Advanced processing equipment and high-performance CNC tools can fully utilize their due performance and obtain good economic benefits.
With the rapid development of tool materials, the physical properties, mechanical properties and cutting performance of various new tool materials have been greatly improved, and the range of applications has continuously expanded.
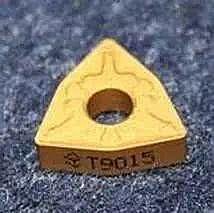
The basic performance of cutting tool materials
The choice of cutting tool materials has a great impact on tool life, machining efficiency, machining quality and machining costs. The tool must withstand high pressure, high temperature, friction, shock and vibration during cutting. Therefore, the cutting tool material must have the following basic properties:
(1) Hardness and wear resistance.
The hardness of the cutting tool material must be higher than the hardness of the workpiece material, generally above 60HRC.
The higher the hardness of the tool material, the better the wear resistance.
(2) Strength and tenacity.
Cutting tool materials must have high strength and toughness to withstand cutting forces, shocks and vibrations and prevent brittle fractures and chipping of the tool.
(3) Heat resistance.
The material of the cutting tool must have good heat resistance, withstand high cutting temperatures and have good oxidation resistance.
(4) Process performance and economics.
The tool material must have good forging performance, heat treatment performance, welding performance, grinding performance, etc., and pursue a high performance-price ratio.
Type, performance, characteristics and application is cutting tool materials
diamond cutter
Diamond is an isomer of carbon, the hardest material ever found in nature.
Diamond cutting tools have high hardness, high wear resistance and high thermal conductivity, and are widely used in the processing of non-ferrous metals and non-metallic materials.
Related Reading: Ferrous vs Non-Ferrous Metals
Especially in the high-speed machining of aluminum and silicon-aluminum alloys, diamond tools are the main types of cutting tools that are difficult to replace. Diamond tools can achieve high efficiency, high stability and long service life, and are indispensable in modern CNC machining processes.
Diamond cutter type
Natural Diamond Cutter
Natural diamonds have been used as cutting tools for hundreds of years. The natural single crystal diamond tool is finely ground and the edge can be sharpened with a cutting radius of 0.002μm. Ultra-fine cutting allows for extremely high part precision and very low surface roughness. It is a recognized, ideal and irreplaceable ultra-precision machining tool.
PCD Diamond Cutter
Natural diamonds are expensive. The diamond widely used in cutting machining is polycrystalline diamond (PCD). Since the early 1970s, polycrystalline diamond (PCD blade) has been successfully developed and natural diamond tools have been replaced by synthetic polycrystalline diamond.
PCD raw materials are abundant and the price is only a few tenths to one tenth of the price of natural diamond. PCD tools cannot produce extremely sharp edges, and the surface quality of the machined part is not as good as that of natural diamond.
It is currently not easy to manufacture PCD inserts with chipbreakers in the industry. Therefore, PCD can only be used for fine cutting of non-ferrous metals and non-metals, and it is difficult to achieve ultra-precision mirror cutting.
CVD Diamond Cutter
From the late 1970s to the early 1980s, CVD diamond technology appeared in Japan. CVD diamond refers to the synthesis of a diamond film on a heterogeneous substrate (such as carbide, ceramic, etc. ) by chemical vapor deposition (CVD). CVD diamond has exactly the same structure and properties as natural diamond.
The performance of CVD diamond is very close to that of natural diamond, and it has the advantages of natural single crystal diamond and polycrystalline diamond (PCD), and to a certain extent overcomes their shortcomings.
Diamond cutting tool performance characteristics
Extremely high hardness and wear resistance
Natural diamond is the hardest substance found in nature. Diamond has very high wear resistance. When machining high-hardness materials, the service life of diamond tools is 10 to 100 times, or even hundreds of times, that of carbide tools.
It has a very low coefficient of friction
The coefficient of friction between diamond and some non-ferrous metals is lower than that of other tools. The low coefficient of friction results in less deformation during processing and a reduced cutting force.
The tip is very sharp
The cutting edge of the diamond tool can be sharpened. Natural single crystal diamond tools can achieve edge sharpness up to 0.002~0.008μm for ultra-fine cutting and ultra-precision machining.
