I . Features/Applications of Mold Mills
In modern mold manufacturing, as the aesthetic and functional requirements of new products in industries such as mechanical electronics, automobiles and household appliances increase, increasingly complex components make the mold surface more complex.
The proportion of free-form surfaces increases continuously, which places greater demands on mold processing technology. Due to the complex structure of the mold and high precision requirements, the surface characteristics and materials of different parts vary significantly, necessitating the use of different types of mold cutters.
II. Selection of Machining Methods
1. The choice of tools for CNC milling in mold making largely depends on the task at hand.
For milling the inner and outer contours of parts and milling flats, flat-bottom end mills are often used. For some three-dimensional surfaces and contours with variable angles, ball mills, annular mills, drum mills, conical mills and disc mills are commonly employed.
Mold cutters are used to machine mold cavity surfaces. Cavity section machining mainly depends on various types of end mills. Mold cutters evolved from end mills and can be categorized by the shape of their workpiece into flat-point conical, ball-end cylindrical, and ball-end conical types.
They can also be classified by material into carbide mold cutters, high speed steel mold cutters, etc. Carbide mold cutters have extremely wide applications. In addition to milling various mold cavities, they can replace hand files and grinding heads for deburring cast, forged and welded parts, and for fine finishing of certain molded surfaces.
2. Mold milling cutter selection .
Rational tool life generally falls into two categories: tool life at maximum production rate and tool life at minimum cost. The first is determined based on the objective of lowest time per piece, while the second is determined based on the objective of lowest operating cost.
Compared with traditional machining methods, CNC machining places higher demands on tools. They not only need to be rigid and precise, but also have stable dimensions, high tool life and easy installation and adjustment to meet the high efficiency requirements of CNC machine tools. Tools used in CNC machines generally adopt materials suitable for high-speed cutting and employ indexable inserts.
For multi-tool machine tools and combination machine tools where tool assembly, changing and adjustment are complex, tool life standards must be higher while ensuring tool reliability.
When the production rate of a given operation within a shop limits the increase in the production rate of the entire shop, or when a given operation supports a large portion of the factory's total expenses within a unit of time, a useful life of the lowest tool should be chosen.
Repositionable oval ball end mill
- Rod diameter/mm: φ20-φ50
- Maximum setback/mm: Up to full blade length
- Programming difficulty:
- Number of blades: 2
- Scope of use: A versatile mold processing tool, conveniently applicable, more suitable for stamping mold machining.
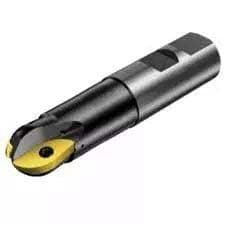
Indexable disc cutter
- Cutter shank diameter/mm: φ10-φ160
- Maximum Setback/mm: Tool Radius
- Programming difficulty:
- Number of blades: disc cutter
- Applicable range: Most suitable for contouring, cavity milling and equal height line processing. It is excellent in plastic molds, die casting, forging and stamping molds.
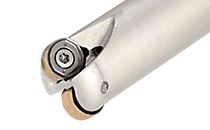
High Speed Milling Cutter Specifications
- Cutter shank diameter (mm): φ20 – φ100
- Maximum amount of recoil (mm): 1.2 – 2
- Programming difficulty:
- Number of cutting blades: 3
- Application range: Suitable for milling deep and long cavities.
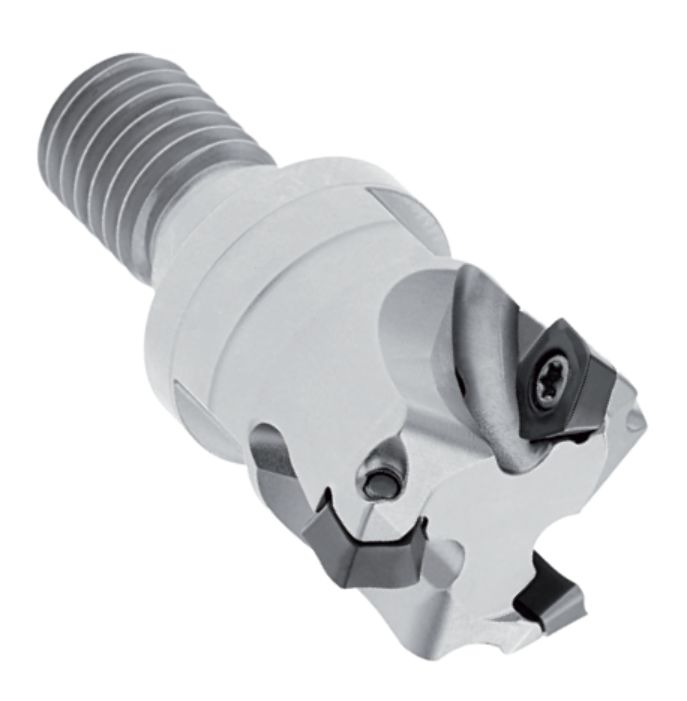
Integral brazed milling cutter
- Shaft diameter/mm: φ1-φ40
- Maximum rear feed/mm: 5
- Programming difficulty:
- Number of blades: 2/4
- Applicability: Wide range. It can be ground for use by adopting various tool materials and structural characteristics.
