Currently, machining can be categorized into two groups based on the production batch:
- Single piece, multiple varieties and small batch production.
- Small variety, large batch or mass production.
Between these two categories, the first represents around 70-80% of the total value of machining production and is the primary machining sector.
Why does the production efficiency of the same CNC machine tool vary greatly?
The answer lies in selecting an unsuitable accessory for the CNC machine tool, significantly reducing its production efficiency.
Today, we will provide a comprehensive overview of the reasonable selection and use of CNC accessories.
Basic principles for selecting equipment
The requirements for fixtures in CNC machining are twofold:
- Make sure that the coordinate direction of the fixture is fixed relative to the coordinate direction of the machine tool.
- Align the dimensional relationship between parts and the machine tool coordinate system.
Furthermore, the following four points must be considered:
- When the parts processing batch is not large, general fixtures such as combined or adjustable fixtures should be used as much as possible to reduce production setup time and save production costs.
- For batch production, special luminaires with simple structure should be considered.
- Loading and unloading parts must be fast, convenient and reliable to minimize machine tool downtime.
- The accessory must be designed so as not to interfere with the machining of parts and surfaces by the machine tool. All parts and components of the fixture must not affect the movement of the tool during machining, and the fixture must be open and its positioning and clamping mechanism elements do not cause collisions with the tool.
How to improve the use of CNC machine tools?
Technical analysis shows that the use of luminaires has a significant impact.
Statistics show that more than 50% of national companies choose unsuitable accessories for their CNC machine tools.
The cycle time for small batch production is made up of the “production time (preparation/waiting)” and the “part processing time”. Since the “part processing time” in small batch production is short, the duration of the “production (preparation/waiting) time” has a crucial impact on the overall processing cycle.
To improve production efficiency, it is necessary to find ways to reduce “production (preparation/waiting) time”. The following three types of CNC machine tools and accessories are recommended for priority use in small batch production:
①Combo device
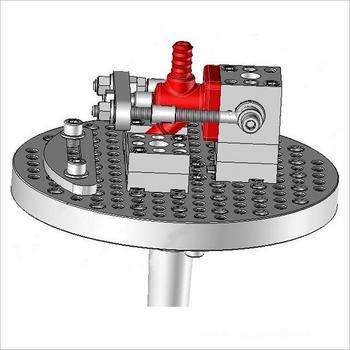
Modular fixtures, also known as “building block fixtures”, are composed of a series of standardized machine tool fixture elements with different functions and sizes.
Customers can quickly assemble various types of machine tool accessories as needed, similar to building blocks.
Because the modular fixture saves time in the design and manufacturing of special fixtures, it significantly reduces production setup time, thereby shortening the small batch production cycle and improving production efficiency.
Furthermore, the combined accessory also presents advantages such as high positioning accuracy, great fixing flexibility, recyclability, energy and material savings in manufacturing and low cost of use.
Therefore, for small batch processing, especially for complex product shapes, the use of combined accessories should be given priority.
② Precision combined flat pliers
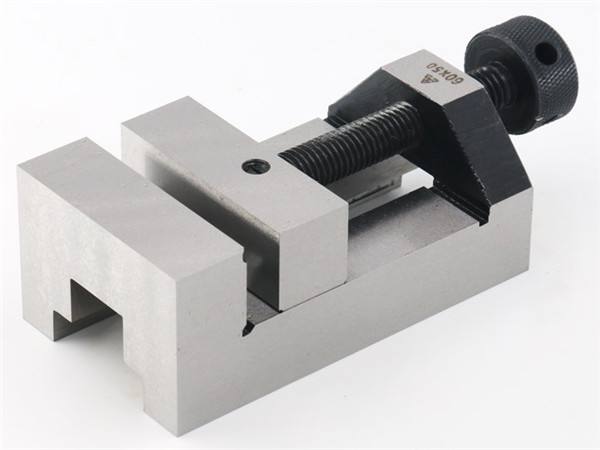
Precision combination pliers are a type of component within the combination accessory category.
Compared with other components in combination accessories, precision combination flat pliers are more versatile, standardized, easy to use and reliable in clamping.
As a result, they are widely used across the world.
Precision combination flat pliers offer quick installation and clamping, which reduces production setup time and improves efficiency in small batch production.
At present, the clamping range commonly used for precision combined flat pliers around the world is within 1000mm, and the clamping force is generally limited to 5000Kgf.
It is important to note that precision combination pliers are not the same as traditional machine vises.
Traditional vises have limited functions, low manufacturing precision, cannot be used in groups, and have a short service life, making them unsuitable for use on CNC machine tools and machining centers.
In contrast, precision combination pliers are a new type of pliers originating from developed industrial countries such as Europe and America, designed specifically for the needs of CNC machine tools and machining centers.
