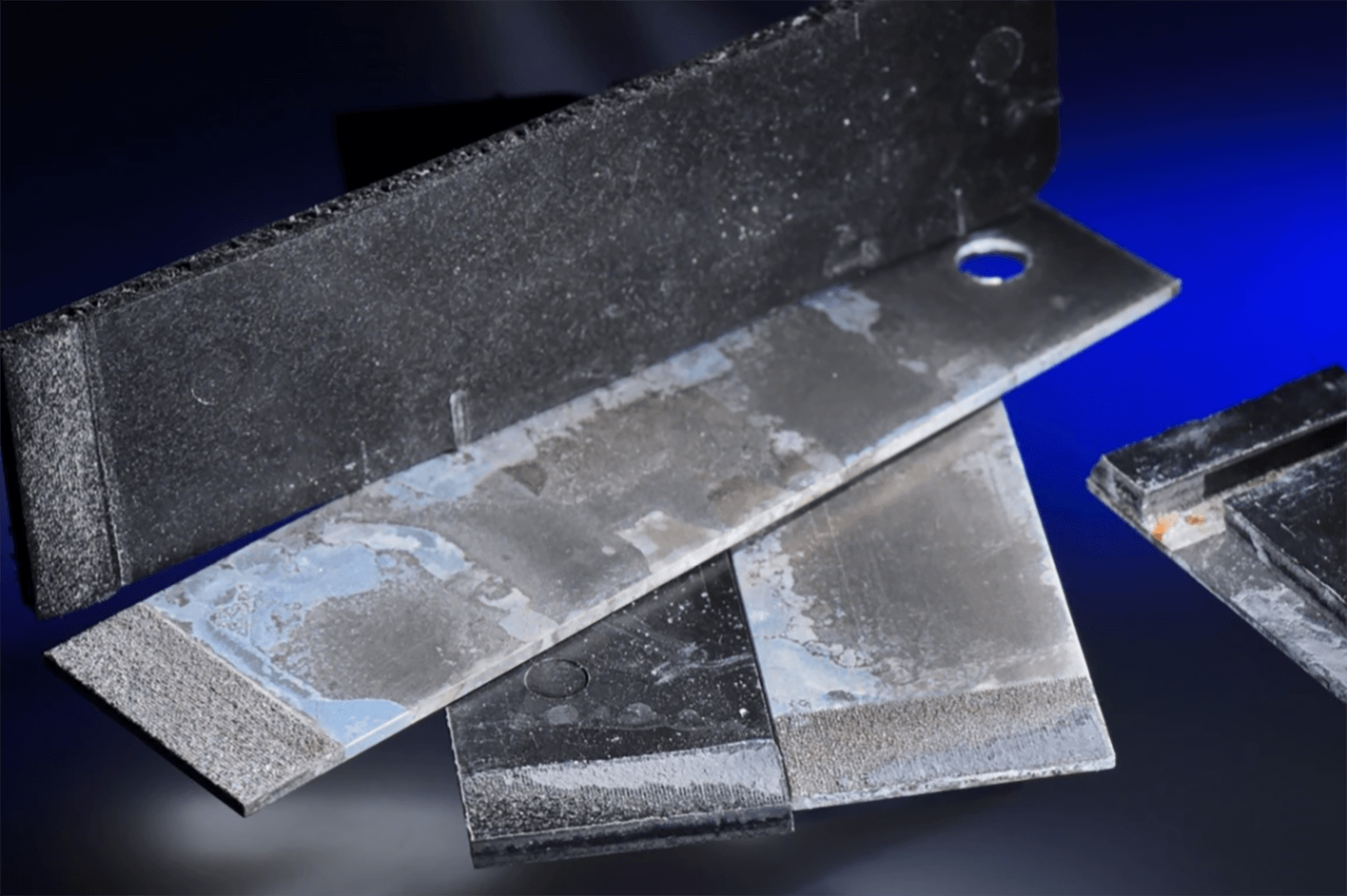
Fig. 4 Fracture surface of metal and plastic joint after corrosion test
A 1 kW single-mode fiber laser is used to microprocess the metal surface, with a spot diameter of approximately 40 micrometers. The laser produces a reproducible groove structure on the metal surface. The plastic is heated using a semiconductor laser of nominal power of 3 kW, with a spot size of 7.5 mm x 25 mm. The two parts are fixed with a pressure of 0.3 MPa.
The test results are as follows:
- For the connection between stainless steel and PP with fiberglass, the connection area is 150 mm².
- For the connection between stainless steel and PP, the connection area is 100 mm².
Destructive tests were carried out on 5 samples of each of the above two types.
For the connection between stainless steel and PP with fiberglass, a shear strength test was carried out. The results are as follows:
- When the groove spacing was 400 micrometers, the maximum shear load was 13.1 MPa.
- When the groove spacing was 300 micrometers, the maximum shear load was 15.5 MPa.
For the connection between stainless steel and PP, a tensile strength test was carried out. The results are as follows:
- When the groove spacing was 400 micrometers, the maximum tensile load was 5.1 MPa.
- When the groove spacing was 300 micrometers, the maximum tensile load was 9.1 MPa.
It is evident that a dense distribution of grooves improves the strength of the connection. However, it should be noted that a dense distribution of channels will also increase the micromachining time.
A similar experiment was also conducted on a magnesium sheet.
All tests demonstrated that the laser-based bonding technology creates a strong and reliable connection between metal and plastic components.
3. Aging test
Another important concern in automotive products is their resistance to the impacts of climate change and corrosion. To answer this question, experts from the Hoff Laser Technology Institute in Germany carried out several tests.
In the experiment, various metals (steel and aluminum) and plastics (PP with 30% glass fiber and PP with 40% talc) were connected using laser technology. For the climate change test, the VW PV 1200 standard was used, with temperatures ranging from 80°C to 40°C.
Each test cycle lasted 12 hours and was repeated twice, 10 times and 30 times, respectively. The destructive shear strength of the samples was tested before and after each cycle. The results showed that all samples presented shear strength ranging from 8 to 15 MPa.
An interesting observation was made in the test: after 30 cycles, all PP samples filled with talcum powder showed cracks outside the connection area during the strength test, indicating that the joint was stronger than the bulk PP material.
A similar result was observed in the corrosion resistance test, which was conducted in accordance with VDA 621-415 over 7 days, including salt spray and high humidity conditions. Before testing, all samples had a shear strength of 8-5 MPa. After the corrosion test, the shear test showed that all the PP samples containing talcum powder had cracks outside the connection area, while the PP sample containing glass fiber broke in the joint area, but its strength was higher than that. than before the test.
Corrosion was observed on the stainless steel, especially its microstructure, and the laser bonding area showed obvious corrosion penetration but had no significant effect on the bonding strength. There were also signs of corrosion in the microstructure outside the joint area, but not within the joint area.
Therefore, it can be concluded that the microstructure should not be exposed to open environments.
4. Conclusion
The technique of connecting metal and plastic using laser technology has been tested and shown to produce strong and reliable connections. Weather and corrosion test results showed no impact on joint strength. After aging, the samples showed that the fractures occurred in the plastic body, and not at the connection point.