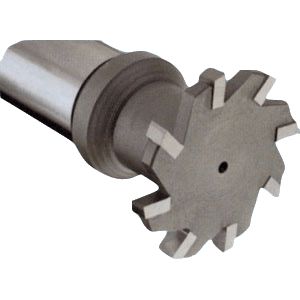
When determining tool life, consider factors such as tool manufacturing, sharpening costs, and complexity. For tools with short replacement times, such as rotating machine clamping tools, choose a shorter tool life to increase productivity and take full advantage of cutting performance. Tools with high complexity and precision should have a longer service life than single-blade tools.
During precision machining of large parts, to ensure at least one complete tool pass and avoid tool changes mid-cut, tool life should be determined based on part precision and surface roughness.
III. Structure Selection
In mold processing, the structure of the selected tool varies according to different processing stages. The rough and precision machining stages have specific tool structures for you to choose from.
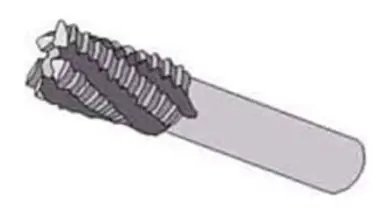
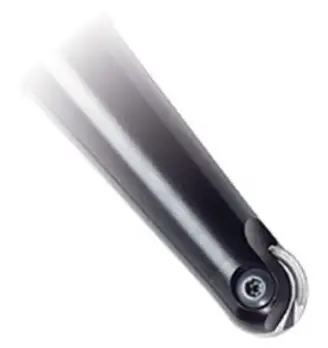
Advanced tools can be used to process small and medium-sized raw parts, thus increasing the quality and productivity of the operation. Large mold dimensions vary and requirements for rough and precision machining are different based on the part being processed. Appropriate vertical cutters are selected for use.
Full vertical cutters are predominantly used in machining. For large mold processes such as bumper injection cavities, the use of machine clamping cutters with indexable inserts is favored due to their cost-effectiveness and efficiency improvements. Precision machining, on the other hand, generally employs full vertical milling cutters.
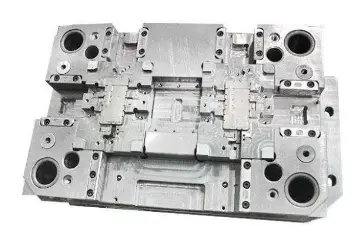
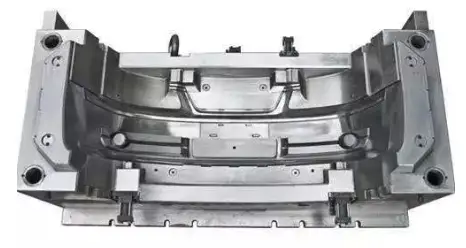
4. Features of roughing/semi-finishing/finishing machining
The main objective of rough machining in die manufacturing is to maximize the metal removal rate per unit time while preparing geometric contours for semi-finishing. The main objective of semi-finishing is to obtain a smooth surface profile on the part, ensuring a uniform margin for subsequent finishing machining.
In both rough and semi-finish machining, higher feeds are used for efficient and economical processing, employing indexable insert cutters and high feed, high speed cutters. The latter can operate under very high cutting parameters.
Although the worktable feed is extremely high, the cutting thickness is minimal, resulting in a large feed but a small amount of back cutting. Most cutting forces are generated axially, which can reduce vibration tendencies and achieve a high metal removal rate.
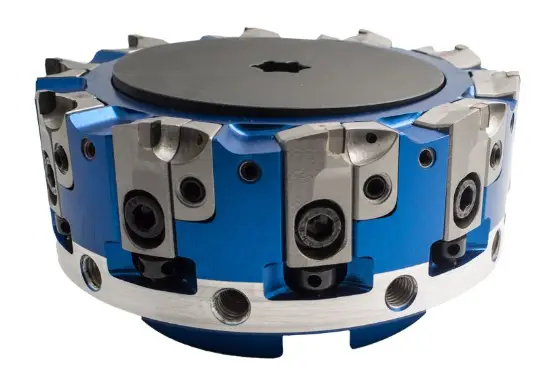
Key Points for Selection of Milling Cutters for Roughing and Semi-Finishing of Different Surfaces
1. For rough machining of larger surfaces (flat or inclined), select indexable insert end mills, face mills, or high-speed feed mills.
