Introduction
Welding is a primary process in sheet metal manufacturing, characterized by high labor intensity and adverse working conditions. As such, high proficiency is essential.
Automation in welding and the development of innovative joining methods have been consistent focal points for welding technology professionals.
A fundamental aspect of welding automation is controlling welding quality and efficiency. During the process, challenges such as arc and weld seam alignment, uniformity of component gaps, weld penetration, and control of welding distortion must be addressed.
With the rapid advancements in laser welding technology, it has made a significant leap and matured in its application in various industries, including home appliances, high-tech electronics, automotive manufacturing, high-speed train production and precision machining.
The benefits of laser welding can be understood by comparing it with traditional arc welding. This post will delve deeper into the laser welding process and explore how to achieve better results.
To evaluate the quality of a laser weld, the depth/width ratio and surface morphology are taken into account. This post will look at the process parameters that impact these indices.
Laser welding experiments were carried out on stainless steel, aluminum and carbon steel plates. The results provide practical insights that can be used in welding production.
Laser welding is a cutting-edge production technique that uses a laser with high energy density as a heat source for welding. It is widely used in the sheet metal manufacturing industry due to its advantages including high energy density, fast welding speed, environmental friendliness, minimum plate deformation and more.
Laser welding, based on the characteristics of weld seam formation, can be divided into conduction welding and deep penetration welding. Conduction welding uses low laser power, resulting in longer weld pool formation times and shallow fusion depths.
It is mainly used for welding small components.
In contrast, deep penetration welding has high power density, where the metal in the laser irradiation area melts quickly.
This fusion is accompanied by intense vaporization, achieving weld beads with significant depth and a width-to-depth ratio of up to 10:1.
Thin sheet metal components can be joined using various welding methods, including laser welding, brazing, atomic hydrogen welding, resistance welding, plasma arc welding, and electron beam welding.
When comparing laser welding with other common welding techniques, it offers significant advantages in terms of heat affected zone, thermal deformation, weld seam quality, filler material requirement and welding environment.
Comparison between laser welding and other welding methods can be found in Table 1.
Table 1 Comparison between laser welding and other welding methods
laser welding | any less | any less | preferably | no | no special requirements |
Brazing | commonly | commonly | commonly | Yes | General heating |
Argon Arc Welding | more | more | commonly | Yes | Required electrode |
Resistance welding | more | more | commonly | no | Required electrode |
Plasma arc welding | commonly | commonly | commonly | Yes | Required electrode |
Electron beam welding | any less | any less | preferably | no | vacuum |
Features of laser welding
Laser welding uses a laser that channels a high-energy laser beam into an optical fiber. After transmission, it is collimated into parallel light using a collimating lens and then focused on the workpiece.
This results in an extremely high energy heat source that melts the material in the joint. The molten metal cools quickly to form a high-quality weld. The appearance of a laser welded sheet metal part is shown in the figure below.
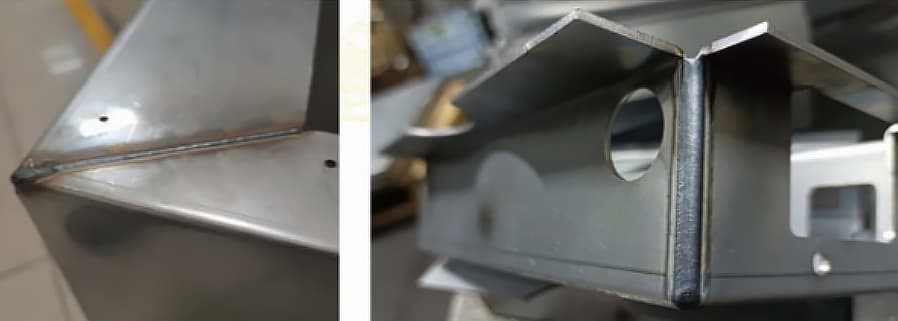
Easy Operation:
Laser welding machines are easy to use. The operation is simple, easy to learn and easy to use. The level of specialization required for operators is relatively low, which translates into savings in labor costs.
