
The hardness of a metal refers to its ability to resist local deformation, particularly plastic deformation, indentations or scratches. It is a measure of the softness or hardness of the material.
There are two main types of metal hardness testing methods: static and dynamic. Static testing methods include Brinell, Rockwell, Vickers, Knoop, Meyer and Barcol, with Brinell, Rockwell and Vickers being the most widely used. Dynamic testing methods involve the dynamic, impactful application of test forces.
Hardness measurement is mainly determined by the depth of the indentation, the projected area of the indentation or the size of the indentation impression. For example, Brinell hardness (HB) is calculated by pressing a given diameter of hardened steel or hard alloy ball onto the tested metal surface under a given test load, holding it for a specified time, then unloading and measuring the diameter of the indentation. . on the tested surface.
There are various methods to increase metal hardness, including alloying with hard elements in the material, process hardening, grain refinement strengthening, dispersion strengthening, second stage strengthening, heat treatment strengthening (such as quenching, carburizing, nitriding, infiltration metal) and surface reinforcement. Reinforcement. Furthermore, the wear resistance of metallic materials can be improved by changing the structural shape and changing the crystalline state.
Mohs hardness table of metals
Mohs hardness is a standard for representing mineral hardness, first proposed in 1822 by German mineralogist Frederich Mohs. It is a pattern used in mineralogy or gemology. Mohs hardness is determined by using a diamond pyramid needle to scratch the surface of the tested mineral and measure the depth of the scratch. The depth of this scratch is the Mohs hardness, represented by the symbol HM. It is also used to indicate the hardness of other materials.
The measured scratch depth is divided into ten levels to represent hardness (scratch method): talc 1 (least hardness), gypsum 2, calcite 3, fluorite 4, apatite 5, orthoclase (feldspar) 6, quartz 7, topaz 8 , corundum 9, diamond 10. The hardness of the tested mineral is determined by comparing the scratches with standard minerals on the Mohs hardness tester. Although the measurement of this method is crude, it is convenient and practical. It is often used to measure the hardness of natural minerals.
Hardness values are not absolute hardness values, but values represented in order of hardness.
When applying, compare the hardness by scratching. For example, if a mineral can scratch calcite but not fluorite, its Mohs hardness is 3 to 4, and others are inferred. Mohs hardness is just a relative hardness, which is rough. The hardness of talc is 1, diamond is 10, and corundum is 9, but the absolute hardness measured by a microhardness tester is 4,192 times that of talc for diamond and 442 times that of talc for corundum. Mohs hardness is convenient to use and often used in field operations. For example, the hardness of nails is about 2.5, of copper coins is 3.5-4, of steel knives is 5.5 and of glass is 6.5.
In addition to the original list of 1 to 10 types of minerals, the hardness values of common metals are listed here for reference.