2. For smaller rough and semi-finished surfaces, opt for end mills with round inserts. The larger radius of round inserts provides greater insert strength.
3. For roughing and semi-finishing of smaller surfaces, use spherical end mills with indexable inserts. Willow leaf shaped inserts can be chosen for their low cutting force and high machining efficiency.
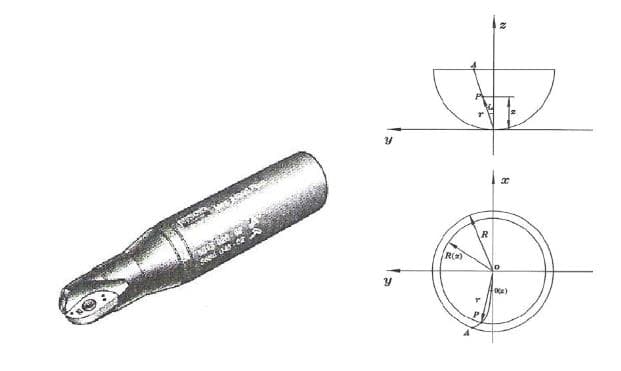
During precision machining of curved surfaces, ball-end milling cutters are used. The cutter radius should be as large as possible to increase tool rigidity, improve heat dissipation and reduce surface roughness values.
Generally, the radius of curvature of a finely machined surface should be greater than 1.5 times the tool radius to avoid abrupt changes in feed direction.
However, when machining concave arcs, the radius of the spherical end of the cutter must be smaller than the minimum radius of curvature of the machined surface. Ball end mills are used for semi-fine and fine milling of surfaces; Small diameter ball end mills can perform fine milling on steep faces and small straight wall chamfers.
However, when using a ball end mill to improve machining efficiency by increasing kickback, noticeable cutting residue will remain on the machined part after processing, increasing the workload for subsequent precision machining tools. Although the efficiency of rough machining is high, it reduces the efficiency of subsequent processes.
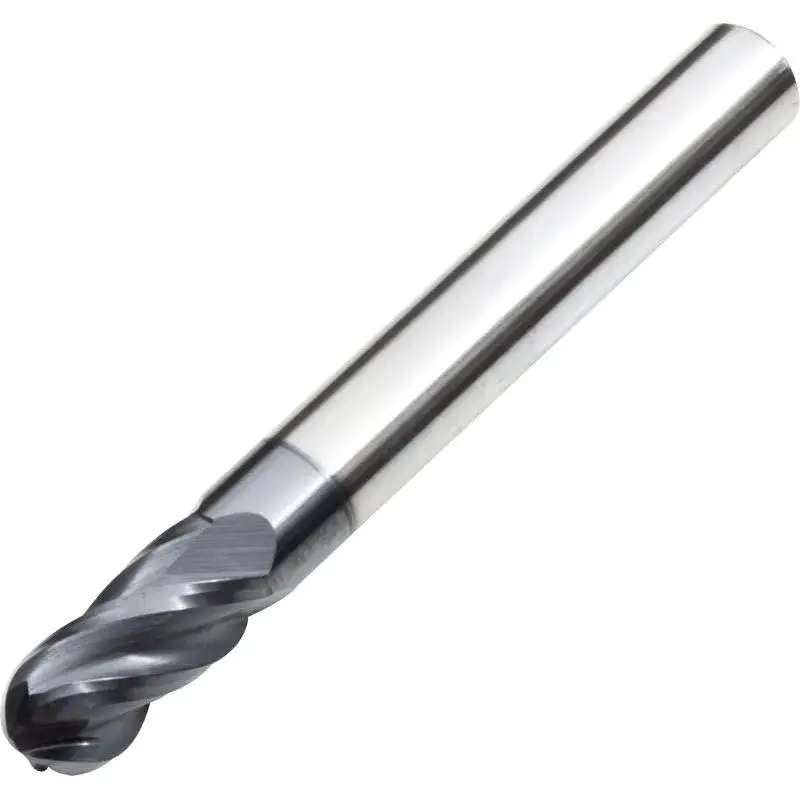
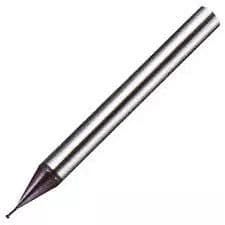
Key points when selecting cutters for precision machining of different surfaces
1. For precision machining of larger surfaces, ball end mills with indexable insert can be used to achieve high precision machining. For smaller surfaces, solid spherical end mills can be selected for high precision machining.
2. High precision machining of arc minute R parts.
3. For deep channels and tiny width corners, small diameter carbide tools can be used in root and corner cleaning operations for each workpiece.