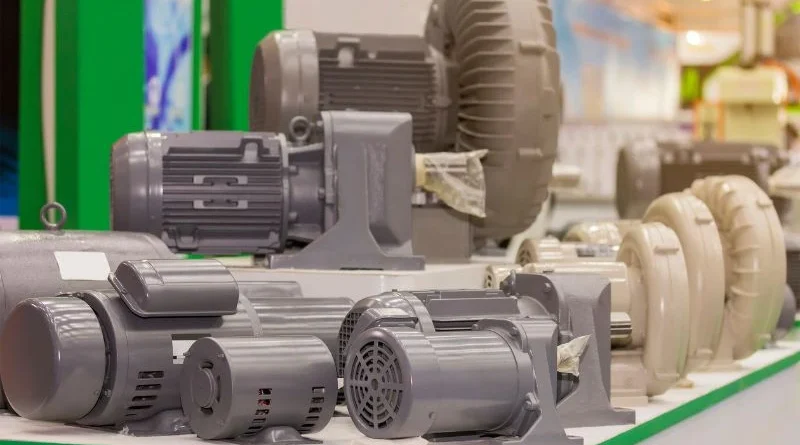
Understanding the maze of electric motors can often be like deciphering a complex algorithm. However, mastering this knowledge opens up a world of possibilities. Whether you're an aspiring engineer, a seasoned technician, or simply a technology enthusiast who wants to understand the machines that power our world, this blog post is your Rosetta Stone. In “A Comprehensive Guide to Types of Electric Motors: Classification and Applications,” we will demystify this topic and navigate AC induction motors, brushed DC motors, brushless DC motors, and more – each with unique features and functions. So grab your gears and schematics as we electrify your knowledge about these ubiquitous machines!
Various electric motors are used today, including brushless AC motors, brushed DC motors, brushless DC motors, direct drive motors, linear motors, servo motors, and stepper motors. Each type has unique characteristics and ideal use cases, depending on your system requirements and performance goals. It is important to carefully consider these factors before selecting a motor for a motion control system.
Understanding Electric Motors
Electric motors are devices that convert electrical energy into mechanical energy. They are used in many different applications, from powering industrial machines to powering electric vehicles. Understanding the fundamentals of electric motors is important to understand their classification and applications.
Electric motors essentially consist of two main components: the stator and the rotor. The stator is the stationary part of the motor that contains coils or magnets, while the rotor is the rotating component that interacts with the stator to produce movement.
Different types of electric motors are used today, each with its own characteristics and applications. Some common types are brushless AC motors, brushed DC motors, brushless DC motors, direct drive motors, linear motors, servo motors, and stepper motors.
To better understand this diversity, think of electric motors as a diverse family. Each member has a unique personality, talent and purpose.
Each type of electric motor works according to different principles and technologies. For example:
- Brushless AC motors create a rotating magnetic field in the stator through induction and rely on permanent electromagnets.
- Brushed DC motors use the orientation of brushes on the stator or rotor rod segments to determine current flow. The commutator is important for these engines.
- Brushless DC motors are designed to achieve high performance in a smaller space. They use an embedded controller rather than a slip ring or switch.
- Direct drive motors are highly efficient alternatives to servo motors because they do not require gears.
- Linear motors have an unwound stator and a motor that produces linear force along the length of the device. They are faster and more accurate than rotary engines.
- Servomotors are coupled with feedback sensors for precise positioning and are commonly used in robotics.
- Stepper motors use externally controlled magnets to move the internal rotor in fixed increments.
When selecting a motor for a motion control system, it is important to consider the specific requirements and performance goals of the system. Factors such as torque, speed, efficiency and control methods must be taken into consideration.
Now that we have a good understanding of electric motors in general, let's focus on one specific type: permanent magnet motors.
