Advanced processing equipment and high-performance CNC tools can fully utilize their due performance and obtain good economic benefits.
With the rapid development of tool materials, the physical properties, mechanical properties and cutting performance of various new tool materials have been greatly improved, and the range of applications has continuously expanded.
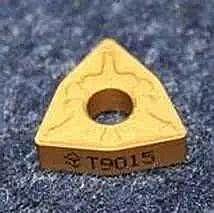
High Speed Steel Universal Cutter
General-purpose high-speed steel can be divided into two types: tungsten steel and tungsten-molybdenum steel.
This type of high-speed steel contains 0.7% to 0.9% carbon (C).
According to the amount of tungsten contained in the steel, it can be divided into tungsten steel with 12% or 18% tungsten.
A tungsten-molybdenum steel containing 6% or 8% tungsten and a molybdenum steel containing 2% tungsten or none.
General purpose high speed steel has a certain hardness (63-66 HRC) and wear resistance, high strength and toughness, good plasticity and processing technology.
Therefore, it is widely used in the manufacture of various complex tools.
Tungsten Steel
The general type of tungsten steel for high speed steel is W18Cr4V (referred to as W18), which has good comprehensive performance. High temperature hardness is 48.5 HRC at 600°C and can be used to manufacture a variety of complex tools. It has the advantages of good grindability and low sensitivity to decarburization. However, due to the high carbide content, the distribution is less uniform, the particles are larger, and the strength and toughness are not high.
Tungsten Carbide Steel
Refers to a high-speed steel obtained by replacing a part of tungsten in tungsten steel with molybdenum.
The typical grade of tungsten-molybdenum steel is W6Mo5Cr4V2 (referred to as M2).
The carbide particles of M2 are fine and uniform, and the high temperature strength, toughness and plasticity are better than W18Cr4V.
Another type of tungsten-molybdenum steel is W9Mo3Cr4V (referred to as W9). Its thermal stability is slightly higher than that of M2 steel, and its flexural strength and toughness are better than W6Mo5Cr4V2, and it has good machinability.
High Performance High Speed Steel Cutter
High-performance high-speed steel refers to a new type of steel that adds some carbon content, vanadium content and alloy elements such as Co and Al to the general-purpose high-speed steel component, thereby improving its heat resistance and wear resistance .
There are mainly the following main categories:
High carbon high speed steel
High carbon high speed steel (such as 95W18Cr4V), high hardness at room temperature and high temperature, suitable for making common steel and cast iron, drills with high wear resistance, reamer, tap and milling cutter or tools for material processing hard. Not suitable for large impacts.
High vanadium high speed steel
Typical grades, such as W12Cr4V4Mo (abbreviated EV4), increase V by 3% to 5%.
It has good wear resistance and is suitable for cutting materials with high tool wear, such as fiber, hard rubber, plastic, etc. It can also be used to process stainless steel, high-strength steel and high-temperature alloys.
Cobalt high speed steel
It is a super high-speed steel containing cobalt, with a typical grade as W2Mo9Cr4VCo8 (referred to as M42).
It has a high hardness of 69-70 HRC and is suitable for processing difficult-to-machine materials such as high-strength heat-resistant steel, high-temperature alloy and titanium alloy.
M42 is highly grindable and suitable for making complex tools, but it is not suitable for working under impact cutting conditions.
Aluminum High Speed Steel
It is a type of aluminum super-hard high-speed steel, typical grade, such as W6Mo5Cr4V2Al, (abbreviation 501).
The high temperature hardness at 6000C also reaches 54HRC and the cutting performance is equivalent to M42.
Suitable for manufacturing milling cutters, drills, reamers, gear hobs, broaches, etc., for processing alloy steel, stainless steel, high-strength steel and high-temperature alloys.
Nitrogen Superhard High Speed Steel
Typical grades such as W12M03Cr4V3N, known as (V3N), are nitrogen-containing super-hard high-speed steels.
Hardness, strength and toughness are comparable to M42.
It can be used as a substitute for cobalt-containing high-speed steel for low-speed cutting of difficult-to-machine materials and low-speed high-precision machining.
