Compared to traditional welding, laser welding offers several benefits, including a small heat input and reduced thermal influence, high aspect ratios and an automated welding process.
Aluminum alloys are popular for their light weight, high toughness, high yield and ease of processing and forming. They are widely used in the production of products such as containers, machines, electrical power equipment, chemical industry components, aviation and aerospace structures.
Replacing steel plate welding with aluminum alloys can significantly improve structural quality. Aluminum is a more reactive metal, with low ionization energy and high thermal conductivity, but is prone to forming refractory Al. 2 Ó 3 film on the surface, which can lead to defects such as unfused areas, pores, inclusions and thermal cracks in the weld, thus reducing the mechanical properties of the joint.
Compared to argon tungsten arc welding or fused argon arc welding, laser welding provides narrow weld beads, small heat affected zones, reduced lap joints, precise control of the welding process and automation.
Currently, laser welding is mainly used in welding thin-walled electronic components, structural parts and aerospace components. The future trend in laser welding research involves the development of 10,000-watt fiber lasers for deep penetration welding of large and thick sheets.
Main high power lasers in laser welding applications
Performance/type | carbon dioxide laser | NdYAG laser |
YbYAG LaserDac |
fiber laser |
---|---|---|---|---|
Wavelength / hum | 10.6 | 1.06 | 1.06 | 1-2 |
Electrical conversion efficiency/% | 12-15 | 2-6 | 20 | 8-10 |
Power density/(MW/cm-2) | 10 | 10 | 100 | 100 |
Maximum power/kW) | 50 | 6 | 15 | 50 |
Beam output | Optical lens | Optical fiber | Optical fiber | Optical fiber |
Metal absorptivity/% | 8 | 20 | 20 | 20 |
Maintenance cycle/hour | 1000 | 1000 | 1oooo | 20,000 |
Laser brightness (103W/mm2steradian)(4kW/h) | – | 7.5 (focal length: 200; Fiber diameter: 0.6mm) |
134.2 (focal length: 200; Fiber diameter: 0.2mm) |
264.4 (focal length:160; Fiber diameter: 0.1mm) |
CO2 gas laser
The working medium for CO 2 lasers is CO 2 gas, and with an output wavelength of 10.6 μm, it can be classified into cross-flow and axial flow based on the excitation structure of the laser.
While CO2 crossflow lasers have reached an output power of 150KW, the beam quality is not suitable for welding. On the other hand, axial flow CO2 lasers have a good beam quality and can be used to weld aluminum alloys with high laser reflectivity.
YAG solid state laser
The working medium for laser systems includes ruby, neodymium glass, and neodymium-doped yttrium aluminum garnet (YAG), with an output wavelength of 1.06 μm.
Compared to CO 2 lasers, YAG lasers are more easily absorbed by metal and are less affected by plasma. Additionally, YAG lasers offer the benefits of fiber optic transmission, flexible welding operations and easy access to the weld position.
Currently, YAG lasers are the main laser systems used for welding aluminum alloy structures.
YLR fiber laser
YLR fiber laser is a newer laser technology developed after 2002. It uses optical fiber as matrix material, doped with different rare earth ions, and has an output wavelength range of 1.08 μm, which also is transmitted via optical fiber.
The fiber laser features a revolutionary dual fiber structure, which increases pump length and improves pump efficiency, resulting in greatly improved output power compared to traditional fiber lasers.
Compared to YAG lasers, YLR fiber lasers were developed later, but offer advantages such as small size, low operating costs, high beam quality and high laser power.
Classification and weldability of aluminum alloy
Aluminum and aluminum alloys can be divided into:
- 1000 Series (industrial pure aluminum)
- 2000 series (Al-Cu series)
- 3000 series (Al-Mn series)
- 4000 Series (Al-Si)
- 5000 Series (Al-Mg)
- 6000 Series (Al-Mg-Si)
- 7000 Series (Al-Zn-Mg-Cu)
Aluminum alloys can be divided into two categories based on process characteristics: deformed aluminum alloys and cast aluminum alloys. Deformed aluminum alloys can be divided into two subcategories: non-heat-treated reinforced aluminum alloys and heat-treated reinforced aluminum alloys.
