The colors of the drills indicate the type of coating that directly impacts their performance and durability. Black oxide (black) bits are heat resistant, good for soft metals. Titanium (gold) drill bits resist wear and tear and are suitable for various materials, while cobalt (bronze) drill bits are ideal for drilling hard and abrasive materials due to high heat resistance.
In mechanical processing, hole processing accounts for about one-fifth of its total processing, of which drilling accounts for about 30% of all hole processing. Those of you who work on the front lines of drilling are probably familiar with drill bits. When purchasing a drill, you can find drills of different colors and materials.
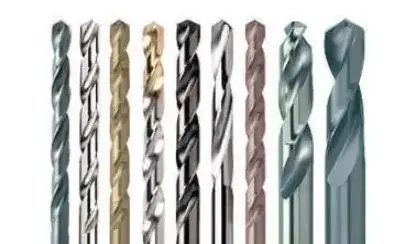
So what is the difference between drills of different colors? Does the color have anything to do with the quality of the drill and which is the best?
Does drill color have anything to do with quality?
Firstly, it is not possible to determine the quality of a drill simply by its color; color is not directly related to quality. Bits of different colors are mainly the result of different processing methods.
Of course, you can make a general judgment based on color, but even low-quality drill bits can have their own color treatment to achieve the look of a quality drill bit.
What is the difference between bits of different colors?
High-quality, fully grounded HSS bits usually appear white. Rolled pieces can also turn white with the outer round finish. The reason for the high quality is that, in addition to the material itself, the quality control of the grinding process is also very strict, so that the surface of the tool is not burned.
Black is a nitrided bit. It is a chemical method to improve tool durability by placing the finished tool in a mixture of ammonia and water vapor after insulation treatment at 540-560°C. Most of the black bits currently on the market are just black (to cover up burns or black skin on the surface of the tool), but the actual use has not been effectively improved.
There are three drill production processes, and the black one is laminated and the worst. The white is light and ground. Unlike rolling, there is no high-temperature oxidation, so the grain structure of the steel is not damaged and is used to drill slightly harder parts.
The yellowish-brown drill, known in the industry as a cobalt-containing drill, is something of a subterfuge in this drilling industry. The cobalt-containing drill was originally white and produced by grinding. Later, when it was atomized, it turned yellowish-brown (often called amber), which is what is in best circulation today.
Another type of drill is the M35 (Co 5%), which is gold. This type of drill is called titanium coated drill and is divided into decorative and industrial coating. The decorative coating does nothing; It's just beautiful and golden. The industrial coating is excellent, with a hardness of HRC78, which is higher than the hardness of cobalt-containing drills (HRC54).
How to choose a drill
Since color is not a criterion for judging the quality of a drill, how to choose a drill?
From experience, the white one is usually a fully ground HSS drill and should be of the best quality. Gold drill bits are coated with titanium nitride and can be of good or poor quality. The quality of black drills also varies; some are made of low-carbon tool steel, which is easy to anneal and rust, which is why blackening treatment is necessary.
When purchasing a drill, look for the logo on the drill shank and the diameter tolerance marking. The marking must be clear, and the quality of the laser or electrical etching must not be bad. If the word is shaped and the edge of the word is protruding, the drill is of poor quality because the protruding outline of the word causes the drill to be held less precisely than necessary. The word is of good quality if the edge is clear and intersects well with the cylindrical side of the drill shank.
Another thing to look at is the tip of the drill bit. The fully ground drill has a good open edge and the spiral face meets the requirements, while the low-quality drill is not very good at the back corner face.
Drilling accuracy
With the drill selected, let's examine the drilling accuracy.
Drilling accuracy is influenced by factors such as hole size, positional accuracy, coaxiality, roundness, surface roughness and hole burr.
Factors that affect hole accuracy during drilling include:
① The cutting accuracy and conditions of the drill, such as tool holder, cutting speed, feed rate, cutting fluid, etc.
② Drill size and shape, including length, edge shape, core shape, etc.
③ Workpiece shape, such as hole side shape, hole shape, thickness, assembly status, etc.
1 . Enlargement
Flaring is caused by drill oscillation during the process.
Clamp oscillation has a significant impact on both hole diameter and positioning accuracy. If the clamps are worn, it is important to replace them in a timely manner.
Drilling small holes can be challenging in terms of measuring and adjusting wobble. To overcome this problem, it is recommended to use a drill with a thick shank and a small edge that has good coaxiality between the shank and the edge.
In the case of machining with a resharpened drill, a decrease in hole accuracy is normally due to the asymmetrical shape at the back.
Controlling the blade height difference can effectively reduce the amount of hole expansion.
two . The roundness of the hole
Drill vibrations can cause holes to have a polygonal shape, with the walls appearing striated.
Triangular or pentagonal shapes are common among polygonal holes.
The triangular shape is the result of two centers of rotation of the drill that vibrate at frequencies that alternate every 600 intervals.
The main cause of vibration is an imbalance in cutting forces. During the first turn, the hole circularity processing is not good, leading to an imbalance in cutting forces during the second turn, and the vibration repeats.
However, the vibration phase is slightly changed, resulting in a striated pattern on the hole wall.
When drilling reaches a certain depth, the friction between the ribbed edge of the drill bit and the hole wall increases, causing vibration to decrease, striations disappear, and roundness improves.
The hole appears funnel-shaped in longitudinal section.
For the same reason, pentagonal, heptagonal and other holes may also appear in the cut.
To avoid this phenomenon, measures should be taken to improve the rigidity of the drill, increase the amount of feed per revolution, reduce the back angle, repair the transverse edge, and control the vibration of the chuck and the height difference of the cutting edge, as well as the asymmetry of the back and flaps.
3 . Drilling holes in inclined and curved surfaces
Poor positioning accuracy occurs when the drill has a beveled, curved or stepped surface because the drill is supported radially on only one side, leading to reduced tool life.
To improve positioning accuracy, the following measures can be implemented:
(1) Start by drilling the center hole.
(2) Mill the hole seat using an end mill.
(3) Use a drill bit that has good penetration and rigidity.
(4) Decrease the feed rate.
4 . Burr treatment
During drilling, burrs can form at the entrance and exit of the hole, especially when working with resistant materials and thin sheets.
This occurs because the material being drilled undergoes plastic deformation when the drill is about to break.
At this point, the triangular portion that should be cut by the drill near the outer edge of the drill is deformed and bent outward due to the axial cutting force, and further curled under the influence of the beveled outer edge of the drill and the ribbed cutting edge , resulting in a rolled edge or burr.