What is CNC machining?
Numerical Control (NC) refers to the method of controlling the movement and processing operations of machine tools using digitized information. Numerical control machine tools, often abbreviated as NC machine tools, are machine tools equipped with an NC system. Computer Numerical Control (CNC) is a method in which a general-purpose computer directly controls the movement and processing operations of machine tools.
By changing the corresponding control program, the control function of the CNC system can be changed without changing the hardware circuit, making the CNC system highly versatile and flexible. This is the direction of development of NC technology, and it has found wide application in production.
Numerical Control Machining refers to a method of processing parts on NC machine tools. The machining process of NC machine tools is generally consistent with the processing of traditional machine tools, but due to the unique characteristics of NC machining, there are notable changes in the NC machining process compared with general machining processes.
CNC machining refers to the manufacturing and processing of parts and products controlled by computers. It involves using computer numerical control (CNC) machine tools to automatically remove excess material from a workpiece, processing and adjusting it.
Metal is the most commonly used material in CNC machining and the end result is a finished product or part.
This process is known as subtractive manufacturing and computer applications are used to control machine tool movements for better CNC machining. The most common processing types and processes for CNC machine tools include milling, turning, grinding and EDM.
Milling uses a rotating cutter to remove material from the surface of the part by moving along 3, 4, or 5 axes. This process is used to quickly process complex geometric shapes and precision parts with metal by cutting or trimming the workpiece.
Turning, on the other hand, involves using a lathe to manufacture parts with cylindrical features. The workpiece rotates on the axis and contacts the precision turning tool to form circular edges, radial and axial holes, grooves and grooves.
Compared with traditional manual machining, CNC machining is much faster, with high dimensional accuracy and minimal errors. The finished product meets the design computer code.
CNC manufacturing can be used to manufacture final products and components, but is generally only economical for short-term, low-batch production, making it an ideal rapid prototyping manufacturing method.
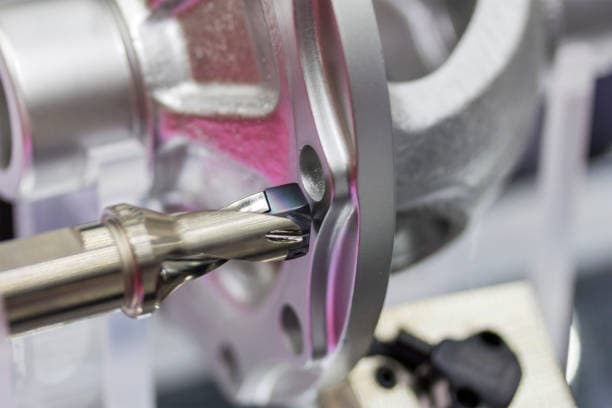
Multi-axis CNC machining
NC milling is a process that uses rotating cutters to remove materials. The part can remain stationary while the tool moves over it or enter the machine tool at a predetermined angle.
The complexity and speed of the forming process depend on the number of moving axes the machine has. The more axes a machine has, the faster and more complex the process can be.
3-axis NC machining
3-axis NC milling is still one of the most used and popular machining processes.
In 3-axis machining, the part remains stationary and the rotating cutter cuts along the X, Y, and Z axes.
This machining method is relatively simple and can produce products with simple structure. However, it is not suitable for machining complex geometries or products with complex components.
Since cutting can only be performed in three axes, the processing speed may be slower than 4-axis or 5-axis NC machining. This is because the workpiece may need to be manually repositioned to achieve the desired shape.
4-axis NC machining
4-axis NC milling adds a fourth axis to the cutting tool movement, allowing rotation around the X-axis.
This method involves the use of four axes: the X-axis, the Y-axis, the Z-axis and the A-axis (rotating around the X-axis).
Most 4-axis CNC machines also have the ability to rotate the part, known as the B axis. This allows the machine to function as both a mill and a lathe.
If you need to drill into the side of a part or the surface of a cylinder, 4-axis CNC machining is the ideal choice.
Significantly improves the machining process and achieves high machining precision.
