When choosing a light source for laser welding, various factors such as welding material, joint geometry, speed and others must be taken into consideration.
In the manufacturing industry, the correct selection of a laser source is a practical challenge that manufacturers must face due to the widespread use of laser welding.
Currently, the laser sources available on the market include optical fiber, pulsed Nd:YAG, diode, disc and CO 2 laser sources. (Note: The CW Nd:YAG laser source has been largely replaced by optical fiber and disk lasers and is therefore not discussed in this article).
Choosing a laser source must consider several factors, including welding material, joint geometry, welding speed, geometric tolerance, system integration requirements and, of course, budget constraints.
Each laser source has unique characteristics that can meet different welding requirements. In some cases, they can also be replaced.
4 types of laser
CO 2 laser
The CO 2 laser, which operates at a wavelength of 10,604 nm and has a power range of 1 to 20 kW, is a highly developed laser technology. It has been the primary laser source for high-power processing since the 1980s.
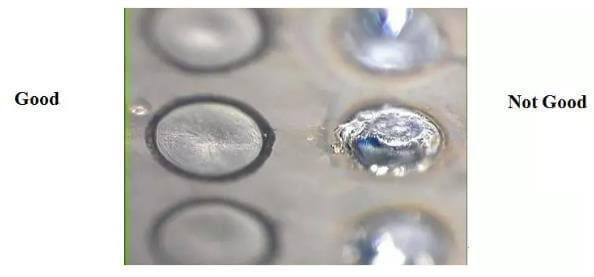
fiber laser
This efficient diode-pumped laser uses a silicon-based fiber with a small core diameter.
The laser source is housed within the optical fiber, eliminating the need for additional correction. With the small core diameter optical fiber mapped to the focusing lens, the minimum focus size can reach 10 microns.
The compact laser is available in two configurations: low power welding (less than 300 W) and multimode for high power welding.
diode laser
The improvement in the power of single-surface diode laser devices, the advent of new cooling channel technology, and the advancement of micro-optical element technology that can focus the beam on optical fibers with a diameter of less than 1000 microns have led to the rise of lasers. of diode as welding sources.

Disk laser
The thin disc of flat YD YAG crystal at the center of the CW laser, known as the disc laser, was designed to eliminate the problems inherent in the rod laser. A disk with a thickness of 0.01 inch is used and kept cool by a support cooling device. This design allows the laser to reach a power of 10 kW while maintaining excellent beam quality.
Pulsed Nd:YAG laser
This laser employs a single Nd:YAG laser rod to generate high peak power and low average power for welding through flash lamp excitation. For example, a 35W average power laser can produce a peak power of 6kW. The combination of high peak power and narrow pulse width not only ensures the material welding quality, but also offers effective control over the energy input.
Select the laser according to the size of the penetration
Laser choice can be categorized into three groups based on penetration: less than 0.01 inch, between 0.01 to 0.03 inch, and more than 0.03 inch.
Generally, multiple laser sources can be used to complete the welding, however, for performance and budget reasons, only one or two light sources may be chosen.
The final decision may also be influenced by several other factors, such as sample quality, geographic considerations, after-sales service, system integrator preferences, and popularity.
Weld penetration less than 0.01 in.
The pulsed Nd:YAG laser is the most commonly used laser, followed by the fiber laser. In terms of component assembly, joint shape, material and coating, the entire welding process must be precisely controlled, making the pulsed Nd:YAG laser the best choice.
With its high peak power, the Pulsed Nd:YAG laser can produce a welding beam with a spot size greater than 1000 microns, providing great flexibility in choosing the spot size and maximizing the welding process window, while ensuring the necessary tolerances in the production environment.
The fiber laser is the only continuous wave laser in this category and can produce a spot size after beam focusing of less than 25 microns, providing the high power density required for welding. However, to maintain cost competitiveness in the micromachining area, the power of fiber lasers is generally limited to 200W, which restricts the maximum spot size and power density.
The size of the welded joint typically does not exceed 75 microns, which is one of the biggest limitations of fiber lasers. In actual production, it is often difficult to guarantee an error range of ±15mm when adjusting joints or components according to the fit tolerance and overlap tolerance.