Metal | Element | Hardness (Mohs) |
Carbon(diamond) | W | 10 |
Boron | B | 9.3 |
Titanium Carbide | Ti+C | 9 |
Tungsten Carbide | W+C | 9 |
Chrome | Cr | 8.5 |
Tungsten | W | 7.5 |
Vanadium | V | 7 |
Renius | Re | 7 |
Osmium | You | 7 |
Silicon | Yes | 6.5 |
Ruthenium | ru | 6.5 |
Tantalum | OK | 6.5 |
Iridium | Go | 6.5 |
Titanium | You | 6 |
Manganese | Mn | 6 |
Germanium | Ge | 6 |
Niobium | No. | 6 |
Rhodium | Rh | 6 |
Uranium | you | 6 |
Beryllium | To be | 6 |
Molybdenum | Mo | 5.5 |
Hafnium | Hf | 5.5 |
Cobalt | co | 5 |
Zirconium | Zr | 5 |
Palladium | P.D. | 4.75 |
White Cholocate bonbon | Au+Ni+Pd | 4 |
Steel | Fe+C | 4 |
Iron | Faith | 4 |
Nickel | No | 4 |
Arsenic | As | 3.5 |
Platinum | Point | 3.5 |
Brass | Cu+Zn | 3 |
Bronze | Cu+Sn | 3 |
Copper | Ass | 3 |
Antimony | Sb | 3 |
Thorium | th | 3 |
Aluminum | Al | 2.75 |
Magnesium | mg | 2.5 |
Zinc | Zn | 2.5 |
Silver | Ag | 2.5 |
Lanthanum | There | 2.5 |
Cerium | Ce | 2.5 |
Gold | Au | 2.5 |
Tellurium | You | 2.25 |
Bismuth | Bi | 2.25 |
Cadmium | CD | two |
Calcium | Here | 1.75 |
Gallium | Gá | 1.5 |
Strontium | Mr. | 1.5 |
Tin | Sn | 1.5 |
Mercury | Hg | 1.5 |
Lead | Pb | 1.5 |
Barium | BA | 1.25 |
Indian | In | 1.2 |
Thallium | You | 1.2 |
Lithium | Li | 1.2 |
Sodium | N/A | 0.5 |
Potassium | K | 0.4 |
Rubidium | Rb | 0.3 |
Cesium | CS | 0.2 |
Hardness table of metallic materials
No. | Material code | Degree of strength | Hardness value(HB) |
01 | 1Ch13 | 440(45) | 197~229 |
355 | 187~229 | ||
02 | 1Cr12Mo | 550 | 229~255 |
450 | 197~229 | ||
03 | Cr11MoV | 490(50) | 217~248 |
390 | 192~241 | ||
590 | 235~269 | ||
04 | Cr12WMoV | 590 | 235~269 |
690 | 269~302 | ||
05 | 2Cr12NiMoWV | 760 | 293~331 |
06 | ZG20CrMoV | 310 | 140~201 |
07 | 25Cr2MoVA | 590 | 241~277 |
735 | 269~302 | ||
08 | 30Cr2MoV | 440 | 179~229 |
590 | 241~277 | ||
735 | 269~302 | ||
09 | 38CrMoAl | 590 | 241~277 |
685 | 277~302 | ||
785 | 293~321 | ||
10 | A3 | Hardness after normalization of the nitriding component | <131 |
11 | 15# | <143 | |
12 | 25# | <170 | |
13 | ZG25 | <170 | |
14 | 20CrA | <179 | |
15 | 12CrNi3A | <252 | |
16 | 2Ch13 | 490 | 217~248 |
590 | 235~269 | ||
17 | 2Cr12NiW1Mo1V | 735 | 285~302 |
18 | 0Cr17Ni4Cu4Nb | 590 | 262~302 |
760 | 277~311 | ||
19 | Cr5Mo | / | 248~302 |
20 | GH132(GBn181-82) | / | 284~349 |
21 | GH136(GBn181-82) | / | 298~390 |
22 | R-26 | 550 | 262~331 |
23 | 3Ch13 | 590 | 235~269 |
685 | 269~302 | ||
23 | 3Ch13 | 785 | 286~321 |
24 | 1Cr18Ni9Ti | 205(225) | ≦187 |
25 | 0Cr18Ni9 | 205 | ≦187 |
26 | 1Cr18Ni9 | 205 | ≦187 |
27 | Cr15Ni3Bw3Ti | 390 | 207~255 |
28 | 34CrMo1A | 490(590) | / |
29 | 30Cr2MoV | 590 | 241~277 |
690 | 256~287 | ||
735 | 269~302 | ||
30 | 34CrNi3Mo | 590 | 220~260 |
690 | 240~282 | ||
735 | 255~284 | ||
785 | 271~298 | ||
31 | 30Cr2Ni4MoV | 550 | 207~262 |
690 | 241~302 | ||
760 | 262~321 | ||
830 | 285~341 | ||
32 | 15CrMoA | 245 | 131~163 |
490 | 207~241 | ||
33 | 15Cr1Mo | 275 | ≦207 |
34 | 12Cr1MoVA | 245 | 131~163 |
35 | 12Cr2Mo1 | 275 | ≦197 |
315 | ≦207 | ||
36 | 15Cr1Mo1VA | 325 | 146~196 |
37 | 25# | 235(215) | 110~170 |
38 | 30# | 265 | ≦187 |
39 | 35# | 265 | 156~217 |
255 | 140~187 | ||
235 | 121~187 | ||
40 | 45# | 295 | 162~217 |
285 | 149~217 | ||
440 | 197~229 | ||
345 | 217~255 | ||
41 | 15CrMoA | 245 | 131~163 |
490 | 207~241 | ||
