This article mainly introduces several mature special processing methods.
I. Electrical Discharge Machining (EDM)
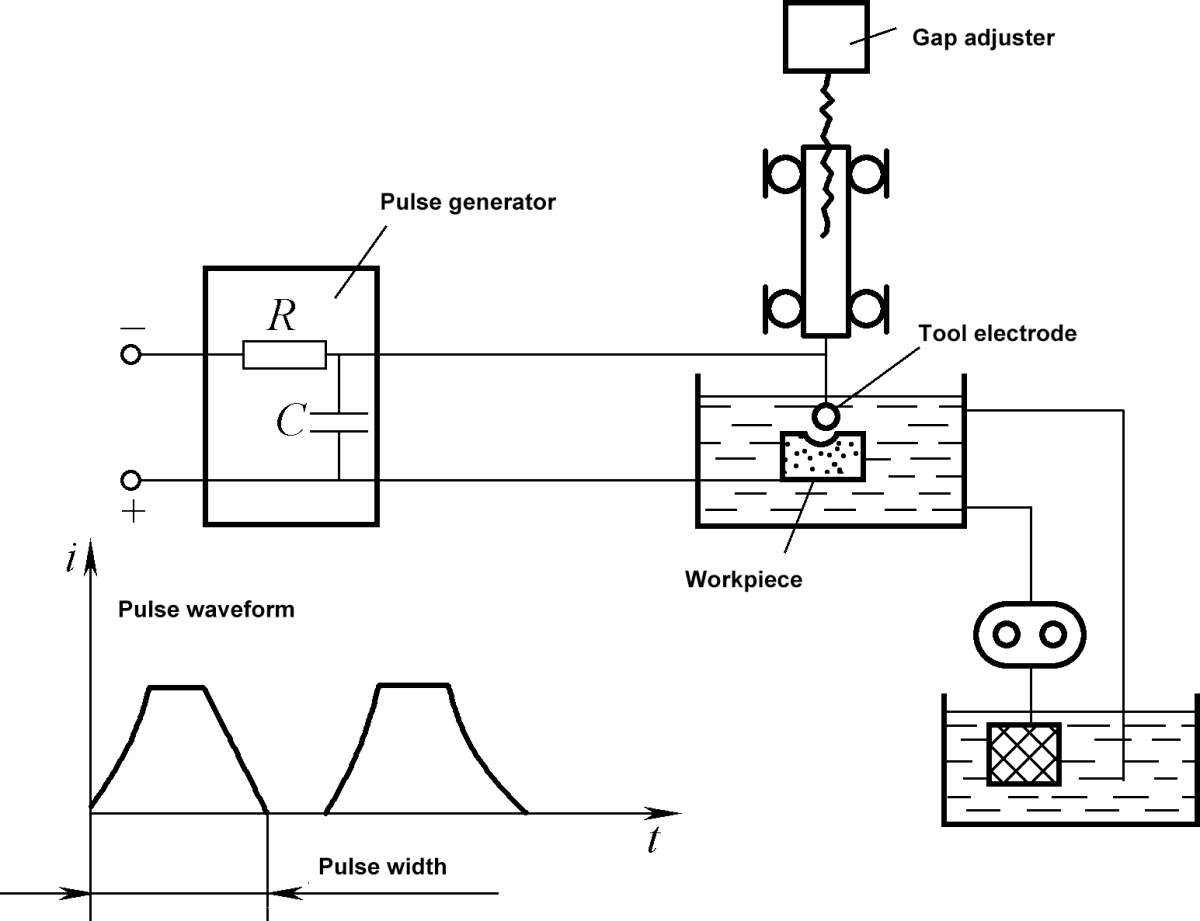
EDM is a method of machining conductive materials that utilizes the phenomenon of electrical corrosion during pulse discharge between positive and negative electrodes in a given liquid medium. This makes the dimensions, shape and surface quality of the parts meet technical requirements. It is also known as discharge machining or EDM machining. The working principle is shown in Figure 8-41.
During EDM, the workpiece and tool (made of pure copper or graphite), which are charged with pulse voltage, act as positive and negative electrodes, respectively. When they are close together in the insulating working fluid (kerosene or mineral oil), the electrode voltage will be broken at the closest point between the two electrodes, forming a pulsed discharge.
The high temperature generated in the discharge channel causes the metal to melt and vaporize, and the molten metal is expelled under the effect of the discharge explosion force and carried away by the insulating working fluid.
