What is a laser welding machine?
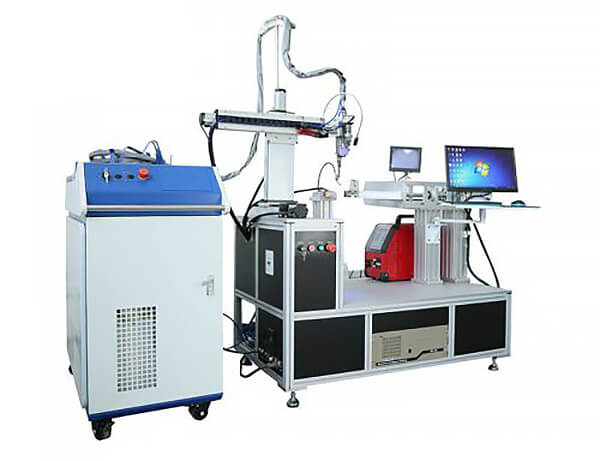
A laser welding machine is a device that uses high-energy pulsed laser to irradiate the workpiece and achieve the welding purpose. It can weld the workpiece precisely by adjusting the pulse laser energy using different laser frequencies and pulse widths.
Types of laser welding machines
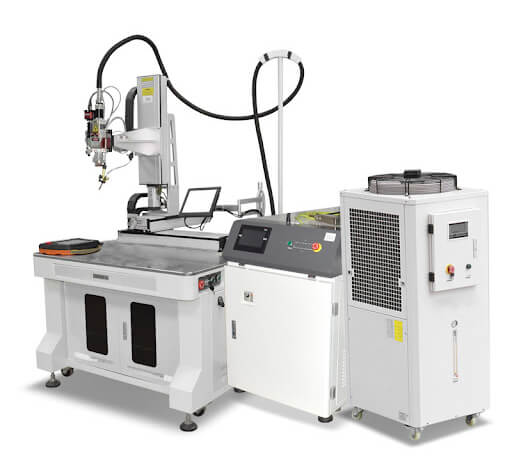
Laser welding machine is also often called energy negative feedback laser welding machine, laser cold welding machine, argon laser welding machine, laser welding equipment and more.
Based on its working mode, it can be classified into several types, such as mold laser welding machine (manual laser welding equipment), automatic laser welding machine, jewelry laser welding machine, welding machine spot laser, fiber optic transmission laser welding machine, galvanometer welding machine, portable welding machine and more.
Special laser welding equipment includes sensor welding machine, silicon steel sheet laser welding equipment and keyboard laser welding equipment.
Weldable graphics include points, straight lines, circles, squares, or any flat graphics drawn with AutoCAD software.
Laser welding machine working principle
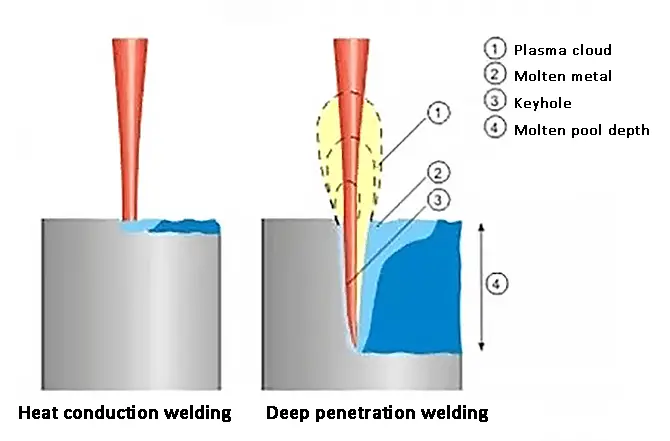
A laser welding machine is a device that uses the characteristics of the laser to weld the part.
Laser welding involves irradiating a high-intensity laser beam onto the metal surface. Through the interaction between the laser and the metal, the metal absorbs the laser and converts it into thermal energy. This causes the metal to melt and subsequently cool and crystallize, resulting in a welded joint.
Mechanism of two types of laser welding
1. Heat conduction welding
When the laser irradiates the surface of the material, part of the laser is reflected and the rest is absorbed by the material, causing the light energy to be converted into thermal energy, resulting in the heating and melting of the material.
Heat from the surface layer of the material continues to be transferred to the depth of the material in the form of heat conduction, ultimately welding the two welds.
2. Laser deep penetration welding
When a laser beam with high power density irradiates the surface of the material, the material absorbs light energy, which is then converted into thermal energy.
The material is heated, melted and vaporized, resulting in the production of a considerable amount of metallic vapor. As the vapor leaves the surface, it generates a reaction force that pushes the liquid away from the molten metal, forming holes.
With continuous laser irradiation, the pits penetrate deeper. Once the laser stops irradiating, the molten liquid around the well flows back and the two weldments are joined together after cooling and solidifying.
This is a new welding method that is mainly used for welding thin-walled materials and precision parts, and can perform spot welding, butt welding, overlap welding, seal welding and more.
Laser Welding Machine Parts and Functions
Laser welding is an efficient and precise welding method that uses a high-energy density laser beam as a heat source. It is one of the significant applications of laser material processing technology.
In the 1970s, laser welding was mainly used for welding thin-walled materials and low-speed welding. The welding process belongs to the heat conduction type, that is, the laser radiation heats the surface of the part and the heat from the surface diffuses internally through heat transfer. By controlling parameters such as laser pulse width, energy, peak power and repetition frequency, the part melts and forms a specific molten pool.
Due to its unique advantages, laser welding has been successfully applied to the precision welding of micro and small parts.
A complete laser welding machine mainly comprises five parts.
Part I: laser welding host
The laser welding host mainly produces a laser beam for welding and comprises the power supply, laser generator, optical path part, control system and other components.
In some cases, low-power lasers are typically integrated into the automatic worktable of the laser welding system.
Part II: cooling system
The cooling system provides the cooling function for the laser generator, which is generally equipped with a 1 to 5 HP water circulation chiller.