High thermal conductivity
The thermal conductivity and thermal diffusivity of diamond are high. This allows cutting heat to be easily dissipated, resulting in a lower cutting temperature of the tool.
Has a lower coefficient of thermal expansion
Diamond has a coefficient of thermal expansion several times lower than that of hard metal. The small change in tool size caused by cutting heat is especially important for precision and ultra-precision machining, where dimensional accuracy is critical.
Diamond tool application
Diamond tools are mainly used for fine cutting and boring of non-ferrous and non-metallic materials at high speeds. They are suitable for processing various wear-resistant non-metallic materials such as FRP powder metallurgy blanks, ceramic materials, etc., as well as various wear-resistant non-ferrous metals such as various silicon-aluminum alloys and non-ferrous finishing metallic.
However, the disadvantage of diamond tools is their poor thermal stability. When the cutting temperature exceeds 700°C to 800°C, the hardness of the diamond is completely lost. Furthermore, diamond tools are not suitable for cutting ferrous metals, as diamond (carbon) can easily interact with iron atoms at high temperatures, converting carbon atoms into graphite structures, which can make the tool extremely brittle.
Cubic Boron Nitride Cutter
The second superhard material, cubic boron nitride (CBN), synthesized by a method similar to the diamond manufacturing method, is second only to diamond in terms of hardness and thermal conductivity.
It has excellent thermal stability and does not oxidize when heated to 10,000 ℃ in atmosphere.
CBN has extremely stable chemical properties for ferrous metals and can be widely used in the processing of steel products.
Cubic Boron Nitride Tool Type
Cubic boron nitride (CBN) is a substance that does not exist in nature.
There are two types: single-crystalline and polycrystalline, namely single-crystalline CBN and polycrystalline cubic boron nitride (PCBN).
CBN is one of the isomers of boron nitride (BN) and has a structure similar to diamond.
PCBN (polycrystalline cubic boron nitride) is a polycrystalline material in which fine CBN materials are sintered through a bonding phase (TiC, TiN, Al, Ti, etc.) under high temperature and high pressure.
It is currently a tool material that uses artificially synthesized hardness close to diamond.
It is collectively referred to as a super-hard tool material.
PCBN is mainly used to make tools.
PCBN tools can be divided into integral PCBN inserts and carbide sintered PCBN composite inserts.
PCBN composite blade is formed by sintering a 0.5~1.0mm thick PCBN layer onto carbide with good strength and toughness.
Its properties combine good toughness, high hardness and wear resistance.
It solves the problems of low bending strength and difficult welding of CBN inserts.
Main properties and characteristics of cubic boron nitride
Although the hardness of cubic boron nitride is slightly lower than that of diamond, it is far higher than that of other high-hardness materials.
The great advantage of CBN is that its thermal stability is much higher than that of diamond, up to 1200 °C (compared to 700-800 °C for diamond).
Another notable advantage is that it is chemically inert and does not react chemically with iron at 1200-1300 °C.
The main performance characteristics of cubic boron nitride are as follows:
High hardness and wear resistance
The crystalline structure of CBN is similar to that of diamond and has comparable hardness and strength.
PCBN is particularly suitable for processing high-hardness materials that can only be pre-ground and can achieve superior surface quality of the workpiece.
High thermal stability
The heat resistance of CBN can reach 1400 to 1500 ℃, which is almost twice that of the heat resistance of diamond (700 to 800 ℃).
PCBN tools can cut superalloys and hardened steels at speeds 3 to 5 times faster than carbide tools.
Excellent chemical stability
Does not play a chemical role with iron-based materials up to 1200-1300°C.
It does not wear as sharply as diamond, but still maintains the hardness of carbide.
PCBN tools are suitable for cutting hardened steel and cooled cast iron parts, and can be widely used for high-speed cutting of cast iron.
It has good thermal conductivity
Although the thermal conductivity of CBN cannot keep up with that of diamond, the thermal conductivity of PCBN in various tool materials is second only to diamond, which is much higher than that of high-speed steel and hard alloy.