5-axis NC machining
5-axis NC milling has an additional axis of rotation compared to 4-axis NC milling.
The fifth axis is typically the B axis, which rotates around the Y axis.
Some 5-axis CNC machines also allow rotation of the part, known as the B-axis or C-axis.
Due to the high versatility of 5-axis NC machining, it is often used to manufacture complex and precise parts such as medical components such as artificial limbs or bones, aerospace parts, titanium parts, oil and gas mechanical parts, military products and much more. more. .
CNC machining process and CNC programming
A complete CNC machining process includes the following steps: process analysis based on the part processing drawing, determination of machining planes, process parameters and displacement data; write the parts processing program spreadsheet with prescribed program codes and formats; program entry or transmission; trial operation, tool path simulation, etc., of the machining program entered or transmitted to the NC unit; automatic operation of the machine tool through correct operation, first sample trial cutting; inspection of processed parts.
CNC machining program is a sequence of instructions that drives the NC machine tool to perform machining and is the application software of the NC machine tool. The main tasks of CNC programming include part design analysis, process design, machining route planning, and determining machine tool auxiliary functions. It is an important step in CNC machining.
The contents and steps of CNC programming are shown below:
Part drawing analysis -> Determine process route for processing -> Tool path calculation -> Write programs -> Program input -> Program check and trial cutting
NC program compilation methods include manual programming and automatic programming.
1) Manual programming refers to the programming method where the entire process, from analyzing part drawings, formulating process procedures, calculating tool movement trajectories, writing part processing program spreadsheets, preparing From media control to program verification, it is all completed manually. For parts with less complex geometric shapes, simple calculations and few machining programs, manual writing is easy to implement.
Manual programming is the basis for compiling machining programs and also the main method for on-site machining debugging of NC machine tools. It is a basic skill that machine tool operators must master.
For parts with complex shapes, such as parts with non-circular curves and tabular curve contours, manual programming is tedious, the program volume is huge, the possibility of errors is high, the efficiency is low, and manual programming is not up to par of the task, therefore automatic scheduling must be adopted.
2) Automatic programming refers to the method in which most or part of the work of writing the program for NC machine tools is done by a computer. Automatic programming reduces the labor intensity of programmers, improves programming efficiency and quality, and solves complex part programming problems that manual programming cannot solve.
Depending on the different forms of information input and processing methods, automatic programming methods are mainly divided into language programming and interactive graphical programming.
Language programming uses a certain high-level language to define the part's geometric shape and feed path, with the computer completing complex geometric calculations or selecting tools, fixtures, and cutting quantities through a technology database. The most famous NC programming systems include APT (Automatically Programmed Tools).
Language programming does not provide an intuitive description of the geometric shape of the part, it is an early programming method used by NC machine tools and has been gradually replaced by interactive graphical programming methods.
Interactive graphical programming is based on certain CAD/CAM software, where the machining graphical definition and process parameter setting are completed through human-computer interaction, and then the programming software automatically processes to generate the tool trajectory. tool and CNC machining program.
Interactive graphical programming is currently the most commonly used method, with typical software systems including Mastercam, UG, Pro/E and other CNC programming systems.
CNC Machining Features
Compared with traditional mechanical machining, the advantages of CNC machining are:
1) High adaptability to the workpiece.
The shape of parts processed by CNC machine tools mainly depends on the processing program. When the part changes, a new program can be reprogrammed to process the parts, making it particularly suitable for single part production, small batches and prototype testing. Additionally, the controllable motion of CNC machining allows you to complete complex surface machining that is difficult or impossible for common machine tools.
2) High machining precision and stable product quality.
CNC machine tools have higher precision than ordinary machine tools. During the machining process, the automatic machining mode of CNC machine tools can avoid errors caused by human factors, resulting in good dimensional consistency, high precision and very stable machining quality for the same batch of parts.
3) High production efficiency.
The adjustment range of spindle speed and feed rate of CNC machine tools is much larger than that of ordinary machine tools. The rigidity of the machine tool is high, allowing large amounts of cutting, effectively saving machining time. The fast moving speed of the moving parts of the CNC machine tool reduces positioning and non-cutting time.