- Electric motors are important devices that convert electrical energy into mechanical energy for various applications. They consist of two main components: the stator and the rotor. There are several types of electric motors available today, each with unique features and applications. When selecting a motor for a motion control system, factors such as torque, speed, efficiency, and control methods must be considered. Permanent magnet motors are a type that can be used in a variety of applications.
Permanent magnet motors
Permanent magnet motors are electric motors that use permanent magnets in the stator or rotor to create the required magnetic field. These magnets can be made from neodymium iron boron (NdFeB) or samarium cobalt (SmCo).
One of the main advantages of permanent magnet motors is their high efficiency, as there are no losses in the generation of the magnetic field through electromagnets. The strong magnetic field created by the permanent magnets allows for strong and efficient operation of the motor.
These motors are widely used in a variety of applications, from consumer electronics such as computers and household appliances to industrial machinery and electric vehicles. For example, many electric cars, like Tesla's, use permanent magnet motors because of their power and efficiency.
Imagine driving an electric car with a permanent magnet motor. Instant acceleration and smooth performance are due to the high torque and efficiency of these engines.
In addition to efficiency, permanent magnet motors are characterized by compact dimensions and lower weight compared to other motors. This makes them particularly interesting for applications where space is limited or weight restrictions are important.
However, it should be noted that the cost of rare earth magnets used in permanent magnet motors can be relatively high. Additionally, the magnetic properties of these materials can deteriorate over time if not handled properly or exposed to extreme conditions.
Despite these considerations, permanent magnet motors continue to be widely used in various industries due to their excellent performance characteristics and versatility.
Like a superhero with extraordinary powers, permanent magnet motors feature exceptional strength and efficiency, making them an essential choice for many applications.
Brushed motors
Brushed motors are among the oldest and simplest electric motors. They consist of a rotor with permanent magnets surrounded by a stator made of electromagnets. The most important feature of these motors are the brushes and commutators essential to their operation.
When an electric current flows through the electromagnets in the stator, a magnetic field is created that interacts with the permanent magnets in the rotor and causes it to rotate. The brushes and commutators ensure a continuous flow of current to the stator electromagnets. The brushes remain in contact with the commutator segments during rotation, facilitating the change of current direction.
Imagine you have a simple toy car powered by a brushed electric motor. When you connect the battery to the motor, the brushes touch the commutator and allow current to flow through the electromagnets in the stator. This creates a magnetic field that interacts with the rotor's permanent magnets and sets them in motion. The continuous rotation of the rotor propels your toy car forward.
Although brushed motors are widely used due to their simplicity and low cost, they have some limitations. A major disadvantage is that brushes and commutators wear out over time, reducing efficiency and causing maintenance problems. Additionally, brushed motors generate more heat and create electrical noise due to the arcing between the brushes and commutator segments.
Now let's move on to another type of electric motor that has gained popularity in recent years – the brushless motor.
- According to the International Energy Agency, electric motors will account for almost 40% of global electricity consumption in 2020.
- According to a report by the Electric Power Research Institute, AC induction motors account for more than 90% of all motors used in industry due to their robustness and reliability.
- According to a Market Watch study, demand for brushless DC motors in consumer applications is expected to record the highest rate of growth, with an estimated compound annual growth rate of 8.2% between 2018 and 2023.
Brushless electric motors
Brushless electric motors offer several advantages over their brushed counterparts. Unlike brushed motors, which rely on physical brushes and commutators to transfer power, brushless motors use an embedded controller or electronic circuit to transfer power to different stator coils.
Imagine this scenario: you are climbing a steep hill and, as you pedal harder, you feel the increase in power of an electric bike with a brushless motor. The absence of brushes and commutators allows for smoother operation and greater efficiency. The electronic control circuitry in brushless motors actively controls current flow to various stator coils, optimizing performance and reducing wear.
Think of a brushless engine like the fuel injection system in a modern car, delivering just the right amount of fuel to ensure optimal combustion. Likewise, brushless motors allow precise control of power delivery to improve performance.