Part III: automatic laser welding worktable or motion system
The laser welding system is used to realize the automatic welding function by moving the laser beam along the welding track as per specific requirements. There are typically three forms of motion control:
- The part moves and the laser head is fixed.
- The laser head moves and the part is fixed.
- Both the laser head and the part move.
The whole system compiles the motion control program using CNC programming to regulate the movement of the work table according to the requirements. The simplified programming system offers several advantages, such as ease of operation, no need for professional technology or educational basis, and quick support and understanding.
Common countertop systems on the market include:
- Manipulator movement system;
- 2D bench;
- 3D workbench;
- Four-axis articulation bench;
- Gantry welding bench;
- Cantilever bench, etc;
Both can realize precise control of the welding movement.
Part IV: Tool Attachment
In the laser welding process, a laser welding fixture is generally employed to clamp the welded part and allow it to be loaded, unloaded and positioned repeatedly. This makes automatic laser welding more manageable.
Therefore, the luminaire is one of the essential equipment in laser welding production. Especially during batch production, proper fixture design will have a direct impact on production efficiency and yield.
Part V: observation system
Generally, the laser welding machine must be equipped with an observation system that can perform real-time microscopic observations on the workpiece. This observation system is used to facilitate accurate positioning when compiling the welding program and inspecting the welding effect during the welding process.
Common observation systems include a CCD display system or a microscope.
Features of laser welding machine
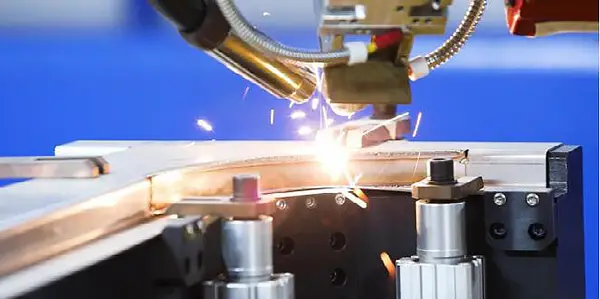
Features of laser welding:
High aspect ratio, small weld width, small heat affected zone, minimal deformation, fast welding speed, flat and aesthetically pleasing weld, no or minimal treatment required after welding, high weld quality, no pores, precise control, small focusing light spots, high positioning accuracy and easy realization of automation.
Features of laser welding machine:
The laser welding machine has a high degree of automation and a simple welding process. Its non-contact operation method can meet cleanliness and environmental protection requirements.
Using a laser welding machine to process parts can improve work efficiency. The finished parts have beautiful appearance, small welds, large welding depth and high welding quality. The laser welding machine is widely used in denture processing, keyboard welding, silicon steel sheet welding, sensor welding, battery seal cover welding and more.
However, the cost of a laser welding machine is high, and the part assembly accuracy must also be high. Therefore, there are still limitations in these aspects.
Specifications of laser welding machine
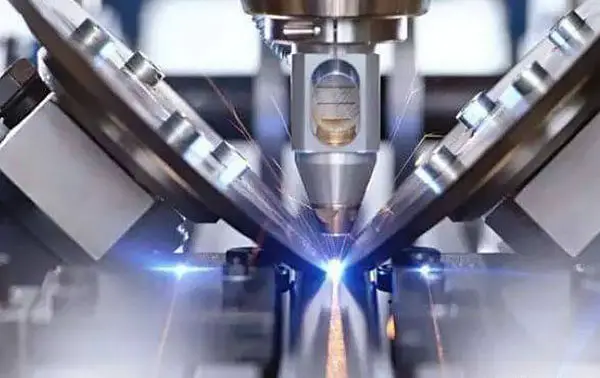
Laser power density
Laser power density is one of the most critical parameters in laser processing.
With high power density, the surface layer can be heated to the boiling point in the microsecond time range, resulting in a significant amount of vaporization. Therefore, high power density is preferable for material removal processing such as punching, cutting and engraving.
For low power density, it takes several milliseconds for the surface temperature to reach the boiling point. Before the surface is vaporized, the bottom layer reaches the melting point, facilitating the formation of a good molten weld.
Therefore, in conductive laser welding, the power density is in the range of 10^4 ~ 10^6 W/cm 2 .
Pulse waveform
The pulse waveform is a crucial factor in welding, especially in sheet metal welding.
When a high-intensity beam hits the surface of the material, some energy at the metal surface is lost due to reflection, and the reflectivity changes with surface temperature.
The reflectivity of the metal varies significantly during a pulse.
P pulse width
Pulse width is one of the essential parameters in pulse welding.
It differs from material removal and melting and is also a crucial parameter in determining the cost and volume of processing equipment.
Blur effect
Because the power density at the center of the laser focus is very high, it is easy to create holes due to evaporation.
The power density distribution is relatively uniform in each plane away from the laser focus.
There are two blurring modes: positive blurring and negative blurring.
If the focal plane is above the workpiece, it is positive defocus; otherwise it will be negative blur.
According to the theory of geometric optics, when the distance between the positive and negative defocus planes and the welding plane is equal, the power density in the corresponding plane is approximately the same. However, in reality, the shape of the weld pool is different.
By using negative defocus, greater penetration is achieved, which is related to the molten pool formation process.
