There are many types of CNC machine tools available today, each with different structures and functions. They can generally be classified according to the following methods:
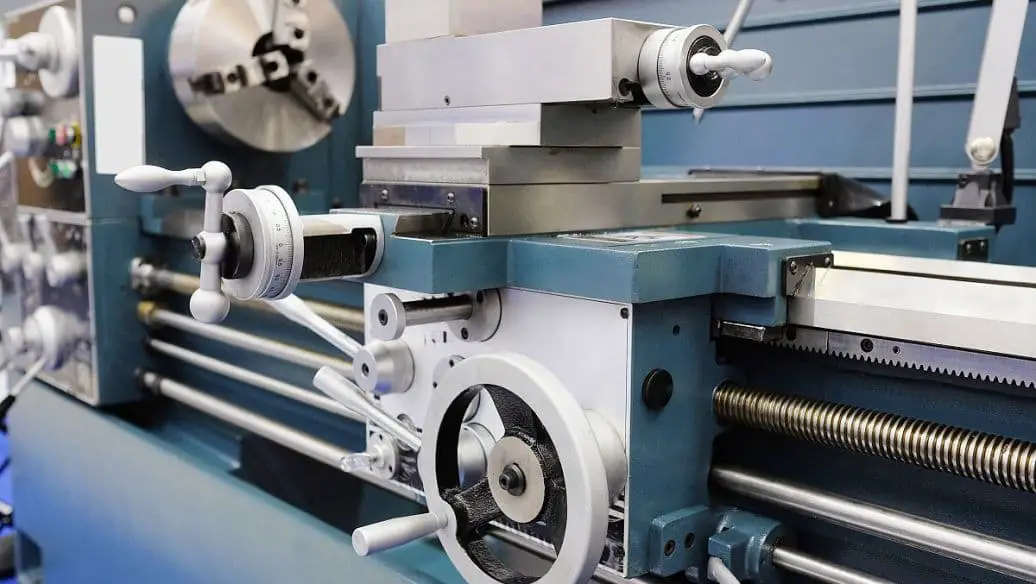
1. Classification based on the motion trajectory of the machine tool
According to the different movement trajectories of the machine tool, it can be divided into point-to-point control CNC machine tools, linear control CNC machine tools and contour control CNC machine tools.
(1) Point-to-point control CNC machine tools
Point-to-point control (also known as positioning control or point control) refers to the movement of the tool from one position to another without strict requirements for the intermediate trajectory, as long as the tool reaches the target position accurately.
The characteristic of point-to-point control machine tools is that they only control the precise positioning of moving parts from one position to another, without carrying out any processing during their movement and positioning.
To minimize the movement and positioning time of moving parts, the movement between two related points is first carried out at a fast speed until close to the new position, and then continuously decelerated or gradually decelerated to slowly approach the positioning point, ensuring its positioning accuracy. .
The schematic diagram of point-to-point control processing is shown in Figure 1-3.
This type of machine tool mainly includes CNC boring machines, CNC drilling machines, CNC spot welding machines and CNC bending machines. The corresponding CNC device is called a point-to-point control CNC device.
(2) Linear control CNC machine tools
Linear control (also known as parallel cutting control) not only controls the precise position (distance) of two related points, but also ensures that the trajectory between them is a straight line and controls the speed of movement because this type of machine- tool performs cutting processing while moving between two points.
The characteristic of linear control CNC machine tools is that they control not only the precise positions of the tool relative to the workpiece, but also the speed and trajectory of movement between two related points, the trajectory of which is usually composed of parallel straight segments . for each axis.
The difference between linear control and point-to-point control CNC machine tools is that when the moving parts of the machine move, they can perform cutting processing along the direction of a coordinate axis and have more auxiliary functions than the Point-to-point CNC control machine tools.
The schematic diagram of linear control processing is shown in Figure 1-4.
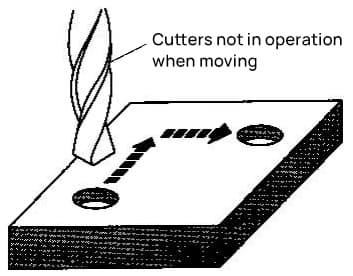
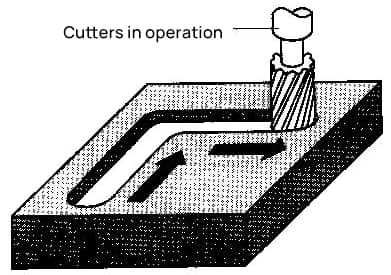
This type of machine tool mainly includes CNC coordinate lathes, CNC grinding machines, and CNC boring and milling machines. The corresponding CNC device is called a linear control CNC device.