One of the main advantages of brushless motors is their longer lifespan and less need for maintenance. Without mechanical brushes to wear out, these motors can run longer without needing replacement or repair.
Brushless motors also generate less heat than brushed motors because there is no physical contact between the brushes and commutators. This not only improves overall efficiency, but also results in quieter operation. Additionally, brushless motors offer a better power-to-weight ratio, making them ideal for applications where size and weight limitations are critical factors.
While brushed motors have their place in certain applications, brushless electric motors are a popular choice in several industries due to their advantages. In the next section, we will look at two more types of electric motors – induction motors and synchronous motors.
Induction and synchronous motors
Two common types of electric motors are induction and synchronous AC motors . These engines share similar operating principles but differ in specific features that make them suitable for different applications.
Induction Motors
Let's start by looking at induction motors. Because of the way they work, induction motors are also called squirrel cage motors or asynchronous motors. They are based on the principle of induction to create a rotating magnetic field in the stator. This rotating field induces a current in the rotor and allows it to rotate.
The main component of an induction motor is the rotor which consists of conductive rods arranged in a cylindrical structure. These rods are short-circuited at both ends by conductive rings and resemble a squirrel cage. Hence the name “squirrel cage engine”.
When an alternating current is supplied to the stator windings, it creates a rotating magnetic field. When this magnetic field crosses the rotor bars, it induces currents in them through electromagnetic induction. The resulting interaction between the magnetic fields of the stator and rotor creates a torque that causes the rotor to rotate.
Induction motors are widely used due to their simplicity and robustness. They do not require brushes or commutators, resulting in minimal maintenance and high reliability. Furthermore, they can operate from single-phase and three-phase power supplies.
These motors are used in a variety of industries, including pumps, compressors, fans, conveyors, and machines that require constant speed operation. Furthermore, their ability to produce high torque at low speeds makes them suitable for demanding tasks.
Think of an induction motor as a tireless worker, working continuously without much attention – reliably and efficiently.
Now that we have taken an in-depth look at induction motors, let's focus on their unique features and applications.
Characteristics and applications of induction motors
Induction motors offer several features and benefits that make them a popular choice for many applications. An important advantage is their ability to work efficiently, making them energy-efficient options for various industries.
The absence of brushes and commutators eliminates the friction and wear associated with these components in other types of engines, contributing to their reliability and longevity. This also means that induction motors require minimal maintenance, reducing downtime and associated costs.
Another notable feature of induction motors is their ability to provide high starting torque. This makes them suitable for applications where heavy loads need to be accelerated from a standstill, such as in conveyor systems or crushers.
Induction motors are available in single-phase and three-phase versions, providing flexibility in a variety of power supply scenarios. Due to their inherent design features, they can handle variable loads relatively well.
Additionally, induction motors have a relatively simple design, resulting in low manufacturing cost and affordability compared to other types of motors. This cost advantage makes them a popular choice across multiple industries.
Despite these advantages, it is important to know that induction motors also have their limitations. For example, they generally operate at a constant speed, which is determined by the frequency of the power supply. For applications that require precise speed control, alternative motor types such as servo motors may be more suitable.
Imagine a scenario where an industrial facility requires a motor to operate a conveyor belt consistently and reliably. An induction motor would be an excellent choice as it allows constant speed operation and handles medium to heavy loads efficiently.
Now that we have covered the main features and applications of induction motors, let us now look at another type of electric motors – AC synchronous motors.
Synchronous AC Motors
AC synchronous motors are a type of electric motor that operates synchronously with the frequency and phase of an alternating current (AC) source. These motors have a fixed rotating magnetic field at the same speed as the frequency of the AC power supply. This synchronization allows for precise control of motor speed and position, making AC synchronous motors particularly suitable for applications where precise timing and synchronization are critical.