Laser welding machine parameter table
Diameter | Joint form | Specifications. | Joint performance | |||
---|---|---|---|---|---|---|
output power/pulse J | Pulse width/ms | Maximum load/N | Resistance/Ω | |||
301 Stainless steel(1Cr17Ni7) |
Φ0.33 | butt joint | 8 | 3.0 | 97 | 0.003 |
overlap | 8 | 3.0 | 103 | 0.003 | ||
in the shape of a cross | 8 | 3.0 | 113 | 0.003 | ||
T shape | 8 | 3.4 | 106 | 0.003 | ||
Φ0.79 | butt joint | 10 | 3.4 | 145 | 0.002 | |
overlap | 10 | 3.4 | 157 | 0.002 | ||
in the shape of a cross | 10 | 3.4 | 181 | 0.002 | ||
T shape | 11 | 3.6 | 182 | 0.002 | ||
Φ0.38+Φ0.79 | butt joint | 10 | 3.4 | 106 | 0.002 | |
overlap | 10 | 3.4 | 113 | 0.003 | ||
in the shape of a cross | 10 | 3.4 | 116 | 0.003 | ||
T shape | 11 | 3.6 | 102 | 0.003 | ||
Φ0.38+Φ0.40 | T shape | 11 | 3.6 | 89 | 0.001 | |
Copper | Φ0.38 | butt joint | 10 | 3.4 | 23 | 0.001 |
overlap | 10 | 3.4 | 23 | 0.001 | ||
in the shape of a cross | 10 | 3.4 | 19 | 0.001 | ||
T shape | 11 | 3.6 | 14 | 0.001 | ||
Nickel | Φ0.51 | butt joint | 10 | 3.4 | 55 | 0.001 |
overlap | 7 | 2.8 | 35 | 0.001 | ||
in the shape of a cross | 9 | 3.2 | 30 | 0.001 | ||
T shape | 11 | 3.6 | 57 | 0.001 | ||
Tantalum | Φ0.38 | butt joint | 8 | 3.0 | 52 | 0.001 |
overlap | 8 | 3.0 | 40 | 0.001 | ||
in the shape of a cross | 9 | 3.2 | 42 | 0.001 | ||
T shape | 8 | 3.0 | 50 | 0.001 | ||
Φ0.63 | butt joint | 11 | 3.5 | 67 | 0.001 | |
overlap | 11 | 3.5 | 58 | 0.001 | ||
T shape | 11 | 3.5 | 77 | 0.001 | ||
Φ0.65+Φ0.38 | T shape | 11 | 3.6 | 51 | 0.001 | |
Copper and tantalum | Φ0.38 | butt joint | 10 | 3.4 | 17 | 0.001 |
overlap | 10 | 3.4 | 24 | 0.001 | ||
in the shape of a cross | 10 | 3.4 | 18 | 0.001 | ||
T shape | 10 | 3.4 | 18 | 0.001 |
Advantages of laser welding machine
With the continuous upgrading of laser welding technology, laser welding has undergone a qualitative leap.
Now laser welding machines have been used in many fields such as high-tech electronics, automobile manufacturing, precision machining and more.
As a laser application direction, laser welding is the combination of current and traditional technology, but it offers different advantages from traditional processing.

10 advantages of laser welding machine
1. Good laser beam quality
After laser focusing, the power density becomes high.
The diameter of the focal spot is small when focusing the high-power low-order mode laser.
2. Laser welding has the advantages of high speed, large depth and small deformation
Due to the high power density, small holes are formed in metal materials during laser welding, and the laser energy is transmitted to the deep part of the workpiece through these small holes, with less transverse diffusion.
Therefore, the melting depth of the material is significant in the laser beam scanning process, and the process offers high speed and large welding area per unit time.
3. Laser welding is especially suitable for welding precision sensitive parts
As the laser welding machine has a large aspect ratio, low specific energy, small heat-affected zone and minimal welding deformation, it is especially suitable for precision welding and heat-sensitive parts. It can also eliminate the need for post-weld correction and secondary processing.
4. High flexibility of laser welding
Laser welding machines can perform welding at any angle and weld hard-to-reach parts.
They can also weld various complex parts and large parts with irregular shapes.
The machines offer great flexibility to perform welding at any angle.
5. Laser welding can weld difficult materials
Laser welding can be used not only for welding between various different metal materials, but also for welding between titanium, nickel, zinc, copper, aluminum, chromium, niobium, gold, silver and its alloys, steel, kovar alloy and other materials league. .
6. Low labor cost of laser welding machine
Because the heat input of laser welding is very low and the deformation after welding is minimal, a beautiful welding effect can be achieved.
As a result, there is little need for laser welding follow-up treatment, which can significantly reduce or eliminate labor-intensive polishing and leveling processes.
7. The laser welding machine is easy to operate
The laser welding machine has the advantages of simple welding equipment, simple operation process, and is easy to learn and use.
Professional requirements for staff are not high, which can save labor costs.
8. The laser welding machine has strong safety performance
The high-security welding nozzle can only be activated when it comes into contact with the metal, and the touch switch has a temperature sensor.
There are safety precautions for the special laser generator during operation. It is necessary to wear protective glasses on the laser generator to reduce the risk of eye injury.
9. The working environment of laser welding machines is diverse
The laser welding machine can be used in various complex working environments and can perform welding at room temperature or under special conditions.
For example, laser welding shares many similarities with electron beam welding. Although its welding quality is slightly inferior to electron beam welding, the latter can only be used in a vacuum environment. On the other hand, laser welding technology is more advanced and can be used in a wider variety of work environments.
10. The welding system is highly flexible and easy to realize automation
However, the laser welding machine also has some limitations. Due to the high cost of laser-related systems, the one-time investment cost will be higher. In addition, the laser welding machine also requires high welding installation precision, and the position of the light source on commercial parts should not have an obvious deviation.
It can be seen that the ten advantages of laser welding machines are much better than traditional welding methods. In the future, the application of laser welding technology will not be limited to the current electronic, automotive, instrument and other fields. It will also be more extensive in the military and medical fields, especially in the medical field, which has broad prospects.
