Classification by purpose
There are many types of turning tools, which can be divided into:
Cylindrical Turning Tool:
According to the main deflection angle, there are 95 degrees (for semi-finishing and finishing of the outer circle and end face), 45 degrees (for outer circle and end face, mainly for rough turning), 75 degrees (mainly for rough turning of outer circle), 93 degrees (mainly for profile finishing) and 90 degrees (for roughing and finishing turning of the outer circle).
Channel Tool:
The outer groove turning tool is mainly used for outer circle cutting and grooving, and the inner groove turning tool is mainly used for inner groove processing
Thread turning tool:
Thread turning tools are categorized into two types: external thread turning tools and internal thread turning tools. External thread turning tools are used to process external threads, while internal thread turning tools are used to process internal threads.
External thread turning tool
Internal thread turning tool
Inner Hole Turning Tool:
It is mainly used for internal hole processing
According to the structure, it is divided into:
Integral type: The main body of the integral type tool is made of one piece and is not divided. This makes grinding on sharp cutting edges easier and the tool has good rigidity.
It is suitable for small turning tools and non-ferrous metal turning tools.
Related Reading: Ferrous vs Non-Ferrous Metals
Welding type: It is connected by welding method and divided into tool head and tool shank.
It has compact structure and convenient manufacturing.
It is suitable for all types of turning tools, especially small tools.
Machine clamp type: the blade is fixed to the tool bar with a mechanical bracket. The blade can be replaced after it becomes dull.
It is a commonly used tool for NC lathe. The toolbar is reused.
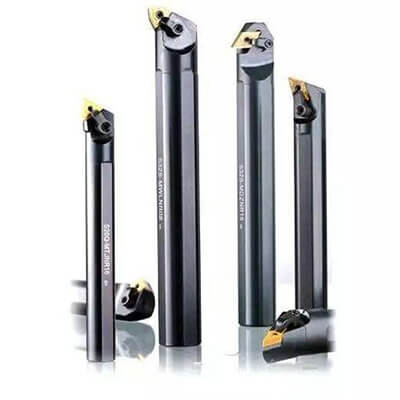
Special type: such as compound cutter, damping cutter, etc.
Classification by turning tool material
High Speed Steel Tool:
It is made of high-speed steel and can be continuously polished, making it a general tool for rough and semi-finish machining.
Carbide Cutting Tool:
The blade made of carbide is suitable for cutting various materials, including cast iron, non-ferrous metals, plastics, chemical fibers, graphite, glass, stone and common steel. It is also capable of cutting challenging materials such as refractory steel, stainless steel, high-strength steel and tool steel.
Diamond:
The blade is inlaid with diamond, which has the benefits of high hardness and wear resistance, low coefficient of friction, high modulus of elasticity, high thermal conductivity, low coefficient of thermal expansion and low affinity with non-metallic materials. It is suitable for precision processing of brittle and hard non-metallic materials such as graphite, high wear-resistant materials, composites, high-silicon aluminum alloys and other ductile non-ferrous metal materials.
Other materials :
Cutting tools such as cubic boron nitride and ceramics are being developed for rough machining and intermittent cutting of high hardness cast iron alloys.
Four Station Tool Rest Assembly Requirements
1. The tip of the turning tool must be at the same height as the center of rotation of the workpiece.
Common methods of tool tip to center height: In the first step, when installing the turning tool, make sure the tip of the tool is equal to the top of the tailstock. The second step is to perform a test cut on the end face.
2. The length of the turning tool extending out of the tool holder must be appropriate.
The turning tool is mounted on the tool holder. Generally, the length extending from the tool holder is 1 to 1.5 times the thickness of the tool bar and should not be too long. If the extension is excessive, the rigidity of the toolbar will deteriorate, making it prone to vibrating during cutting.
3. The sizing block of the NC lathe turning tool must be flat, and the smaller the number, the better. The sizing block must also be aligned with the tool holder to avoid vibration.
4. The NC lathe turning tool must be fixed to the tool holder with at least two screws, and they must be tightened one by one in sequence. The clamping force must be appropriate.
5. The center line of the NC lathe turning toolbar must be perpendicular to the feed direction, otherwise the values of the main and auxiliary deflection angles will be changed. If the NC machine tool is different, the loading and unloading method will also be different.