Has a lower coefficient of friction
A low coefficient of friction results in reduced cutting forces during cutting, reduced cutting temperatures and improved surface quality.
Cubic Boron Nitride Tool Application
Cubic boron nitride is suitable for finishing difficult-to-cut materials such as hardened steel, hard cast iron, superalloys, hard alloys and surface spraying materials.
The processing accuracy can reach IT5 (the hole is IT6) and the surface roughness value can be as small as Ra 1.25 to 0.20 μm.
The cubic boron nitride tool material has low toughness and bending resistance. Therefore, cubic boron nitride turning tools are not suitable for rough machining with low speed and large impact load. Furthermore, they are not suitable for cutting plastic materials (such as aluminum alloy, copper alloy, nickel-based alloy, steel with high plasticity, etc.) because cutting these metals may cause serious wear on the edge, which may deteriorate. the machining. surface.
C ceramic knife
Ceramic knives have the characteristics of high hardness, good wear resistance, excellent heat resistance and chemical stability, and are not easy to bond with metals.
Ceramic tools play an important role in CNC machining and have become one of the main tools for high-speed cutting and difficult-to-machine materials.
Ceramic tools are widely used for high-speed cutting, dry cutting, hard cutting and machining of difficult-to-machine materials.
Ceramic knives can efficiently process high-hardness materials that traditional knives cannot process and achieve “milling instead of grinding”.
The ideal cutting speed of ceramic tools can be 2 to 10 times that of carbide tools, greatly improving the efficiency of cutting production.
The main raw material used in ceramic materials for tools is the most abundant element in the Earth's crust. Therefore, the promotion and application of ceramic tools is of great importance to improve productivity, reduce processing costs and save strategic precious metals. This will greatly promote the advancement of cutting technology.
Types of ceramic materials for tools
The types of ceramic tool materials can be generally divided into three categories: alumina-based ceramics, silicon nitride-based ceramics and silicon-alumina nitride-based composite ceramics.
Among them, alumina and silicon nitride-based ceramic tool materials are the most widely used.
Silicon nitride-based ceramics are superior to alumina-based ceramics.
Ceramic tool performance and characteristics
High hardness and good wear resistance
Although the hardness of ceramic tools is not as high as PCD and PCBN, it is much higher than that of hard alloys and high-speed steel tools, reaching 93-95 HRA.
Ceramic tools can process high hardness materials that are difficult to machine with traditional tools and are suitable for high-speed cutting and hard cutting.
High temperature resistance and heat resistance
Ceramic tools can still cut at temperatures above 1200°C.
Ceramic tools have good mechanical properties at high temperatures.
The Al2O3 ceramic tool has excellent oxidation resistance and the cutting edge can be used continuously even in a glowing state.
Therefore, ceramic tools can achieve dry cutting, eliminating the need for cutting fluid.
Good chemical stability
Ceramic knives are not easy to bond with metal and have good corrosion resistance and chemical stability, which can reduce the bonding wear of the tool.
Low coefficient of friction
Ceramic knives have a low affinity for metals and a low coefficient of friction, which reduces cutting forces and temperatures.
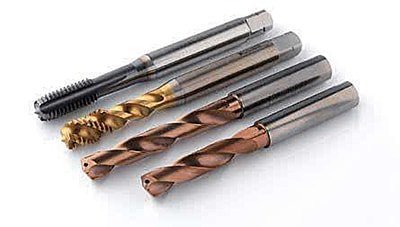
Ceramic tool application
Ceramic is one of the tool materials mainly used for high-speed finishing and semi-finishing.
Ceramic cutters are suitable for cutting all types of cast iron (gray cast iron, ductile iron, malleable cast iron, chilled cast iron, high-alloy wear-resistant cast iron) and steel (carbon structural steel, alloy, high strength steel, high manganese steel, hardened steel, etc.). They can also be used to cut copper alloys, graphite, engineering plastics and composites.
The performance of ceramic tool materials has low bending strength and low impact strength, and they are not suitable for cutting under low speed and impact load.
Coated tool
Tool coating is one of the important ways to improve tool performance.