High flexibility:
Laser welders can weld from any angle and are adept at accessing hard-to-reach areas. They can handle complex welding components and large, irregularly shaped parts, offering unparalleled flexibility in welding in any orientation.
Enhanced Security:
The high-security welding nozzle is activated only in contact with the metal, featuring a touch switch with body temperature sensor. Specific safety standards must be adhered to when operating the specialized laser generator, including the use of protective glasses to minimize possible eye damage.
Superior laser beam quality:
Once focused, the laser achieves a high power density. With high-power laser focusing and low mode, the resulting spot diameter is tiny, significantly promoting automation in thin plate welding.
Fast welding speed with deep penetration and minimal distortion:
Due to the high power density of laser welding, small pores form in the metal during the process. The laser energy penetrates deep into the material through these pores with minimal lateral propagation. The depth of material fusion is considerable and the welding speed is fast, covering a large area in a short time.
Reduced labor costs:
Due to minimal heat input during laser welding, post-welding distortion is less. This results in a visually appealing weld finish, leading to reduced post-weld processing, which in turn significantly reduces or even eliminates labor costs associated with smoothing and leveling.
Ability to weld difficult materials:
Laser welding is not only suitable for joining a variety of different metals, but also for welding metals and alloys such as titanium, nickel, zinc, copper, aluminum, chromium, gold, silver, steel and cutting alloys. It well meets the needs of developing new materials in household appliances.
Particularly suitable for welding thin sheets and uncoated aesthetic components:
Given its high welding aspect ratio, low heat input, minimal heat-affected zone and reduced distortion, laser welding is especially suitable for welding thin sheets, uncoated aesthetic components, precision parts and thermally sensitive components. This can further minimize post-weld corrections and secondary processing.
Comparison between laser welding and traditional arc welding
Introduction to Arc Welding
Traditional arc welding can be broadly categorized into several types, including stick arc welding, tungsten inert gas (TIG) welding, metal inert gas (MIG) welding, and submerged arc welding.
Stick arc welding involves forming an arc between the electrode and the workpiece, generating heat that melts the metal at the point of contact between the electrode and the workpiece. This creates a pool of molten metal. The electrode is then moved in a specific direction, creating new pools of molten metal and solidifying the previous pools, resulting in the formation of a weld.
A diagram of the welding process is shown in Figure 1.
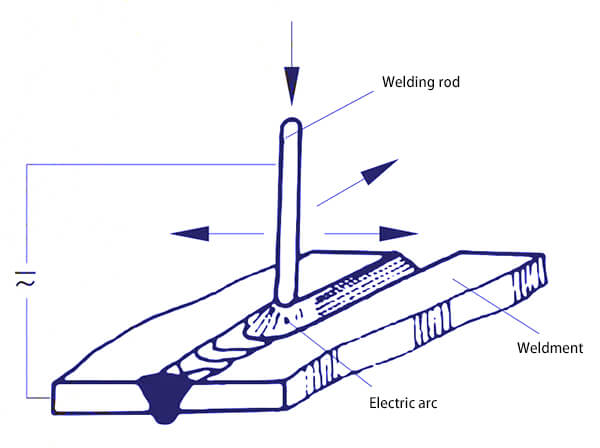
Fig. 1 Schematic diagram of electrode arc welding
Tungsten inert gas (TIG) welding uses a tungsten electrode as a discharge electrode, which is not consumed during the process. The welding area is protected by an inert gas, typically argon, and the heat generated by the arc is used to melt both the base metal and the welding material. The result is a smooth welding surface with little or no spatter.
Gas metal arc welding (GMAW) is a process where an arc is generated between the welding wire and the base metal, causing the wire and base metal to melt. The molten material solidifies, forming a weld.