Laser welding versus other welding processes
Comparison Items | laser welding | Electron beam welding | Arc welding with tungsten inert gas | Gas Metal Arc Welding | Resistance welding |
Welding efficiency | 0 | 0 | – | – | + |
Large depth ratio | + | + | – | – | – |
Small heat affected zone | + | + | – | – | 0 |
High welding rate | + | + | – | + | – |
Morphology of the weld section | + | + | 0 | 0 | 0 |
Atmospheric pressure welding | + | – | + | + | + |
Welding high reflectivity materials | – | + | + | + | + |
Use filler material | 0 | – | + | + | – |
Automatic welding | + | – | + | 0 | + |
Cost | – | – | + | + | + |
Cost of operation | 0 | 0 | + | + | + |
Reliability | + | – | + | + | + |
To assemble | + | – | – | – | – |
Application of laser welding machine
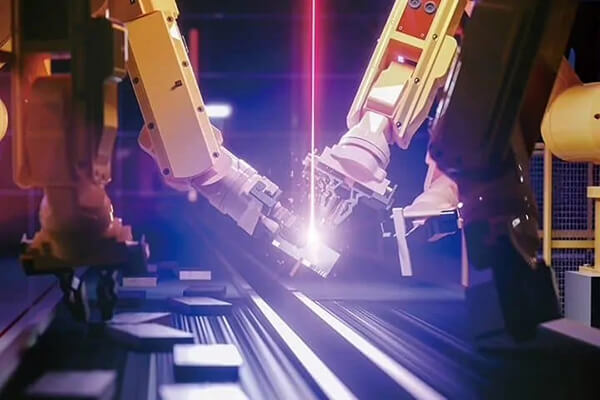
M manufacturing
Tailored laser welding technology has been widely used in automobile manufacturing. According to statistics, there were more than 100 custom laser welding production lines around the world in 2000, and the number continues to grow at a high rate.
In Japan, CO2 laser welding is used to replace flash butt welding for connecting rolled steel coils in the steel industry. In the welding research of ultra-thin plates, such as sheets with a plate thickness of less than 100 microns, fusion welding cannot be carried out, but YAG laser welding with special output power waveform is successful, which shows the broad future of laser welding.
Japan has also successfully developed YAG laser welding for the first time in the world for the maintenance of steam generator tubes in nuclear reactors and implemented gear laser welding technology in China.
P oldest metallurgy
With the continuous development of science and technology, many industrial technologies have special requirements for materials that cannot be met by materials manufactured by casting and casting. Due to the special properties and manufacturing advantages of powder metallurgy materials, they are replacing traditional metallurgical materials in some fields such as automobile, aircraft, tool and cutting tool manufacturing.
With the increasing development of powder metallurgy materials, the connection between powder metallurgy materials and other parts is becoming more and more prominent, which limits the application of powder metallurgy materials. In the early 1980s, laser welding entered the field of powder metallurgy materials processing with its unique advantages, which opened a new perspective for the application of powder metallurgy materials.
For example, the brazing method commonly used in connecting powder metallurgy materials may lead to weld melting and falling off due to the low bonding strength and wide heat-affected zone, especially unable to adapt to high temperatures and heat requirements. high resistance. Laser welding can improve welding strength and high temperature resistance.
The automotive industry
In the late 1980s, the kW laser was successfully applied in industrial production. At present, laser welding production line has appeared on a large scale in the automobile industry and has become one of the outstanding achievements of the automobile industry.
As early as the 1980s, European car manufacturers took the lead in using laser welding for welding sheet metal such as roof, body and side structures. In the 1990s, the United States introduced laser welding into automobile manufacturing, and although it started late, it developed rapidly.
Italy uses laser welding in the welding and assembly of most sheet steel components, and Japan uses laser welding and cutting processes in the manufacture of body panels.
High-strength steel laser welding sets are increasingly used in automobile body manufacturing due to their excellent performance.
According to the characteristics of large batches and high degrees of automation in the automobile industry, laser welding equipment is developing in the direction of high power and multi-channel.
In terms of process, the United States' Sandia National Laboratory and Pratt Witney jointly conducted research on the addition of metal powder and wire in the laser welding process, and the Bremen Institute of Applied Beam Technology in Germany conducted Extensive research on laser welding aluminum alloy body frames.
Adding filler to the weld is considered to be useful in eliminating thermal cracks and improving welding speed. The developed production line was put into production in the factory to solve the tolerance problem.
And electronics industry
Laser welding has been widely used in the electronics industry, especially in the microelectronics industry.
Due to its small heat-affected zone, rapid heating concentration, and low thermal stress, laser welding presents unique advantages in the packaging of integrated circuits and semiconductor device casings.
In the development of vacuum devices, laser welding has also been applied, such as molybdenum focusing electrodes and stainless steel support rings, fast heating cathode filament assembly and more.
The thickness of the thin-walled elastic corrugated sheet in the temperature sensor or controller is 0.05-0.1mm, which is difficult to weld using traditional welding methods.
TIG welding is prone to penetration, plasma stability is poor, and there are many influencing factors. However, laser welding has a good effect and is widely used in this field.
B medical science
Laser welding of biological tissues began in the 1970s.
The successful welding of fallopian tubes and blood vessels with lasers, and its advantages, have encouraged more researchers to try welding various biological tissues and expand to welding other tissues.
Research on laser welding nerves, both domestically and abroad, mainly focuses on laser wavelength, dosage, functional recovery and laser welding selection.
Compared with the traditional suturing method, laser welding has the advantages of faster anastomosis speed, no foreign body reaction in the healing process, maintaining the mechanical properties of the welding site, and allowing the repaired tissue to grow according to its original biomechanical properties.
It will be more widely used in biomedicine in the future.
Other areas
In other industries, laser welding is also gradually increasing, especially in the welding of special materials.
Many studies have been carried out in China, such as laser welding of BT20 titanium alloy, HEL30 alloy and lithium-ion battery. Germany has developed a new laser welding technology for flat glass.
Development history of laser welding machine
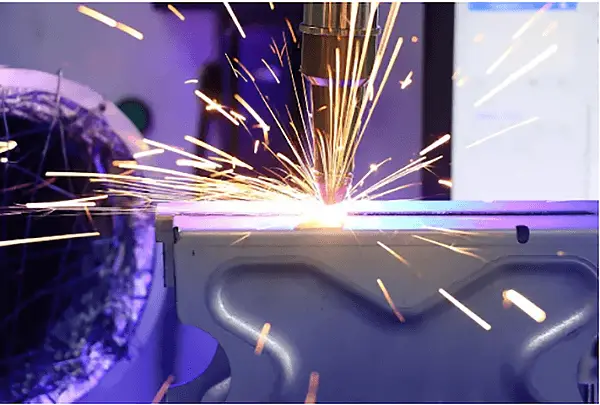
Before the 1970s, high-power CW lasers had not been developed, so research focused on pulsed laser (PW) welding. Most early laser welding experiments used Ruby pulse lasers with a typical PM peak output power of 5kW for a 1ms pulse, pulse energy of 1-5J, and a pulse frequency less than or equal to 1Hz.