42 | 20MnMo | 350 | 149~217 |
43 | 40CrNi3MoA | 550 | 207~262 |
690 | 241~302 | ||
44 | 15CrMoA | 490 | 207~241 |
45 | 40CrA | 390 | 192~223 |
45 | 40CrA | 490 | 217~235 |
590 | 241~277 | ||
685 | 269~302 | ||
46 | 40CrNi2MoA | 540 | 207~269 |
640 | 248~277 | ||
785 | 269~321 | ||
47 | 35CrMoA | 490 | 217~255 |
590 | 241~277 | ||
48 | 40CrNiMoA | 690 | 255~293 |
49 | 20Cr1Mo1VtiB | 690 | 255~293 |
50 | 30Cr1Mo1V | 590 | 241~277 |
51 | 30Cr1Mo1V | 690 | 255~285 |
Materials | Reference Standards and Requirements(HB) | Control scope(HB) | Observation |
210°C | ASTM A210,≤179 | 130~179 | |
T1a, 20MoG, STBA12, 15Mo3 | ASTM A209,≤153 | 125~153 | |
T2, T11, T12, T21, T22, 10CrMo910 | ASTM A213,≤163 | 120~163 | |
P2, P11, P12, /P21, P22, 10CrMo910 | 125~179 | ||
P2, P11, P12, /P21P22, 10CrMo910 type pipe fittings | 130~197 | The lower limit of the weld seam should not be lower than that of the base material, upper limit≤241 | |
T23 | ASTM A213,≤220 | 150~220 | |
12Cr2MoWVTiB(G102) | 150~220 | ||
T24 | ASTM A213,≤250 | 180~250 | |
T/P91, T/P92, T911, T/P122 | ASTM A213,≤250ASTM A335,≤250 | 180~250 | The hardness of “P” type tubes refers to that of “T” type tubes. |
(T/P91, T/P92, T911, T/P122) Welding seam | 180~270 | ||
WB36 | ASME code case2353,≤252 | 180~252 | The weld seam must be no less hard than the base material. |
Pipe Fittings Type A515, A106B, A106C, A672 B70 | 130~197 | The lower limit of the weld seam should not be lower than the base material, with the upper limit≤241. | |
12CrMo | GB3077,≤179 | 120~179 | |
15CrMo | JB4726,118~180(Rm:440~610)JB4726,115~178(Rm:430~600) | 118~180115~178 | |
12Cr1MoV | GB3077,≤179 | 135~179 | |
15Cr1Mo1V | 135~180 | ||
F2 (Fittings for forged or rolled pipes, valves and components) | ASTM A182.143~192 | 143~192 | |
F11, Class 1 | ASTM A182.121~174 | 121~174 | |
F11, Class 2 | ASTM A182.143~207 | 143~207 | |
F11, Class 3 | ASTM A182.156~207 | 156~207 | |
F12, Class 1 | ASTM A182.121~174 | 121~174 | |
F12, Class 2 | ASTM A182.143~207 | 143~207 | |
F22, Class 1 | ASTM A182, ≤170 | 130~170 | |
F22, Class 3 | ASTM A182.156~207 | 156~207 | |
F91 | ASTM A182, ≤248 | 175~248 | |
F92 | ASTM A182, ≤269 | 180~269 | |
F911 | ASTM A182, 187~248 | 187~248 | |
F122 | ASTM A182, ≤250 | 177~250 | |
20 carbon steel and low alloy steel forgings for pressure vessels | JB4726,106~159 | 106~159 | |
35 (Note: The Rm in the table refers to the tensile strength of the material, measured in MPa.) | JB4726,136~200(Rm:510~670)JB4726,130~190(Rm:490~640) | 136~200130~190 | |
16 minutes | JB4726,121~178(Rm:450~600) | 121~178 | |
20MnMo | JB4726, 156~208 (Rm: 530~700) JB4726, 136~201 (Rm: 510~680) JB4726, 130~196 (Rm: 490~660) | 156~208136~201130~196 | |
35CrMo | JB4726,185~235(Rm:620~790)JB4726,180~223(Rm:610~780) | 185~235180~223 | |
0Cr18Ni90Cr17Ni12Mo2 | JB4728,139~187(Rm:520)JB4728,131~187(Rm:490) | 139~187131~187 | Stainless Steel Forgings for Pressure Vessels |
1Cr18Ni9 | GB1220 ≤187 | 140~187 | |
0Cr17Ni12Mo2 | GB1220 ≤187 | 140~187 | |
0Cr18Ni11Nb | GB1220 ≤187 | 140~187 | |
TP304H, TP316H, TP347H | ASTM A213,≤192 | 140~192 | |
1Ch13 | 192~211 | Moving Blades | |
2Ch13 | 212~277 | Moving Blades | |
1Cr11MoV | 212~277 | Moving Blades | |
1Cr12MoWV | 229~311 | Moving Blades | |
ZG20CrMo | JB/T 7024,135~180 | 135~180 | |