Due to the polar effect (i.e., the unequal erosion amounts of the two electrodes), the erosion speed of the workpiece electrode is much higher than that of the tool electrode. Therefore, during the EDM process, if the tool electrode is continuously fed into the workpiece, the machining of the workpiece can be completed accurately according to the shape of the tool.
(1) Features of the EDM process
1) It can process any hard, brittle, tough and high melting point conductive materials such as hard alloys, hardened steel and stainless steel.
2) There is no significant mechanical force during processing, which is beneficial for machining small holes, thin walls and parts with various complex cross-sectional shapes and cavities.
3) Pulse parameters can be adjusted, allowing rough and fine machining on the same machine.
4) The machining size accuracy can reach 0.01mm, and the surface roughness Ra value is 0.8μm. For micro-precision machining, the size accuracy can reach 0.04 ~ 0.002 mm, and the surface roughness Ra value is 0.1 ~ 0.05 μm.
5) EDM has a slow processing speed, and the tool electrode suffers from wear, affecting the processing efficiency and forming accuracy.
(2) EDM Applications
EDM is used to machine various cross-sectional shapes of molded holes, small holes; machining of various forging molds, extrusion molds, die casting molds and other molded cavities, integral impellers, blades and various curved surface parts; surface reinforcement and engraving; and for electrical discharge wire cutting processing.
II. Electrochemical Machining (ECM)
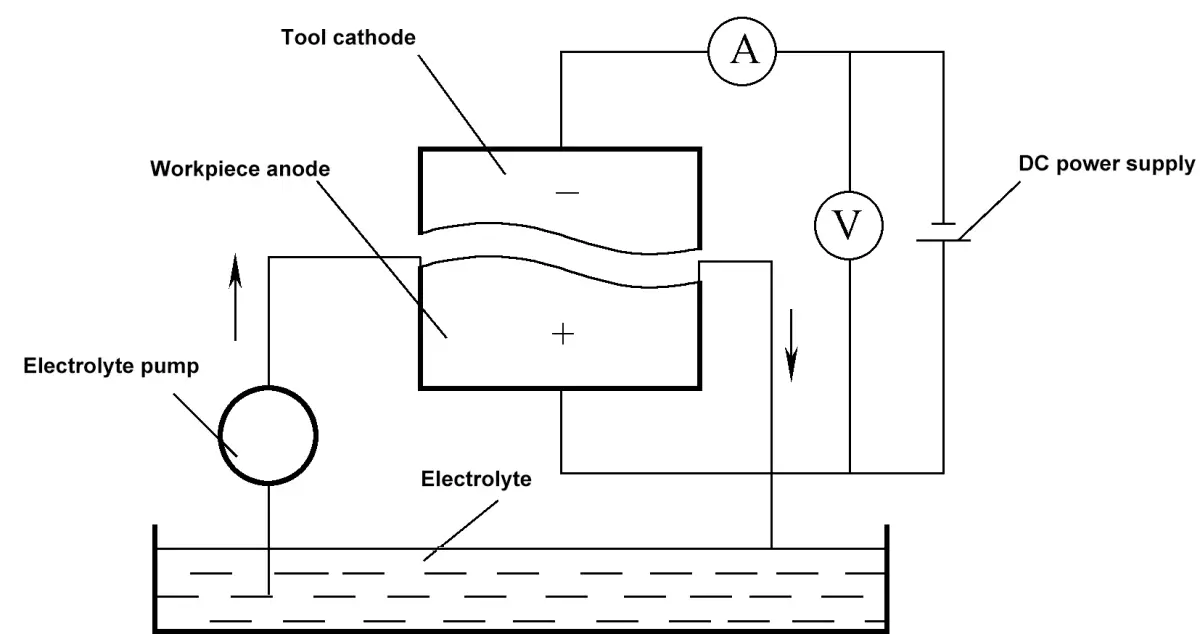
ECM is a method of forming a part using the principle of an electrochemical reaction, where the metal dissolves as an anode in the electrolyte. As illustrated in Figure 8-42, during ECM, the workpiece is connected to the positive terminal and the tool electrode to the negative terminal, with a low voltage and high current passing between them.
A high-velocity electrolyte is injected into the narrow space between the two terminals. As the tool electrode continuously feeds the workpiece, the workpiece material dissolves into the shape of the tool surface due to the anodic dissolution of the metal in the electrolyte. The electrolysis products are then removed by the high-speed electrolyte flow, thus creating a shape on the part that matches the surface of the tool.
(1) ECM Process Features
1) It can machine high hardness, high strength and high toughness metals such as hardened steel, hard alloy and stainless steel with high production rates.
2) There are no cutting forces or cutting heat, making it suitable for machining easily deformable parts (such as thin-walled parts).