These products feature the benefits of great clamping flexibility, high positioning accuracy, fast clamping and group use capability, making them ideal for use on CNC machine tools and machining centers.
③ Electropermanent magnet fixture
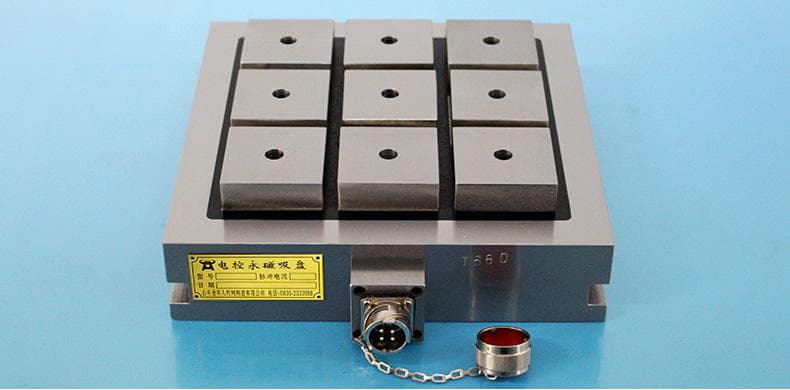
Permanent magnet electric tweezer is a new type of tweezer that uses neodymium, iron, boron and other advanced permanent magnet materials as a source of magnetic force and is designed based on modern magnetic circuit principles. In practice, the use of permanent magnet electric collets has been shown to significantly improve the overall efficiency of CNC machine tools and machining centers.
The process of attaching and releasing the permanent magnetic clamp only takes about 1 second, greatly reducing attachment time. Furthermore, the permanent magnet electric clamp does not have space-consuming positioning and clamping elements like traditional machine tool clamps, increasing the clamping range and allowing better utilization of the work table and processing stroke of the machine tool. CNC.
The suction force of the permanent magnet gripper is normally around 15 to 18 kgf/ cm2 , so it is important to ensure that the suction force is sufficient to withstand the cutting force. The adsorption area must not be less than 30 cm 2 which means that the clamping force must not be less than 450 kgf.
What are the types of machine tools and accessories?
Machine tool accessories can be broadly categorized into eight types:
1. Flat tweezers
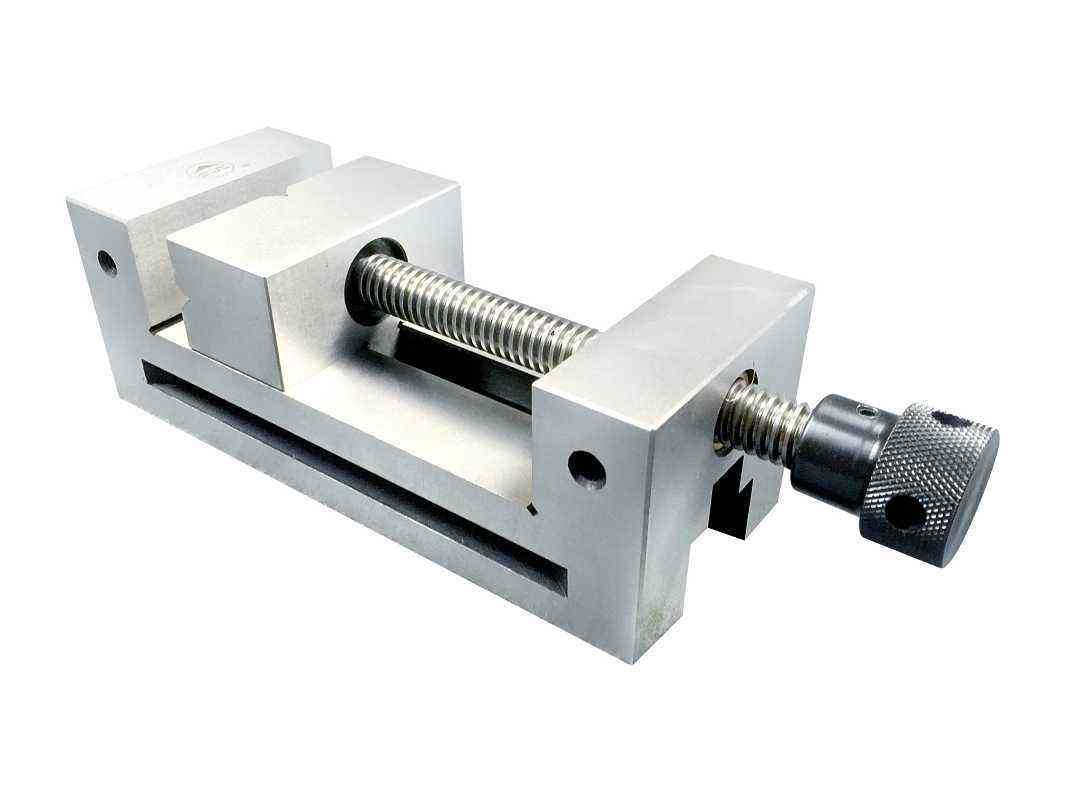
Flat clamps are highly versatile and cost-effective, making them ideal for clamping small-sized, square-shaped parts. The V-shaped groove or V-shaped block in the jaw also allows clamping of cylindrical surfaces.