ZG15Cr1Mo | JB/T 7024,140~220 | 140~220 | |
ZG15Cr2Mo1 | JB/T 7024,140~220 | 140~220 | |
ZG20CrMoV | JB/T 7024,140~220 | 140~220 | |
ZG15Cr1Mo1V | JB/T 7024,140~220 | 140~220 | |
35 | DL/T439,146~196 | 146~196 | Screw |
45 | DL/T439,187~229 | 187~229 | Screw |
20CrMo | DL/T439,197~241 | 197~241 | Screw |
35CrMo | DL/T439,241~285 | 241~285 | Screw(Diameter >50mm) |
35CrMo | DL/T439,255~311 | 255~311 | Screw(Diameter≤50mm) |
42CrMo | DL/T439,248~311 | 248~311 | Screw(Diameter >65mm) |
42CrMo | DL/T439,255~321 | 255~321 | Screw(Diameter≤65mm) |
25Cr2MoV | DL/T439,248~293 | 248~293 | Screw |
25Cr2Mo1V | DL/T439,248~293 | 248~293 | Screw |
20Cr1Mo1V1 | DL/T439,248~293 | 248~293 | Screw |
20Cr1Mo1VTiB | DL/T439,255~293 | 255~293 | Screw |
20Cr1Mo1VNbTiB | DL/T439,252~302 | 252~302 | Screw |
20Cr12NiMoWV(C422) | DL/T439,277~331 | 277~331 | Screw |
2Cr12NiW1Mo1V | Eastern Steam Turbine Factory Pattern | 291~321 | Screw |
2Cr11Mo1NiWVNbN | Eastern Steam Turbine Factory Pattern | 290~321 | Screw |
45Cr1MoV | Eastern Steam Turbine Factory Pattern | 248~293 | Screw |
R-26 (Ni-Cr-Co) alloy | DL/T439,262~331 | 262~331 | Screw |
GH445 | DL/T439,262~331 | 262~331 | Screw |
ZG20CrMo | JB/T7024,135~180 | 135~180 | Cylinder |
ZG15Cr1Mo, ZG15Cr2MoZG20Cr1MoV, ZG15Cr1Mo1V | JB/T7024,140~220 | 140~220 | Cylinder |
Hardness table of non-ferrous and ferrous metals
1. Non-ferrous metal hardness table
Hardness of non-ferrous metals | Tensile strength δb /MPa |
|||||||||||||||
---|---|---|---|---|---|---|---|---|---|---|---|---|---|---|---|---|
Rockwell | Rockwell Surface | Vickers | Brinell (F/D2=30) |
|||||||||||||
CDH | HR | HR15N | HR30N | HR45N | High voltage | HBS | HBW | IN | Cr.S | Cr-VS | CrNi.S | Cr-Mo.S | Cr-Ni-Mo .S | CrMnSi.S | UHSS | SS |
20.0 | 60.2 | 68.8 | 40.7 | 19.2 | 226 | 225 | 225 | 774 | 742 | 736 | 782 | 747 | / | 781 | / | 740 |
20.5 | 60.4 | 69.0 | 41.2 | 19.8 | 228 | 227 | 227 | 784 | 751 | 744 | 787 | 753 | / | 788 | / | 749 |
21.0 | 60.7 | 69.3 | 41.7 | 20.4 | 230 | 229 | 229 | 793 | 760 | 753 | 792 | 760 | / | 794 | / | 758 |
21.5 | 61.0 | 69.5 | 42.2 | 21.0 | 233 | 232 | 232 | 803 | 769 | 761 | 797 | 767 | / | 801 | / | 767 |
22.0 | 61.2 | 69.8 | 42.6 | 21.5 | 235 | 234 | 234 | 813 | 779 | 770 | 803 | 774 | / | 809 | / | 777 |
22.5 | 61.5 | 70.0 | 43.1 | 22.1 | 238 | 237 | 237 | 823 | 788 | 779 | 809 | 781 | / | 816 | / | 786 |
23.0 | 61.7 | 70.3 | 43.6 | 22.7 | 24 liters | 240 | 240 | 833 | 798 | 788 | 815 | 789 | / | 824 | / | 796 |
23.5 | 62.0 | 70.6 | 44.0 | 23.3 | 244 | 242 | 242 | 843 | 808 | 797 | 822 | 797 | / | 832 | / | 806 |
24.0 | 62.2 | 70.8 | 44.5 | 23.9 | 247 | 245 | 245 | 854 | 818 | 807 | 829 | 805 | / | 840 | / | 816 |
24.5 | 62.5 | 71.1 | 45.0 | 24.5 | 250 | 248 | 248 | 864 | 828 | 816 | 836 | 813 | / | 848 | / | 826 |
25.0 | 62.8 | 71.4 | 45.5 | 25.1 | 253 | 251 | 251 | 875 | 838 | 826 | 843 | 822 | / | 856 | / | 837 |
25.5 | 63.0 | 71.6 | 45.9 | 25.7 | 256 | 254 | 254 | 886 | 848 | 837 | 851 | 831 | 850 | 865 | / | 847 |
26.0 | 63.3 | 71.9 | 46.4 | 26.3 | 259 | 257 | 257 | 897 | 859 | 847 | 859 | 840 | 859 | 874 | / | 858 |
26.5 | 63.5 | 72.2 | 46.9 | 26.9 | 262 | 260 | 260 | 908 | 870 | 858 | 867 | 850 | 869 | 883 | / | 868 |
27.0 | 63.8 | 72.4 | 47.3 | 27.5 | 266 | 263 | 263 | 919 | 880 | 869 | 876 | 860 | 879 | 893 | / | 879 |