At that time, although the pulse energy was high, the average output power of these lasers was quite low due to the low working efficiency of lasers and the properties of luminous substances. The laser soon became the equipment of choice for spot and seam welding due to its high average power.
The welding process was carried out through lapping spot welding, and laser seam welding of real significance was not carried out until the development of continuous power waveform lasers of more than 1kW.
Current status and perspective of welding automation technology
With the increasing maturity of digital technology, digital welding machines and digital control technology such as dynamic grounding technology have steadily entered the market. Large-scale national basic engineering has effectively promoted the development and progress of advanced welding, especially welding automation technology.
The manufacture of automobiles and parts requires the automation of welding with each passing day. Since the end of the 20th century, the country has gradually promoted the basic automatic welding method – gas shielded welding – to replace traditional manual arc welding, which achieved initial results. It can be predicted that in the future, automatic welding technology will develop at an unprecedented speed.
Current status of automatic and high-efficiency welding technology
In the 1990s, the welding industry made the achievement of mechanization and automation of the welding process its strategic objective, which has been achieved in the scientific and technological development of several industries.
It is developing welding production automation, researching and developing welding production lines and flexible manufacturing technology, and developing computer-aided design and manufacturing.
Flux cored wire has increased from 2% to 20%, and submerged arc welding materials will also continue to grow at the 10% level.
Among them, the growth rate of flux-cored wire is significantly higher and is expected to exceed that of solid cored wire in the next 20 years, eventually becoming the leading product of the welding industry.
The perspective of welding automation technology
The development of electronic technology, computational microelectronics and automation technology promotes the development of welding automation technology.
In particular, the introduction of unitary technology such as numerical control technology, flexible manufacturing technology and information processing technology has promoted the revolutionary development of welding automation technology.
(1) The intellectualization of welding process control systems is one of the main challenges in welding automation and an important area for future research. We need to investigate optimal control methods, including linear controls and various nonlinear controls. The most representative methods include fuzzy control, neural network control, and expert systems for the welding process.
(2) Welding flexibility technology involves the organic combination of various optical, mechanical and electrical technologies with welding technology to achieve precise and flexible welding. To improve the level of welding automation, we need to transform traditional welding process equipment with microelectronic technology. Our current research focus is to combine numerical control technology with all types of welding machines and equipment to improve their flexibility. In addition, our research also focuses on combining welding robots and specialized systems to achieve automatic trajectory planning, automatic trajectory correction and automatic penetration control.
(3) The integration of welding control systems involves the integration of human and technology, welding technology and information technology, and material flow and information flow. By promoting your organic combination, we can significantly reduce the amount of information and real-time control requirements. We need to pay attention to giving full play to people's responsiveness and judgment in on-site control and processing, establishing a user-friendly human-machine interface, and making people and the automatic system harmonious and unified. These factors are crucial in the integrated system.
(4) Our research also focuses on improving the reliability, quality stability and control of welding power supplies, as well as developing excellent dynamic performance. Our goal is to develop a high-performance welder that can adjust arc movement, wire feed and torch attitude, detect the onset of weld tilt, temperature field, molten pool state and penetration, and provide welding specification parameters in a timely manner. We also actively develop computer simulation technology for the welding process to help welding technology evolve from “technology” to “science”, which is an important aspect of welding automation.
Why choose laser welding machine ?
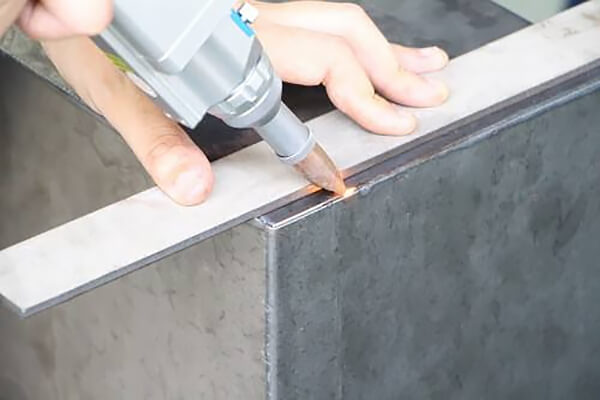
Laser welding machine saves time and energy
In any line of work, it is essential to invent corresponding tools to improve process flow, save time and energy, and better meet needs. With the continuous development of technology, there have been great advances in these aspects, and automatic operation can now be implemented in various industries.
In factories, automation can significantly improve production and supply efficiency, reduce costs and increase operational benefits. When welding, it is essential to choose suitable tools to improve operational speed, with a laser welding machine being an excellent choice.
Laser welding can achieve better production effect
Why laser welding machines can achieve better work efficiency for users?
As a new energy, laser technology provides a stronger working state and enables effective treatment of various materials. Furthermore, new welding methods are used to ensure excellent welding results and complete operations quickly.
In the future market, people's speed of life and work will continue to accelerate. To achieve better production results and satisfy the needs of more users, each factory must continually improve its technology, make breakthroughs and resolve any defects and deficiencies to improve overall performance.
Only by consistently moving in this direction can products gain a competitive advantage, provide better user experiences, and facilitate effective collaboration between both sides.
Laser welding machine brings more convenience to manufacturers
In my opinion, selecting a laser welding machine in the welding process is a wise choice for manufacturers as it can increase work efficiency and provide more convenience.
In the operation process, each factory can complete its tasks within a specific time frame, thus improving its overall operational efficiency. It is also essential to perform effective welding of large tools and improve process flow.
Failure to ensure this crucial aspect can waste time and energy during the welding process of significant equipment, which no user wants to experience.