Each type of aluminum alloy has unique welding properties. For example, non-heat-treated aluminum and aluminum alloys in the 1000, 3000 and 5000 series have good weldability. The 4000 series alloys have low crack sensitivity.
However, when the magnesium content reaches 2% in 5000 series alloys, the alloy becomes prone to cracking. Although increasing magnesium content improves welding performance, it decreases the ductility and corrosion resistance of the alloy.
On the other hand, 2000, 6000 and 7000 series alloys are more susceptible to hot cracking, have poor welding seam formation and have a significant reduction in aging hardness after welding.
Therefore, it is crucial to adopt appropriate technological measures for welding aluminum alloys and select the correct welding method and filler material to obtain good welded joints. Before welding, the material must undergo surface treatment, including removing oily dirt with organic solvents, immersing it in a NaOH solution, rinsing the surface with running water and carrying out a photochemical treatment.
The processed weldments must also undergo welding process experiments within 24 hours.
Application of aluminum alloy laser welding structure
Since the 1990s, advances in science and technology and the development of high-power, high-brightness lasers have led to the growth of laser welding technology and its increasing maturity in terms of integration, intelligence, flexibility and diversity. There has been increasing attention to the application of laser welding to aluminum alloy structures in various industries, both nationally and internationally.
Currently, some car manufacturers in China have already adopted laser welding technology in some of their new models. As laser welding technology for thick aluminum alloy plates continues to develop, it is expected to be used in the future for the structure of armored vehicles.
In order to achieve lightweight manufacturing, the application and research of laser welding on aluminum alloy sandwich structures is a current focus of research in the structural manufacturing of ships and high-speed trains.
Aluminum alloys are also an important metallic material for aerospace structures, which is why developed countries such as Japan, the United States, Great Britain and Germany place great emphasis on the research of aluminum alloy laser welding technology.
With the advancement of fiber laser welding technology, fiber laser welding and hybrid laser arc welding technology have become the focus of aluminum alloy welding technology in the field of aviation manufacturing in advanced countries , particularly for welding thick plates and welding dissimilar metals.
For example, the American NALI project is conducting research on fiber laser welding and hybrid laser arc welding technology for the combustion chamber structure of civil aircraft and JSF aircraft engines.
Features of aluminum alloy laser welding
Compared with conventional fusion welding, laser welding of aluminum alloy offers advantages such as concentrated heating, a large weld depth-to-width ratio, and reduced deformation of the welding structure. However, there are also some limitations, including:
- The small diameter of the laser focus spot requires high precision when welding and assembling the part. Generally, mounting clearance and misalignment must be less than 0.1 mm or 10% of the board thickness, making implementing complex three-dimensional weld structures a challenge.
- The high reflectivity of aluminum alloys to lasers, up to 90% at room temperature, means that laser deep penetration welding of aluminum alloys requires high power.
Research on laser welding of aluminum alloy sheets shows that:
Laser deep penetration welding of aluminum alloys depends on both laser power density and linear energy. These two factors jointly impact the behavior of the molten pool during the welding process and are reflected in the characteristics of the weld.
To optimize the full penetration welding process, the relationship of the back width of the characteristic weld formation parameters can be used to evaluate its effectiveness.
- Aluminum alloys have a low melting point and good liquid metal fluidity, which can result in strong vaporization of the metal under the influence of high-power lasers. The photoinduced metal vapor/plasma cloud that forms with the keyhole effect can affect the absorption of laser energy by the aluminum alloy during welding, causing instability in the deep penetration welding process and leading to defects such as porosity, collapse superficial and lower cut.
- Laser welding has high heating and cooling speeds, resulting in greater weld hardness compared to arc welding. However, the burning loss of alloy elements during laser welding of aluminum alloy may affect its strengthening effect, leading to a reduction in the strength of the aluminum alloy welded joint due to softening.
Therefore, the main challenge in laser welding of aluminum alloys is to control weld defects and improve the properties of welded joints.
The main problems in laser welding of aluminum alloys
Laser welding uses the laser as a high-density light source that offers rapid heating and instant solidification, with an aspect ratio of up to 12:1. However, due to the high reflectivity and good thermal conductivity of aluminum alloys, as well as the shielding effect of plasma, defects are likely to occur during the welding process.
The two most significant defects are pores and thermal cracks. The challenge in laser welding of aluminum alloy is to effectively improve the absorption of laser light by the material due to its strong reflection.