(3) CNC machine tools for contour control
Contour control, also known as continuous control, is a function that most CNC machine tools have. The characteristic of CNC machine tools for contour control is that they can simultaneously control two or more axes with interpolation capabilities.
They not only control the position and movement speed of the tool at each point during processing, but also can process any curve or surface shape.
The schematic diagram of contour control processing is shown in Figure 1-5.
CNC coordinated lathes, CNC milling machines, machining centers, etc., belong to contour control machine tools. The corresponding CNC device is called a contour control device. Contour control devices are much more complex in structure and more fully functional than point-to-point and linear control devices.
2. Classification based on servo system type
According to different types of servo systems, CNC machine tools can be divided into open loop control CNC machine tools, closed loop control CNC machine tools and semi-closed loop control CNC machine tools.
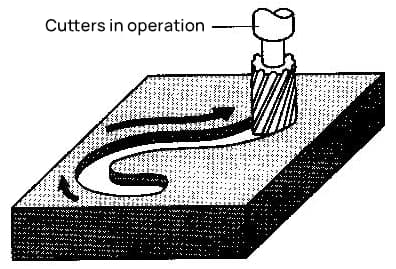
(1) Open Loop Control CNC Machine Tools
Open-loop control CNC machine tools generally do not have position sensing elements, and the servo drive components are generally stepper motors.
After the CNC device sends a power pulse, the pulse is amplified and drives the stepper motor to rotate at a fixed angle, and then the worktable is driven to move through mechanical transmission.
The open-loop servo system is shown in Figure 1-6. This type of system has no feedback values from the controlled object, and its accuracy depends entirely on the step size accuracy of the stepper motor and the accuracy of the mechanical transmission.
Its control circuit is simple, easy to adjust and has low precision (generally up to 0.02mm), generally applied to small or economical CNC machine tools.
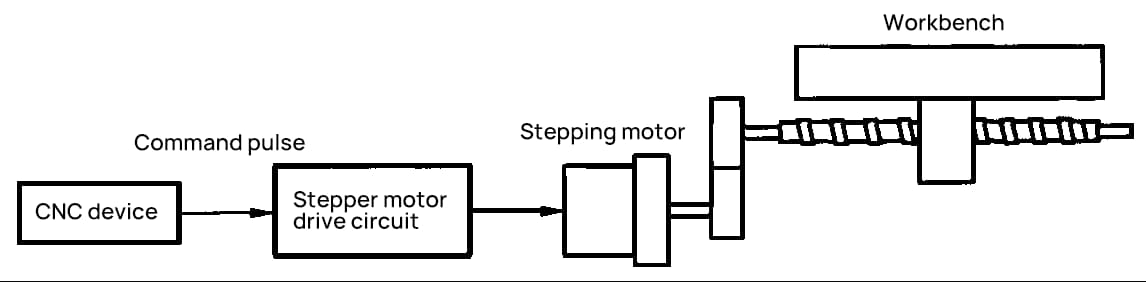
(2) Closed-loop control CNC machine tools
Closed-loop control CNC machine tools often have position sensing elements that can detect the actual displacement of the work table at any time and feed it back to the CNC device. After comparing it with the set instruction value, the servo motor is controlled using the difference until the difference is zero.
This type of machine tool generally uses DC or AC servo motors for drive. Commonly used position sensing elements are linear grids, magnetic grids, synchronization sensors, etc. The closed-loop servo system is shown in Figure 1-7.
From the working principle of the closed-loop servo system, it can be seen that the accuracy of the system mainly depends on the accuracy of the position sensing device. In theory, it can completely eliminate the impact of errors in transmission components in part processing.
Therefore, this system can achieve high processing accuracy. The design and adjustment of the closed-loop servo system presents great difficulty, and the price of linear displacement sensing elements is relatively expensive, mainly used in some high-precision boring machines and milling machines, ultra-precision lathes and machining centers.
(3) Semi-closed loop control CNC machine tools
Semi-closed-loop control CNC machine tools generally install the position sensing elements on the servo motor shaft or ball screw end, but do not directly feed back the machine tool displacement.