The importance of choosing a suitable laser welding machine
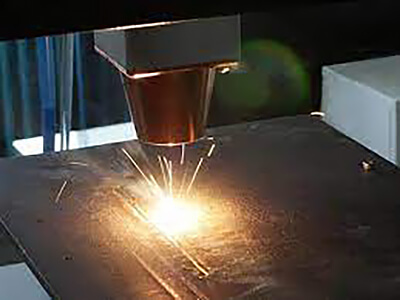
With the continuous maturity and development of laser welding technology, different equipment configurations of laser welding machines also correspond to different effects. However, among many companies, is it right to choose the most expensive and best laser welding machine equipment? The answer is, obviously, no.
So how to choose the most suitable laser welding machine equipment? Only when we understand it clearly can we know what benefits it brings us. Let's talk about the importance of selecting the appropriate laser welding machine now!
Before customers choose laser welding machine equipment, our idea is that the selected equipment can meet our needs, realize our processing effect, and bring benefits to us. This equipment is what we want.
However, for laser welding machine manufacturers, the price positioning of laser equipment is high and low cost. In terms of processing effect, high-end equipment can make the processing effect more complete, and the styles are also diverse, such as processing various materials, metals and non-metals. The processing effect is also very good, but this equipment is also valuable.
Is it better to choose high-end laser welding machine equipment? Of course. If your material is focused on non-metallic materials, there are no metallic materials and the processing effect is not that great, it is recommended to choose the general one. Because the more functions, the better the effect of the equipment, the more products will be processed, and the more expensive the machines and equipment will be. Furthermore, if you don't use all its functions when you buy it, you will spend money on furniture, so it's not worth it.
Just understand what you want to do with this machine and equipment, make the same or several products and then make choices according to your needs. Therefore, when choosing laser welding machine equipment, only the right one is best. The so-called suitability means that merchants' products can be processed, and industries with more applications can meet their needs. The benefits it brings can meet your needs. These equipment are worth more and correspond to your suitability.
What factors determine the price of a laser welding machine?
Without saying anything about this problem, it is certain that a high-efficiency and high-quality laser welding machine is definitely worth buying! However, with tens of thousands to hundreds of thousands of laser welding machines on the market, a good laser welding machine can double the success of your work. So what should we consider when determining whether a laser welder is worth it?
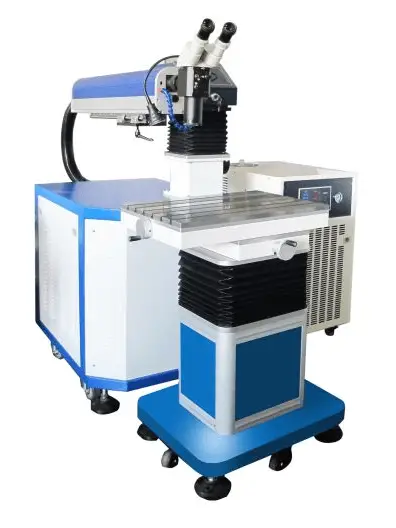
1. Power
The first consideration is power.
The laser is the core of laser equipment and the higher the power, the higher the price. This is because higher power requirements are placed on the laser rod and cooling system.
2. Configuration
Setting up a laser welding machine involves many aspects. Laser welding machines for different purposes have different configurations, such as mold welding for welding molds, jewelry welding for jewelry welding, vibrating mirror welding inside an automatic welding machine, fiber transmission laser welding machine optics, optical fiber continuous laser welding machine and so on. The equipment configuration is different and the price also varies.
In addition, automatic welding machines are generally more expensive than manual welding machines because the automatic control system requires automatic support configuration such as a CCD camera monitoring system.
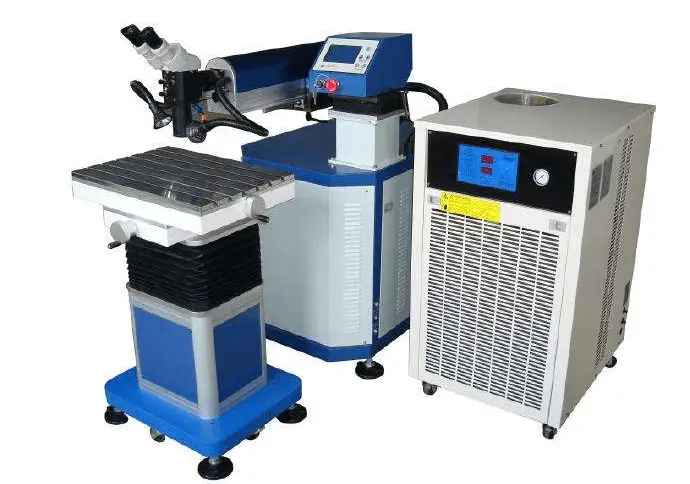
3. Requirements for customization
There are also some customized needs, so the price will be higher.
For example, some production processes may require custom automatic fixtures, modified workbenches, or additional functional fixtures.
4. Working methods
The laser welding machine should be equipped with a working table, such as galvanometer working mode, automatic working mode, spot welding working mode and portable working mode.
The work table belongs to non-standard products and needs to be designed according to the customer's products, so the price is not fixed.
5. Accessories
Imports are generally more expensive than domestically produced products and domestic prices can vary greatly.
It can be said that the price of accessories can vary greatly.
6. Brand
The brand will also affect the quote.
The brand is also an aspect that cannot be ignored.
Laser welding machines generally cost hundreds of thousands and have high technical content and a high level of after-sales service, so they must be purchased through formal channels.
It is recommended to find manufacturers for direct sales. The technology of a reputable brand is more mature, the product quality is good, the performance is stable, and the after-sales guarantee is perfect.
What is the price difference between different brands of laser welding machines?
At present, laser welding equipment has been widely used in various industries, including digital products, power batteries, hardware and plastics, kitchens and bathrooms, machine manufacturing, precision electronics and handmade jewelry.
