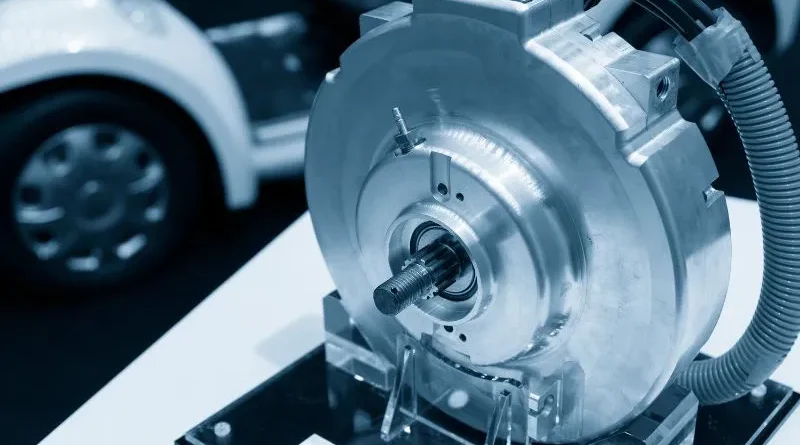
Electrical braking is crucial for the efficient control and stopping of DC motors, especially when rapid deceleration is required. While your existing article provides valuable information about the fundamentals of electric braking, this updated version will delve deeper into the topic and explore advanced concepts, benefits, and applications. To improve clarity, we also provide a structured overview with headings, subheadings, bullet points, and frequently asked questions.
Understanding Electric Braking
Electric braking is a modern and efficient alternative to traditional mechanical braking methods. Although both approaches aim to stop DC motors, electric braking offers distinct advantages, such as: B. less wear on mechanical components and faster braking times. By converting kinetic energy into electrical energy, electric braking systems allow precise control of deceleration and are therefore invaluable for applications where safety, efficiency and maintenance savings are of paramount importance.
Electric braking vs. mechanical braking
Electric braking is an alternative to mechanical braking, which relies on friction between moving parts and brake shoes. Both methods achieve the same goal of stopping a DC motor, but electric braking offers significant advantages:
- Reduced wear: Electric braking minimizes wear on mechanical brakes, resulting in longer component life and lower maintenance costs.
- Shorter stopping time: The electric brake guarantees a high braking delay and therefore faster braking times, which can be crucial in emergencies.
Electric braking methods
Electrical braking of DC motors includes several methods, each suited to specific applications. The following three methods are commonly used for DC shunt motors and DC series motors:
Dynamic braking or rheostatic braking
- principle : During dynamic braking, the armature of the running motor is disconnected from the power supply and connected via an adjustable resistor. The field winding remains connected to the power source. As the armature slows down, it rotates in a strong magnetic field and acts as a generator, sending a high current through the resistor. This rapid dissipation of energy in the form of heat causes the engine to stop immediately.
- Braking torque control : Braking torque can be controlled by varying the adjustable resistance (R). By reducing the resistance value, the motor speed is reduced and the braking torque can be precisely controlled. Lower engine speed results in lower braking torque and eventually stops the engine due to friction.
- Applications : Dynamic braking is widely used to control hoists, elevators, and in scenarios where engines need to be repeatedly stopped, started, and reversed.
Plug in
- principle : Plugging is a braking method that reverses the direction of the armature by changing the polarity of the supply voltage while the motor is still running. This abrupt reversal of movement creates a counter torque that quickly decelerates the engine.
- Braking torque control : The intensity of clogging can be controlled by adjusting the voltage applied during reversal. This method is particularly effective in applications where an engine needs to be stopped quickly.
- Forms : Obstructions are commonly used in conveying systems where precise control of material movement is important and in industrial machines that need to be stopped quickly.
Regenerative braking
- principle : Regenerative braking is a sophisticated method that converts the motor's kinetic energy back into electrical energy, which can be dissipated as heat in a resistor or returned to the power source. This process helps to recover part of the energy and reduce electricity consumption.
- Braking torque control : Regenerative braking allows more precise control of braking torque by adjusting the energy dissipation or regeneration rate. It is often used in energy efficiency applications.
- Applications : Regenerative braking is often used in electric vehicles, where it helps extend battery life by recovering energy during braking, as well as in renewable energy systems, where excess energy can be stored or exported to the grid.
Relationship between braking torque and engine speed
Let's take a closer look at the mathematical relationship between braking torque (TB) and motor speed (N) for a shunt motor:
Armature current I A =E b / (R+R A )
= (K 1 .NΦ) / (R+R A ) (∵E b ∝N)
Braking torque T b =K 2 IaΦ
=K 2 Φ(K 1 .NΦ /R+R A )
=K 3 No 2 Where,
(where K2 and K3 are constants and Φ is constant for a shunt motor)
Hence the braking torque T b ∝N
This equation shows that the braking torque (TB) is directly proportional to the engine speed (N). This means that as engine speed decreases, braking torque also increases. This relationship is important to understand how to effectively control the stalling of a DC motor.
Advantages of electric brake
- Energy efficiency: Electric braking methods, such as recuperative braking, can recover and reuse energy, making systems more energy efficient and reducing operating costs.
- Reduced maintenance effort: The electric brake reduces wear on mechanical brakes, resulting in longer component life and less maintenance.
- Enhanced safety: Fast braking times through electric braking systems increase safety in critical applications and emergencies.
Electric brake applications
Electric braking plays a crucial role in several industries and applications:
- Automotive industry: Regenerative braking is widely used in electric and hybrid vehicles to improve fuel efficiency and extend battery life.
- Production: Electric brakes are used in transportation systems, industrial machines and robotics for precise control and safety.
- Transport: Trains, trams and elevators use electric brakes for safe and efficient stopping.
- Renewable energy: Wind turbines and hydroelectric generators use recovery to control energy production and grid stability.
Common questions
1. What is the difference between electric and mechanical brakes?
During electrical braking, kinetic energy is converted into electrical energy, which is then dissipated. This reduces wear on mechanical components and results in faster braking times.
2. What are the main electrical braking methods for DC motors?
The most important methods include dynamic braking (rheostatic braking), clogging and regenerative braking.
3. What is regenerative braking and where is it commonly used?
During regenerative braking, kinetic energy is converted into electrical energy. This process is commonly used in electric vehicles, renewable energy systems and industrial applications.
4. How to control the braking torque of a DC motor using electrical braking methods?
Depending on the method, braking torque can be controlled by adjusting parameters such as resistance, voltage or energy dissipation rate.
5. Are there any disadvantages to electric braking?
While electric braking offers numerous benefits, it can require additional components and electronics, which can increase the initial cost. To obtain maximum benefit, careful system design is essential.
Conclusion
Electric braking is a versatile and efficient way to control and stop DC motors in various applications. Understanding the principles and methods of electrical braking can improve safety and energy efficiency and reduce maintenance costs. Whether in the automotive industry, industry, transport or renewable energy, electric braking is fundamental in modern technology and therefore an important topic for engineers and enthusiasts.