Laser welding is highly advantageous due to its fast speed, minimal deformation, aesthetically pleasing welds and high strength. It is widely used in areas such as aviation, automobiles and medicine.
Specifically, laser fusion welding is a non-contact welding process that creates a variety of welding seam shapes with excellent seam consistency. It has enormous potential in sheet metal manufacturing.
This article focuses on the application of sheet metal design in laser welding of housing structures with 45° bevel flanged joints.
Sheet metal design on laser welding box structure
The case body is made of 1.5mm thick 304 stainless steel and has dimensions of 200mm × 200mm × 115mm. The box is bent at angles of 90°, 90° and 80° from bottom to top.
The structure of the box is illustrated in Figure 1.
Table 1 displays laser welding parameters.
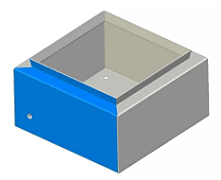
Figure 1 Schematic diagram of the box structure
Welding process | Laser thermal conduction welding |
---|---|
Power (W) | 3,000 |
Speed (m/min) | 1.8 |
Blur (mm) | 10 |
Table 1 Laser welding parameters
In the traditional process of welding stainless steel box structures, it is common to carry out grinding and polishing treatments after welding, in order to obtain a more aesthetically pleasing final product. However, these subsequent procedures can be complicated and time-consuming, and can also result in weld deformation and penetration.
Laser welding, on the other hand, offers significant advantages in sheet metal welding, such as fast welding speeds, minimal deformation, and visually appealing welding seams. As such, finding ways to apply the benefits of laser welding, including its narrow heat-affected zone and high precision, to the welding of box structures has become an urgent issue to address.
Laser welding box frame overlay design
In welded stainless steel box structures, box fillet welding forms a significant part of the overall welding process.
To obtain a round laser welding seam, we optimize the overlap amount in traditional welding techniques, as illustrated in Figures 2 and 3. In these figures, t represents the plate thickness, a is the overlap amount, b is the position denotes the center of the laser on the plate cross-section and α denotes the laser inclination angle.
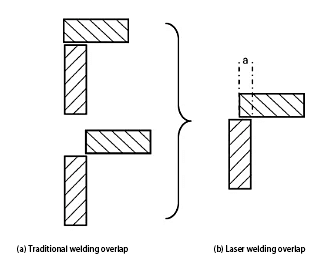
Figure 2 Improved fillet weld seam overlap
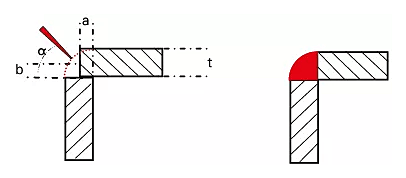
Figure 3 Laser Welding Overlay
The optimized amount of overlap is welded using laser thermal conduction welding. The defocus distance is precisely set to 10.00mm and the focusing accuracy is maintained within 0.01mm through the use of an automatic focusing system.
With the aid of a high-magnification CCD camera, the b value can be precisely positioned, resulting in a round laser weld without the need for filler wire, as illustrated in Figure 4b.
This optimization method for the amount of overlap is best suited for boards with a thickness of 3 mm or less, where the values of a, b and α are determined by the value of t.

Figure 4 Schematic diagram of optimizing the amount of overlap and the actual effect of laser welding
Corner release groove design of laser welding box frame
In welded stainless steel case structures, optimization of the corner relief groove is crucial as it directly impacts the effectiveness of the case bottom structure.
In traditional welding processes, rectangular or rounded corner relief grooves are commonly used. However, such corner relief grooves can easily result in welding or underwelding when using laser welding techniques.
The schematic diagram of the corner relief groove is illustrated in Figure 5.
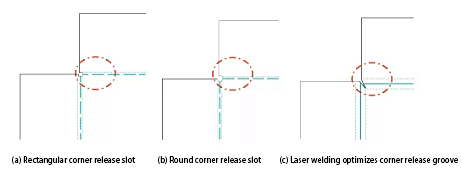
Figure 5 Corner Release Slot Schematic
By using the corner relief groove process block for laser welding, the product structure can be optimized.
With laser welding, it is possible to obtain a complete and rounded welding effect, with almost no need for secondary treatment and greatly reducing subsequent processing time, as shown in Figures 6 and 7.
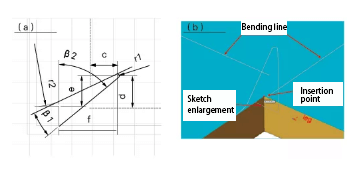
Fig. 6 Schematic diagram of corner release groove laser welding project
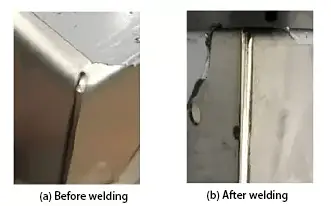
Figure 7 Actual effect of laser welding of corner release groove
45° Bevel Interface Design for Laser Welding Box Frame Flanging
In the box structure made of welded stainless steel, the 45° bevel interface of the flange has difficulty closing tightly due to the amount of bending deformation, as illustrated at A in Figure 8. This issue represents a significant challenge for laser welding. .
Consequently, the interface design directly impacts the welding quality of the box structure. Furthermore, there will be a considerable gap in B, making direct laser welding difficult to manage.
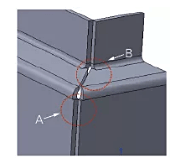
Figure 8 Schematic diagram before optimization
To solve this problem, we optimized the cabinet structure. In the design process, a portion of the step surface metal was removed and two smaller step surfaces were extended, as illustrated in Figure 9a.
During unfolding, the previously cut portion is offset using the end surface as a reference, as shown in Figures 9b and 9c.
At B in Figure 8, two stepped surfaces are alternatively extended to increase the amount of metal compensation, which compensates for the gap created in this area. This solution is illustrated in Figure 9d.
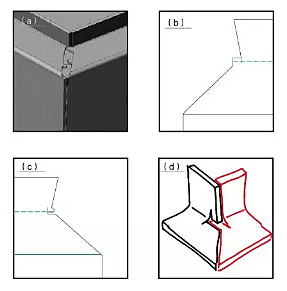
Figure 9 45° Bevel Flange Interface Sheet Metal Design Schematic
Figure 10 demonstrates the result of the laser welding process.
As shown in Figure 10a, the interface is hermetically sealed, meeting the requirements of the laser welding process. The surface of the welding seam is smooth and aesthetically pleasing, with a natural transition and no visible sags or welding defects.
Furthermore, as shown in Figure 8, the gap in B is also well filled, demonstrating the effectiveness of the implemented optimization solution.
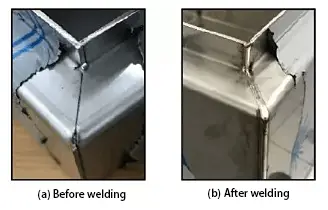
Figure 10 Laser welding effect of flange 45° bevel interface
Conclusions
As the welding process continues to evolve, traditional sheet metal design schemes will gradually become outdated. Likewise, as laser welding gains greater adoption in the sheet metal industry, there will be a need for new sheet metal design solutions for laser welding. It is imperative to develop and introduce innovative designs that are best suited to the capabilities and limitations of the laser welding process.