Instead, they detect the rotation angle of the servo system and send that signal back to the CNC device for instruction comparison, using the difference to control the servo motor. The semi-closed loop servo system is shown in Figure 1-8.
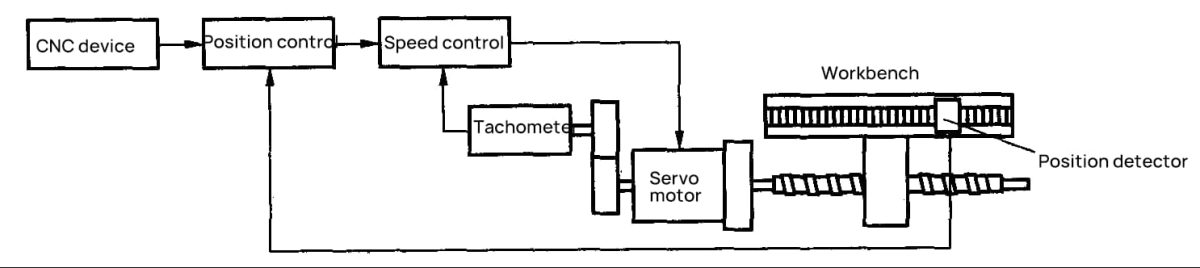
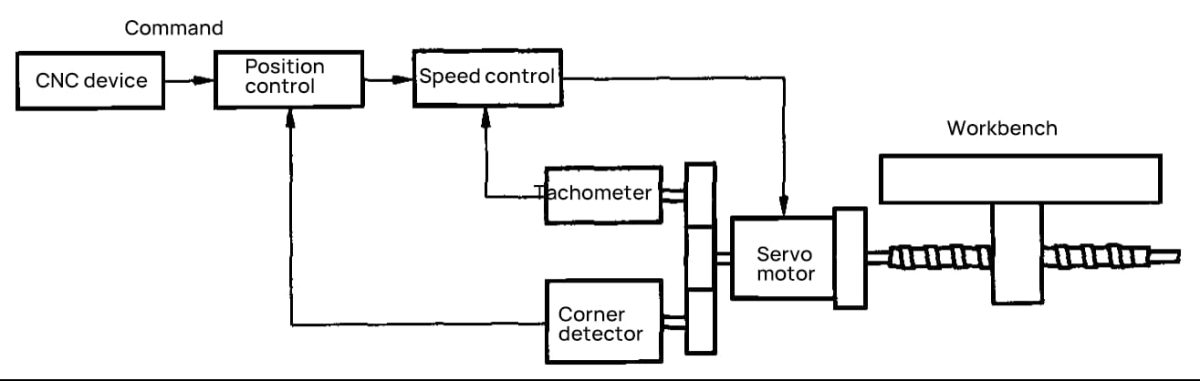
Since the feedback signal of the semi-closed-loop servo system is obtained from the rotation of the motor shaft, the mechanical transmission device in the system is outside the feedback loop, and its stiffness, intermittency and other non-linear factors have no effect on the stability of the system, facilitating debugging.
Similarly, the positioning accuracy of the machine tool mainly depends on the accuracy of the mechanical transmission device.
However, modern CNC devices have feed error compensation and intermittent compensation functions, so it is not necessary to greatly increase the accuracy of the various components of the transmission device.
Accuracy can be improved to a level acceptable to most users through compensation. Furthermore, linear displacement detection devices are much more expensive than angular displacement detection devices.
Therefore, except for large machine tools that require very high positioning accuracy or have special long travel requirements and cannot use ball screws, the vast majority of CNC machine tools use semi-closed loop servo systems.
3. Classification by Process Purpose
According to different process purposes, CNC machine tools can be divided into metal cutting CNC machine tools, metal forming CNC machine tools, special processing CNC machine tools and other types of machine tools CNC.
(1) CNC machine tools for metal cutting CNC machine tools for metal cutting include CNC lathes, CNC drills, CNC milling machines, CNC grinding machines, CNC boring machines and machining centers.
Cutting machine tools were developed first, and today there are many types with significant functional differences. Machining centers can perform automatic tool changes.
All of these machine tools have a tool library that can accommodate 10 to 100 tools. Its feature is that multiple processes can be completed by fixing the part once.
To further improve production efficiency, some machining centers use double work tables, one for processing and the other for loading and unloading, and the work table can be switched automatically.