27.5 | 64.0 | 72.7 | 47.8 | 28.1 | 269 | 266 | 266 | 930 | 891 | 880 | 885 | 870 | 890 | 902 | / | 890 |
28.0 | 64.3 | 73.0 | 48.3 | 28.7 | 273 | 269 | 269 | 942 | 902 | 892 | 894 | 880 | 901 | 912 | / | 901 |
28.5 | 64.6 | 73.3 | 48.7 | 29.3 | 276 | 273 | 273 | 954 | 914 | 903 | 904 | 891 | 912 | 922 | / | 913 |
29.0 | 64.8 | 73.5 | 49.2 | 29.9 | 280 | 276 | 276 | 965 | 925 | 915 | 914 | 902 | 923 | 933 | / | 924 |
29.5 | 65.1 | 73.8 | 49.7 | 30.5 | 284 | 280 | 280 | 977 | 937 | 928 | 924 | 913 | 935 | 943 | / | 936 |
30.0 | 65.3 | 74.1 | 50.2 | 31.1 | 288 | 283 | 283 | 989 | 948 | 940 | 935 | 924 | 947 | 954 | / | 947 |
30.5 | 65.6 | 74.4 | 50.6 | 31.7 | 292 | 287 | 287 | 1002 | 960 | 953 | 946 | 936 | 959 | 965 | / | 959 |
31.0 | 65.8 | 74.7 | 51.1 | 32.3 | 296 | 29l | 29l | 1014 | 972 | 966 | 957 | 948 | 972 | 977 | / | 971 |
31.5 | 66.1 | 74.9 | 51.6 | 32.9 | 300 | 294 | 294 | 1027 | 984 | 980 | 969 | 961 | 985 | 989 | / | 983 |
32.0 | 66.4 | 75.2 | 52.0 | 33.5 | 304 | 298 | 298 | 1039 | 996 | 993 | 981 | 974 | 999 | 1001 | / | 996 |
32.5 | 66.6 | 75.5 | 52.5 | 34.1 | 308 | 302 | 302 | 1052 | 1009 | 1007 | 994 | 987 | 1012 | 1013 | / | 1008 |
33.0 | 66.9 | 75.8 | 53.0 | 34.7 | 313 | 306 | 306 | 1065 | 1022 | 1022 | 1007 | 1001 | 1027 | 1026 | / | 1021 |
33.5 | 67.1 | 76.1 | 53.4 | 35.3 | 317 | 310 | 310 | 1078 | 1034 | 1036 | 1020 | 1015 | 1041 | 1039 | / | 1034 |
34.0 | 67.4 | 76.4 | 53.9 | 35.9 | 32 liters | 314 | 314 | 1092 | 1048 | 1051 | 1034 | 1029 | 1056 | 1052 | / | 1047 |
34.5 | 67.7 | 76.7 | 54.4 | 36.5 | 326 | 318 | 318 | 1105 | 1061 | 1067 | 1048 | 1043 | 1071 | 1066 | / | 1060 |
35.0 | 67.9 | 77.0 | 54.8 | 37.0 | 33 liters | 323 | 323 | 1119 | 1074 | 1082 | 1063 | 1058 | 1087 | 1079 | / | 1074 |
35.5 | 68.2 | 77.2 | 55.3 | 37.6 | 335 | 327 | 327 | 1133 | 1088 | 1098 | 1078 | 1074 | 1103 | 1094 | / | 1087 |
36.0 | 68.4 | 77.5 | 55.8 | 38.2 | 340 | 332 | 332 | 1147 | 1102 | 1114 | 1093 | 1090 | 1119 | 1108 | / | 1101 |
36.5 | 68.7 | 77.8 | 56.2 | 38.8 | 345 | 336 | 336 | 1162 | 1116 | 1131 | 1109 | 1106 | 1136 | 1123 | / | 1116 |
37.0 | 69.0 | 78.1 | 56.7 | 39.4 | 350 | 341 | 341 | 1177 | 1131 | 1148 | 1125 | 1122 | 1153 | 1139 | / | 1130 |
37.5 | 69.2 | 78.4 | 57.2 | 40.0 | 355 | 345 | 345 | 1192 | 1146 | 1165 | 1142 | 1139 | 1171 | 1155 | / | 1145 |
38.0 | 69.5 | 78.7 | 57.6 | 40.6 | 360 | 350 | 350 | 1207 | 1161 | 1183 | 1159 | 1157 | 1189 | 1171 | / | 1161 |
38.5 | 69.7 | 79.0 | 58.1 | 41.2 | 365 | 355 | 355 | 1222 | 1176 | 1201 | 1177 | 1174 | 1207 | 1187 | 1170 | 1176 |
39.0 | 70.0 | 79.3 | 58.6 | 41.8 | 37 liters | 360 | 360 | 1238 | 1192 | 1219 | 1195 | 1192 | 1226 | 1204 | 1195 | 1193 |
39.5 | 70.3 | 79.6 | 59.0 | 42.4 | 376 | 365 | 365 | 1254 | 1208 | 1238 | 1214 | 1211 | 1245 | 1222 | 1219 | 1209 |
40.0 | 70.5 | 79.9 | 59.5 | 43.0 | 381 | 370 | 370 | 1271 | 1225 | 1257 | 1233 | 1230 | 1265 | 1240 | 1243 | 1226 |
40.5 | 70.8 | 80.2 | 60.0 | 43.6 | 387 | 375 | 375 | 1288 | 1242 | 1276 | 1252 | 1249 | 1285 | 1258 | 1267 | 1244 |
41.0 | 71.1 | 80.5 | 60.4 | 44.2 | 393 | 380 | 381 | 1305 | 1260 | 1296 | 1273 | 1269 | 1306 | 1277 | 1290 | 1262 |
41.5 | 71.3 | 80.8 | 60.9 | 44.8 | 398 | 385 | 386 | 1322 | 1278 | 1317 | 1293 | 1289 | 1327 | 1296 | 1313 | 1280 |