The emergence of coated tools has brought a great advancement in tool cutting performance.
A coated tool is coated with one or more layers of a refractory compound with good wear resistance on a tougher tool body. This combines the tool base with a hard coating to maximize tool performance.
Coated tools can increase machining efficiency, increase machining accuracy, extend tool life and reduce machining costs.
About 80% of cutting tools used in new CNC machine tools use coated tools.
Coated tools will be the most important tool in the field of CNC machining in the future.
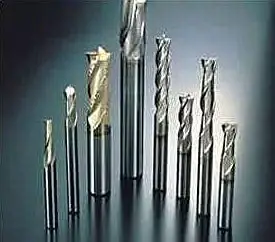
Coated tool type
According to the coating method:
Coated tools can be divided into chemical vapor deposition (CVD) coated tools and physical vapor deposition (PVD) coated tools.
Coated carbide tools are generally coated using the chemical vapor deposition method with a deposition temperature of about 1000°C.
Coated high speed steel tools generally adopt the physical vapor deposition method, and the deposition temperature is about 500°C.
According to the difference of coating tool base material:
Coated tools can be divided into carbide coated tools, high-speed steel coated tools, and ceramic and super-hard materials (diamond and cubic boron nitride) coated tools.
According to the nature of the coating material:
Coated tools can be divided into two broad categories, namely “hard” coated tools and “soft” coated tools.
The main purpose of “hard” coated tools is high hardness and wear resistance. Its main advantages are high hardness and good wear resistance, typically TiC and TiN coatings.
The goal of “soft” coated tools is a low coefficient of friction, also known as self-lubricating tools. Its coefficient of friction with the workpiece material is very low, only about 0.1, which can reduce bonding, friction, cutting force and cutting temperature.
Nanoaction tools have been developed recently.
This coated tool can be used on different coating material combinations (such as metal/metal, metal/ceramic, ceramic/ceramic, etc.) to meet different functional and performance requirements.
The well-designed nanocoating enables the tool material to have excellent anti-friction and anti-wear properties, making it suitable for high-speed dry cutting.
Lining Tool Features
Good mechanics and cutting performance
The coated tool combines the excellent properties of the base material and the coating material to maintain the good toughness and high strength of the substrate, as well as the high hardness, high wear resistance and low friction coefficient of the coating.
As a result, coated tools can cut twice as fast as uncoated tools and allow for higher feed rates.
The service life of coated tools is also improved.
Strong versatility
Coated tools have wide versatility and a wide processing range, and one coated tool can be used in place of multiple uncoated tools.
Coating thickness
Tool life increases as coating thickness increases.
However, when the coating thickness is saturated, tool life does not increase significantly.
When the coating is too thick, it is easy to cause peeling, and when the coating is too thin, the abrasion resistance is poor.
Removed
The coated blade has poor resharpening, complicated coating equipment, high process requirements and long coating time.
Lining material
Cutting tools with different coating materials have different cutting performance.
For example, TiC coatings have an advantage in cutting at low speeds, and TiN is suitable for high-speed cutting.
Application of coated tools
Coated tools have great potential in the field of CNC machining and will be the most important tool in the field of CNC machining in the future.
Coating technology has been applied to end mills, reamers, drills, compound hole machining tools, gear hobs, pinion hobs, razor mills, forming broaches and various machine indexable inserts.
It meets the needs of high-speed machining of various steels and cast iron, heat-resistant alloys and non-ferrous metals.
C arbide tip cutting tool
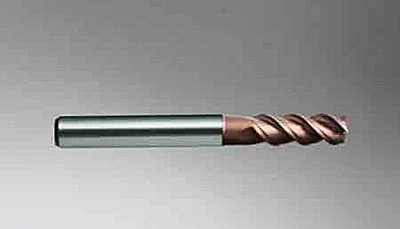
Carbide tools, especially indexable carbide tools, are the main products for CNC machining tools.
Since the 1980s, various types of integral and indexable carbide tools or inserts have been extended to various fields of cutting tools.
Among them, indexable carbide tools have been expanded from simple turning tools and face mills to various precision, complex and forming tools.