The laser welding process for aluminum alloys is more complex, and it is essential to improve and perfect it due to the characteristics of the aluminum alloy itself.
Laser absorption rate
The higher the laser absorption rate by the material, or the lower the heat transfer coefficient and temperature conductivity coefficient, the easier the laser energy is absorbed by the surface of the material, leading to a rapid increase in surface temperature and the melting or evaporation of the material.
Table 1 shows the reflectivity of various metals for lasers with different wavelengths.
Table 1 The reflectivity of metals for lasers of different wavelengths at room temperature (%)
λ/μm | Ag | Al | Ass | Cr | No | Steel |
---|---|---|---|---|---|---|
0.7 | 95 | 77 | 82 | 56 | 68 | 58 |
1.06 | 97 | 80 | 91 | 58 | 75 | 63 |
10.6 | 99 | 98 | 98 | 93 | 95 | 93 |
The reflectivity of different metals decreases as the wavelength becomes shorter, with the reflectivity of Ag, Al and Cu to laser light reaching 90% or more. This significantly increases the difficulty of laser processing.
At room temperature, the absorption rate of CO2 lasers by aluminum alloys is very low, with 98% of the laser energy being reflected by the aluminum alloy surface. The reflectivity of Nd:YAG lasers is also up to 80%.
It is clear that aluminum alloys have high reflectivity to laser light and a low absorption rate, due to their high density of free electrons. The strong vibration of light electromagnetic waves results in the generation of strong reflected waves and weaker transmitted waves. The reflected waves are not easily absorbed by the aluminum alloy surface, leading to its high reflectivity to lasers at room temperature.
Induction and stabilization of “small holes”
In the laser welding process, when the laser energy density exceeds 3.5*10 6 C/cm 2 , ions will be generated. This welding method is done through deep penetration welding and is based on the “small hole” effect. The presence of “small holes” significantly increases the absorption rate of the material by the laser and results in a good welding effect when welding welding at high energy density.
The main challenge in laser welding of aluminum alloys is to induce and maintain the stability of small holes, which is due to both the material properties of aluminum alloys and the optical properties of the laser beam. As mentioned previously, aluminum reflects 80% of energy at room temperature and has good thermal conductivity, requiring a large laser energy density threshold to produce “small holes”.
Once the input power exceeds this value, the transmission of laser energy to the material is no longer limited by heat conduction, and welding is carried out by deep penetration. Laser radiation causes strong evaporation of the base metal and forms an evaporation groove. The laser beam penetrates the material through this groove, resulting in a marked increase in weld depth and efficiency.
For highly reflective materials such as aluminum alloys and copper alloys, a large power density is required during welding. This imposes certain requirements on the selection of welding models and collimating and focusing lenses.
Mechanical properties of welds
Refining strengthening, solid solution strengthening, and aging precipitation strengthening are three different ways to strengthen aluminum alloys. Despite these mechanisms, the large amount of evaporation of low-melting alloy elements such as Mg and Zn during laser welding causes the weld to sink and reduce its hardness and strength.
During the rapid solidification process, the transformation of the fine-grained reinforced structure into a cast structure results in a decrease in hardness and strength. Furthermore, the presence of cracks and pores in the weld reduces tensile strength.
In conclusion, joint softening is another challenge in laser welding of aluminum alloys.
Stomach
There are two main types of pores in the laser welding process of aluminum alloys: hydrogen gas pores and keyhole collapse pores.
( 1) Hydrogen pores: Aluminum alloys form an oxide film on their surface at high temperatures, which easily absorbs moisture from the environment. When heated by a laser, water decomposes into hydrogen, and the solubility of hydrogen in liquid aluminum is about 20 times greater than that in solid aluminum. During rapid solidification of the alloy, the solubility of hydrogen decreases drastically as it passes from liquid aluminum to the solid state. If the excess hydrogen in liquid aluminum does not rise and overflow smoothly, it will form hydrogen pores. These pores are generally regular in shape and larger in size than the dendrites, and the solidification patterns of the dendrites can be seen on the inner surface.