Casting of high-speed steel and high-speed steel for powder metallurgy
According to different manufacturing processes, high-speed steel can be divided into smelting high-speed steel and powder metallurgy high-speed steel.
High speed steel sm elting
Both common high-speed steel and high-performance high-speed steel are manufactured using a melting method.
They are turned into tools through processes such as casting, ingot casting and rolling.
A serious problem likely to occur in high-speed steel casting is carbide segregation. Hard and brittle carbides are unevenly distributed in high-speed steel and have coarse grains (up to several tens of microns), which negatively affects the wear resistance, toughness and cutting performance of high-speed steel tools.
High-speed steel for powder metallurgy (PM HSS)
Powder metallurgy high speed steel (PM HSS) is molten steel melted in a high-frequency induction furnace and atomized by high-pressure argon or pure nitrogen. It is then tempered to obtain a fine and uniform crystalline structure (high-speed steel powder). The obtained powder is then pressed into a raw sheet under high temperature and high pressure, or first formed into a steel plate and then forged and rolled into tool shape.
Compared with high-speed steel produced by the melting method, PM HSS has the advantages of fine and uniform carbide grains, as well as higher strength, toughness and wear resistance.
In the field of complex CNC tools, PM HSS tools will play an increasingly important role. Typical classes include F15, FR71, GFl, GF2, GF3, PT1, PVN, etc.
It can be used to make large-sized, impact-resistant and impact-resistant tools as well as precision tools.
S election principles of CNC cutting tool materials
At present, widely used CNC tool materials include diamond tools, cubic boron nitride tools, ceramic tools, coated tools, carbide tools and high-speed steel tools.
The total number of tool materials is large and their performance varies greatly. The main performance indicators of various tool materials are as follows:
Types | Density g/ cm2 |
Heat resistant ℃ |
Toughness | Doubling strength MPa |
Thermal conductivity with (mK) |
Coefficient of thermal expansion ×10 -5 /℃ | |
---|---|---|---|---|---|---|---|
Polycrystalline diamond | 3.47-3.56 | 700-800 | >9000HV | 600-1100 | 210 | 3.1 | |
Polycrystalline Cubic Boron Carbide | 3.44-3.49 | 1300-1500 | 4500HV | 500-800 | 130 | 4.7 | |
Ceramic knife | 3.1-5.0 | >1200 | 91-95HRA | 700-1500 | 15.0-38.0 | 7.0-9.0 | |
Hard metal | Tungsten Cobalt | 14.0-15.5 | 800 | 89-91.5HRA | 1000-2350 | 74.5-87.9 | 3-7.5 |
tungsten cobalt titanium | 9.0-14.0 | 900 | 89-92.5 HRA | 800-1800 | 20.9-62.8 | ||
General league | 12.0-14.0 | 1000-1100 | ~92.5HRA | / | / | ||
TiC-based alloy | 5.0-7.0 | 1100 | 92-93.5HRA | 1150-1350 | / | 8.2 | |
High speed steel | 8.0-8.8 | 600-700 | 62-70HRC | 2000-4500 | 15.0-30.0 | 8-12 |
Cutting tool materials for CNC machining should be selected based on the part to be machined and the nature of the process.
The selection of cutting tool materials must be suitable for the machined object. The matching of cutting tool material with the processing object mainly refers to the matching of the mechanical properties, physical properties and chemical properties of the two to obtain the longest tool life and maximum productivity of cutting processing.
Match the cutting tool material to the mechanical properties of the machined object
The mechanical property matching problem between the cutting tool and the machined object mainly refers to the mechanical property parameters such as strength, toughness and hardness of the tool and workpiece material.
Tool materials with different mechanical properties are suitable for machining part materials.
The order of tool material hardness is as follows: diamond tool > cubic boron nitride tool > ceramic tool > hard alloy > high speed steel.
The order of bending strength of tool material is as follows: high-speed steel > hard alloy > ceramic tool > diamond tool and cubic boron nitride.
The toughness order of tool material is as follows: high-speed steel > hard alloy > cubic boron nitride, diamond and ceramic tools.