Characteristics:
Flat clamps offer convenient clamping, fast and reliable operation and precise positioning, making them suitable for a variety of square parts, but are not ideal for clamping thin sheet metal parts. On CNC milling machines, flat collets are often clamped using mechanical screws, pneumatic or hydraulic clamping methods, as shown in the figure. Commonly used types include:
(a) Universal flat clamps fixed by screw;
(b) Flat clamps for hydraulic sinusoidal meter;
(c) Precision pneumatic flat grippers;
(d) Hydraulic precision flat grippers.
2. Pressure plate and screw

For larger or irregularly shaped workpieces that cannot be clamped with flat clamps or other clamps, press plates can be used for direct clamping, or workpieces can be clamped through process holes using screws.
(a) Universal flat clamps fixed by screw;
(b) Flat clamps for hydraulic sinusoidal meter;
(c) Precision pneumatic flat grippers;
(d) Hydraulic precision flat grippers.
C feature:
Clamping and alignment using press plates takes significant time, and the position and height of the press plate must be carefully considered in machining programming to avoid interference with the cutting tool.
The screw penetration method through process holes saves space and is easy to implement, but the position of the hole must be aligned with the position of the T-slot on the machine tool. Otherwise, fabricating a backing plate for screw penetration becomes a complicated task.
This method is most appropriate for specialized shaped parts, large parts, and workpieces that cannot be clamped with flat clamps.
3. Chuck
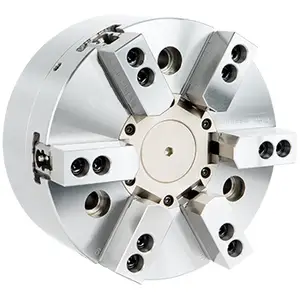
Chucks can be categorized into two-jaw chucks, three-jaw self-centering chucks, four-jaw chucks, and six-jaw chucks based on the number of jaws they have.
Three-jaw self-centering single-action chucks and four-jaw chucks are widely used in CNC milling machines and machining centers. The three-jaw self-centering chuck is highly sought after due to its automatic centering and convenient clamping ability. As a result, when processing small to medium-sized cylindrical parts on a CNC milling machine or machining center, the three-jaw single-action self-centering chuck is often employed for clamping purposes.
Chucks can be clamped using various methods, including mechanical, pneumatic, hydraulic screw and others.
The features of a chuck include convenient and reliable clamping, automatic centering and suitability for cylindrical parts.
4. 3R fastening system
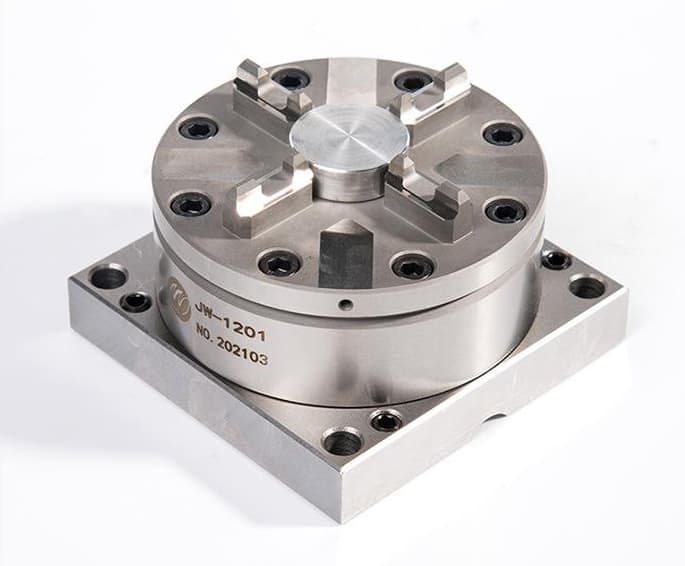
C feature:
Chuck clamping is convenient and reliable, with a high degree of repeatable positioning accuracy. It is particularly suitable for manufacturing matrix electrodes.