(2) Keyhole collapse: The welding hole is in equilibrium with its own gravity and atmospheric pressure. Once this balance is disturbed, the liquid metal in the molten pool is unable to flow and fill over time, resulting in uneven holes. Studies have found that the magnesium content of the inner hole wall is about 4 times that of the weld vicinity. Because the cooling rate of laser welding is very fast, the problem of hydrogen gas pores is more serious, and there are more holes caused by the collapse of small holes in laser welding.
Thermal cracking
Aluminum alloy is a common eutectic alloy that is prone to hot cracking during welding, including weld crystallization cracks and HAZ (heat affected zone) liquefaction cracks. Typically, crystallization cracks appear in the weld zone, while liquefaction cracks appear near the joint. Among aluminum alloys, 6000 series Al-Mg-Si alloys are particularly susceptible to cracking.
The base metal is subjected to rapid heating and cooling, which can lead to the instantaneous solidification and crystallization process. The large degree of subcooling during this process causes the crystal grains to grow perpendicular to the center of the weld, forming low melting point eutectic compounds such as Al-Si or Mg-Si, Al-Mg2Si and others. This weakens the bonding strength of the crystalline plane, making it more prone to cracking under thermal stress.
In the aluminum alloy welding process, low boiling point elements such as Mg, Zn, Mn and Si are easily evaporated and burned. The slower the welding speed, the more severe the burn, which changes the chemical composition of the weld metal. Due to the segregation of components in the weld zone, eutectic segregation and grain boundary melting occurs, leading to liquefaction cracks at the grain boundaries under stress, reducing the performance of the welded joint.
Aluminum alloy laser welding process
To achieve success in laser welding of aluminum alloys and solve the problems mentioned above, several approaches are commonly adopted.
Gas protection device
One of the most important factors affecting the loss of low-melting point elements in aluminum alloys during welding is the pressure of the gas expelled from the nozzle. To mitigate this problem, the nozzle diameter can be reduced and the gas pressure and flow rate can be increased. This will reduce the burning loss of elements such as Mg and Zn during the welding process and also increase penetration.
There are two blowing methods available: direct blowing and side blowing. Furthermore, it is possible to blast welding up and down simultaneously. The choice of blowing method should be determined based on the specific circumstances during welding.
Surface treatment
Aluminum alloy has a strong reaction to laser energy. Proper surface preparation of aluminum alloy, such as anodic oxidation, electrolytic polishing, sandblasting, etc., can greatly improve the beam energy absorption on the surface.
Research has shown that removing the oxide film from aluminum alloys increases their tendency to form crystallization cracks. To avoid damaging the surface condition of the aluminum alloy and at the same time simplify the laser welding process, the surface temperature of the workpiece can be increased before welding, which will increase the laser absorption rate of the material.
Laser Parameters
Laser welding is divided into two categories: pulsed lasers and continuous lasers. Pulsed lasers with a wavelength of 1064 nm have a highly concentrated beam, and the energy of the single-point pulse is greater than that of continuous lasers. However, the energy of pulsed lasers is generally limited, making them more suitable for welding thin-walled materials.
Pulse mode welding
When performing laser welding, it is important to select the appropriate welding waveform. Common pulse waveforms include square wave, spike wave and double peak wave. Typically, pulse waves last in the range of milliseconds. During a laser pulse, the reflectivity of the metal changes drastically. Aluminum alloys have high light reflectivity, which means that 60-98% of the laser energy reaching the surface of the material can be lost due to reflection. This reflectivity changes with surface temperature.
Steep wave and double peak wave are the best options for aluminum alloy welding as the rising phase of the waveform provides more energy to melt the aluminum alloy. Once a “small hole” is formed in the workpiece, the absorption rate of the liquid metal by the laser increases rapidly during deep penetration welding. At this point, it is important to quickly reduce laser power and perform welding at low power to avoid spatter.
The slower part of the welding waveform has a longer pulse width, which effectively reduces the formation of pores and cracks. This waveform causes the solder to melt and solidify repeatedly, reducing the rate of solidification of the molten pool. The waveform can be adjusted as needed when welding different types of samples.