Carbide tool type
According to the main chemical composition, carbide can be divided into tungsten carbide-based hard alloy and carbon (titanium nitride)-based hard alloy (TiC(N)).
Tungsten carbide-based cemented carbides include tungsten cobalt (YG), tungsten cobalt titanium (YT) and rare carbides (YW), each of which has advantages and disadvantages.
The main components are tungsten carbide (WC), titanium carbide (TiC), tantalum carbide (TaC), niobium carbide (NbC), etc., and the commonly used metal bonding phase is Co.
Carbon (nitrogen) and titanium-based cemented carbide is a hard alloy containing TiC as the main component (some of which are added with other carbides or nitrides), and the commonly used metal bonding phases are Mo and Ni.
The International Organization for Standardization (ISO) classifies carbide cutting into three categories:
K class, including K10 to K40, is equivalent to China's YG class (the main component is WC.Co).
P class, including P01 to P50, is equivalent to YT in China (the main component is WC.TiC.Co).
Class M, including M10 to M40, is equivalent to YW in China (the main component is WC-TiC-TaC(NbC)-Co).
Each class represents a series of alloys from high hardness to maximum toughness, with numbers between 01 and 50, respectively.
Performance characteristics of carbide tools
High hardness
Carbide tools are made by powder metallurgy from carbides with high hardness and melting points (called hard phase) and metal binders (called bonded phases).
Its hardness is 89-93 HRA, much higher than that of high-speed steel.
At 540°C, the hardness still reaches 82-87 HRA.
At room temperature, the hardness value is the same as that of high-speed steel (83 ~ 86 HRA).
The hardness value of carbide varies with the nature, quantity, particle size and content of the carbide bonded metal phase and generally decreases as the content of the bonded metal phase increases.
When the content of the binder phase is the same, the hardness of YT alloy is greater than that of YG alloy.
The alloy to which TaC (NbC) is added has a hardness at high temperatures.
Bending strength and toughness
The flexural strength of commonly used cemented carbides is in the range of 900 ~ 1500 MPa.
The greater the content of the metallic bonding phase, the greater the flexural strength.
When the binder content is the same, the strength of the YG-based alloy (WC-Co) is greater than that of the YT-based alloy (WC-TiC-Co), and the strength decreases as the content increases. of TiC increases.
Carbide is a brittle material, and its impact strength is only 1/30 ~ 1/8 of that of high-speed steel at room temperature.
Applications of commonly used carbide tools
YG alloys are mainly used to process cast iron, non-ferrous metals and non-metallic materials.
Fine-grained hard alloys (such as YG3X, YG6X) have higher hardness and wear resistance than medium-grained alloys when the cobalt content is the same. They are suitable for processing some special hard cast irons, austenitic stainless steel, heat-resistant alloys, titanium alloys, hard bronze and wear-resistant insulation materials.
The outstanding advantages of YT type cemented carbides are high hardness, good heat resistance, high hardness and compressive strength at high temperatures, higher YG resistance and better oxidation resistance.
Therefore, when the tool requires high heat and wear resistance, a grade with high TiC content should be selected.
YT alloys are suitable for processing steel materials, but are not suitable for processing titanium alloys and silicon aluminum alloys.
YW alloys have the properties of YG and YT alloys and have good comprehensive properties. They can be used to process steel materials as well as to process cast iron and non-ferrous metals.
Such alloys, if cobalt content is added appropriately, can be used with high strength and for grinding and interrupted cutting of various difficult-to-machine materials.
High Speed Steel Cutter
High-speed steel (HSS) is a high-alloy tool steel with more alloying elements such as W, Mo, Cr, and V.
High speed steel cutters have excellent comprehensive properties in terms of strength, toughness and finish.
In complex tools, especially for the production of drilling tools, milling cutters, thread cutters, broaches, cutting tools and other complex blade-shaped tools, high-speed steel still dominates.
High speed steel tools are easy to grind sharp cutting edges.
High speed steel can be classified into general purpose high speed steel and high performance high speed steel depending on the application.