3) The average machining accuracy can reach 0.03 ~ 0.05mm, and the surface roughness Ra value can reach 1.6 ~ 0.2μm, without residual stress.
4) In theory, the tool's cathode does not wear out during the process, allowing for long-term use.
5) The electrolyte corrodes the machine tool, and the electrolysis products are difficult to treat and recycle.
(2) ECM Applications
ECM is widely used for deep hole drilling, hole enlargement, spline hole drilling, small size and complex shape hole drilling, low precision cavity mold processing, irregular part suppression, deburring and electrochemical chamfering.
III. Ultrasonic Machining (USM)
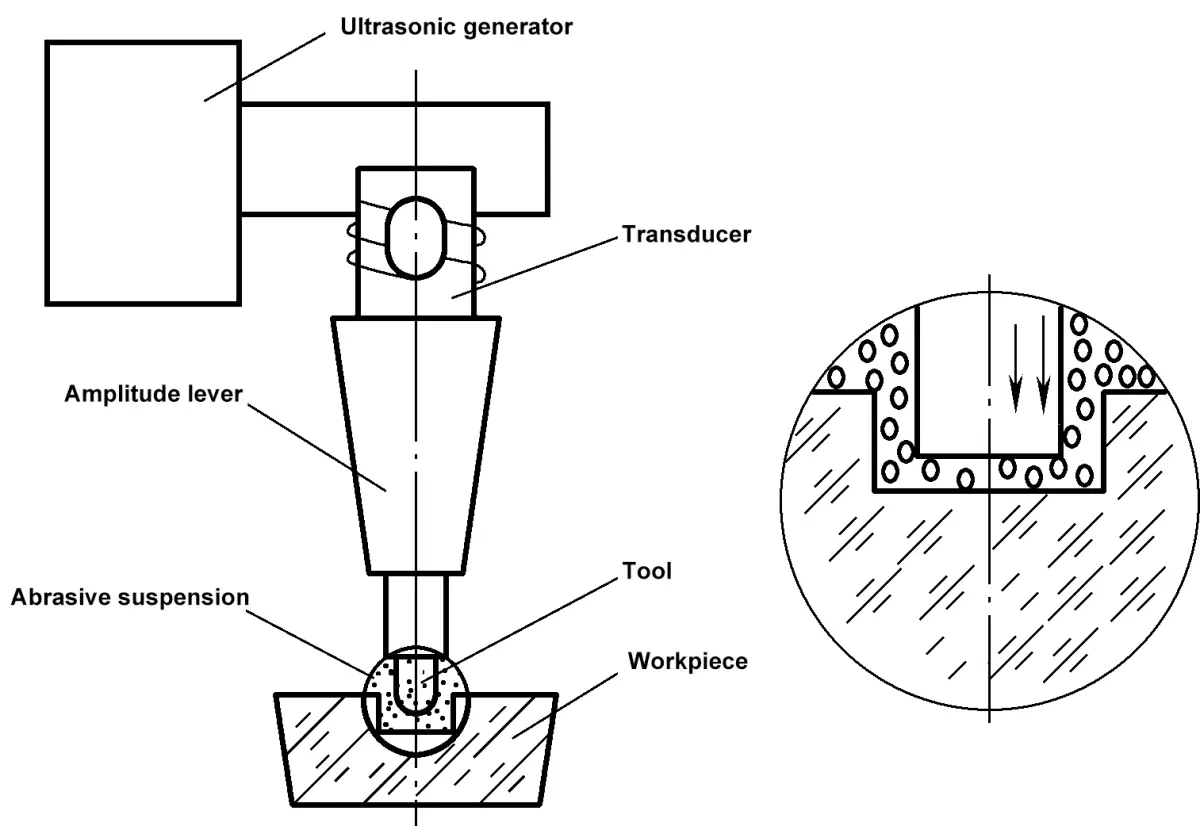
USM is a method of machining a part using high-frequency vibrations on the tool face and abrasive mud. As shown in Figure 8-43, the ultrasonic generator creates high-frequency electrical oscillations that are transformed into small-amplitude ultrasonic mechanical vibrations by the transducer. The amplitude is then amplified to 0.01~0.15mm by the amplitude rod and transferred to the tool to make it vibrate.
Meanwhile, the abrasive paste is continuously injected between the workpiece and the tool. The ultrasonic vibrating tool face continuously hammers the abrasive into the surface of the part, spraying the material into the machining area into fine particles that are removed by the circulating abrasive slurry. The tool gradually enters the workpiece, replicating its shape on the workpiece.