42.0 | 71.6 | 81.1 | 61.3 | 45.4 | 404 | 39 liters | 392 | 1340 | 1296 | 1337 | 1314 | 1310 | 1348 | 1316 | 1336 | 1299 |
42.5 | 71.8 | 81.4 | 61.8 | 45.9 | 410 | 396 | 397 | 1359 | 1315 | 1358 | 1336 | 1331 | 1370 | 1336 | 1359 | 1319 |
43.0 | 72.1 | 81.7 | 62.3 | 46.5 | 416 | 40l | 403 | 1378 | 1335 | 1380 | 1358 | 1353 | 1392 | 1357 | 1381 | 1339 |
43.5 | 72.4 | 82.0 | 62.7 | 47.1 | 422 | 407 | 409 | 1397 | 1355 | 1401 | 1380 | 1375 | 1415 | 1378 | 1404 | 1361 |
44.0 | 72.6 | 82.3 | 63.2 | 47.7 | 428 | 413 | 415 | 1417 | 1376 | 1424 | 1404 | 1397 | 1439 | 1400 | 1427 | 1383 |
44.5 | 72.9 | 82.6 | 63.6 | 48.3 | 435 | 418 | 422 | 1438 | 1398 | 1446 | 1427 | 1420 | 1462 | 1422 | 1450 | 1405 |
45.0 | 73.2 | 82.9 | 64.1 | 48.9 | 44 liters | 424 | 428 | 1459 | 1420 | 1469 | 1451 | 1444 | 1487 | 1445 | 1473 | 1429 |
45.5 | 73.4 | 83.2 | 64.6 | 49.5 | 448 | 430 | 435 | 1481 | 1444 | 1493 | 1476 | 1468 | 1512 | 1469 | 1496 | 1453 |
46.0 | 73.7 | 83.5 | 65.0 | 50.1 | 454 | 436 | 44 liters | 1503 | 1468 | 1517 | 1502 | 1492 | 1537 | 1493 | 1520 | 1479 |
46.5 | 73.9 | 83.7 | 65.5 | 50.7 | 46 liters | 442 | 448 | 1526 | 1493 | 1541 | 1527 | 1517 | 1563 | 1517 | 1544 | 1505 |
47.0 | 74.2 | 84.0 | 65.9 | 51.2 | 468 | 449 | 455 | 1550 | 1519 | 1566 | 1554 | 1542 | 1589 | 1543 | 1569 | 1533 |
47.5 | 74.5 | 84.3 | 66.4 | 51.8 | 475 | / | 463 | 1575 | 1546 | 1591 | 1581 | 1568 | 1616 | 1569 | 1594 | 1562 |
48.0 | 74.7 | 84.6 | 66.8 | 52.4 | 482 | / | 470 | 1600 | 1574 | 1617 | 1608 | 1595 | 1643 | 1595 | 1620 | 1592 |
48.5 | 75.0 | 84.9 | 67.3 | 53.0 | 489 | / | 478 | 1626 | 1603 | 1643 | 1636 | 1622 | 1671 | 1623 | 1646 | 1623 |
49.0 | 75.3 | 85.2 | 67.7 | 53.6 | 497 | / | 486 | 1653 | 1633 | 1670 | 1665 | 1649 | 1699 | 1651 | 1674 | 1655 |
49.5 | 75.5 | 85.5 | 68.2 | 54.2 | 504 | / | 494 | 1681 | 1665 | 1697 | 1695 | 1677 | 1728 | 1679 | 1702 | 1689 |
50.0 | 75.8 | 85.7 | 68.6 | 54.7 | 512 | 502 | 502 | 1710 | 1698 | 1724 | 1724 | 1706 | 1758 | 1709 | 1731 | 1725 |
50.5 | 76.1 | 86.0 | 69.1 | 55.3 | 520 | 510 | 510 | / | 1732 | 1752 | 1755 | 1735 | 1788 | 1739 | 1761 | / |
51.0 | 76.3 | 86.3 | 69.5 | 55.9 | 527 | 518 | 518 | / | 1768 | 1780 | 1786 | 1764 | 1819 | 1770 | 1792 | / |
51.5 | 76.6 | 86.6 | 70.0 | 56.5 | 535 | 527 | 527 | / | 1806 | 1809 | 1818 | 1794 | 1850 | 1801 | 1824 | / |
52.0 | 76.9 | 86.8 | 70.4 | 57.1 | 544 | 535 | 535 | / | 1845 | 1839 | 1850 | 1825 | 1881 | 1834 | 1857 | / |
52.5 | 77.1 | 87.1 | 70.9 | 57.6 | 552 | 544 | 544 | / | / | 1869 | 1883 | 1856 | 1914 | 1867 | 1892 | / |
53.0 | 77.4 | 87.4 | 71.3 | 58.2 | 561 | 552 | 552 | / | / | 1899 | 1917 | 1888 | 1947 | 1901 | 1929 | / |
53.5 | 77.7 | 87.6 | 71.8 | 58.8 | 569 | 56 liters | 56 liters | / | / | 1930 | 1951 | / | / | 1936 | 1966 | / |
54.0 | 77.9 | 87.9 | 72.2 | 59.4 | 578 | 569 | 569 | / | / | 1961 | 1986 | / | / | 1971 | 2006 | / |
54.5 | 78.2 | 88.1 | 72.6 | 59.9 | 587 | 577 | 577 | / | / | 1993 | 2022 | / | / | 2008 | 2047 | / |
55.0 | 78.5 | 88.4 | 73.1 | 60.5 | 596 | 585 | 585 | / | / | 2026 | 2058 | / | / | 2045 | 2090 | / |
55.5 | 78.7 | 88.6 | 73.5 | 61.1 | 606 | 593 | 593 | / | / | / | / | / | / | / | 2135 | / |
56.0 | 79.0 | 88.9 | 73.9 | 61.7 | 615 | 601 | 601 | / | / | / | / | / | / | / | 2181 | / |
56.5 | 79.3 | 89.1 | 74.4 | 62.2 | 625 | 608 | 608 | / | / | / | / | / | / | / | 2230 | / |