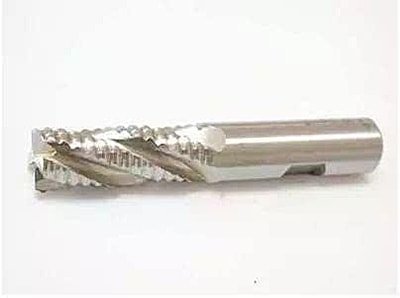
High Speed Steel Universal Cutter
General-purpose high-speed steel can be divided into two types: tungsten steel and tungsten-molybdenum steel.
This type of high-speed steel contains 0.7% to 0.9% carbon (C).
According to the amount of tungsten contained in the steel, it can be divided into tungsten steel with 12% or 18% tungsten.
A tungsten-molybdenum steel containing 6% or 8% tungsten and a molybdenum steel containing 2% tungsten or none.
General purpose high speed steel has a certain hardness (63-66 HRC) and wear resistance, high strength and toughness, good plasticity and processing technology.
Therefore, it is widely used in the manufacture of various complex tools.
Tungsten Steel
The general type of tungsten steel for high speed steel is W18Cr4V (referred to as W18), which has good comprehensive performance. High temperature hardness is 48.5 HRC at 600°C and can be used to manufacture a variety of complex tools. It has the advantages of good grindability and low sensitivity to decarburization. However, due to the high carbide content, the distribution is less uniform, the particles are larger, and the strength and toughness are not high.
Tungsten Carbide Steel
Refers to a high-speed steel obtained by replacing a part of tungsten in tungsten steel with molybdenum.
The typical grade of tungsten-molybdenum steel is W6Mo5Cr4V2 (referred to as M2).
The carbide particles of M2 are fine and uniform, and the high temperature strength, toughness and plasticity are better than W18Cr4V.
Another type of tungsten-molybdenum steel is W9Mo3Cr4V (referred to as W9). Its thermal stability is slightly higher than that of M2 steel, and its flexural strength and toughness are better than W6Mo5Cr4V2, and it has good machinability.
High Performance High Speed Steel Cutter
High-performance high-speed steel refers to a new type of steel that adds some carbon content, vanadium content and alloy elements such as Co and Al to the general-purpose high-speed steel component, thereby improving its heat resistance and wear resistance .
There are mainly the following main categories:
High carbon high speed steel
High carbon high speed steel (such as 95W18Cr4V), high hardness at room temperature and high temperature, suitable for making common steel and cast iron, drills with high wear resistance, reamer, tap and milling cutter or tools for material processing hard. Not suitable for large impacts.
High vanadium high speed steel
Typical grades, such as W12Cr4V4Mo (abbreviated EV4), increase V by 3% to 5%.
It has good wear resistance and is suitable for cutting materials with high tool wear, such as fiber, hard rubber, plastic, etc. It can also be used to process stainless steel, high-strength steel and high-temperature alloys.
Cobalt high speed steel
It is a super high-speed steel containing cobalt, with a typical grade as W2Mo9Cr4VCo8 (referred to as M42).
It has a high hardness of 69-70 HRC and is suitable for processing difficult-to-machine materials such as high-strength heat-resistant steel, high-temperature alloy and titanium alloy.
M42 is highly grindable and suitable for making complex tools, but it is not suitable for working under impact cutting conditions.
Aluminum High Speed Steel
It is a type of aluminum super-hard high-speed steel, typical grade, such as W6Mo5Cr4V2Al, (abbreviation 501).
The high temperature hardness at 6000C also reaches 54HRC and the cutting performance is equivalent to M42.
Suitable for manufacturing milling cutters, drills, reamers, gear hobs, broaches, etc., for processing alloy steel, stainless steel, high-strength steel and high-temperature alloys.
Nitrogen Superhard High Speed Steel
Typical grades such as W12M03Cr4V3N, known as (V3N), are nitrogen-containing super-hard high-speed steels.
Hardness, strength and toughness are comparable to M42.
It can be used as a substitute for cobalt-containing high-speed steel for low-speed cutting of difficult-to-machine materials and low-speed high-precision machining.
