At present, the application of laser welding in the development of automotive body stamping parts is mainly reflected in laser welding plate.
This allows different materials, thicknesses and steel coatings to form a single material unit, better satisfying different parts requirements regarding material properties.
With lighter weight, ideal structure and better performance, the body can be lighter and costs can be reduced through promotion and application.
At the same time, it also reduces the research and development costs of automotive stamping dies, design and manufacturing process analysis.
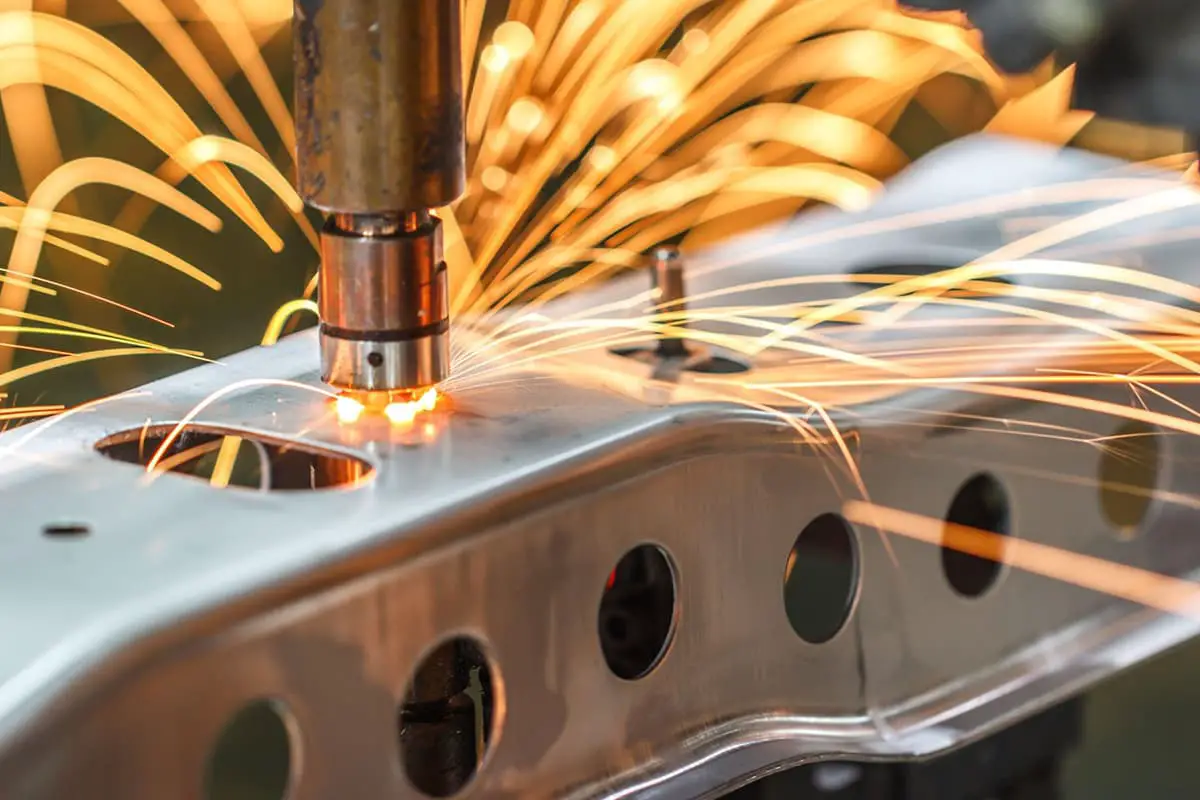
Advantages of laser welding
Laser welding is a type of fusion welding that completes the welding of the joint by a beam of laser energy. The heat generated by welding can be minimized, the heat-affected zone is small and the thermal deformation is minimal.
These advantages determine its importance in the production of automotive stamped parts. The plate flatness requirements during the production of automotive stamping parts are very high, and the welding deformation of the laser welding plate can meet the production needs of stamping parts.
Stamped parts are formed directly by the edge turning process during production, so the plate flatness requirements are higher.
At the same time, the supply quality requirements of laser welding plate will be higher. To reduce sheet metal deformation and improve production efficiency, steel mills generally adopt a welding first, cutting later method.
This reduces deformation caused by welding, preventing quality problems such as poor fusion at the welding joint, lost welds and cracks in the seams.
The application of laser welding to automotive structural components
Taking as an example some of the commonly used laser welded sheet internal parts, such as roof cross beam, wheel arch inner reinforcement sheet and front reinforcement plate, thin and thick sheets are used for laser welding to meet resistance to the body's demands.
Figure 1 shows a laser-welded part of a roof crossbeam of a specific model, which consists of sheets of the same grade, 210P1, but with varying thicknesses, with the thickest sheet being 1.0mm and the thinnest 0. .7mm.

Figure 2: Reinforcement of the laser-welded internal panel for the shell of a given model, with varying thicknesses, with identical plate classes of HC260YD+Z-50/50-M. The thickest plate is 1.0 mm, while the thinnest is 0.8 mm.