Although arc welding still holds a dominant position in the welding industry, increasing demands for efficient and high-quality welding have led to limitations in its application in some high-quality sheet metal fabrication fields. Some of the disadvantages of traditional arc welding include:
- The need for high purity argon as a shielding gas, which can be expensive.
- A high level of skill and certification is required for proper operation, making it inaccessible to many.
- The high density current and heat generated during the welding process can negatively impact the welding of metal plates with low melting points.
- Low welding efficiency and slow speed.
- The welding surface is rough, requiring additional grinding to obtain a smooth surface.
- Limited welding force.
Advantages of laser welding
The main laser welding techniques include autofusion welding, oscillation welding, wire fill welding, galvanometer welding and compound welding that combine several welding methods.
Table 1 highlights the advantages of laser welding technology compared to traditional arc welding.
For high-quality sheet metal manufacturing industries that require high value-added products with consistent quality, small weld gaps and high efficiency, laser welding is the best choice.
Table 1 Comparison of characteristics between laser welding and arc welding
Arc welding | laser welding |
High density current is required and the thermal effect is large | Low welding heat, small deformation and thermal effect |
Surface penetration and low welding resistance | Deep penetration and high welding strength |
Contact type, limited by space | Contactless type, less limited by space |
Large arc starting current and large welding range | Small welding point, capable of welding precision parts |
Operators have high requirements and require special operating certificates. | Low requirements for operators |
Low welding efficiency and slow welding speed | High welding efficiency and fast welding speed |
Pollution and electrode loss | No electrode loss |
The surface is rough and requires further grinding. | The surface morphology is stable and there is basically no need for further grinding. |
Laser welding process parameters
Laser Welding Seam Index
Requirements for the welding effect of sheet metal parts vary depending on customer needs. These requirements are mainly reflected in the following indicators:
- Surface morphology (e.g., concave, flat, or convex)
- The depth-width relationship of the weld pool
- Absence of defects such as pores, cracks, impurities and recesses
The weld surface morphology can be changed by adjusting factors such as welding power, defocus and splicing mode. The depth/width ratio of the weld pool is an important factor in determining the strength of the weld.
For customers who have strength requirements for their welding products, a series of steps must be performed, including wire cutting, embedding, grinding and polishing, corrosion testing and microscopic metallographic analysis. This process reflects the hardness of the weld, which is closely related to the depth/width ratio. The tensile strength index of the weld can also be determined through a tensile strength test. Figure 2 shows the metallographic analysis of the penetration rate.
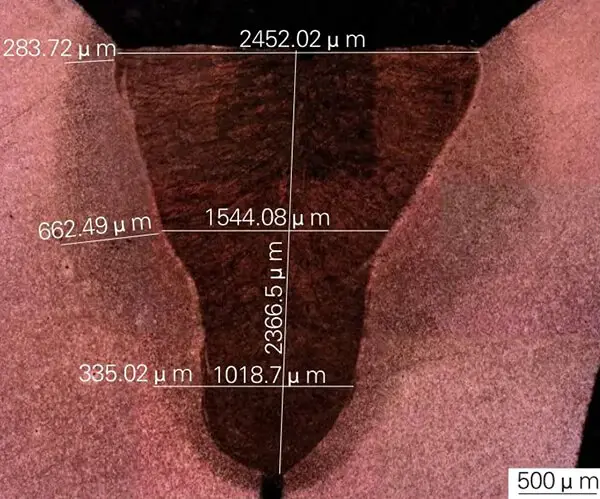
Fig. 2 Metallographic analysis of penetration rate
In certain work environments, welding can present defects such as pores, cracks, impurities and recesses, which can pose serious safety risks. For example, some products require strict air and water tightness standards.
Figure 3 shows a comparison between normal welds and welds with defects.