Casting of high-speed steel and high-speed steel for powder metallurgy
According to different manufacturing processes, high-speed steel can be divided into smelting high-speed steel and powder metallurgy high-speed steel.
High speed steel sm elting
Both common high-speed steel and high-performance high-speed steel are manufactured using a melting method.
They are turned into tools through processes such as casting, ingot casting and rolling.
A serious problem likely to occur in high-speed steel casting is carbide segregation. Hard and brittle carbides are unevenly distributed in high-speed steel and have coarse grains (up to several tens of microns), which negatively affects the wear resistance, toughness and cutting performance of high-speed steel tools.
High-speed steel for powder metallurgy (PM HSS)
Powder metallurgy high speed steel (PM HSS) is molten steel melted in a high-frequency induction furnace and atomized by high-pressure argon or pure nitrogen. It is then tempered to obtain a fine and uniform crystalline structure (high-speed steel powder). The obtained powder is then pressed into a raw sheet under high temperature and high pressure, or first formed into a steel plate and then forged and rolled into tool shape.
Compared with high-speed steel produced by the melting method, PM HSS has the advantages of fine and uniform carbide grains, as well as higher strength, toughness and wear resistance.
In the field of complex CNC tools, PM HSS tools will play an increasingly important role. Typical classes include F15, FR71, GFl, GF2, GF3, PT1, PVN, etc.
It can be used to make large-sized, impact-resistant and impact-resistant tools as well as precision tools.
S election principles of CNC cutting tool materials
At present, widely used CNC tool materials include diamond tools, cubic boron nitride tools, ceramic tools, coated tools, carbide tools and high-speed steel tools.
The total number of tool materials is large and their performance varies greatly. The main performance indicators of various tool materials are as follows:
Types | Density g/ cm2 |
Heat resistant ℃ |
Toughness | Doubling strength MPa |
Thermal conductivity with (mK) |
Coefficient of thermal expansion ×10 -5 /℃ | |
---|---|---|---|---|---|---|---|
Polycrystalline diamond | 3.47-3.56 | 700-800 | >9000HV | 600-1100 | 210 | 3.1 | |
Polycrystalline Cubic Boron Carbide | 3.44-3.49 | 1300-1500 | 4500HV | 500-800 | 130 | 4.7 | |
Ceramic knife | 3.1-5.0 | >1200 | 91-95HRA | 700-1500 | 15.0-38.0 | 7.0-9.0 | |
Hard metal | Tungsten Cobalt | 14.0-15.5 | 800 | 89-91.5HRA | 1000-2350 | 74.5-87.9 | 3-7.5 |
tungsten cobalt titanium | 9.0-14.0 | 900 | 89-92.5 HRA | 800-1800 | 20.9-62.8 | ||
General league | 12.0-14.0 | 1000-1100 | ~92.5HRA | / | / | ||
TiC-based alloy | 5.0-7.0 | 1100 | 92-93.5HRA | 1150-1350 | / | 8.2 | |
High speed steel | 8.0-8.8 | 600-700 | 62-70HRC | 2000-4500 | 15.0-30.0 | 8-12 |
Cutting tool materials for CNC machining should be selected based on the part to be machined and the nature of the process.
The selection of cutting tool materials must be suitable for the machined object. The matching of cutting tool material with the processing object mainly refers to the matching of the mechanical properties, physical properties and chemical properties of the two to obtain the longest tool life and maximum productivity of cutting processing.
Match the cutting tool material to the mechanical properties of the machined object
The mechanical property matching problem between the cutting tool and the machined object mainly refers to the mechanical property parameters such as strength, toughness and hardness of the tool and workpiece material.
Tool materials with different mechanical properties are suitable for machining part materials.
The order of tool material hardness is as follows: diamond tool > cubic boron nitride tool > ceramic tool > hard alloy > high speed steel.
The order of bending strength of tool material is as follows: high-speed steel > hard alloy > ceramic tool > diamond tool and cubic boron nitride.
The toughness order of tool material is as follows: high-speed steel > hard alloy > cubic boron nitride, diamond and ceramic tools.