CNC machine tools move according to coordinates, saving auxiliary operations such as line drawing and reducing auxiliary time. The part is often installed in a simple positioning and clamping device, which shortens the design and manufacturing cycle of process equipment, thereby accelerating the production preparation process.
In CNC machine tools with a tool magazine and automatic tool changer, the workpiece can perform multiple continuous machining processes with a single clamping, reducing the turnaround time of semi-finished products and making the improvement in production efficiency more apparent.
4) High degree of automation.
Work intensity is low. The machining of parts by CNC machine tools is done automatically according to a pre-programmed program. The operator's main tasks are program editing, program entry, loading and unloading parts, preparing tools, observing the machining status and inspecting parts, without the need for heavy repetitive manual operations.
Therefore, the labor intensity is significantly reduced and the machine tool operator's work tends towards intellectual operations. Furthermore, CNC machine tools generally process in a closed, clean and safe manner.
5) Facilitates modern production management.
Programmatic control machining makes changing varieties convenient. Furthermore, multi-sequence machining on one machine simplifies production process management, reduces the number of management personnel, and can achieve unmanned production. Using CNC machine tools for machining can accurately calculate the working hours of a single product and organize production reasonably.
CNC machine tools use digital information and standard code processing to control machining, creating conditions for automation of the production process and effectively simplifying the transmission of information between inspections, work devices and semi-finished products.
Advantages and Disadvantages of CNC Machining
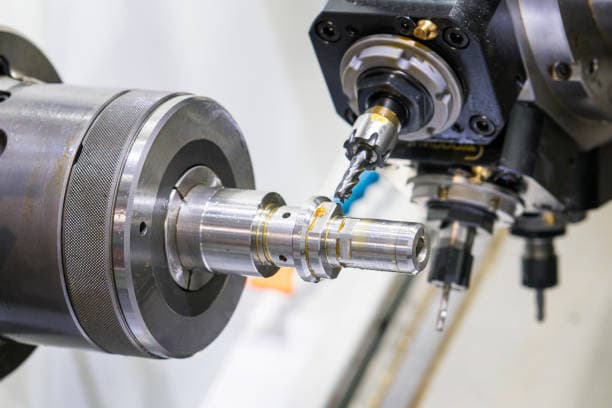
CNC machining has the following advantages:
① Reduce the number of tools required and eliminate the need for complex tools to process parts with complex shapes.
If you need to change the shape or size of a part, simply modify the processing program for that part, making it ideal for developing and modifying new products.
② The machining quality is consistent with high precision and repeatability, making it suitable for the rigorous requirements of aircraft machining.
④ It can efficiently handle complex profiles that are difficult to process using conventional methods, and can even work on parts that cannot be seen during processing.
Disadvantages of CNC machining
The disadvantage of NC machining is that the cost of machines and equipment is quite high and maintenance personnel must have a high level of expertise.
CNC machining steps
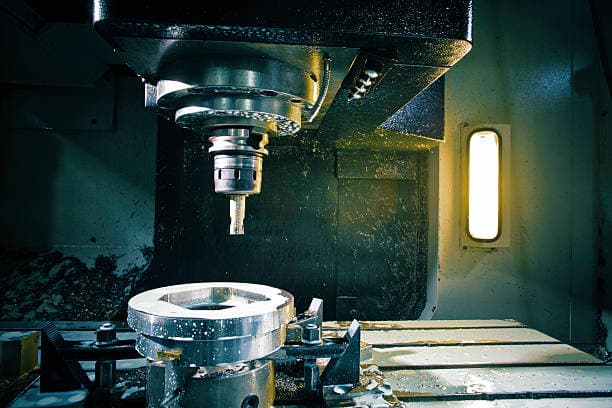
CNC machining is currently the most widely used machining method.
When carrying out CNC machining, it is important to not only understand its characteristics, but also the steps involved in the process in order to improve machining efficiency.
What are the steps involved in CNC machining?