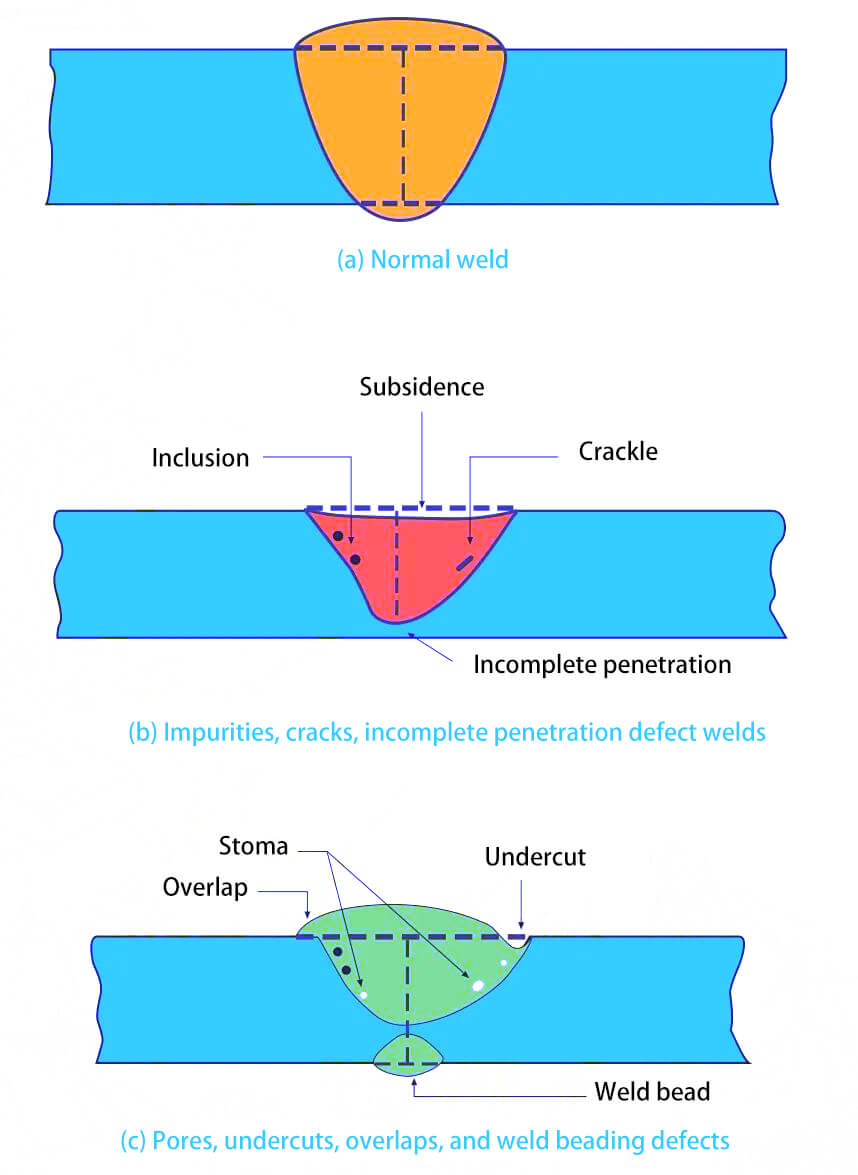
Fig.3 weld seam diagram
Factors influencing laser welding
Several factors directly impact laser welding, including welding temperature, melting point of welding materials, laser absorption rate of welding materials, and thermal influence.
In terms of the welding process, factors such as material properties, laser power, welding speed, focus position, shielding gas and weld gap must be taken into account.
The laser absorptivity of welding materials affects the weld quality. Materials such as aluminum and copper have higher laser absorptivity, while carbon steel and stainless steel have lower laser absorptivity. Welding materials with high absorptivity typically require more energy to melt and form a stable weld pool.
Laser power is the energy source for laser welding and plays a critical role in determining the welding effect. The higher the laser power, the better the welding effect. However, too much laser power can lead to weld pool instability and reduced depth. Therefore, choosing the appropriate laser power value is crucial.
