Tool selection and determination of cutting parameters in NC machining are carried out through human-computer interaction, which differentiates it from machining with conventional machine tools. To perform NC machining effectively, programmers must have a good understanding of the basic principles of tool selection and cutting parameters, take into account the unique characteristics of digital machining in their programming, and be able to correctly choose tools and appropriate parameters.
CNC machining tools must be designed to work with the high speed, efficiency and automation of CNC machine tools. They generally include standard tools, standard tool holders, and a limited number of specialized tool holders. The tool holder is attached to the tool and mounted on the machine tool spindle, which has led to greater standardization and modularization.
NC cutting tools can be classified in several ways.
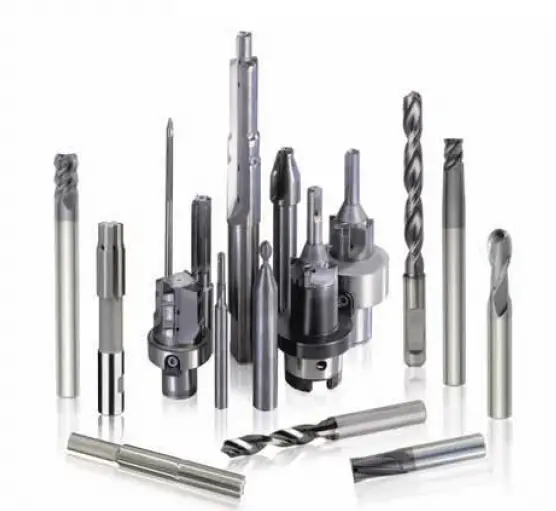
1. NC machine cutting tool structure is
1. Integral type;
2. Inlay type, which adopts welding or machine clamp connection. The type of machine clamp can be divided into non-indexable and indexable;
3. Special types such as compound cutting tools, cushion cutting tools, etc.
2. Materials used to make tools
1. High speed steel cutting tools;
2. Carbide cutting tools;
3. Diamond cutting tools;
4. Other material cutting tools, such as cubic boron nitride cutting tools, ceramic cutting tools, etc.
3. Classification of cutting process
1. Turning tools including outer circle, inner hole, thread, cutting tool and so on;
2. Drilling tools, including drill bits, reamers, taps, etc.;
3. Boring tools;
4. Milling tools, etc.
To meet the requirements of CNC machine tools, the number of adjustable and durable tools has reached 40%~90% of the total number of CNC machine tools in recent years.
4. Features of NC tools
1. Good rigidity (especially rough machining tools), high precision, low resistance to vibration and thermal deformation;
2. Good interchangeability, convenient for quick tool changing;
3. High service life, stable and reliable cutting performance;
4. Tool size is easy to adjust to reduce tool change adjustment time;
5. The cutting tool must be able to reliably break or roll chips so as to facilitate chip removal;
6. Serialization and standardization to facilitate tool programming and management.
5. Tool selection
Tool selection in NC programming is performed through human-computer interaction. The cutter and shank should be selected based on the processing capacity of the machine tool, workpiece material performance, processing procedure, cutting parameters and other relevant factors.
The general principle for tool selection is to choose tools that are easy to install and adjust, have good rigidity, high durability and precision. When meeting processing requirements, try to choose a shorter tool holder to increase the processing rigidity of the tool.
When selecting a tool, make sure that its size matches the size of the surface of the part to be processed. In production, an end mill is often used to process the peripheral contour of flat parts. For milling flat surfaces, a cutter with a carbide blade should be used. During high-speed milling, a convex cutter or channel cutter must be chosen. For machining rough surfaces or machining rough holes, a corn mill with carbide blade can be used. Ball end mills, ring mills, taper mills and disc mills are often used to machine some three-dimensional profiles and variable angle profiles.
When machining free-form surfaces (such as molds), the cutting speed of the ball nose tool is zero at its end, therefore, to maintain machining accuracy, the spacing between cutting lines is generally set to a dense distance. As a result, ball nose tools are often used for surface finishing. Flat end mills are superior to ball end mills in terms of surface machining quality and cutting efficiency. Therefore, whenever possible, flat end mills should be preferred for roughing and finishing machining of curved surfaces.
The durability and precision of cutting tools have a significant impact on their cost. It is important to keep in mind that although the use of high-quality cutting tools may increase the cost of cutting tools, it can significantly reduce the overall processing cost while improving processing quality and efficiency.
In a machining center, different cutting tools are mounted in the tool magazine, and tool selection and exchange are carried out according to program specifications at any time. To ensure quick and accurate installation of standard tools for drilling, boring, expanding, milling and other processes, it is necessary to use a standard tool holder.
Programmers must be familiar with the structural size of the tool holder, the adjustment method, and the adjustment range used on the machine tool in order to determine the radial and axial dimensions of the tool during programming.
6. The principle of tool arrangement must be followed
In the machining process of economical NC machine tools, manual grinding, measuring and replacing cutting tools often take up a lot of auxiliary time. Therefore, it is important to organize the order of cutting tools efficiently. The following principles must be followed:
- Minimize the number of tools used.
- Once a tool is clamped, all machining steps it can perform must be completed.
- Tools for roughing and finishing must be used separately, even if they have the same size and specification.
- Milling must be carried out before drilling.
- The surface must be finished first, followed by the two-dimensional contour.
- Whenever possible, the automatic tool change function of the NC machine tool should be used to improve production efficiency.
7. Principle of reasonable selection of cutting parameters
During rough machining, productivity is typically improved, but economics and processing cost must also be considered. In semi-finishing and finishing, cutting efficiency, economy and processing cost must be considered while maintaining processing quality. Specific values should be determined based on the machine tool manual, cutting parameter manual and experience.
The following factors must be considered:
Cutting depth t: If the machine tool, workpiece and tool rigidity allow, t is equal to the machining tolerance, which improves productivity. A finishing tolerance must be reserved to ensure machining accuracy and surface roughness of the part. NC machine tools may have a slightly smaller finishing margin than conventional machine tools.
Cutting width L: L is generally proportional to the tool diameter D and inversely proportional to the depth of cut. In the machining process of economical NC machine tools, L is generally in the range of L = (0.6 ~ 0.9) D.
Cutting speed v: Increasing v improves productivity, but also affects tool durability. The choice of v depends mainly on the durability of the tool, which decreases as v increases. The cutting speed also depends on the processing material. For example, when milling 30CrNi2MoVA alloy with an end mill, v can be about 8 m/min, while milling aluminum alloy with the same end mill, v can be more than 200 m/min.
Spindle speed n (R/min): Spindle speed is generally selected based on the cutting speed v. The calculation formula is: v = πnd/1000. The control panel of the NC machine tool usually has a spindle speed adjustment (magnification) switch, which can adjust the spindle speed by an integral multiple during machining.
Feed speed vF: vF should be selected based on the machining accuracy and surface roughness requirements of the parts, as well as the cutting tool and workpiece materials. Increasing vF improves production efficiency. When the surface roughness requirement is low, vF can be higher. During processing, vF can also be adjusted manually via the adjustment switch on the machine tool control panel, but the maximum feeding speed is limited by the rigidity of the equipment and the performance of the feeding system.