Why does the same machine tool have significant differences in production efficiency?
The reason is that the clamps used in CNC machine tools are often not suitable, leading to a significant reduction in the production efficiency of these tools.
In this article, we will discuss the proper selection and use of CNC machine tool clamps.
How can we improve the efficiency of CNC machine tools?
Technical analysis revealed that the choice of clamps plays a crucial role in this aspect.
Statistics indicate that a large proportion of clamps used on home CNC machine tools are inappropriately selected, with an estimated 50% of cases. At the end of 2018, there were nearly one million CNC machine tools in China, meaning that more than 500,000 of these tools suffered “downtime” as a result of poor clamp selection or use.
From an economic perspective, there is a significant opportunity to improve the selection and use of fasteners for CNC machine tools, which could lead to substantial benefits.
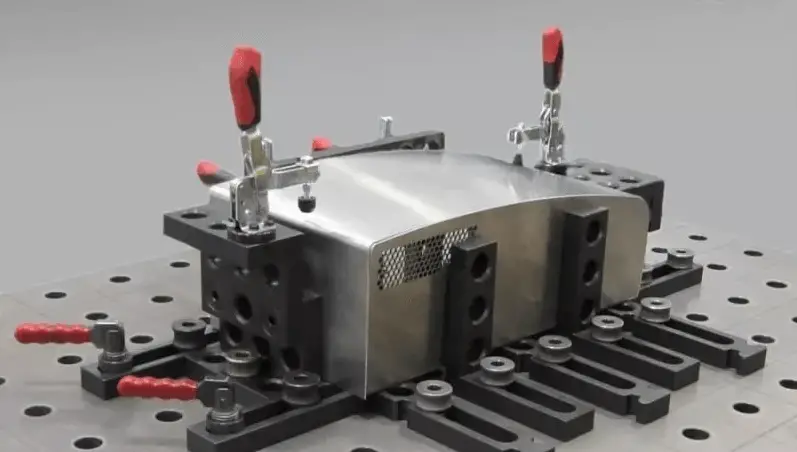
Small batch production cycle = production time (preparation/waiting) + part processing time.
In small batch production, the “part processing time” is relatively short, making the duration of the “production prep/waiting time” a critical factor in determining the overall processing cycle.
To increase production efficiency, it is essential to find ways to reduce the duration of production preparation/waiting time.
Three types of clamps in small-scale production of CNC machine tools can take priority
Clamp combination
The combination clamp, also known as a “building block clamp”, is composed of a series of standardized components with varying functions, specifications and sizes. Customers can easily assemble different types of machine tool clamps as needed, like building blocks.
The use of a combined clamp can save time in design and manufacturing, significantly reduce production setup time, and therefore effectively shorten the processing cycle in small batch production, leading to greater efficiency.
Furthermore, combination clamps offer several advantages, including high positioning accuracy, great clamping versatility, repeatable use capability, energy and material savings, and low usage cost.
Therefore, when processing small batches, especially when the product shape is complex, the use of combination grippers is highly recommended.
Combined precision flat pliers
The combination precision flat pliers is a component of the combination clamp.
Compared to other combination clamp components, they have more versatility, higher levels of standardization, easier use and more reliable fixation, making them widely used around the world.
The combined precision flat pliers have the advantages of quick installation and removal as well as quick clamping, which helps to reduce production setup time and improve the efficiency of small batch production.
At present, the commonly used combination precision flat pliers have a clamping range generally within 1000mm, with a clamping force of up to 5000Kgf.
Smooth base clamp
Smooth fixing bases are not widely used in China, but are commonly used in industrialized countries such as Europe and the United States.
These clamp bases are made from finely finished machining and have a finished positioning connection piece for components as well as a finished positioning surface on the clamp. This allows for the creation of custom clamps based on specific needs.
It is important to note that the combination precision pliers mentioned are not traditional machine vises. Traditional machine lathes have limited functions, low manufacturing precision, short service life, and cannot be used in conjunction with other lathes.
They are not suitable for use on CNC machine tools or machining centers.
The aforementioned combination precision flat pliers are a new type of pliers originating from industrialized countries such as Europe and the United States, specifically designed for use in CNC machine tools and machining centers.
These pliers offer great clamping versatility, high positioning accuracy and fast clamping, and can be used in groups, making them ideal for use on CNC machine tools and machining centers.
Electric permanent magnet – containment clamp
Electromagnetic permanent magnet clamp clamp is a new type of clamp designed using advanced permanent magnet materials such as neodymium, iron, boron and modern magnetic circuit principles.
Numerous machining practices have shown that this type of clamp can greatly improve the overall machining efficiency of CNC machine tools and machining centers.