57.0 | 79.5 | 89.4 | 74.8 | 62.8 | 635 | 616 | 616 | / | / | / | / | / | / | / | 2281 | / |
57.5 | 79.8 | 89.6 | 75.2 | 63.4 | 645 | 622 | 622 | / | / | / | / | / | / | / | 2334 | / |
58.0 | 80.1 | 89.8 | 75.6 | 63.9 | 655 | 628 | 628 | / | / | / | / | / | / | / | 2390 | / |
58.5 | 80.3 | 90.0 | 76.1 | 64.5 | 666 | 634 | 634 | / | / | / | / | / | / | / | 2448 | / |
59.0 | 80.6 | 90.2 | 76.5 | 65.1 | 676 | 639 | 639 | / | / | / | / | / | / | / | 2509 | / |
59.5 | 80.9 | 90.4 | 76.9 | 65.6 | 687 | 643 | 643 | / | / | / | / | / | / | / | 2572 | / |
60.0 | 81.2 | 90.6 | 77.3 | 66.2 | 698 | 647 | 647 | / | / | / | / | / | / | / | / | / |
60.5 | 81.4 | 90.8 | 77.7 | 66.8 | 710 | 650 | 650 | / | / | / | / | / | / | / | / | / |
61.0 | 81.7 | 91.0 | 78.1 | 67.3 | 72 liters | / | / | / | / | / | / | / | / | / | / | / |
61.5 | 82.0 | 91.2 | 78.6 | 67.9 | 733 | / | / | / | / | / | / | / | / | / | / | / |
62.0 | 82.2 | 91.4 | 79.0 | 68.4 | 745 | / | / | / | / | / | / | / | / | / | / | / |
62.5 | 82.5 | 91.5 | 79.4 | 69.0 | 757 | / | / | / | / | / | / | / | / | / | / | / |
63.0 | 82.8 | 91.7 | 79.8 | 69.5 | 770 | / | / | / | / | / | / | / | / | / | / | / |
63.5 | 83.1 | 91.8 | 80.2 | 70.1 | 782 | / | / | / | / | / | / | / | / | / | / | / |
64.0 | 83.3 | 91.9 | 80.6 | 70.6 | 795 | / | / | / | / | / | / | / | / | / | / | / |
64.5 | 83.6 | 92.1 | 81.0 | 71.2 | 809 | / | / | / | / | / | / | / | / | / | / | / |
65.0 | 83.9 | 92.2 | 81.3 | 71.1 | 822 | / | / | / | / | / | / | / | / | / | / | / |
65.5 | 84.1 | / | / | / | 836 | / | / | / | / | / | / | / | / | / | / | / |
66.0 | 84.4 | / | / | / | 850 | / | / | / | / | / | / | / | / | / | / | / |
66.5 | 84.7 | / | / | / | 865 | / | / | / | / | / | / | / | / | / | / | / |
67.0 | 85.0 | / | / | / | 879 | / | / | / | / | / | / | / | / | / | / | / |
67.5 | 85.2 | / | / | / | 894 | / | / | / | / | / | / | / | / | / | / | / |
68.0 | 85.5 | / | / | / | 909 | / | / | / | / | / | / | / | / | / | / | / |
2. Hardness table of ferrous metals
The following data is mainly applicable to low carbon steel (mild steel).
Hardness of ferrous metals | Tensile strength | ||||||
---|---|---|---|---|---|---|---|
Rockwell | Rockwell Surface | Vickers | Brinell HBS | ||||
HRB | HR15T | HR30T | HR45T | High voltage | F/D2=10 | F/D2=10 | MPa |
60.0 | 80.4 | 56.1 | 30.4 | 105 | 102 | / | 375 |
60.5 | 80.5 | 56.4 | 30.9 | 105 | 102 | / | 377 |
61.0 | 80.7 | 56.7 | 31.4 | 106 | 103 | / | 379 |
61.5 | 80.8 | 57.1 | 31.9 | 107 | 103 | / | 381 |
62.0 | 80.9 | 57.4 | 32.4 | 108 | 104 | / | 382 |
62.5 | 81.1 | 57.7 | 32.9 | 108 | 104 | / | 384 |
63.0 | 81.2 | 58.0 | 33.5 | 109 | 105 | / | 386 |
63.5 | 81.4 | 58.3 | 34.0 | 110 | 105 | / | 388 |
64.0 | 81.5 | 58.7 | 34.5 | 110 | 106 | / | 390 |
64.5 | 81.6 | 59.0 | 35.0 | 11l | 106 | / | 393 |
65.0 | 81.8 | 59.3 | 35.5 | 112 | 107 | / | 395 |
65.5 | 81.9 | 59.6 | 36.1 | 113 | 107 | / | 397 |
66.0 | 82.1 | 59.9 | 36.6 | 114 | 108 | / | 399 |
66.5 | 82.2 | 60.3 | 37.1 | 115 | 108 | / | 402 |
67.0 | 82.3 | 60.6 | 37.6 | 115 | 109 | / | 404 |
67.5 | 82.5 | 60.9 | 38.1 | 116 | 110 | / | 407 |
68.0 | 82.6 | 61.2 | 38.6 | 117 | 110 | / | 409 |
68.5 | 82.7 | 61.5 | 39.2 | 118 | 111 | / | 412 |
69.0 | 82.9 | 61.9 | 39.7 | 119 | 112 | / | 415 |
69.5 | 83.0 | 62.2 | 40.2 | 120 | 112 | / | 418 |
