The main tool for machining flat parts is a face mill, which has cutting edges along its circumference and end face. The cutting edge of the end face is considered a secondary cutting edge.
The face milling cutter typically has a large diameter, so when selecting the cutter, it is common to separate the teeth and the cutter body to ensure long-term use.
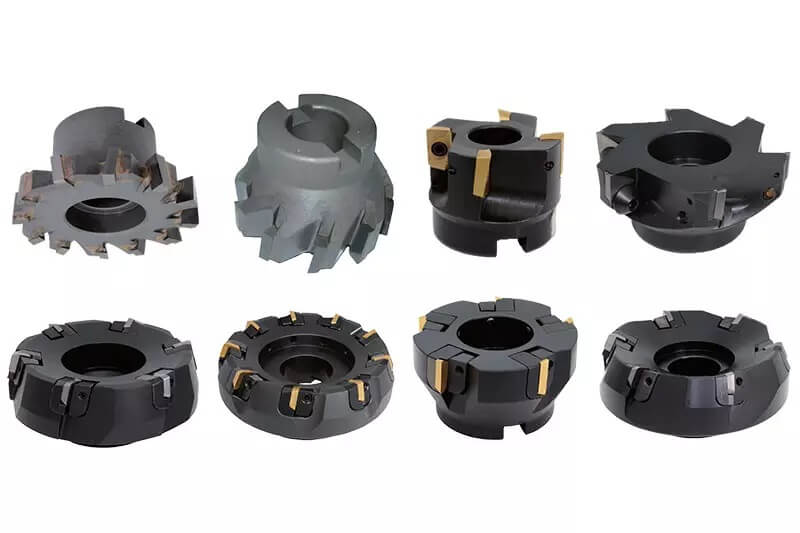
1. Selection of face mill diameter
The selection of face mill diameter is mainly divided into three cases:
(1) When machining a small flat area, it is important to choose a tool or cutter with a diameter larger than the plane width to achieve single-plane milling. Best results are achieved when the diameter of the flat cutter is 1.3 to 1.6 times the width of the machining surface.
(2) For a large area of the machining plane, multiple passes with a cutter of appropriate diameter are required. The diameter of the cutter will be limited by machine tool limitations, cutting depth and width, and blade and tool size.
(3) When the machining plane is small and the workpieces are scattered, a smaller diameter end mill should be selected for milling. To maximize efficiency, the cutter must have 2/3 of its diameter in contact with the part, which means that the diameter of the cutter is equal to 1.5 times the milled width.
When forward milling, the appropriate ratio of tool diameter to cutting width will ensure a proper cutting angle for the cutter when entering the workpiece.
If there is uncertainty about the machine tool's ability to maintain this cutting ratio, the axial cutting thickness can be completed in multiple passes to maintain the relationship between the cutter diameter and cutting width as much as possible.
2. Selection of the number of cutter teeth
When choosing a cutter for machining, it is important to consider the number of teeth on the cutter. For example, a 100mm diameter sparse-toothed milling cutter has only 6 teeth, while a 100mm diameter dense-toothed milling cutter may have 8 teeth. The density of cutter teeth affects production efficiency and product quality.
Dense teeth lead to greater production efficiency and better product quality, but they also make chip discharge difficult. Cutters can be divided into sparse teeth, fine teeth and dense teeth based on the diameter of the teeth. Sparse teeth are used for rough machining of parts and have 1 to 1.5 blades for every 25.4 mm in diameter, providing ample space for chip retention.
This type of tool is used to cut soft materials that produce continuous chips and is best suited for cutting with long, wide blades.
Dense teeth are ideal for stable machining conditions and are commonly used for rough machining of cast iron. They are also suitable for shallow, narrow cuts in superalloys and for cuts without space for chips. Dense teeth are used in finish milling with a back axial cutting amount of 0.25 to 0.64 mm, resulting in a low cutting load per tooth and reduced energy requirements. This type of cutter is ideal for processing thin-walled materials.
The tooth pitch determines the number of cutter teeth involved in cutting at the same time during milling. It is important to have at least one blade cutting at all times to avoid milling impacts that can cause damage to the tool and overload the machine tool. Furthermore, the number of teeth on the blade must be selected to allow the chips to easily roll up and exit the cutting area. Insufficient space to hold the chips can cause chips to jam, damaging the cutting edge and potentially the workpiece. The blade must also have sufficient density to ensure that at least one blade is cutting at all times during cutting, or it may cause severe impact, leading to fracture of the cutting edge, damage to the tool, and overloading of the machine tool.
3. Tool angle selection
The cutting angle of the tool can be positioned as a positive rake angle, negative rake angle, or zero rake angle with respect to the radial plane and the axial plane. The zero rake angle, where the entire cutting edge impacts the workpiece at the same time, is generally not used.
The choice of face mill angle affects the contact mode of the flat cutter. To minimize impact on the cutter, reduce cutter damage, and avoid stuv face contact mode, it is important to consider both the cutting angle of the cutter and the geometric angle of the face cutter.
The cutting angle is determined by combining the radial and axial rake angle.
Common basic combination methods include:
- Negative radial tilt angle and negative axial tilt angle.
- Positive radial tilt angle and positive axial tilt angle.
- Negative radial tilt angle and positive axial tilt angle.
- Positive radial tilt angle and negative axial tilt angle.
Tools with negative axial and radial feed angles (referred to as “double negative”) are mainly used for rough machining of cast iron and cast steel, but the machine tool must have high power and sufficient rigidity. The “double negative” blade has a strong cutting edge and can withstand large cutting loads, but the machine tool, workpiece and accessory must also have high rigidity.
Tools with positive axial and radial feed angles (called “double positive”) increase the cutting angle, making cutting lighter and chip removal smoother, but cutting edge strength is poor.
This combination is ideal for processing soft materials and materials such as stainless steel, heat-resistant steel, common steel and cast iron. It should be used when the machine tool has low power, the process system has insufficient rigidity, and chip accumulation tumors occur.
The combination of negative radial rake angle and positive axial rake angle increases cutting edge strength with negative radial rake angle and produces shear force with positive axial rake angle. This combination has strong impact resistance and a sharp cutting edge, making it suitable for heavy milling of steel, cast steel and cast iron.
The positive radial rake angle and negative axial rake angle cause the broken chips to move below the center, causing the chips to scratch the machined surface and leading to poor chip removal.
4. Milling insert selection
The choice of milling insert preparation is also an important factor in flat milling. In some cases, a pressed blade is more appropriate and in others, a ground blade is necessary.
A pressed blade is more economical for rough machining and has better edge strength, making it impact resistant and capable of handling large feedbacks and feeds. It also has a chip bending groove on the rake face that reduces cutting force, friction with the workpiece and chips, and energy demand.
However, the surface of the pressed blade is not as smooth as a ground blade and has low dimensional accuracy, with a large difference in the height of each tool tip on the cutter body. Despite these disadvantages, the pressed blade is widely used in production due to its low cost.
For finish milling, a ground blade is preferred due to its good dimensional accuracy, resulting in high cutting edge positioning accuracy, higher machining accuracy and lower surface roughness value. The trend in grinding milling inserts used in finish machining is to grind a curved chip groove to form a large positive cutting edge, allowing the blade to cut with small feed and backfeed.
However, without a steep rake angle, a carbide blade processed with small feed and back projection will result in friction of the tool tip on the workpiece and reduce tool life.