Its clamping and releasing process only takes about 1 second, significantly reducing clamping time.
Traditional machine tool collets have positioning and clamping components that take up a lot of space, while electromagnetic permanent magnetic clamping collets do not have these space-consuming components. This allows for a greater clamping range compared to traditional clamps, taking full advantage of the CNC machine tool's machining table and travel and improving its overall machining efficiency.
The suction force of permanent magnetic clamping electromagnetic clamps is normally between 15 to 18Kgf/cm 2 so it is crucial to ensure that the suction force (clamping force) is strong enough to resist the cutting force.
In general, the adsorption area should not be less than 30cm 2 which means that the clamping force should not be less than 450Kgf.
CNC machine tool clamps suitable for mass processing
The processing cycle for large batch production is composed of processing waiting time, part processing time and production preparation time.
“Processing waiting time” mainly includes the time of workpiece clamping and tool changing.
The “part clamping time” for traditional manual machine tool clamps can reach 10-30% of the total processing cycle in large batch production.
As a result, part clamping has become a crucial factor affecting production efficiency and is a key area for improvement in machine tool clamping.
For large-scale processing, it is recommended to use clamps with quick positioning and clamping/releasing capabilities. The following three types of machine tool clamps are highly recommended:
Hydraulic/pneumatic clamp
Hydraulic/pneumatic clamps are special clamps that use hydraulic or pneumatic components as a source of energy to position, support and compress the workpiece.
These clamps accurately and quickly determine the position between the workpiece, machine tools and cutting tools. The clamp guarantees accurate positioning of the part and, with its high machining precision and fast positioning and clamping process, it greatly reduces the time spent clamping and releasing the part.
Hydraulic/pneumatic grippers also offer several advantages, including a compact structure, multi-station clamping, high-speed heavy cutting and automatic control.
These benefits make hydraulic/pneumatic clamps suitable for use on CNC machine tools, machining centers and flexible production lines, and are particularly suitable for large-scale processing.
Electric Permanent Magnetic Fixing Clamp
Permanent magnetic clamping electric clamp has several advantages, including fast clamping, easy multi-station clamping, multi-face processing in one clamping, reliable and stable clamping, energy efficiency and environmental protection, as well as automatic control.
Compared with traditional machine tool clamps, permanent magnetic clamping electric clamps can significantly reduce clamping time and increase clamping efficiency by reducing the number of clamping cycles.
Therefore, these clamps are not only suitable for small batch production, but also for large batch production.
Smooth base clamp
The smooth clamp base can effectively shorten the manufacturing cycle of special clamps and reduce production setup time, resulting in a shorter overall mass production cycle and higher production efficiency.
Furthermore, it can reduce the manufacturing cost of special clamps.
Therefore, the smooth clamping base is particularly suitable for mass production under tight deadlines.
Use clamps correctly and take advantage of the equipment's potential.
Experience has shown that to improve the machining efficiency of CNC machine tools, it is not enough to simply “select” the correct clamps. We must also make an effort to “use” tweezers effectively.
How to Use Clamps for CNC Machine Tools
Here are three common methods that will teach you how to use machine tool clamps:
Multistation method
Basic principle:
One way to reduce unit clamping time and extend the effective cutting time of tools is to clamp multiple workpieces at once.
Multi-station clamps are clamps with multiple positioning and fixing positions. With the advancement of CNC machine tools and the need to improve production efficiency, multi-station clamps are becoming more widely used. The multi-station design is becoming increasingly prevalent in the design of hydraulic/pneumatic tongs, combination tongs, permanent magnetic clamping electric tongs, and combination precision flat pliers.
Group usage
Placing the same clamps on the same bench can also achieve multi-station fastening.
For this method to be effective, clamps generally must have standardized design and high-precision manufacturing, otherwise they may not meet the process requirements of the CNC machine tool.
Using clamps in a group can make full use of the stroke of the CNC machine tool, which promotes balanced wear of the machine tool's transmission parts.
Additionally, the clamps can be used independently for fastening multiple parts or combined for fastening large-scale parts.
Local quick change method
The local quick change method involves quickly changing parts of a CNC machine tool clamp, such as positioning elements, clamping elements, tool setting elements and guide elements, to achieve the purpose of quickly changing functions or use the clamp.
For example, quick-change combined flat jaw collets can change their clamping function by quickly changing jaws, such as from clamping square materials to clamping bar materials.
It is also possible to change the clamping mode by quickly replacing the clamping elements, such as from manual clamping to hydraulic clamping. The local quick change method significantly reduces clamp replacement and adjustment time, making it an obvious advantage in small batch production.