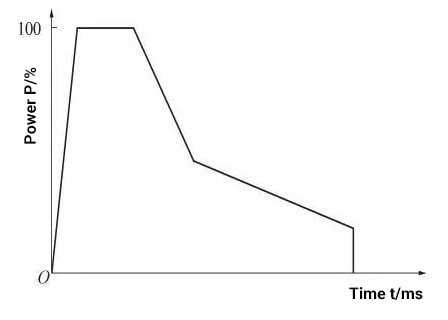
Figure 1 Aluminum alloy welding pulse waveform
Selecting the appropriate amount of blur can also minimize pore formation. The change in defocus has a significant impact on weld surface formation and penetration. Negative defocus can increase penetration, while positive defocus in pulse welding can make the weld surface smoother and more visually appealing.
Due to the high reflectivity of aluminum alloys to laser energy, the welding head is generally tilted to prevent the laser beam from being reflected vertically and damaging the laser focusing lens. The solder joint diameter and effective bonding surface increase as the laser inclination angle increases. The largest solder joint and effective bonding surface are achieved when the laser tilt angle is 40°. However, the welding spot penetration and effective penetration decrease with increasing laser inclination angle, and when it exceeds 60°, the effective welding penetration decreases to zero. Tilting the welding head at a certain angle can increase the penetration depth and weld width.
Furthermore, it is important to note that the faster the welding speed, the greater the risk of cracking. This is because a fast welding speed leads to a large degree of subcooling, causing the grains in the weld zone to be refined and a large number of “crystal beams” to grow in the same direction, which increases the probability of formation of cracks in the crystal. plane between these beam crystals. If the welding speed is too fast, the welding penetration depth will be relatively shallow.
Continuous mode welding
Traditional laser welding can result in embrittlement or cracking. In contrast, continuous laser welding does not have the same sudden cooling and heating process as pulsed laser welding, leading to fewer cracks during the welding process. Additionally, fiber laser welding of most aluminum alloys results in greater toughness after welding and reduces the risk of brittleness.
Pulsed laser welding is suitable for industrial pure aluminum welding, with little risk of cracking after welding. However, some industries may require post-welding surface polishing, and pulsed laser welding can cause dents and increase the amount of polishing required, leading to an increase in processing time and production costs. Continuous lasers can solve these problems.
As shown in Figure 2, the comparison of the battery shell welding seam after pulsed laser welding and continuous laser welding demonstrates the advantages of continuous laser welding. Impulse welding joints are irregular and have recessed and dented surfaces, with lots of spatter and lower post-welding resistance. In contrast, continuous laser welding results in a smooth and uniform weld seam surface, free from defects and spatter, with no cracks found in the weld seam.
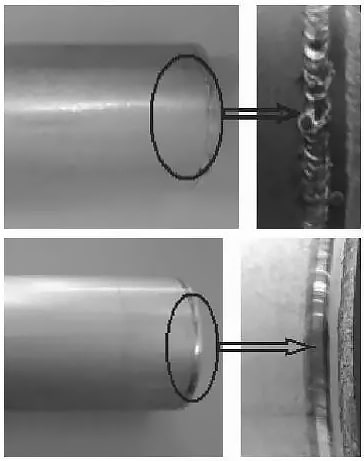
Figure 2 Pulsed and continuous welding of Al-Mn alloy
Arc craters are a common occurrence during argon arc welding, and the same can occur during laser welding. To minimize the appearance of small craters, a slow rise and fall stage can be set on the waveform during welding, and the welding speed can be increased as needed.
Continuous laser welding has numerous advantages when welding aluminum alloys. Compared to traditional welding methods, continuous laser welding is more efficient and eliminates the need for wire stuffing. Compared with pulsed laser welding, continuous laser welding eliminates defects such as cracks, pores and spatter and ensures that the aluminum alloy has good mechanical properties after welding. Furthermore, there will be no dents after welding and the amount of polishing and grinding required will be reduced, saving production costs.
However, it is important to note that continuous lasers have a relatively small spot size, so the part assembly accuracy must be high.
Introducing Alloy Elements
Thermal crack prevention is a critical technology for laser welding of aluminum alloys, especially for the 6000 series alloys, which are highly sensitive to cracking. If the ω(Mg2Si) content reaches 1%, hot cracking is likely to occur. To reduce the risk of cracking, suitable alloying elements can be added to adjust the chemical composition of the molten pool, such as adding Al-Si or Al-Mg-Si powder.
In addition, wire feeding can improve the welding effect and produce a uniform weld seam with higher hardness. The introduction of filler material increases the Mg and Si content in the dendrite in the fusion zone, leading to an increase in joint strength due to the strengthening effect of the solid solution β”.