5. Magnetic chuck
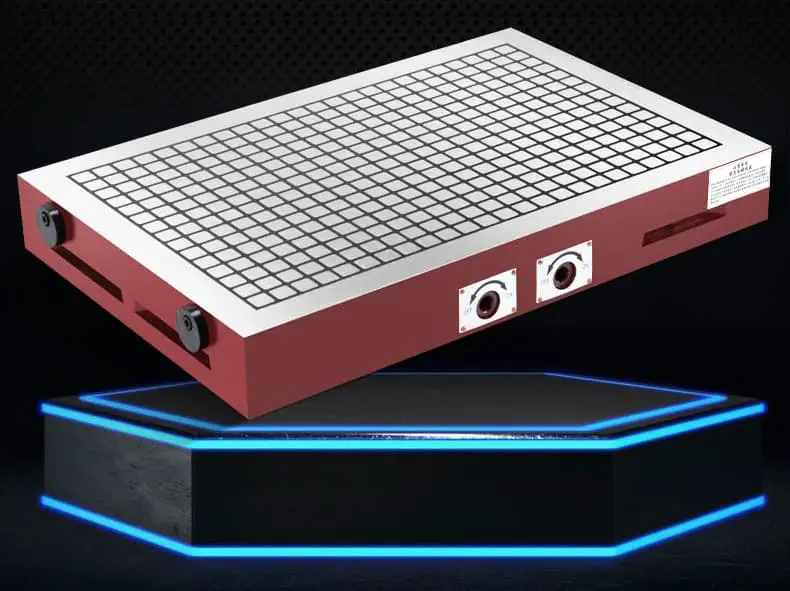
Features: easy and reliable fixing, wide range of applications, but parts must be made of magnetic absorbing materials.
6. Vacuum device
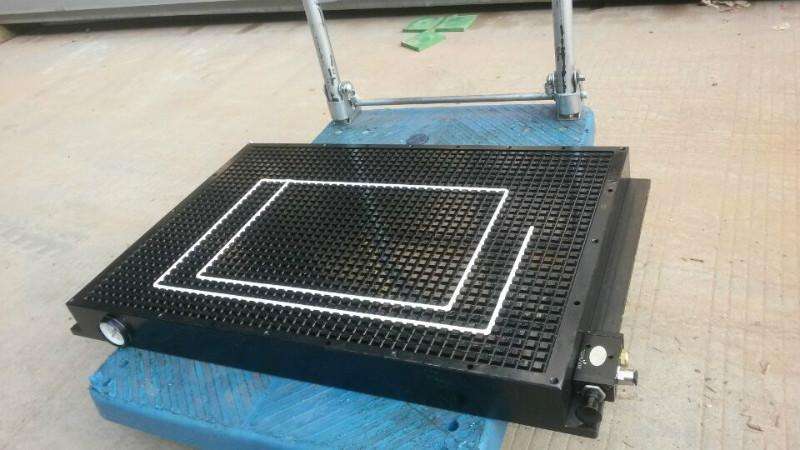
It is suitable for parts with a large positioning plane or large sealable area.
Some CNC milling machines, such as wall plate milling machines, are equipped with a general vacuum platform for easy installation of workpieces. For regular shaped parts such as rectangular, special rubber strips can be inserted directly into the sealing groove of the fixture. These rubber strips come in hollow or solid circular sections and must meet certain size requirements. Once the workpieces are placed on the surface, the vacuum pump can be activated to securely hold them in place.
However, for irregularly shaped parts, the use of rubber strips is not suitable. In this case, rubber putty, commonly known as putty, must be applied around the parts for sealing. This process is not only time-consuming and inefficient, but also tedious.
To overcome this challenge, a special transition vacuum platform can be used, which can be placed on top of the general vacuum platform.
7. Indexing head
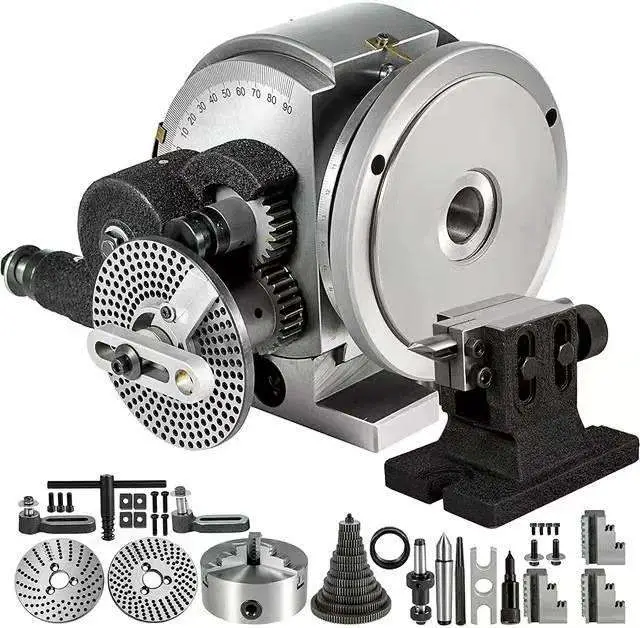
When processing mechanical parts such as splines, clutches, gears and others in a machining center, the dividing plate method is often used to divide each tooth groove equally and produce high-quality parts. This method ensures that each part is processed accurately and consistently.
