“CNC machining” refers to the use of numerical control machining tools.
Because it is controlled by computer programming, CNC machining offers several benefits, such as consistent quality, high precision, high repeat accuracy, the ability to machine complex surfaces, and greater efficiency.
However, it is worth noting that the final quality of the machined product can be greatly impacted by human factors and operator experience during the actual machining process.
Let's now take a look at ten valuable machining tips, summarized by a CNC machine operator with over a decade of experience in the field.
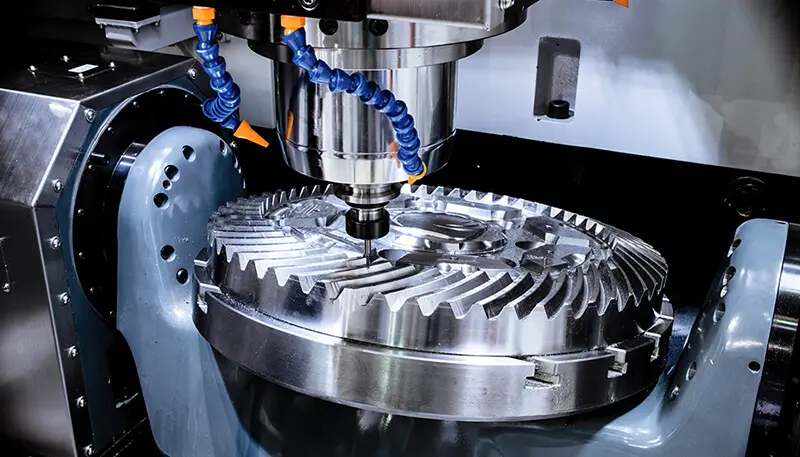
1 . How to divide CNC machining processes?
The division of CNC machining processes can generally be carried out using the following methods:
Tool-centric classification method
The tool-centric classification method consists of dividing processes based on the tools used and using the same tool to machine all parts that can be completed. The second and third knives are used to complete other pieces that can finish. This approach reduces the number of tool changes, minimizes downtime and reduces unnecessary positioning errors.
Sorting by processing position
For parts with many CNC processing steps, the processing part can be divided into several sections based on its structural characteristics, such as internal shape, external shape, curved or flat surface, etc. followed by holes; simple geometries are machined before complex ones; and low-precision parts are processed before those with high-precision requirements.
Classification by rough and fine CNC machining
For parts that are prone to deformation during rough and fine CNC machining, the shape needs to be calibrated due to possible deformation after rough machining. Therefore, the processes are generally separated for rough machining and fine machining.
In conclusion, when dividing the process, it is important to consider the structure and manufacturability of the parts, the function of the machine tool, the amount of NC machining of the parts, the installation times and the unit production organization. In addition, the principle of process concentration or dispersion should be determined based on the actual situation, but it should be reasonable.
two . What principles should be followed in arranging the CNC machining sequence?
The machining sequence must be planned based on the structure and condition of the parts, as well as positioning and clamping requirements, with a focus on avoiding damage to the rigidity of the part. The following principles must be followed when organizing the sequence:
- The CNC processing of the previous process must not interfere with the positioning and fixing of the following process. The general interleaved process of machine tool processing must also be considered.
- Machining of the internal shape and cavity must be carried out first, followed by machining of the contour.
- CNC machining processes with the same positioning and clamping mode or the same tool should be grouped together to reduce the number of repeated positioning, tool changes and press plate movements.
- When multiple processes are run in the same configuration, the process that has the least impact on part stiffness should be run first.
3 . What aspects should we pay attention to when determining how to fix the part?
When determining the positioning reference point and fixing scheme, the following four points must be taken into consideration:
- Objective to standardize the benchmark used in design, processing and programming calculations.
- Minimize the number of clamping times as much as possible and try to carry out CNC processing on all surfaces to be machined after a single positioning.
- Avoid using manual tuning schemes.
- The clamping device must be designed to be openable, and its positioning and clamping mechanism must not interfere with the movement of the tool during CNC processing (to avoid collisions). In these cases, fixation can be achieved using a vise or by adding a base plate and extracting screws.