Typically, 6063 and 6082 aluminum alloys are filled with Al-5Si and Al-7Si welding wires, while 6013 and 6056 plates are welded with CO2 and Nd:YAG, respectively, and filled with Al-12Si welding wires. .
Other process methods
Aiming for stability and quality in laser welding of aluminum alloys.
The current focus of research in laser welding of aluminum alloys is the use of a composite process that combines the high energy density of laser beams with the wide heating range of arcs, utilizing the strengths of both heat sources and improving its high energy density and stability characteristics. bows.
For materials with high reflectivity such as aluminum alloys, hybrid laser welding can preheat or melt the surface of the material using arc energy, significantly improving the absorption of laser energy by the aluminum alloy.
Shida et al. successfully used a 10 kW CO2 laser in conjunction with TIG and MIG arcs to weld aluminum alloys. The introduction of arcs improved the laser energy utilization rate and increased the weld penetration rate by 5-20%. The result was a smooth, well-formed weld surface.
Hybrid laser welding increases the size of the molten pool and modifies the flow conditions of the material in the molten state through the coupling of laser beams and arcs, which is beneficial in eliminating pores.
Eliminating air holes when welding aluminum alloys can also be achieved through double beam welding. A 6 kW continuous fiber laser was used for dual-beam butt welding of 5052 aluminum alloy, and the effects of two-beam parallel and serial welding modes and different welding speeds on seam morphology and structure were studied. The research found that double-beam parallel welding resulted in large holes in the welds, while series welding of aluminum alloys produced good pore-free weld formation.
Aluminum alloy laser welding defect control technology
Under the influence of high-power lasers, the main defects in laser deep penetration welding of aluminum alloys are porosity, surface collapse and undercut. Surface collapse and undercut defects can be improved through laser wire fill welding or hybrid laser arc welding. However, controlling porosity defects is challenging.
Research has shown that there are two types of characteristic pores in laser deep penetration welding of aluminum alloys. One type is metallurgical pores, caused by material contamination or air intrusion during the welding process, similar to arc fusion welding. The other type is process porosity, caused by the unstable fluctuation of small holes inherent in the laser deep penetration welding process.
During laser deep penetration welding, the small hole generally lags behind the beam movement due to the viscosity of liquid metal, and its diameter and depth fluctuate under the influence of plasma/metal vapor. As the beam moves and the molten pool metal flows, the incomplete deep penetration weldment is closed due to the flow of the molten pool metal, causing bubbles to appear at the tip of the small hole. In deep penetration and full penetration welding, bubbles appear at the waist of the small hole in the middle.
These bubbles migrate and roll with the flow of liquid metal, escaping the surface of the molten pool or being pushed back into the small hole. When the bubbles are solidified by the weld pool and captured by the metal front, they become weld pores.
Metallurgical pores can be controlled through pre-welding surface treatment and adequate gas shielding during the welding process. The key to controlling process pores is to ensure stability during the laser deep penetration welding process.
According to research on domestic laser welding technology, the control of air holes in laser deep penetration welding of aluminum alloy requires consideration of all links, including before welding, the welding process and post treatment. -welding. This can be achieved through the following new processes and technologies.
Pre-welding treatment method
Pre-welding surface treatment is an effective method to control metallurgical pores in laser welding of aluminum alloys. Common surface treatment methods include physical mechanical cleaning and chemical cleaning. Recently, laser impact cleaning has also emerged, which further improves the automation of laser welding.
Parameter Stability Optimization Control
Aluminum alloy laser welding process parameters typically include laser power, defocus, welding speed, and shielding gas composition and flow. These parameters not only affect the protective effect of the welding area, but also affect the stability of the laser deep penetration welding process, which in turn affects the porosity of the weld.
Through laser deep penetration welding of aluminum alloy sheets, it was discovered that the stability of penetration into small holes influences the stability of the molten pool, which impacts weld formation and results in porosity defects. Furthermore, the stability of laser deep penetration welding is related to the correspondence between laser power density and linear energy.
Therefore, determining reasonable process parameters for stable weld formation is an effective method for controlling the porosity of laser welding of aluminum alloys. The research results on full penetration stable weld formation characteristics showed that the relationship between the weld back width and the weld surface width (proportion of the back weld width) can be used to evaluate the weld formation and the stability of aluminum alloy sheets.