(2) CNC metal forming machine tools CNC metal forming machine tools include CNC bending machines, CNC combination punching machines and CNC rotary head presses. This type of machine tool started later but developed quickly.
(3) CNC special processing machine tools CNC special processing machine tools include wire cutting machine tools, CNC electrical discharge machines, flame cutting machines and CNC laser cutting machine tools, etc.
(4) Other types of CNC machine tools Other types of CNC machine tools include three-coordinate measuring CNC machine tools, etc.
4. Classification by CNC system function level
CNC machine tools can be classified into three grades: low, medium and high, according to the different technical parameters, functional indicators and function levels of the main components of the CNC system.
In China, they are also classified as complete CNC machine tools, popular CNC machine tools and economical CNC machine tools.
These classification methods have relative limits, and the division patterns differ in different periods, mainly in the following aspects.
(1) Control system CPU grade
Low-level CNC systems generally use 8-bit CPUs, while mid- and high-end CNC systems use 16-bit or 64-bit CPUs. Some CNC devices now use 64-bit CPUs.
(2) Resolution and feed rate
Resolution is the smallest unit of displacement that the displacement detection device can detect. The lower the resolution, the higher the detection accuracy. It depends on the type and manufacturing precision of the detection device.
Generally, a resolution of 10μm and a feed rate of 8~10m/min are considered low-quality CNC machine tools; a resolution of 1μm and a feed rate of 10~20m/min are considered mid-level CNC machine tools; and a resolution of 0.1μm and a feed rate of 15~20m/min are considered high-quality CNC machine tools.
Typically, the resolution must be an order of magnitude greater than the machining accuracy required by the machine tool.
(3) Servo system type
CNC machine tools with stepper motor or open-loop power systems are generally of low quality, while mid- and high-grade CNC machine tools use semi-closed or closed-loop DC or AC servo systems.
(4) Coordinate link axis number
The number of coordinate link axes of CNC machine tools is also a commonly used indicator to distinguish the level of machine tools.
According to the number of coordinate axes controlled at the same time, they can be divided into 2-axis linkage, 3-axis linkage, 2.5-axis linkage (at any time, only two axes can be linked among the three axes, and the other axis is point or line control), 4-axis linkage, 5-axis linkage, etc.
The number of coordinate axes for low-quality CNC machine tools generally does not exceed 2 axes, while medium and high-quality CNC machine tools have 3 to 5 coordinate axes.
(5) Communication function
Low-level CNC systems generally do not have communication capabilities, while mid-level CNC systems may have RS-232C or Direct Numerical Control (DNC) interfaces.
High-quality CNC systems may also have Manufacturing Automation Protocol (MAP) communication interfaces with networking capabilities.
(6) Display function
Low-quality CNC systems often only have simple digital tube displays or single-color CRT character displays.
Mid-level CNC systems have more complete CRT monitors, which not only display characters, but also have two-dimensional graphics, human-machine dialogue, status and self-diagnosis functions.
High-quality CNC systems can also have three-dimensional graphics display, graphic editing and other functions.
5. Classification by CNC device composition
CNC machine tools can be classified into two types: wired CNC systems and soft wire CNC systems, according to the composition of the CNC device used.
(1) Connected CNC system
Wired CNC systems use wired CNC devices. Input processing, interpolation calculation, and control functions are performed by dedicated fixed-combination logic circuits.
Different types of machine tools have different combination logic circuits. When changing or adding control and operation functions, it is necessary to change the hardware circuit of the CNC device.
Therefore, this system has little universality and flexibility, long manufacturing cycle and high cost. Before the early 1970s, most CNC machine tools belonged to this type.
(2) CNC system with soft wire
Soft wire CNC systems, also known as computer numerical control (CNC) systems, use soft wire CNC devices. The hardware circuit of this type of CNC device is composed of small or microcomputers and large-scale general or special integrated circuits.
Almost all the main functions of CNC machine tools are implemented by system software, so the system software for different types of CNC machine tools is different.
Changing or adding system functions does not require changing the hardware circuitry, only changing the system software.
Therefore, this system has greater flexibility. At the same time, because the hardware circuit is basically universal, it is conducive to mass production, improving quality and reliability, shortening manufacturing cycles, and reducing costs.
After the mid-1970s, with the development of microelectronic technology and the emergence of microcomputers, as well as the continuous improvement of integrated circuit integration, computer numerical control systems have been continuously developed and improved.
Currently, almost all CNC machine tools use soft-wire CNC systems.