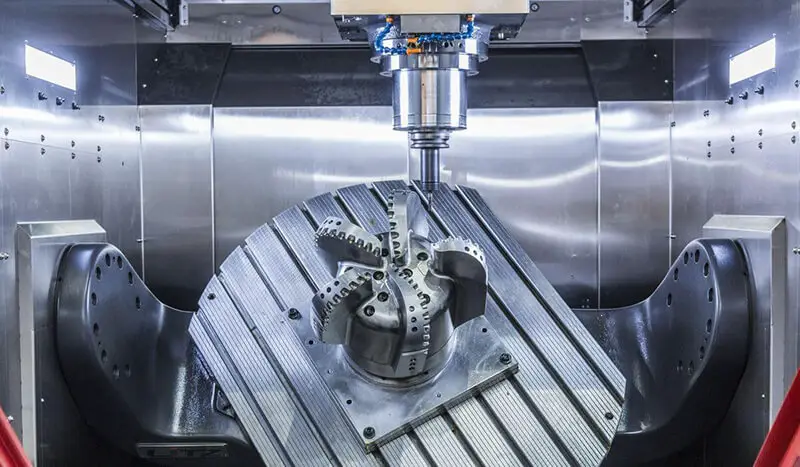
4. How to determine the reasonableness of the tool set point? What is the relationship between the part coordinate system and the programming coordinate system?
The tool set point can be established on the machined part, but it is important to note that the tool set point must be a reference position or the final product. In some cases, after the first machining process, the tool set point may be damaged, making it difficult to locate the tool set point in subsequent processes.
To avoid this, care must be taken to define a relative tool configuration position in the first process that has a consistent relationship with a reference benchmark. In this way, the original tool setting point can be identified based on the relative relationship between them.
This relative tool adjustment position is generally located on the machine tool bench or fixture, and selection should take into account the following principles:
- Easy alignment
- Convenient programming
- Minimum tool configuration error
- Facilitates inspection during machining and allows for easy checking.
The starting point of the part coordinate system is established by the operator. Once the workpiece is securely clamped, adjusting the tool will set its position. This defines the distance between the workpiece and the machine tool zero point.
Once the part coordinate system is established, it normally remains unchanged. To ensure accurate machining, it is important that the workpiece coordinate system and the programming coordinate system are synchronized, which means that they are consistent with each other during the machining process.
5 . How to select the cutting route?
Tool path refers to the path and direction of movement of the tool relative to the workpiece during NC machining. Cutting path selection is crucial as it affects the accuracy and surface quality of machined parts.
The following factors are taken into consideration when determining the cutting path:
- Meeting the machining precision requirements of parts.
- Facilitating numerical calculation and reducing programming effort.
- Find the shortest NC processing route and reduce tool idle time to improve NC processing efficiency.
- Minimizing the number of segments.
- Ensure the required surface roughness of the workpiece contour after NC machining and ensure that the final contour is continuously processed with the last tool.
- Careful consideration of the forward and backward path (entry and exit) of the tool to minimize knife marks caused by sudden changes in cutting force and to avoid scratching the workpiece when cutting vertically on the contour surface.
6 . How to monitor and adjust during CNC machining?
Once the part is properly aligned and the program is fully debugged, it can proceed to the automatic machining stage.
During this step, the operator must closely monitor the cutting process to ensure that part quality is not compromised and to avoid accidents that may occur as a result of abnormal cuts.
The following aspects must be taken into account when monitoring the cutting process:
(1) During the rough machining phase, the focus of monitoring the machining process is mainly on the rapid removal of excess material from the workpiece surface.
In machine tool operation, the cutting process is carried out automatically according to the predetermined cutting path and cutting parameters set by the operator.
The operator must closely monitor changes in cutting load throughout the process by checking the cutting load chart. Based on the rolling force of the tool, the cutting parameters must be adjusted to maximize the efficiency of the machine tool.
(2) Monitoring the cutting sound during the cutting process
During the automatic cutting process, when the cutting process starts, the sound of the tool cutting the workpiece is generally stable, continuous and light.
At this stage, the movement of the machine tool is stable. However, as the cutting process progresses, problems such as hard spots on the workpiece, tool wear, or improper tool clamping can make the cutting process unstable.
Indicators of instability include changes in cutting sound, tool-workpiece collision, and machine tool vibration. In these cases, the parameters and cutting conditions must be adjusted immediately.
If the adjustment does not produce the desired result, the machine tool must be stopped to inspect the condition of the tools and parts.
(3) Finishing process monitoring to ensure part machining size and surface quality
During the finishing process, the cutting speed is high and the feed is large. Attention should be paid to the impact of chip accumulation on the machined surface.