High hardness part materials must be machined with higher hardness tools. The hardness of the tool material must be greater than the hardness of the workpiece material, generally greater than 60 HRC. The higher the hardness of the tool material, the better its wear resistance.
For example, when the amount of cobalt in carbide increases, the strength and toughness increase, the hardness decreases, and it is suitable for coarse processing. When the amount of cobalt decreases, the hardness and wear resistance increase, which is suitable for finishing.
Tools with excellent high-temperature mechanical properties are especially suitable for high-speed machining. The excellent high temperature performance of ceramic tools allows them to be cut at high speeds, allowing cutting speeds to be 2 to 10 times higher than those of carbide.
The material of the cutting tool corresponds to the physical properties of the machined object
Tools with different physical properties, such as high-speed steel tools with high thermal conductivity and low melting point, ceramic tools with high melting point and low thermal expansion, and diamond tools with high thermal conductivity and low thermal expansion, are suitable for processing workpieces. work. materials.
When machining a workpiece with low thermal conductivity, a tool material with better thermal conductivity should be used to allow cutting heat to be transmitted quickly to lower the cutting temperature.
Due to the high thermal conductivity and thermal diffusivity of diamond, the cutting heat is easily dissipated and does not cause large thermal deformation. This is especially important for precision machining tools with high dimensional accuracy.
Heat resistance temperature of various tool materials:
700~8000C for diamond tools, 13000~15000C for PCBN tools, 1100~12000C for ceramic tools, 900~11000C for TiC(N) based hard alloys, WC based hard ultrafine grains Alloy quality is 800 to 9000 C, and the HSS is 600 to 7000 C.
Thermal conductivity sequence of various tool materials:
PCD > PCBN > WC based carbide > TiC(N) based carbide > HSS > Si3N4 based ceramic > A1203 based ceramic.
The order of thermal expansion coefficient of various tool materials is:
HSS>WC-based cemented carbide>TiC(N)>A1203-based ceramic>PCBN>Si3N4-based ceramic>PCD.
The order of thermal shock resistance of various tool materials is:
HSS > WC based carbide > Si3N4 based ceramic > PCBN > PCD > TiC(N) based carbide > A1203 based ceramic.
The material of the cutting tool corresponds to the chemical properties of the machined object
The correspondence of the chemical properties of the cutting tool material with the processing object mainly refers to the correspondence of the chemical properties of the tool material with the chemical affinity, chemical reaction, diffusion and dissolution of the workpiece material.
Tools with different materials are suitable for machining different workpiece materials.
The anti-stick temperature of various tool materials (and steel) is:
PCBN>ceramic>hard alloy>HSS.
The oxidation temperature of various tool materials is:
ceramic>PCBN>hard alloy>diamond>HSS.
The diffusion resistance of various tool materials (for steel) is:
diamond > Si3N4-based ceramic > PCBN > A1203-based ceramic.
The diffusion force (for titanium) is:
A1203-based ceramic > PCBN > SiC > Si3N4 > diamond.
Reasonable choice of materials for CNC tools
In general, PCBN, ceramic tools, coated carbide and TiCN-based carbide tools are suitable for CNC machining of ferrous metals such as steel.
PCD tools are suitable for processing non-ferrous materials such as Al, Mg, Cu, alloys and non-metallic materials.
Table 2 lists some of the part materials that are suitable for machining using the above tool materials.
snipping tool | High toughness steel |
Warm resistant turns on |
Titanium turns on |
Nickel based super league |
Cast iron |
Pure steel |
High silicon aluminum turns on |
FRP compound material |
---|---|---|---|---|---|---|---|---|
PCD | × | × | ◎ | × | × | × | ◎ | ◎ |
PCBN | ◎ | ◎ | ○ | ◎ | ◎ | ● | ● | |
Ceramic knife | ◎ | ◎ | × | ◎ | ◎ | ● | × | × |
Carbide layer | ○ | ◎ | ◎ | ● | ◎ | ◎ | ● | ● |
TiCN-based hard alloy | ● | × | × | × | ◎ | ● | × | × |
Observation:
◎ – Excellent
○ – Good
● – OK
× – Bad