There is an inverse relationship between welding speed and penetration. Faster welding speeds result in lower energy consumption, while slower speeds can cause overheating, especially in heat-sensitive materials such as aluminum.
The focus position directly affects the penetration and width of the weld. When the focus is located on the surface of the welding material, it is called zero focus. When the focus is above or below the welding material, it is called eccentric focusing. Zero focus spot is the smallest and has the highest power density, while off-focus welding has a lower power density but a larger light spot, making it suitable for welding parts with a longer range.
The type and method of gas shielding also affect the welding process. The function of shielding gas is not only to prevent oxidation during welding, but also to suppress the plasma cloud generated during laser welding. The choice of shielding gas can affect the appearance and color of the weld surface.
The weld gap of the part to be welded is related to the penetration, width and morphology of the weld. Too large a weld gap can result in difficult fusion and matching, as well as exposing the laser and potentially damaging the tool or workpiece. Increasing the light spot or flicker can improve welding, but the improvement is limited.
Welding Test Analysis
The welding test was carried out using a Yaskawa GP25 robot, Prima laser, ospri welding joint (core diameter 100μm, focal length 300mm) and WSX wire feeder. The welding effect was tested on 1.5mm Q235 carbon steel plate, SS304 stainless steel and 3 series aluminum alloy plate.
Based on experience, the following reference can be provided for the testing process:
For the 1mm thin plate welding test, an initial power of 1kW and a welding speed of 30mm/s can be used. The reference power can be calculated as P=A·X, where A is a constant coefficient (A≥0) and X is the plate thickness. As the plate thickness increases, the constant coefficient A gradually decreases and is also influenced by the welding method.
Analysis of the carbon steel plate welding process
Refer to Table 2 for the oscillation welding process parameters of 1.5mm thick Q235 carbon steel sheet.
Table 2 Oscillating welding process parameters of Q235 carbon steel plate
NO. |
Laser power (kW) |
Welding speed (mm/s) |
Swing range (mm) |
Swing speed (mm/s) |
Welding effect |
1 | 1.6 | 32 | 1 | 143 | good |
two | 1.6 | 31 | 1 | 148 | good |
3 | 1.6 | 30 | 1 | 148 | good |
4 | 1.7 | 33 | 1 | 151 | good |
5 | 1.7 | 32 | 1 | 152 | good |
6 | 1.7 | 34 | 1 | 150 | good |
7 | 1.8 | 35 | 1 | 153 | good |
8 | 1.8 | 35 | 1 | 154 | good |
9 | 1.8 | 36 | 1 | 154 | good |
10 | 1.9 | 36 | 1 | 156 | good |
11 | 1.9 | 37 | 1 | 155 | good |
12 | 1.9 | 37 | 1 | 160 | good |
Test data shows that during oscillation welding of carbon steel plates, the laser power must be increased with increasing welding speed, while ensuring that the oscillation range remains unchanged. If the oscillation speed is too slow, the weld will be uneven.
In general, less energy is required for self-fusion oscillating welding of carbon steel compared with self-fusion oscillating welding of carbon steel, and less energy is required for self-fusion oscillating welding of carbon steel compared with wire filler welding carbon steel oscillator. The energy required is controlled primarily by power and speed, with higher power and faster speed requiring more energy.
Ideally, to balance quality and efficiency, welding speed should be increased as much as possible. However, welding too quickly can cause instability and be limited by laser power and material properties. Therefore, a balance is usually sought between power and speed.
Analysis of the aluminum plate welding process
In the test, the core diameter of the selected optical fiber was 100μm. To weld highly reflective and heat-absorbing materials such as aluminum and copper, a higher power density is required for fusion. In this case, zero focus welding is required.
Zero-focus welding allows maximum power density with minimum power, making it ideal for welding small parts and melting metal to form a weld pool. Table 3 provides the welding process parameters for different materials.