8. Special game, combined game and group game
For small and medium batches of parts, combination fixtures can be used for clamping during processing in a machining center. However, when processing large quantities of workpieces, special or group fixtures are commonly used for clamping.
It is worth noting that the machining center is more suitable for processing single or small batches of parts, and therefore the use of special or group fixtures is less common on CNC machine tools.

Main components of a luminaire
Figure 10-8 illustrates an accessory used to pierce a glove. Despite the variety in their purposes, types and structures, machine tool accessories are composed of the following fundamental elements.
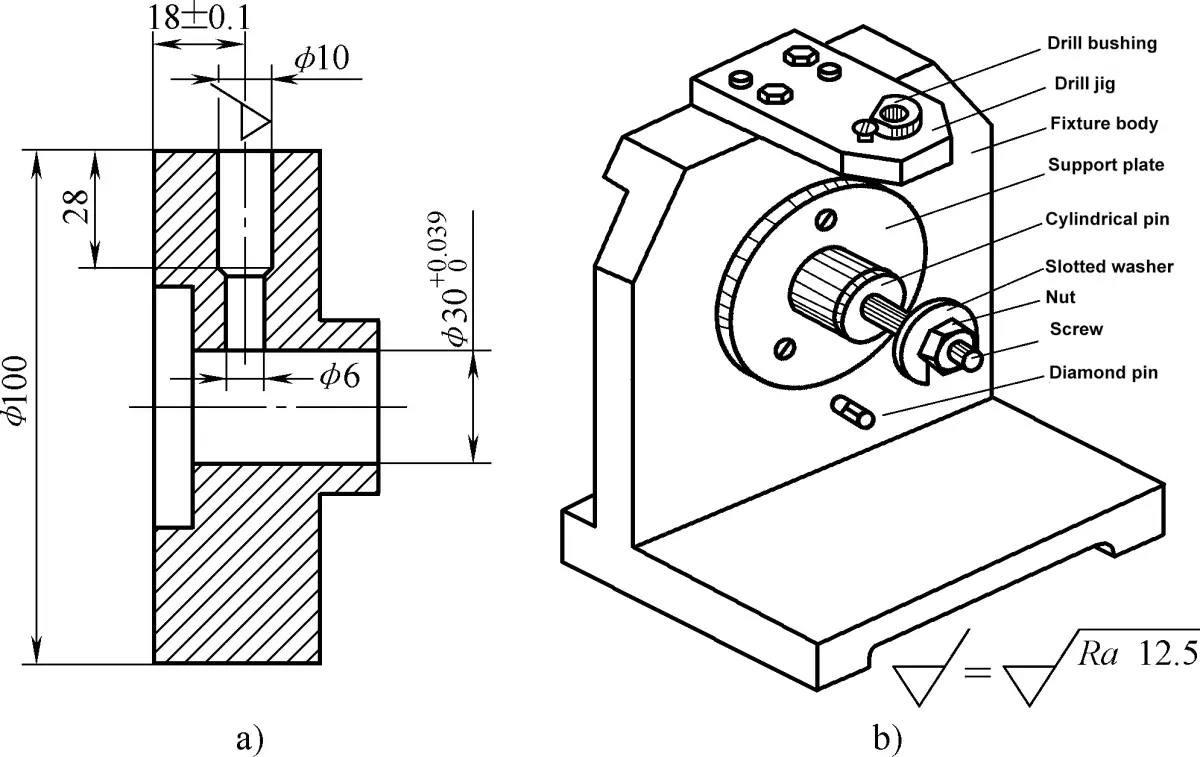
a) Diagram of the back cover part
b) Drilling jig for drilling holes
1) Finding Elements.
These are various components used to establish the correct position of the part within the fixture. When the workpiece is positioned on a plane, pins or support plates serve as locating elements (Figure 10-9).