High hardness part materials must be machined with higher hardness tools. The hardness of the tool material must be greater than the hardness of the workpiece material, generally greater than 60 HRC. The higher the hardness of the tool material, the better its wear resistance.
For example, when the amount of cobalt in carbide increases, the strength and toughness increase, the hardness decreases, and it is suitable for coarse processing. When the amount of cobalt decreases, the hardness and wear resistance increase, which is suitable for finishing.
Tools with excellent high-temperature mechanical properties are especially suitable for high-speed machining. The excellent high temperature performance of ceramic tools allows them to be cut at high speeds, allowing cutting speeds to be 2 to 10 times higher than those of carbide.
The material of the cutting tool corresponds to the physical properties of the machined object
Tools with different physical properties, such as high-speed steel tools with high thermal conductivity and low melting point, ceramic tools with high melting point and low thermal expansion, and diamond tools with high thermal conductivity and low thermal expansion, are suitable for processing workpieces. work. materials.
When machining a workpiece with low thermal conductivity, a tool material with better thermal conductivity should be used to allow cutting heat to be transmitted quickly to lower the cutting temperature.
Due to the high thermal conductivity and thermal diffusivity of diamond, the cutting heat is easily dissipated and does not cause large thermal deformation. This is especially important for precision machining tools with high dimensional accuracy.
Heat resistance temperature of various tool materials:
700~8000C for diamond tools, 13000~15000C for PCBN tools, 1100~12000C for ceramic tools, 900~11000C for TiC(N) based hard alloys, WC based hard ultrafine grains Alloy quality is 800 to 9000 C, and the HSS is 600 to 7000 C.
Thermal conductivity sequence of various tool materials:
PCD > PCBN > WC based carbide > TiC(N) based carbide > HSS > Si3N4 based ceramic > A1203 based ceramic.
The order of thermal expansion coefficient of various tool materials is:
HSS>WC-based cemented carbide>TiC(N)>A1203-based ceramic>PCBN>Si3N4-based ceramic>PCD.
The order of thermal shock resistance of various tool materials is:
HSS > WC based carbide > Si3N4 based ceramic > PCBN > PCD > TiC(N) based carbide > A1203 based ceramic.
The material of the cutting tool corresponds to the chemical properties of the machined object
The correspondence of the chemical properties of the cutting tool material with the processing object mainly refers to the correspondence of the chemical properties of the tool material with the chemical affinity, chemical reaction, diffusion and dissolution of the workpiece material.
Tools with different materials are suitable for machining different workpiece materials.
The anti-stick temperature of various tool materials (and steel) is:
PCBN>ceramic>hard alloy>HSS.
The oxidation temperature of various tool materials is:
ceramic>PCBN>hard alloy>diamond>HSS.
The diffusion resistance of various tool materials (for steel) is:
diamond > Si3N4-based ceramic > PCBN > A1203-based ceramic.
The diffusion force (for titanium) is:
A1203-based ceramic > PCBN > SiC > Si3N4 > diamond.
Reasonable choice of materials for CNC tools
In general, PCBN, ceramic tools, coated carbide and TiCN-based carbide tools are suitable for CNC machining of ferrous metals such as steel.
PCD tools are suitable for processing non-ferrous materials such as Al, Mg, Cu, alloys and non-metallic materials.
Table 2 lists some of the part materials that are suitable for machining using the above tool materials.
snipping tool | High toughness steel |
Warm resistant turns on |
Titanium turns on |
Nickel based super league |
Cast iron |
Pure steel |
High silicon aluminum turns on |
FRP compound material |
---|---|---|---|---|---|---|---|---|
PCD | × | × | ◎ | × | × | × | ◎ | ◎ |
PCBN | ◎ | ◎ | ○ | ◎ | ◎ | ● | ● | |
Ceramic knife | ◎ | ◎ | × | ◎ | ◎ | ● | × | × |
Carbide layer | ○ | ◎ | ◎ | ● | ◎ | ◎ | ● | ● |
TiCN-based hard alloy | ● | × | × | × | ◎ | ● | × | × |
Observation:
◎ – Excellent
○ – Good
● – OK
× – Bad