One of the main advantages of synchronous AC motors is their ability to maintain a constant speed even under fluctuating loads. This makes them ideal for high-precision applications such as industrial machinery, robotics and automation. AC synchronous motors are used, for example, in CNC machines where precise positioning and motion control are essential for precise cutting or forming operations.
Another important characteristic of AC synchronous motors is their efficiency. Due to their synchronous operation, these motors do not suffer from slippage like asynchronous motors, resulting in greater efficiency. This makes them more energy efficient and economical in the long term, especially in applications with constant torque requirements.
Additionally, AC synchronous motors can benefit power generation and renewable energy systems. With appropriate control and synchronization techniques, these motors can be used as generators to efficiently convert mechanical energy into electrical energy. This makes them suitable for applications such as wind turbines or hydroelectric plants.
However, it should be noted that synchronous AC motors require careful control and additional components, such as rotor position sensors or variable frequency drives (VFDs), to maintain synchronization with the power supply. Otherwise, the engine may lose synchronization and potentially be damaged or inefficient.
Motor control and application
The control and application of electric motors plays a crucial role in various industries and everyday devices. This involves controlling the speed, direction, torque and other operating parameters of the engine to achieve desired results. Thanks to advances in motor control technology, numerous options are available, from simple speed controllers to complex programmable systems.
A popular method of motor control is to use motor speed controllers. These devices regulate the voltage and current supplied to the motor, effectively controlling its speed. For example, a ZOWZEA AC motor speed controller provides a versatile solution for controlling the speed of electric motors with an input voltage range of 110-120V and a maximum current capacity of 15A. These controllers are useful in applications that require precise speed control, such as. such as: B. industrial machines or household appliances.
Another approach to motor control is to use specialized control techniques such as pulse width modulation (PWM) or field-oriented control (FOC). PWM techniques rapidly switch the power supplied to the motor and change the average voltage or current to change the speed or torque of the motor. FOC techniques, on the other hand, focus on manipulating the magnetic fields in the motor to gain precise control over parameters such as torque and flux. These techniques are often used in robotics or electric vehicles, where precise control is crucial.
As far as applications are concerned, electric motors are used in various industries. They power everything from household appliances like refrigerators and washing machines to transportation systems like electric cars and trains. In industrial environments, motors are essential for pumps, fans, conveyors and manufacturing equipment. The versatility and reliability of electric motors make them indispensable in countless applications around the world.
For example, think of an automated assembly line in an automobile factory. Electric motors are responsible for powering conveyor belts, robotic arms and other machines that move and assemble automotive parts with precision along the production line. Without effective motor control strategies, it would be nearly impossible to achieve consistency and efficiency in such operations.
Ultimately, if we understand how to control and use electric motors effectively, we can use their power for a variety of purposes in different industries. This enables innovative process optimization and contributes to advances in technology and automation.
High Voltage DC Motor Controller
The high voltage DC motor controller controls DC motors that operate on high voltage power sources. These motors are widely used in various industrial applications that require high power and precise control. One of the main advantages of high voltage DC motor control is its ability to provide fast and efficient acceleration over a wide speed range.
Depending on the specific application requirements, several techniques can be used to control high voltage DC motors. A common method is pulse width modulation (PWM), in which the duty cycle of the signal determines the speed and torque of the motor. By adjusting the duty cycle, the average voltage reaching the motor can be changed, allowing smooth speed control.
Another technique used in controlling high voltage DC motors is field oriented control (FOC) or vector control. This method decouples the torque and flux components of the engine, allowing independent control of both parameters. FOC improves performance and efficiency by optimizing magnetic field alignment and torque generation.
It is worth noting that high voltage DC motor control systems often incorporate advanced technologies such as microcontrollers and power electronics. These components enable precise monitoring, feedback control and protection mechanisms to ensure safe and reliable operation. Additionally, some applications may require additional features, such as regenerative braking or fault diagnosis, which can be integrated into the control system.