Fiber lasers are mainly used in overlap welding of thin materials with high requirements for welding joints to ensure stability. The fiber laser uses a 150mm focal length lens that can produce light spots with a diameter of less than 25 microns, providing ample processing space. With lap welding, the fiber laser can produce a weld with a penetration depth of 0.01 in. or greater at high speed, with a penetration depth of 0.004 in. achieved by a 200 W single-mode fiber laser at speeds of up to 50 in./s.
On the other hand, pulsed Nd:YAG laser can meet almost all applications except thin sheet welding. Its large spot size, pulse width and peak power range allow adjustment and optimization to meet various welding requirements.
0.01 ~ 0.03 in. (0.254-0.762 mm) weld penetration
The application classification of pulsed Nd:YAG laser and fiber laser is still applicable, but the range is limited. The pulsed Nd:YAG laser is mainly used for spot welding, while fiber lasers with a power of approximately 500W and a spot diameter of 0.01μm can be used in butt welding and fillet welding with low tolerance. The cost-performance of pulsed Nd:YAG laser is relatively high.
Lasers with power levels of 500W and 25W produce different weld penetrations at various welding speeds. Peak power guarantees penetration performance, while average power determines the seam welding speed.
Diode lasers with power ranging between 500W and 800W are suitable for welding components with large tolerances, but the speed is generally slower than that of fiber and disk lasers. However, its great tolerance can compensate for this disadvantage.
Weld penetration greater than 0.03 in. (0.762mm)
All types of lasers are suitable for this range. The penetration depth of the pulsed Nd:YAG laser is about 0.05 in. (1.27 mm), while other laser types can reach up to 0.25 in. (6.35 mm) and some even exceed 0.5 in. (12.5mm).
Generally speaking, parts suitable for pulsed Nd:YAG laser welding in this range are relatively small, such as pressure sensors with seam welding.
The automotive industry requires a wide range of welding and fiber optic applications, CO 2 disk and diode lasers can be used. In terms of speed and penetration, the automotive industry covers almost all welding applications.
Seek balance
The main differences between laser sources are beam quality, brightness and wavelength.
Beam quality refers to the focusing ability of the laser and brightness refers to the power density in the focused beam.
For example, the CO2 laser and fiber laser have similar beam quality, so if other parameters are the same, they can produce light spots with the same diameter.
However, the wavelength of the fiber laser source is one-tenth of the wavelength of the CO 2 light source, which means that the spot diameter it can produce is also one-tenth of the CO 2 light source. The fiber laser source also has better beam quality and brightness.
In laser welding, beam quality and brightness directly affect penetration depth and speed, but do not have as direct an effect on welding stability and tolerance.
Therefore, it is important to find a balance between welding performance and quality and the width of the process window. It is worth noting that although beam quality can be reduced to meet specific needs, poor beam quality cannot be improved.
With a penetration of 0.25 inches, the welding speeds of the lasers mentioned above are quite similar. Optical fibers and disks are faster than CO 2 while diodes are slower.
Welding with high-power lasers typically requires two shifts, making the cost of purchasing the laser a consideration in the selection process. While CO 2 laser is widely used and familiar to many users, its one-time welding cost is significantly higher than that of fiber, disc and diode lasers.
Compared with plasma and arc welding, laser welding has more advantages in welding applications that require penetrations of more than 0.25 inches as it can greatly reduce thermal deformation. This reduction helps maintain the geometric shape of the piece, eliminating the need for remodeling. However, mating parts may cause problems at this thickness. To overcome this, a wire filling process flow or a combination of laser welding, plasma welding and arc welding can be used.
Conclusion
There are several types of laser sources available for laser welding, each with its unique characteristics and suitability for specific requirements.
It is crucial that users fully understand which laser source can best meet their welding needs.
To obtain a welding system, the ideal approach is to collaborate with your system supplier, who will be able to determine the laser that is best suited for you.
You can also contact several laser manufacturers and provide welding samples to determine the ideal solution.
When selecting a laser, it is important to keep in mind that welding must be balanced in terms of penetration, speed, stability, accommodation of production parts and tolerance.