Table 3 Comparison of welding process parameters for different materials
NO. |
Laser power (kW) |
Welding speed (mm/s) |
Board thickness |
Swing range (mm) |
Swing speed (mm/s) |
Whitening effect | Material |
1 | 1.5 | 2.1 | 1.5 | 1 | 300 | Good | Q235 carbon steel |
two | 1.5 | 1.8 | 1.5 | 1 | 300 | Good | 3 Series Aluminum Alloy |
3 | two | 2.0 | two | 1 | 300 | Good | Q235 carbon steel |
4 | two | 1.7 | two | 1 | 300 | Good | 3 Series Aluminum Alloy |
Test data indicates that with other parameters remaining constant, the ideal welding effect for 3 series aluminum alloy requires a slower welding speed compared to Q235 carbon steel as more heat is required.
Stainless Steel White Blowing Process Analysis
Table 4 shows the comparison of bleaching process parameters for stainless steel welding beads with a thickness of 1.5 mm. The welding effect comparison can be seen in Figure 4.
The welding parameters of the three welds in Figure 4 (from left to right) correspond to serial numbers 1, 2 and 3 in Table 4, respectively.
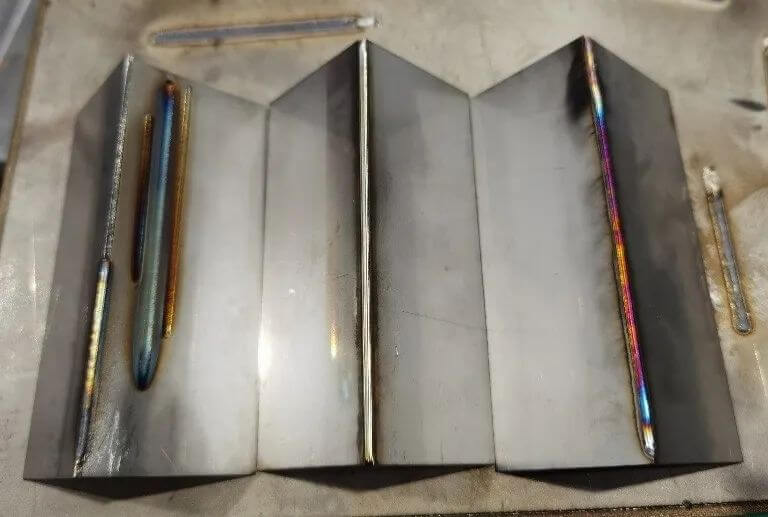
Fig. 4 Comparison of welding effect
Table 4 Comparison of parameters of the bleaching process of stainless steel welding seams
NO. | Laser power (kW) |
Welding speed (mm/s) |
Board thickness | Swing range (mm) |
Swing speed (mm/s) |
Whitening effect |
1 | 1.2 | 1.7 | 1.5 | 1 | 300 | poor |
two | 1.5 | 1.8 | 1.5 | 1 | 300 | good |
3 | 1.6 | 1.8 | 1.5 | 1 | 300 | poor |
To obtain a bleached surface on stainless steel, it is necessary to rapidly cool and crystallize the metal in a shielding gas atmosphere after laser melting. If the power is too high, a lot of heat will be trapped in the metal plate, causing slow cooling and an increased risk of oxidation and discoloration. If the power is too low, the metal may not melt completely.
If the speed is too fast, the blowing tools may not be enough, affecting the blowing effect. If the speed is too slow, excessive heat will build up. To achieve a whitened surface, it is important to find a balance between power, speed and blowing.
If it is not possible to achieve a whitened surface in one attempt, it may be possible to do so by welding one layer at a slightly higher power and then reducing the power for a second layer.
Conclusion
During the laser welding process, to ensure high-quality welding results, it is important to consider a number of factors, including material properties, laser power, welding speed, focus position, shielding gas and weld gap.
For commonly used materials such as carbon steel, stainless steel and aluminum plates, the previously mentioned initial test parameters can be used as a reference and then adjusted according to the specific characteristics of the material and customer requirements to achieve the effect desired welding speed.