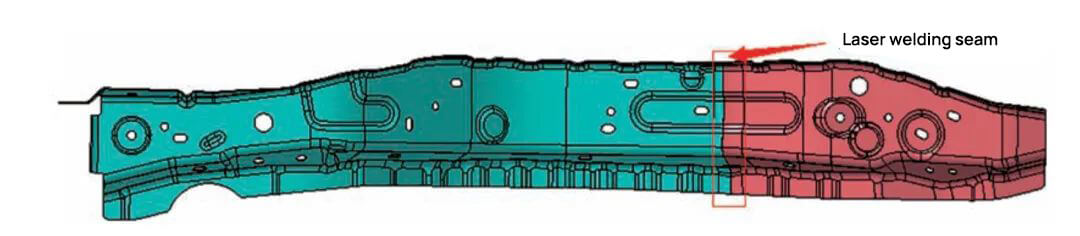
Figure 3: Laser-welded reinforcement panel for the front frame of a specific vehicle model, made up of sheets of varying thicknesses but the same type of material, HC420/780DP. The thickest sheet is 2.0 mm, while the thinnest is 0.8 mm.
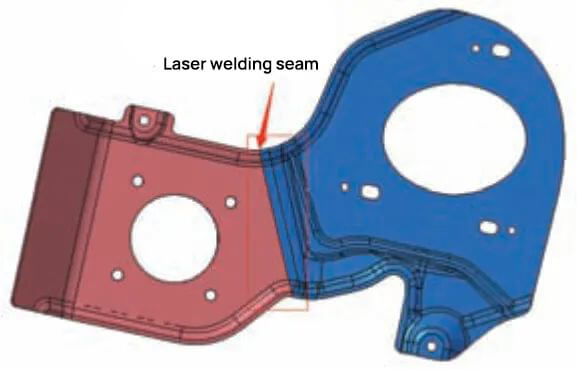
Overcoming challenges in the front reinforcement plate for a given car model
The application of laser-welded plates increased the precision of the vehicle's entire fender, front molding and top lid, resulting in time-saving adjustments to the entire vehicle and reduced labor costs.
However, this production scheme brings significant difficulties to mold development, especially for the front reinforcement plate shown in Figure 3.
The plate presents a substantial variation in thickness and the elastic return of the part during processing is large, according to technical analysis.
This requires a high level of Computer Aided Engineering (CAE) analysis during the design process, as well as high demands on designers' springback compensation techniques.
During the development of this part, problems such as poor formation of the R angle, insufficient strength in areas of thin plates and deformation of the welded assembly frequently occur.
Solution 1: Based on the problems encountered during the production process, a specific process compensation analysis was carried out and elastic compensation was implemented in the early stages of development.
Solution 2: Figure 4 represents the unequal thickness stamping spring feedback compensation analysis for the front gusset plate laser welded assembly of a certain car model shown in Figure 3.
The gray part of the part represents the surface that requires springback compensation.
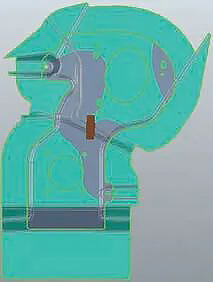
After rebound compensation is complete, the production part can meet the required accuracy.
However, the thin plate area faces problems of overhang and insufficient strength due to the lack of reinforcing ribs.
The deformation problem of the weldment caused by the difference in thickness between the thin and thick plates exceeding the thickness of the thin plate requires additional solutions.
Key Question 3: Figure 5 represents the coordinate data points for the single-piece surface mismatch due to welding deformation of the laser welded assembly of the front panel reinforcement plate for a given vehicle model depicted in Figure 3.
Parallel difference correction was performed for the area inside the red circle in Figure 5.
The final correction conclusion is a surface difference range of -0.5 to 0, which can meet the welding assembly requirements and solve the welding deformation problem.
This problem requires manual arc welding research into the mold to perform rebound compensation for part production.

Summary: Through the above key troubleshooting processes, this part now meets mass production welding requirements and has resolved deformation problems in assembly welding.
At the same time, it provides us with new development approaches and technical improvement guidance for future product development, helping to improve the quality of stamping part development and reduce mold development costs.
It brings cost reduction, efficiency improvement and process optimization benefits to mold manufacturers and component suppliers, while making a significant contribution to environmental protection.
Future development of custom laser welding
Tailor-made laser welding has substantial economic value, offering great appeal to car manufacturers.
Yet, it also presents more significant challenges for the development of stamped parts, requiring greater requirements on preliminary CAE analysis, process layout and technical personnel capabilities.
In the future, laser welding will be applied to automobile body welding and will evolve to include more energetic welding methods to adapt to different scenarios and environmental requirements.
By reducing mold development costs and investment costs for car developers, it creates more economic value for car manufacturers.
Conclusion
(1) Laser fusion welding technology contributes to reducing the cost of stamped parts development and die development.
(2) Laser fusion welding also helps improve the technical proficiency of development engineers in CAE analysis of part springback.
(3) Laser welding also helps reduce vehicle body weight and overall development costs, improving vehicle assembly conditions and reducing deformation caused by extensive welding.