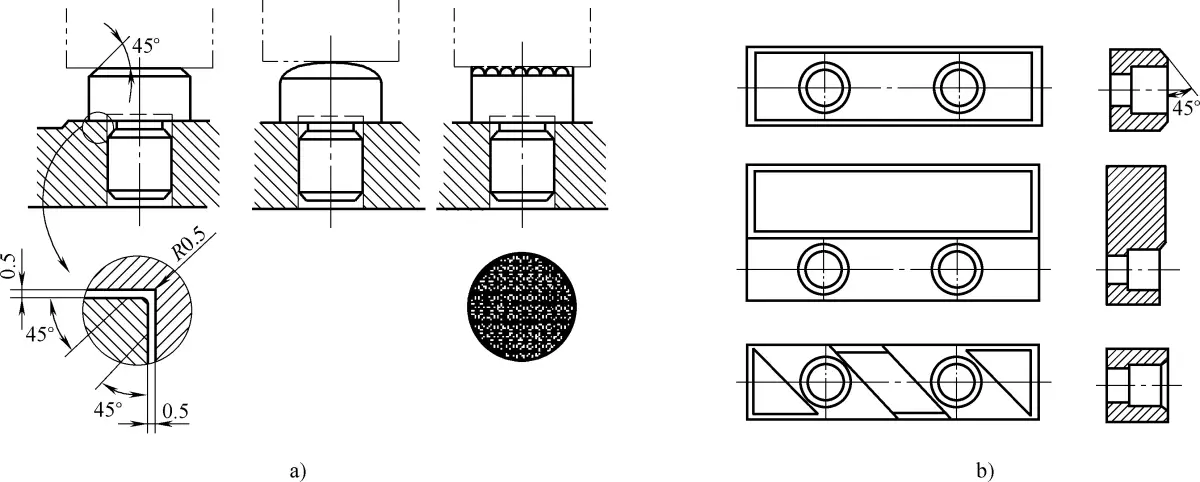
a) Support pin
b) Support plate
There are three forms of support pins: flat-headed ones for positioning machined surfaces, ball-headed ones for positioning rough rough surfaces, and threaded ones to increase friction, but they are not suitable for chip removal, mainly used for lateral positioning . When the workpiece is positioned by an outer cylindrical surface, V-blocks and locating sleeves serve as locating elements (Figure 10-10).
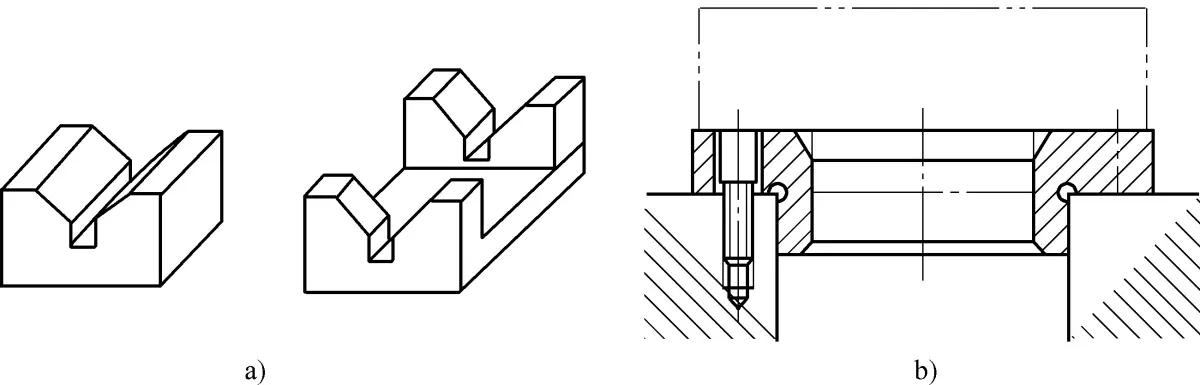
a) Block V
b) Location Sleeve
When the workpiece is positioned through a hole, the locating spindles and pins serve as locating elements (Figure 10-11). In Figure 10-8, the cylindrical pin, diamond pin and support plate in the fixture for drilling a 10 mm radial hole in the back cover are all locating elements, which ensure that the workpiece occupies the correct position in the fixture .
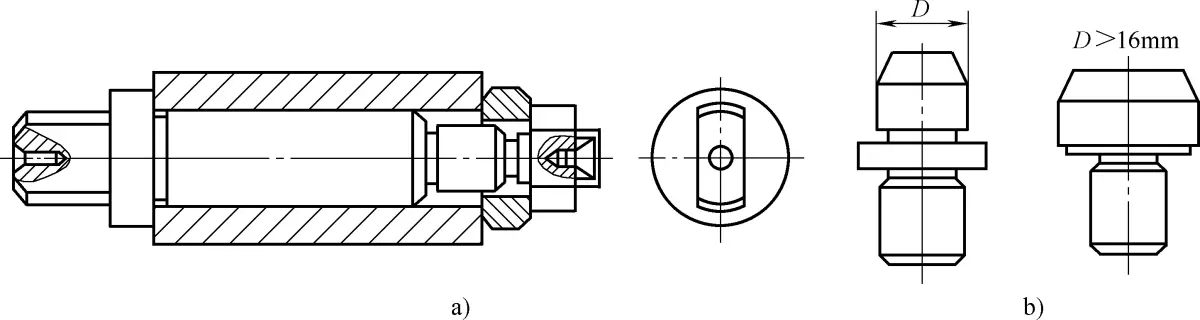
a) Location of the central pin
b) Location Pin
2) Fixing devices.
Clamping devices are used to maintain the correct position of the part in the fixture, ensuring that the position is not compromised when the part is subjected to external forces (such as cutting force, gravity, inertia) during the machining process. As shown in Figure 10-8, the open washer on the drill fixture is a fastener that, together with the screw and nut, forms the clamping device.