For example, imagine a mining company that uses high voltage DC motors to power large underground excavation equipment. By precisely controlling the speed and torque of the motors, operators can ensure optimal digging performance with minimal energy consumption. The sophisticated control system also provides real-time feedback on engine condition, allowing potential problems to be identified early and costly downtime to be avoided.
AC Motor Control
AC motor control involves the management and regulation of AC motors, which are widely used in industrial, commercial and residential applications. AC motors offer several advantages, including greater efficiency, less maintenance, and better speed control than DC motors.
Depending on the AC motor used, different techniques are used to control AC motors. A common method is voltage frequency control. This approach adjusts the frequency of the voltage supplied to the motor to regulate its speed. Precise speed control can be achieved by varying frequency while maintaining constant voltage according to motor specifications.
Another widely used technique is vector control or field-oriented control (FOC). Similar to its implementation in DC motor control, vector control decouples the torque and magnetic flux components in an AC motor. This allows independent control of these parameters and more precise and efficient operation.
An important component in controlling AC motors is the variable frequency drive (VFD), which converts fixed-frequency AC power into adjustable-frequency AC power suitable for controlling AC motors. VFDs are crucial for adjusting the speed and torque of AC motors depending on the desired application requirements.
AC motor control has applications in various industries and sectors. In HVAC systems, for example, precise speed and torque control of AC motors ensures efficient temperature control while minimizing energy consumption. In industrial automation processes, AC motors with advanced control systems enable precise positioning and smooth operation of robotic arms or conveyor belts.
It is important to note that different types of AC motors, such as: B. induction motors or synchronous motors, may require specific control techniques adapted to their characteristics. Selection of the appropriate control method depends on factors such as desired operating range, torque requirements, and efficiency goals.
By effectively controlling AC motors, industries can optimize energy consumption, increase performance and extend motor life. Additionally, the ability to precisely regulate speed and torque enables applications in diverse areas, from manufacturing to transportation and renewable energy systems.
Choosing the Right Engine for Your Needs
There are several factors to consider when selecting the right motor for your application. Understanding these important aspects will help you make an informed decision and ensure optimal performance for your needs.
First, it is important to determine the performance needs of your application. Consider the torque and speed needed to achieve the desired performance. An underpowered engine can result in inefficiency or not meet your needs, while an overpowered engine can be unnecessary and expensive.
Next, consider the operating environment and conditions to which the engine will be exposed. Will it be exposed to extreme temperatures, humidity or dust? In these cases, a motor with suitable protective measures such as sealing or insulation is required. Also consider the space available for installation, as some motors may have size restrictions.
Another crucial factor is understanding the type of load the engine will drive. Different types of loads require specific engine characteristics. For example, a load with high inertia would benefit from a motor with high starting torque, while a variable load may require a motor with good speed control capabilities.
Also, consider the efficiency of the engine. Energy efficiency has become increasingly important for environmental and cost reasons. Look for motors with energy efficiency classes such as NEMA Premium or IE3 (International Efficiency Class 3). These motors generally provide better performance and greater energy savings over time.
To further illustrate this point, let's consider a scenario where you need a motor for an HVAC system in a commercial building. In this case, you would need a motor that can operate continuously at different speeds while maintaining high energy efficiency. You can choose a power-efficient induction motor or even explore newer technologies such as permanent magnet synchronous motors (PMSM) or brushless direct current motors (BLDC) with advanced control options.
Finally, factors such as maintenance and costs must be taken into consideration. Some engines require regular maintenance, while others are virtually maintenance-free. Additionally, evaluate the initial investment cost of the motor and compare it to the potential long-term benefits in terms of performance and energy savings.
To select the right engine for your needs, you must carefully consider power requirements, operating conditions, load characteristics, efficiency, maintenance requirements and cost. By considering all of these factors and consulting experts or industry experts when necessary, you can confidently select a motor that will optimize your application performance while meeting your specific needs.