For cavities that are being machined, it is important to be aware of excessive cutting and tool wear on corners.
To resolve these issues, the following steps can be taken:
- Make sure the machining surface is always cool by adjusting the position of the cutting fluid spray.
- Maintain machined surface quality by adjusting cutting parameters to avoid changes in quality.
If these adjustments are not effective, it may be necessary to stop the machine and evaluate the reasonableness of the original program.
It is important to pay attention to the position of the tool when pausing inspection or stopping the machine. If the cutting tool stops in the middle of the cutting process, the sudden stop of the spindle may result in tool marks on the workpiece surface.
In general, it is recommended to turn off the machine when the tool is no longer in a cutting state.
(4) Tool monitoring: tool quality affects the machining quality of the workpiece
Tool quality plays an important role in determining the machining quality of the part.
During the automatic machining and cutting process, normal wear and any abnormal damage to the tool can be detected through sound monitoring, cutting time control, inspections during the cutting process and analysis of the part surface.
To ensure that the machining quality meets the required standards, cutting tools must be managed in a timely manner to avoid any processing quality problems caused by improper tool handling.
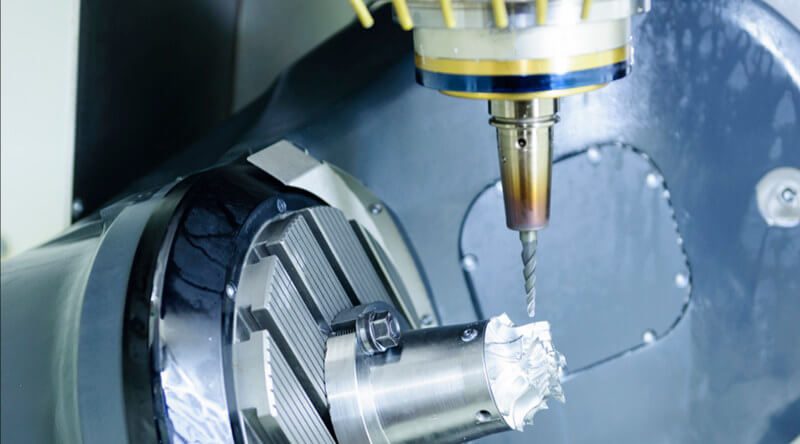
7 . How to reasonably select machining tools? How many factors are there in cutting parameters? How many types of cutting tools are there? How to determine tool speed, cutting speed and cutting width?
(1) For flat milling, it is recommended to use an unground carbide end mill or end mill. In general milling, it is best to use the second tool feed whenever possible. For the first tool feed, it is recommended to use an end mill for rough milling and continuous feed along the surface of the part. The recommended feed width of each tool should be between 60% to 75% of the tool diameter.
(2) End mills and end mills with carbide inserts are mainly used to process bosses, grooves and box mouth surfaces.
(3) Ball cutters and round cutters (also known as round tip cutters) are commonly used to process curved surfaces and contours of variable angles. Ball milling cutters are mainly used for semi-finishing and finishing, while carbide circular milling cutters are mainly used for roughing.
8 . What is the function of the processing program spreadsheet? What should be included in the processing procedure sheet?
(1) The machining program list is an essential component of NC machining process design. It serves as a procedure that must be followed and executed by the operator. The machining program list provides a detailed description of the machining program and is used to clarify the program contents, the clamping and positioning method, and the tools selected for each machining program, among other things.
(2) The machining program file must include the following information: name of the drawing and programming file, name of the part, sketch of the clamping method, name of the program, tools used in each program, maximum value of cutting depth, the nature of the machining (such as roughing or finishing) and the theoretical machining time.
9 . What preparations should be made before programming?
Before programming, it is important to consider the following after determining the processing technology:
- Method of fixing the part;
- The size of the blank embryo – this will determine the processing range or whether multiple fixation is required;
- The material of the part – to select the appropriate tool for machining;
- Tools available in stock – to avoid modifications to the program due to the unavailability of a tool during machining. If a specific tool is needed, it must be prepared in advance.
10 . What are the principles for defining safety height in programming?
The principle of adjusting the safety height is to ensure that it is generally higher than the highest surface of the workpiece or to set the programming zero point to the highest surface. This helps minimize the risk of tool collision.