3) Tool configuration and guidance elements.
They are used to determine the correct position of the tool relative to the fixture and guide the tool during machining. Among them, tool adjusting elements are accessory parts that fix the tool, such as the tool adjusting block and feeler gauge on the milling machine accessory. Guide elements are accessory parts that secure and guide the tool. The drill bushing in the drill fixture shown in Figure 10-8 is a guide element.
4) Electrical device body.
This is the base of the machine tool fixture, used to connect various fixture elements or devices into a whole, and through which the fixture is installed on the machine tool. In Figure 10-8, the body of the drill fixture connects all the fixture elements into a whole.
5) Connecting elements.
These are components that determine the correct position of the accessory on the machine tool, such as positioning keys, pins and fixing screws.
6) Other Elements and Devices.
Depending on the workpiece requirements, indexing mechanisms, loading and unloading devices, workpiece ejection devices (or tool compensation devices) can sometimes be equipped on the fixture.
CNC machine tool clamping suitable for mass processing
The batch processing cycle is made up of three parts: processing waiting time, part processing time, and production setup time. Processing waiting time mainly includes part clamping time and tool changing.
In traditional manual machine tools, part clamping time can take 10 to 30% of the mass processing cycle. As a result, workpiece clamping has become a crucial factor in determining production efficiency and is therefore a key objective for improving machine tool clamping device performance.
To improve production efficiency during mass processing, special fixtures designed for quick positioning and fast clamping (and loosening) should be used. The following three types of machine tool accessories are recommended:
① Hydraulic/pneumatic clamp
The hydraulic/pneumatic gripper is a specialized gripper that uses oil pressure or air pressure as a power source. This type of clamping uses hydraulic or pneumatic elements to achieve precise positioning, support and pressure on the workpiece.
One of the advantages of the hydraulic/pneumatic attachment is its ability to quickly and accurately determine the position of the workpiece, machine tool and tool in relation to each other.

The use of a hydraulic/pneumatic accessory guarantees precise positioning of the part, providing high machining precision. Furthermore, the quick positioning and clamping process significantly reduces the time required to clamp and release the workpiece.
These attachments also have the advantage of a compact design, multi-station clamping capability, high-speed heavy cutting, and automatic control. These attributes make hydraulic/pneumatic accessories particularly suitable for use on CNC machine tools, machining centers and flexible production lines, especially for mass processing.
② Electropermanent magnet fixture
The permanent magnet electrical fixture offers multiple benefits, including fast clamping, ease of multi-station clamping, ability to perform multi-faceted processing with one fixture, stable and reliable clamping, energy efficiency and environmental friendliness, and automatic control.
Compared with traditional machine tool fixtures, permanent magnet electric fixture significantly reduces clamping time, reduces the number of clamping operations, and increases clamping efficiency.
These advantages make the permanent magnet electrical fixture suitable for both small and large batch production, making it a versatile option for diverse manufacturing needs.
③ Smooth fixing base
The smooth fixing base is not commonly used in China, but is widely used in industrialized countries such as Europe and America. This type of accessory is made from a thin blank of the base of the accessory that has undergone finishing processing.
The positioning connection part between the components, the machine tool and the parts positioning surface on the fixture have been completed and finalized. This results in a smooth, polished baseplate that is ready for use.
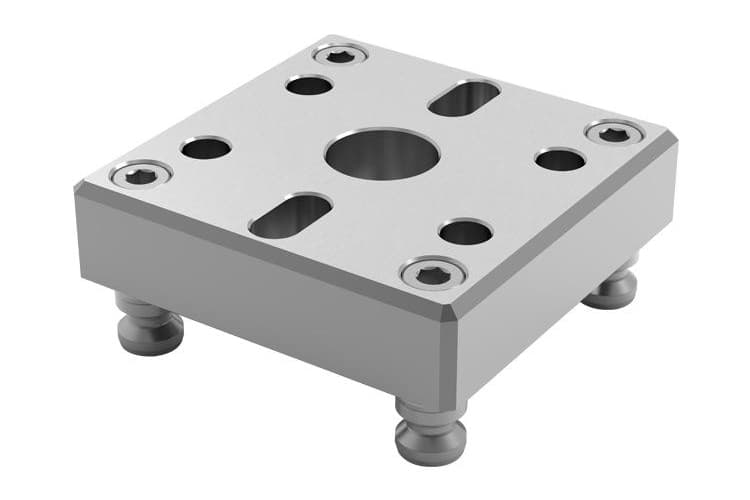
Users have the ability to custom manufacture accessories to meet their specific needs. The smooth surface of the fixture base allows for a shorter manufacturing cycle for these special fixtures and reduces production setup time. This, in turn, shortens the overall mass production cycle and increases production efficiency.
Furthermore, the production cost of a professional accessory can be reduced by using a smooth accessory base.