Although brands of laser welding machines may vary, their structures are generally similar. So what are the differences between different types of laser welding equipment?
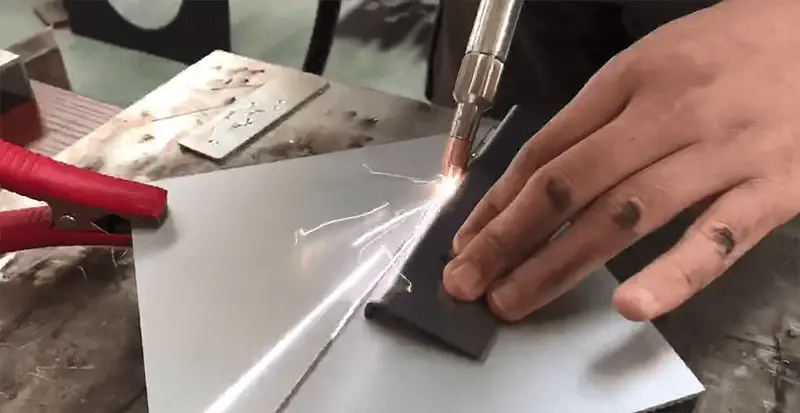
Reasons for the price difference of laser welding machine brands:
1 . Manufacturing cost
There are many brands of laser welding machines, each with its own advantages, but their structures are similar.
A laser welding machine is composed of a laser generator, a welding gun head, a control motherboard, an operating system, electrical circuit components, sheet metal housing and other components.
Good equipment must choose better components, and the equipment composed of good components will be more stable and have higher performance.
The pursuit of a low price will compromise the quality of components, reduce the cost, and the corresponding price will be reduced.
two . Technical level
There are many manufacturers of laser welding machines, and the technical level varies.
A manufacturer's technical strength can be seen in product composition, commissioning and after-sales maintenance of equipment.
Manufacturers' corresponding cost of certain technicians will also increase.
The price of equipment from these manufacturers will not be very low, and some manufacturers without essential technology will promote the market at a low price.
The principle “you get what you pay for” is very practical here.
3 . After sales service
Revised version:
Equipment transactions may involve after-sales issues.
For a laser welding machine, long-term use will certainly present some problems.
How long production will be delayed if there is a problem with the equipment is a big test of the manufacturer's after-sales capabilities.
Excellent after-sales personnel will not only help customers produce better results, but also increase the cost of manufacturers.
For manufacturers without after-sales service, this service is less and the corresponding price will be cheaper.
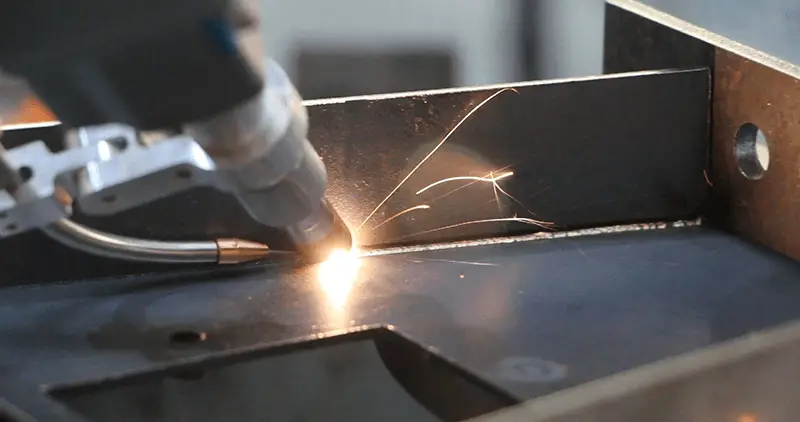
Which laser welding machine equipment manufacturer is good?
The level of development of the manufacturing industry is one of the factors that reflects the overall strength of a country and can also reflect the extent of national economic growth laterally. With the continuous growth of the economy, people's concepts of consumption have also changed and the demand for the quality and functionality of products is greater than ever. This requires laser welding equipment manufacturers to constantly improve the manufacturing process, improve quality and increase production efficiency to meet market demand and gain recognition from users.
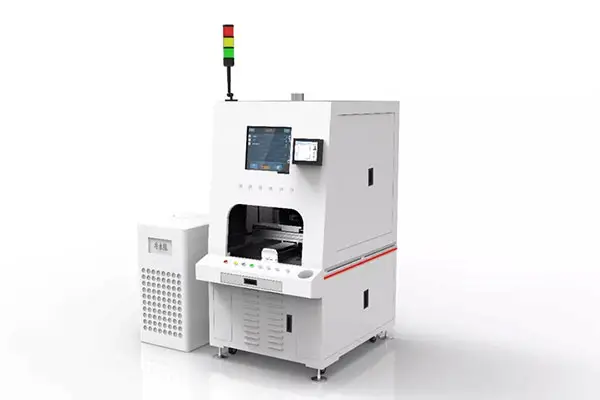
Currently, there is an increasing demand for laser welding machine equipment in manufacturing companies. This is because laser technology is used for welding processing, offering advantages such as fast welding speed, firm and beautiful welds, no need for secondary grinding treatment, simple operation, automatic batch production and processing, greatly improving work efficiency product processing and reduce employment costs for companies.
Therefore, there is a huge market demand for laser welding machine equipment, and there are many laser welding manufacturers on the market. The quality level of various laser welding equipment is uneven, and prices range from tens of thousands of yuan to hundreds of thousands of units. Faced with many laser equipment manufacturers, many users do not know how to choose.
Let me briefly introduce some factors that need to be considered when purchasing laser welding equipment.
1 . First of all, you need to know whether your own welding needs match the welding function of the manufacturer's equipment.
Such as welding thickness, penetration requirements, etc.
two . The quality of the laser welding machine must be considered
After all, tens of thousands of yuan for a device is not a small amount. It is best to go on site to do a welding sample and understand whether the functional requirements of the device are appropriate before making a purchase.