By properly matching the laser power density and line energy during laser welding of thin plates, a certain weld back width ratio can be guaranteed, effectively controlling the porosity of the weld.
Dual Spot Laser Welding
Dual spot laser welding refers to a welding process where two focused laser beams act simultaneously on the same weld pool. In laser deep penetration welding, one of the main causes of weld porosity is gas closure in the small orifice of the weld pool.
When using double-spot laser welding, the opening of the small hole is increased due to the influence of two light sources, facilitating the escape of internal metal vapor and improving the stability of the small hole, thereby reducing the porosity of the weld.
Studies on laser welding of A356, AA5083, 2024 and 5A90 aluminum alloys have shown that double-spot laser welding can significantly reduce weld porosity.
Hybrid laser arc welding
Hybrid laser arc welding is a welding method in which both the laser and the arc influence the same molten pool. Typically, the laser is the main heat source, and the interaction between the laser and the arc increases the penetration and welding speed of laser welding while reducing the accuracy of welding assembly.
The use of the filler wire helps control the microstructure and properties of the welded joints, and the auxiliary effect of the arc improves the stability of the laser welding holes, contributing to the reduction of weld porosity.
In the hybrid laser arc welding process, the arc affects the metal vapor/plasma cloud generated by the laser process, promoting the absorption of laser energy and the stability of small holes.
Studies on hybrid laser arc welding of aluminum alloys have confirmed its effectiveness in reducing weld porosity.
fiber laser welding
The keyhole effect in laser deep penetration welding occurs due to the strong vaporization of the metal under the influence of the laser. The strength of metal vaporization is closely linked to laser power density and beam quality, affecting both laser welding penetration and keyhole stability.
Seiji et al. studied the high power fiber laser on SUS304 stainless steel and showed that:
During high-speed welding, the molten pool elongates, spatter is controlled, the small hole fluctuations are stable, and there are no bubbles at the tip of the small hole. When a fiber laser is used for high-speed welding of titanium alloys and aluminum alloys, a poreless weld can also be produced.
Research on shielding gas control technology for titanium alloy fiber laser welding by Allen et al. this is how it is:
By controlling the position of the welding shielding gas, it is possible to avoid gas engulfment, shorten the small hole closing time, stabilize the small welding hole, and change the solidification behavior of the molten pool, thereby reducing the porosity of the weld. .
Pulsed laser welding
Compared to continuous laser welding, the pulsed mode of the laser output can improve the periodic and constant flow of the molten pool, which helps release bubbles and reduce the porosity of the weld.
TY Kuo and SL Jeng investigated the impact of YAG laser welding power output mode on the porosity and characteristics of welds made of SUS 304L stainless steel and Inconel 690 superalloy.
The results indicate that for square wave pulsed laser welding, as the base power increases to 1700W, the weld porosity decreases with increasing pulse amplitude ΔP. Specifically, the porosity of stainless steel decreases from 2.1% to 0.5%, and that of superalloy decreases from 7.1% to 0.5%.
Post-weld composite treatment technology
In practical engineering applications, despite rigorous surface treatment before welding and a stable welding process, porosity is still a common problem in laser welding of aluminum alloys.
Therefore, post-weld treatment methods to eliminate porosity are crucial.
Currently, the main method used is modified welding.
One such method to eliminate internal and shrinkage porosity in aluminum alloy castings is hot isostatic pressing technology.
By combining this with stress heat treatment after laser welding of aluminum alloy, a composite process of hot isostatic pressing and heat treatment of aluminum alloy laser welding components is formed. This not only eliminates weld porosity but also improves joint performance.
Conclusion
The application of high-power laser welding to aluminum alloys still presents many challenges due to its unique characteristics.
One of the main challenges is to control weld porosity defects and improve welding quality.
To improve the stability of the welding process and control porosity in laser welding of aluminum alloys, a comprehensive approach that considers all aspects from pre-welding to the welding process and post-welding treatment is essential.
To meet this challenge, several new technologies and processes have been developed, including laser cleaning before welding, optimization of welding process parameters by controlling the back width ratio, dual beam laser welding, hybrid arc-laser welding, pulsed laser welding and fiber optic laser. Welding.