1. Analyze processing drawings and determine the processing process
Based on the machining drawings provided by the customer, machining personnel can analyze the shape, dimensional accuracy, surface roughness, workpiece material, blank type and heat treatment status. This information is used to choose machine tools and tools, determine the positioning and clamping device, machining method, cutting sequence and parameters.
When determining the machining process, the control capabilities of the CNC machine tool used must be taken into account. This will maximize machine tool efficiency and result in a more efficient machining path, reducing tool travel time and decreasing machining hours.
2. Reasonably calculate the tool path coordinate value
To calculate the movement path of the center of the tool path, the geometric dimensions of the machined parts and the defined programming coordinate system are taken into account. This results in the determination of all tool position data.
Most CNC systems have linear interpolation and circular arc interpolation capabilities. For processing relatively simple flat parts, such as those composed of circular lines and arcs, the start and end points of geometric elements, the center of circular arcs (or radius), and the coordinate values of the intersection or tangent points are calculated.
If the NC system does not have tool compensation capabilities, the motion path coordinate values for the tool center must be calculated.
For parts with more complex shapes, such as those made up of curves and non-circular surfaces, the actual curves or surfaces should be approximated using straight segments (or arc segments) and the coordinate values of their nodes should be calculated based on what is needed. machining precision.
3. Compile the part's CNC processing program
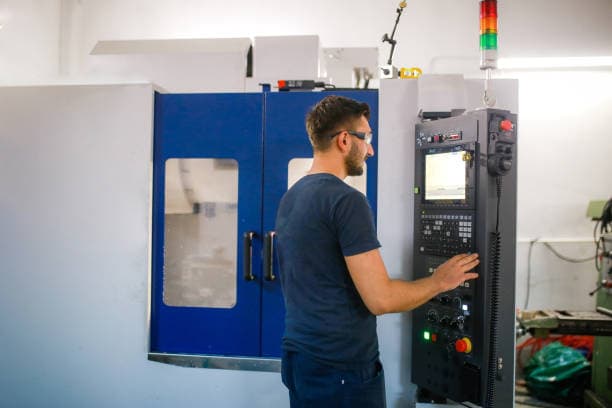
Based on the tool path of the part, tool movement data and determined process parameters and auxiliary actions are calculated.
The programmer then writes the part processing program in sections, following the functional instructions and program section format specified by the NC system in use.
The following must be considered:
- Standardize program writing to improve clarity and communication;
- Have a thorough understanding of the performance and instructions of the CNC machine tool being used and effectively utilize each instruction when writing program segments.
By following these three steps during CNC machining, the machining process can be carried out more efficiently.
CNC Machining Application
The performance characteristics of CNC machine tools determine the scope of application of CNC machining. For CNC machining, objects can be divided into three categories according to their suitability.
1) Most suitable category:
Parts with high machining precision, complex shape and structure, especially those with complex curves and surface contours, or parts with non-open cavities. These parts are difficult to machine and inspect with general machine tools, and it is difficult to guarantee the machining quality; parts that must be completed in one fixture for multiple operations.
2) Most suitable category:
Expensive parts with hard to obtain raw parts that cannot be scrapped. These parts are subject to poor quality or scrapped parts when processed on common machine tools.
For greater reliability, they can be selected for machining on CNC machines; parts with low efficiency, high labor intensity and difficult quality control when processed on machine tools in general; parts used for model changes and performance tests (requiring good dimensional consistency); production parts of multiple varieties, multiple specifications, single pieces and small batches.
3) Inappropriate category:
Parts that depend entirely on manual positioning; parts with very unstable machining tolerances if the CNC machine tool does not have an online inspection system that can automatically check and adjust the part position coordinates; parts that must use specific process equipment, have templates and samples of parts for machining; parts that need to be produced in large quantities.
With the improvement of the performance of CNC machine tools, the improvement of functions, the reduction of costs, the continuous improvement of the performance of CNC machining tools and auxiliary tools, and the continuous improvement of CNC machining technology, the use of machine tools CNC with high automation, high precision and concentrated operations for large-scale production are gradually increasing.