Therefore, this type of fixing base is particularly suitable for large-scale production with tight schedules and deadlines.
Reasonable use of accessories to take advantage of the equipment’s potential
Experience has shown that to improve the efficiency of CNC machine tools, it is not enough to simply choose the correct CNC machine tools and accessories, but it is also important to use them effectively. Here are three common methods to achieve this:
① Multi-station method
The multi-station method is based on the idea of reducing unit clamping time and increasing the tool's effective cutting time by clamping multiple parts at once.
A multi-station accessory is an accessory with multiple positioning and attachment positions. With the advancement of CNC machine tools and the demand for greater production efficiency, the use of multistation attachments has become more widespread.
In the design of hydraulic/pneumatic grippers, combination grippers, electro-permanent magnetic grippers, and precision flat combination grippers, the inclusion of a multi-station design is becoming more common. This design allows for greater efficiency and productivity in mass production processes.
② Group usage method
One method for achieving multi-station clamping is to place multiple clamps on a single workbench. Fixtures used in this approach must be designed with standardization and precision in mind to ensure they meet processing requirements on a CNC machine.
This group clamping method maximizes the travel range of the CNC machine tool, resulting in balanced wear of its transmission components. Additionally, the fixtures can be used separately to clamp multiple parts or together to clamp larger parts, providing versatility and increasing production efficiency to meet the diverse needs of various production processes.
③ Local quick change method
The local quick change method involves quickly changing the fixture function or mode by quickly replacing fixture parts, such as positioning element, clamping element, tool adjusting element and guide element, on the CNC machine tool .
For example, quick-change combined flat-jaw pliers can quickly change their clamping function by replacing the jaws, for example, from square materials to clamping bar materials. Likewise, the clamping mode can be changed quickly by changing the clamping element, for example from manual to hydraulic clamping.
The local quick change method significantly reduces the time required for replacing and adjusting accessories and is especially beneficial for small batch production.
Requirements for CNC machining center clamping
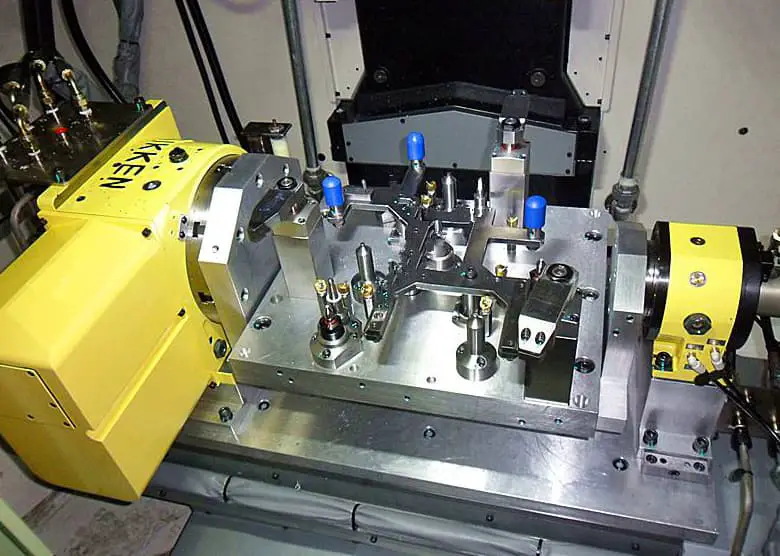
Fixtures are an essential component of a CNC machining center. Every CNC machining center requires the use of accessories, which vary depending on the product to be processed. However, despite differences in the fixtures used, the requirements for fixtures on CNC machining centers are similar, with some variations for fixtures used for special parts.
What are the requirements of a CNC machining center for accessories?
High Precision Fixture
It is widely known that CNC machining centers have exceptional precision and are commonly used to process parts or molds that require high precision.
As a result, CNC machining centers have strict requirements on the accuracy of fixture positioning devices and the accuracy of indexing and positioning.
The fixture must be convenient and quick when clamping the workpiece.
To meet the needs of high-speed machining devices in CNC machining centers, hydraulic and pneumatic fast clamping forces are often selected, especially for locking parts during long processing times.
Typically, the hydraulic clamping system is equipped with a reservoir, which compensates for internal leaks and prevents parts from loosening in the device.
The clamp must have excellent opening
The CNC machining center processes the workpiece through tool-workpiece contact, and the workpiece must be securely clamped by the fixture to provide ample operating space for the fast-moving tool and quick tool changes.
For parts with complex machining and multiple tool changes, the fixture structure should be simple, easy to use and open to facilitate tool entry and exit and avoid collisions between the tool and the part during machining movements.
The accessory must have high adaptability
It is known that the CNC machining center exhibits mobility and multi-deformation during machining, therefore it is essential that the device is highly adaptable to different workpieces and fixture requirements.