(1) Features of the USM process
1) It is suitable for machining various non-conductive, hard and brittle materials such as glass, ceramics, gemstones and diamond.
2) It is easy to machine various complex shapes of holes, cavities and forming surfaces, and with a hollow shape tool, various shapes of blanks can also be obtained.
3) The cutting force and thermal effect are small, making it suitable for machining thin walls, narrow gaps and other low rigidity parts.
4) Common USM equipment is simple.
5) The accuracy can reach 0.05 ~ 0.01mm, and the surface roughness Ra value can reach 0.8 ~ 0.1μm, but the production rate is relatively low.
(2) USM Applications
USM is suitable for machining thin-sheet parts with thin walls and narrow gaps; It is widely used for drilling, cutting, slitting and engraving of hard and brittle materials and machining of diamond drawing dies; in combination with other machining methods, it can also perform composite machining.
4. Laser Machining
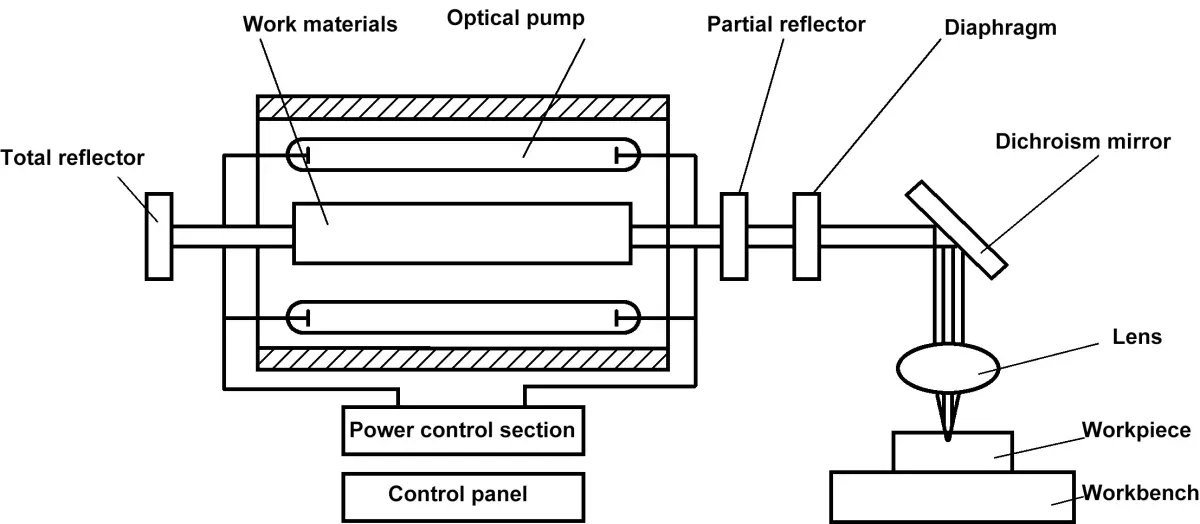
Laser machining is a machining method where a laser is used, a coherent light with good monochromaticity, strong directionality and excellent focusing performance. After focusing, the power density reaches 10 8 ~10 12 C/cm 2 and the temperature reaches more than 10,000 ℃.
The laser irradiates the material being machined, causing it to melt and even vaporize instantly, and strong shock waves are generated, explosively removing the material. The working principle of laser machining is shown in Figure 8-44.
(1) Laser machining process features
1) Laser machining has a short action time, small heat-affected zone, is not affected by electromagnetic interference, and can process almost all metallic and non-metallic materials.
2) The machining speed is extremely high, easy to carry out automated production and assembly line operations, and the thermal deformation is also very small.
3) The process does not require the use of tools and is a non-contact machining method, without mechanical deformation during processing.
4) Can process through air, inert gases or optically transparent media.
5) The machining accuracy can reach 0.01mm, and the surface roughness Ra value can reach 0.1μm.
(2) Laser machining applications
1) Laser machining is mainly used for machining small holes in materials such as diamond drawing dies, watch and jewelry bearings, ceramics, glass, hard alloys and stainless steel. The hole diameter is generally 0.01~1mm, and the smallest hole diameter can reach 0.001mm; the hole depth-diameter ratio can reach 50 ~ 100.
2) Laser machining is used for cutting, and the material thickness can reach several tens of millimeters. It can also cut the filament inside a vacuum tube through the glass. It can weld through glass, which is difficult to achieve with any other mechanical machining. By scanning the surface of the part material with a laser, surface heat treatment of the material can be carried out, such as laser hardening of the surface of low carbon steel.