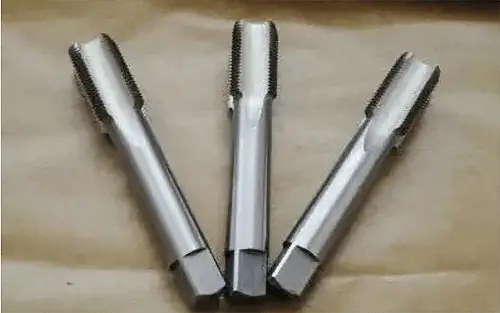
Extrusion Tap (NRT)
The difference between an extrusion tap and a cutting tap is that during threading with an extrusion tap, there is no cutting discharge. The internal thread is created by pressing, resulting in a smooth and aesthetically pleasing surface.
Using an extrusion tap, the material (such as iron wire) is not continuously cut, leading to a 30% increase in thread strength and stable accuracy.
Due to its large core diameter, the extrusion core has high strength and torque resistance, a long service life and is less likely to break. This type of faucet is suitable for materials with high ductility, such as iron sheet, copper sheet, aluminum sheet, stainless steel sheet and pipes.
However, the requirements for the bottom hole of the extrusion core are high. If the hole is too large, the amount of base metal will be small, resulting in a large internal diameter of the thread and insufficient strength. On the other hand, if the hole is too small, the closed extruded metal will have nowhere to go, causing the faucet to break.
The formula for determining the bottom hole diameter is: bottom hole diameter = nominal internal thread diameter – pitch 0.5.
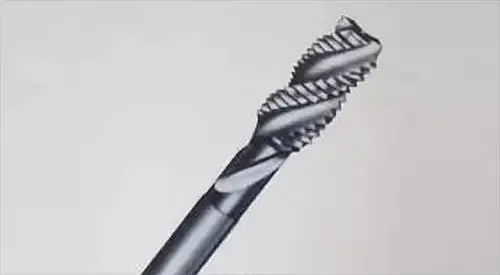
Spiral groove tap (SFT)
Spiral flute tap has advantages when tapping into a blind hole and cutting unloaded steel material continuously. This is because the straight spiral flute, with a cutting angle of approximately 35 degrees, allows for efficient hole discharge, leading to a tapping speed that can be 30% to 50% faster than a straight flute tap. Smooth cutting also results in good high-speed tapping performance in blind holes.
However, the spiral flute tap is not as effective when working with materials such as cast iron, which are easily broken into small pieces.

Straight tap
The straight channel faucet has the strongest versatility of all faucets. It can be used for through or through holes, regardless of whether the material is non-ferrous or ferrous metal, and is the most affordable option.
Related Reading: Ferrous vs Non-Ferrous Metals
However, this versatility also leads to a lack of specificity. The straight flute male is capable of performing a wide range of tasks, but is not the best at any of them.
The tap's cutting cone can have 2, 4 or 6 teeth. The short taper is used for through holes, while the long taper is used for blind holes.
It is recommended to choose the longest cutting cone whenever possible, provided the bottom hole is deep enough, as this will allow more teeth to share the cutting load, resulting in longer service life.
Touch the tip ( POT )
The tip tap has a special design on the front edge groove, known as barrel rim groove, which facilitates starting and cutting, with low torque and stable precision, thus improving its durability to a higher level.
During thread machining, chips are expelled in the forward direction. Its large core size provides good strength and can withstand substantial cutting forces.
The tip tap performs exceptionally well when working with non-ferrous metals, stainless steel and ferrous metals.
For through threads, the point tap is the preferred choice.
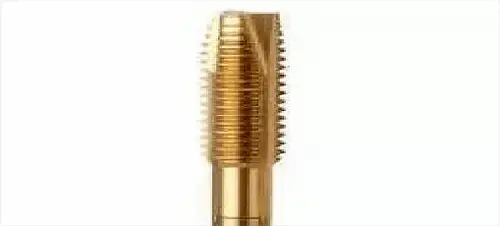
Pipe Tap (SPT)
There are two types of pipe taps: PF (G) threaded tap, which is based on mechanical combination (JISB4445), and tapered thread tap, which is based on tightness (JISB4446).
For pipes, there are taps with conical thread PT (RC) and taps with straight thread PS (RP), as well as taps with American threads such as NPT, NPS, NPTF, etc.
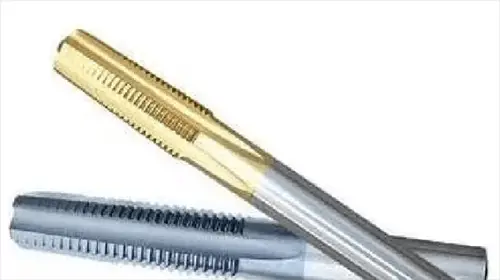
Nut tap (SNT)
Nut taps are specified by JIS and are mainly used for threading nuts.
Taking into account the processing characteristics of nuts, the tooth and shank of nut taps are relatively long (JJS4433).
JIS specifications include long-shank taps and short-shank taps, but tooth length is consistent across both types.
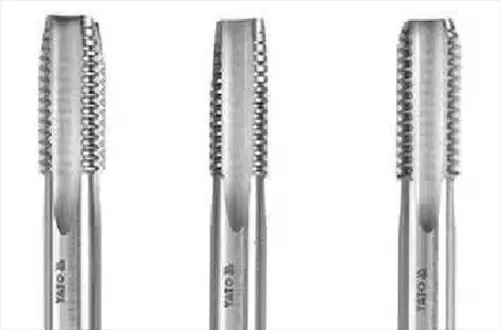
Manual touch ( HT )
The straight channel design of the hand faucet is the most commonly used and widely used.
JIS specifies that manual taps are divided into three classes based on flute length: 1# (9 flutes), 2# (5 flutes), and 3# (1.5 flutes).
When three classes are combined, work efficiency can be increased. Hand taps can also be used as single cutting teeth.