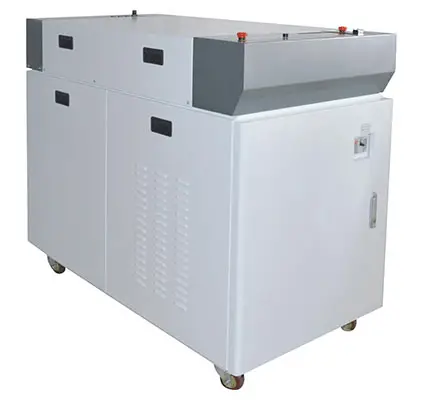
3 . Selection of equipment from large brand manufacturers and small brand manufacturers
Some customers believe that the quality of laser welding machines produced by large manufacturers should be better than that of small companies. However, in reality, there is no right standard for this.
Users buy equipment to create value and make profits, and the price of large enterprises' equipment is obviously much higher, which leads to an increase in cost. On the other hand, the equipment of non-big brand companies generally has large price discounts, the quality is not necessarily worse than that of brand companies, and the cost performance is high, which is also worth considering.
The quality of after-sales service of laser welding machine manufacturers is a matter of great concern to many consumers. After purchasing the welding equipment, the manufacturer's technicians are also required to go to the site for debugging, layout and configuration selection according to the actual production situation. If there are any problems with subsequent equipment or parts that need to be replaced, the manufacturer should be contacted in time for treatment.
How to select a laser welding machine ?
With the rapid development of laser technology, there are many brands of laser welding equipment on the market, but the quality of products is uneven. This can make it difficult for buyers to know where to start when selecting equipment. How can we choose the most suitable laser welding equipment?

When selecting laser welding machine equipment, we can choose from the following aspects:
1 . First determine whether the product is suitable for welding with laser welding technology
When selecting laser welding equipment, we must first determine whether our products are suitable for welding with laser welding equipment. We have analyzed the situation of more than 200 customers in the past and found that there are two main types of products that are not suitable for laser welding: the weld is too large (generally more than 0.5mm) and the thickness is too thick (generally more than 5mm).
The most suitable workpiece for laser welding is a thin plate piece with good consistency (the thickness is generally less than 3mm) and the weld width does not exceed 10% of the plate thickness. Double turning welding joint is necessary for the weld that slightly exceeds the thickness, but the turning point will cause laser energy dispersion and affect the cutting efficiency.
For parts with very large welds, we do not recommend customers to use laser welding. Likewise, laser welding of thick plates is not recommended for customers at this stage due to high equipment costs and complex adjustment processes.
For example, if the welding depth of the product is between 2.5mm-3mm and the welding depth of the laser welding machine exceeds 3mm, it will certainly not be suitable. Currently, most laser welding equipment manufacturers offer free proofing services. Before purchasing, customers should allow the other party to prove the effect to determine whether the use of laser welding equipment can meet their needs.
Manual welding or automatic welding?
Laser welding is a precision welding technique, which has two main aspects: achieving good welding effects on precision products and having high requirements for the welds of welded products.
If the solder has more than 15 wires, the welding wire must be filled, and only manual welding machines can be used. On the other hand, if the solder has less than 15 wires, automation can be achieved. The best scenario is no gap because laser welding is performed by self-melting the sample.
For parts of various types, each batch is small, it is very complicated to make tools or the parts are difficult to locate and weld, and spot welding is more common. In these cases, portable laser welding may be considered.
Portable laser welding machines have been very popular in the last two years, but in fact, they are useless and ineffective. Most customers were deceived by unscrupulous businessmen. Manual laser welding is difficult to control the position of the light spot and focus, and even small deviations can affect the welding effect. In addition, the welding consistency of this method is poor, and it is difficult for manual operators to weld continuously for a long time. Furthermore, the risks associated with manual laser welding are relatively high and accidents can cause significant damage. Customers should be cautious when choosing portable laser welding and should not be influenced by welding videos.
Next, let's talk about automatic laser welding. If the customer's welding track is complex, has many curved tracks, specially shaped tracks or multiple surfaces that need to be welded simultaneously, we recommend using portable laser welding machines. They are highly flexible and can be clamped in turn, achieving fully automatic welding and realizing multi-machine cooperative welding by cooperating with special tools and bonding bench.
If the customer's workpiece is simple, has many long, straight seams, or requires intersection line welding of standard pipe fittings, we recommend modular laser welding machines.
two . Select the laser welding machine power according to your own product attributes
The laser generator is the main component of laser equipment, and generally the higher the power, the higher the price. This is because the hardware configuration requires higher power for laser rods and cooling systems. Generally, the greater the depth and thickness of the welding, the greater the power required of the laser welding machine.
For a welding depth of 0.5mm, a 200W laser welding machine is suitable. It should be noted that 200W is sufficient for penetration welding and spot welding. For continuous welding, it is better to use a little higher laser power, because the 200W laser welder can only weld 0.8mm in the deepest part. For continuous welding with a welding depth of about 0.5mm, it is best to choose a 250W or 300W laser welding machine. The greater the welding depth, the greater the power required for the corresponding laser welder.
3 . Select the corresponding hardware configuration and primary purpose
The hardware configuration of laser welding equipment involves many fields, and the hardware configuration of laser welding equipment varies for different purposes.
For example, the hardware configuration and price of optical fiber laser welding equipment, sheet metal box welding, fillet welding and overlap welding of stainless steel and carbon steel are different.
The choice of laser power, core diameter, welding joint aspect ratio, manipulator spread, ground rail length, welding process, etc. is determined by factors such as penetration depth, penetration width, pulling force or airtightness requirements, welding length, and weld shape.
4 . Make reasonable selections according to cost budget and purpose
Some people choose foreign brands despite the higher price, but in fact, domestic laser welding machine equipment has more advantages. National technology is constantly improving and has already reached international standards. In case of after-sales problems, domestic machines can offer more guaranteed and convenient solutions. Choosing between national and foreign brands should depend on your own budget and purpose.
After considering the four main factors mentioned above, you should have a better idea of how to choose a laser welding machine that meets your practical demands.