Tool material can be divided into two types:
1. Cutting tool material.
2. Material used for machine tools, gauges, presses and press tools, jigs and fixtures.
1. Types, properties and applications of cutting tool materials
The development of cutting tool materials is an ongoing process in modern industries. The cutting speed, feed rate and depth of cut used today have been considerably improved compared to the 19th century due to the development of science and technology. New dimensions are given to cutting tool materials, their development, etc. as they are very effective in manufacturing the products.
The different types of materials for cutting tools are as follows:
1. High carbon steel.
2. High speed steel.
3. Stellite or cast alloys.
4. Cemented carbides.
5. Ceramics.
6. Diamond.
The cutting tool material must have the following three properties:
1. Wear-resistant ability to maintain cutting tool shape and efficiency.
2. Red hardness capability to maintain tool cutting efficiency at high temperatures.
3. Toughness to provide resistance to shocks and impacts that may be sustained by the cutting tool during machining operations.
Again, it is important to check properties such as specific heat and thermal conductivity of the tool material. Higher values of both properties are required so that the heat generated at the cutting edge of the tool can be dissipated quickly. The coefficient of friction of the tool material must be lower so that the surface gloss can be increased and the rate of heat flow produced between the work and the tool remains lower. The machinability property is equally important for the selection of cutting tool material so that machining can be done easily with that tool material.
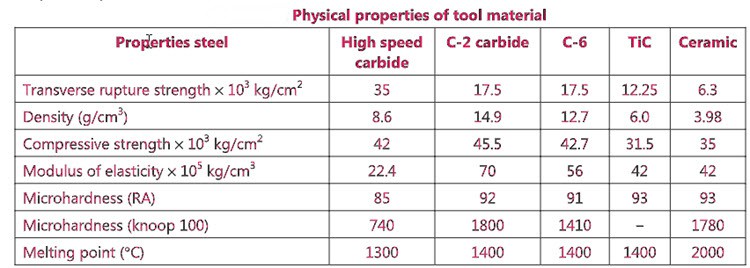
1. High carbon steel:
The carbon content in this steel is 0.9% to 1.2%, which makes the cutting edge of the tool very sharp. It loses its hardness at around 200°C temperature, which means its red hardness value is lower.
Applications of high carbon steel:
1. It can be used as a material for hand tools and low-motion tools.
2. This kind of carbon steel can be forged after heat treatment. Therefore, it is used for lathe tools, hand screw dies and tapes, reamers and broaches. Now the desired properties of high carbon steel can be achieved through alloying.
2. High speed steel:
High speed steel was invented by Tailer, who was an engineer. The currently used HSS 18:4:1 is his invention. This steel contains 18% tungsten, 4% chromium and 1% vanadium. The hardness of the cutting edge of the tool made of HSS is preserved up to 500 °C. The specific classification of HSS is as below:
1. Tungsten steel – contains 14% tungsten.
2. Tungsten molybdenum steel.
3. Tungsten-cobalt steel.
Based on experience, 1% molybdenum satisfies the need for 2% tungsten, and tungsten-cobalt steel is called super high-speed steel, which contains 3 to 5% cobalt, due to its red hardness and increased heat capacity. wear resistance. If vanadium is kept at 3%, a very good finish cut will be obtained and the tool will remain stable against shocks and impacts.
Applications of High Speed Steel :
1. It can be used as tool material for machines that rotate at high speed.
2. For roughing tool for forging and casting rough machining.
3. A different grade of HSS is used in drills to withstand torsional shear stress.
3. Stellite:
Stellite is a non-ferrous alloy containing 12 to 19% tungsten, 38 to 40% cobalt, 30 to 35% chromium, therefore having a red hardness value of 800 °C. The alloy becomes soft at this temperature, but again turns red and hard upon cooling. Its workability and efficiency are the best. Its elements remain in their original form, as this alloy is not oxidized at high temperatures. Therefore, it can provide a better polished surface and can prevent the formation of a built-up edge on the tool face.
Stellite is used at high speed and temperature due to this property.
Stellite Applications:
1. As a cutting tool where full skill is required.
2. It is generally used to machine ductile material at high speed.
Stellite is available in different sections and lengths. It is attached to the tool holder as it is available in the form of different tips. These tips are attached to the rod with silver solder.
4. Cemented Carbide:
Carbide is a cutting tool with specific cutting characteristics. It is made by sintering tungsten carbide grains embedded in stronger metal. Cemented tools are classified as carbide, nitride, borite and silicite, but among them cemented carbide plays a greater role as a tool due to its properties. All physical properties are of higher values than those of steel. According to its properties, it can be said that metallic thermal and electrical conductivities are the same as those of metals. Carbide tips are most commonly used as cutting tools due to their basic properties of greater hardness and high temperature. At certain temperatures, it presents higher red hardness values compared to steel. It contains 55 to 90% carbide particles in the carbide alloy structure and when the carbide is for metal cutting it contains 80% carbide by volume.
It can be broadly classified into three types:
The. P Group: Carbide tool used to cut metal into long chips.
B. K Grouping: Carbide tool used to cut metal into short chips.
w. Grouping M: Carbide tool used to cut metals into medium-length chips.
5. Ceramics:
Aluminum oxide cutting tool material is used in more recent experiments. It is called ceramic or cemented oxide. Generally, tool manufacturers do not produce their commercial composition, but those that are already popular are the following:
The. Aluminum oxide: 99 to 99.5% Al203, remaining silica and chromium oxide.
B. Silicon carbide: 99% AI2O3, remaining silica and chromium oxide.
w. Boron carbide: 60% Al203i remaining refractories containing titanium oxide.
d. Titanium carbide: 60% Al203, remaining molybdenum carbide, titanium carbide and tantalum carbide.
It is. Titanium boride: 60% Al203/remaining titanium boride and molybdenum silysite.
In borite, titanium is contained, therefore it is called titanium borite, and molybdenum used in place of titanium makes the tip easier to braze. The borite tool performs equally well compared to the popular carbide tool. Popular ceramics contain 90% Al203 and the remaining 19% Cr203, MgO and Fe304.
Ceramic tools are produced by sintering containing different percentages of ceramic in their composition with metals, as sintering makes it easy to obtain the metal in a liquid state and the heat conduction coefficient of the metal increases in the presence of carbide. Therefore, this tool can be used for grinding at high temperatures and its edge remains in its original shape without undergoing any changes.
5. Diamond Tools:
The use of diamonds is limited. It is used in powder form for sanding and polishing. It is used in diamond dressers for grinding wheels and in tablet form for drawing dies. It is used for machining expensive plastic materials to obtain the best surface finish and close dimension tolerance.
Diamond is precious and expensive. Therefore, its use is not economically viable, except for certain specific types of machining jobs. It is popularly used for grinding and grinding of grinding wheels. Diamond drill bits are used for machining metals for bearings and other hard steel materials.
Applications of diamond tools:
1. Used in special equipment and accessories.
2. Used in turning and boring tools.
3. For grinding and sharpening grinding wheels.
4. In lapping paste for grinding valves and valve seats.
Desired properties of tool materials
1. Strength.
2. Hardness.
3. Cutting tool geometry.
4. Impact resistance and toughness.
5. High coefficient of thermal expansion.
6. Anticorrosive.
7. Wear resistance.
8. Chemically inactive for cutting fluids.