70.0 | 83.2 | 62.5 | 40.7 | 12l | 113 | / | 42l |
70.5 | 83.3 | 62.8 | 41.2 | 122 | 114 | / | 424 |
71.0 | 83.4 | 63.1 | 41.7 | 123 | 115 | / | 427 |
71.5 | 83.6 | 63.5 | 42.3 | 124 | 115 | / | 430 |
72.0 | 83.7 | 63.8 | 42.8 | 125 | 116 | / | 433 |
72.5 | 83.9 | 64.1 | 43.3 | 126 | 117 | / | 437 |
73.0 | 84.0 | 64.4 | 43.8 | 128 | 118 | / | 440 |
73.5 | 84.1 | 64.7 | 44.3 | 129 | 119 | / | 444 |
74.0 | 84.3 | 65.1 | 44.8 | 130 | 120 | / | 447 |
74.5 | 84.4 | 65.4 | 45.4 | 13l | 12l | / | 451 |
75.0 | 84.5 | 65.7 | 45.9 | 132 | 122 | 152 | 455 |
75.5 | 84.7 | 66.0 | 46.4 | 134 | 123 | 155 | 459 |
76.0 | 84.8 | 66.3 | 46.9 | 135 | 124 | 156 | 463 |
76.5 | 85.0 | 66.6 | 47.4 | 136 | 125 | 158 | 467 |
77.0 | 85.1 | 67.0 | 47.9 | 138 | 126 | 159 | 471 |
77.5 | 85.2 | 67.3 | 48.5 | 139 | 127 | 16 liters | 475 |
78.0 | 85.4 | 67.6 | 49.0 | 140 | 128 | 163 | 480 |
78.5 | 85.5 | 67.9 | 49.5 | 142 | 129 | 164 | 484 |
79.0 | 85.7 | 68.2 | 50.0 | 143 | 130 | 166 | 489 |
79.5 | 85.8 | 68.6 | 50.5 | 145 | 132 | 168 | 493 |
80.0 | 85.9 | 68.9 | 51.0 | 146 | 133 | 170 | 498 |
80.5 | 86.1 | 69.2 | 51.6 | 148 | 134 | 172 | 503 |
81.0 | 86.2 | 69.5 | 52.1 | 149 | 136 | 174 | 508 |
81.5 | 86.3 | 69.8 | 52.6 | 151 | 137 | / | 513 |
82.0 | 86.5 | 70.2 | 53.1 | 152 | 138 | / | 518 |
82.5 | 86.6 | 70.5 | 53.6 | 154 | 140 | / | 523 |
83.0 | 86.8 | 70.8 | 54.1 | 156 | / | / | 529 |
83.5 | 86.9 | 71.1 | 54.7 | 157 | / | / | 534 |
84.0 | 87.0 | 71.4 | 55.2 | 159 | / | / | 540 |
84.5 | 87.2 | 71.8 | 55.7 | 16 liters | / | / | 546 |
85.0 | 87.3 | 72.1 | 56.2 | 163 | / | / | 551 |
85.5 | 87.5 | 72.4 | 56.7 | 165 | / | / | 557 |
86.0 | 87.6 | 72.7 | 57.2 | 166 | / | / | 563 |
86.5 | 87.7 | 73.0 | 57.8 | 168 | / | / | 570 |
87.0 | 87.9 | 73.4 | 58.3 | 170 | / | / | 576 |
87.5 | 88.0 | 73.7 | 58.8 | 172 | / | / | 582 |
88.0 | 88.1 | 74.0 | 59.3 | 174 | / | / | 589 |
88.5 | 88.3 | 74.3 | 59.8 | 176 | / | / | 596 |
89.0 | 88.4 | 74.6 | 60.3 | 178 | / | / | 603 |
89.5 | 88.6 | 75.0 | 60.9 | 180 | / | / | 609 |
90.0 | 88.7 | 75.3 | 61.4 | 183 | / | 176 | 617 |
90.5 | 88.8 | 75.6 | 61.9 | 185 | / | 178 | 624 |
91.0 | 89.0 | 75.9 | 62.4 | 187 | / | 180 | 63 liters |
91.5 | 89.1 | 76.2 | 62.9 | 189 | / | 182 | 639 |
92.0 | 89.3 | 76.6 | 63.4 | 191 | / | 184 | 646 |
92.5 | 89.4 | 76.9 | 64.0 | 194 | / | 187 | 654 |
93.0 | 89.5 | 77.2 | 64.5 | 196 | / | 189 | 662 |
93.5 | 89.7 | 77.5 | 65.0 | 199 | / | 192 | 670 |
94.0 | 89.8 | 77.8 | 65.5 | 201 | / | 195 | 678 |
94.5 | 89.9 | 78.2 | 66.0 | 203 | / | 197 | 686 |
95.5 | 90.1 | 78.5 | 66.5 | 206 | / | 200 | 695 |
95.0 | 90.2 | 78.8 | 67.1 | 208 | / | 203 | 703 |
96.0 | 90.4 | 79.1 | 67.6 | 211 | / | 206 | 712 |
96.5 | 90.5 | 79.4 | 68.1 | 214 | / | 209 | 721 |
97.0 | 90.6 | 79.8 | 68.6 | 216 | / | 212 | 730 |
97.5 | 90.8 | 80.1 | 69.1 | 219 | / | 215 | 739 |
98.0 | 90.9 | 80.4 | 69.6 | 222 | / | 218 | 749 |
98.5 | 91.1 | 80.7 | 70.2 | 225 | / | 222 | 758 |
99.0 | 91.2 | 81.0 | 70.7 | 227 | / | 226 | 768 |
99.5 | 91.3 | 81.4 | 71.2 | 230 | / | 229 | 778 |
100.0 | 91.5 | 81.7 | 71.7 | 233 | / | 232 | 788 |
Related Reading: Metal Hardness Comparison Table: HV, HB, HRC
Commonly used hardness
Brinell hardness
The Brinell hardness test uses a ball made of hardened steel or a hard alloy with diameter D as an indenter.
A specified test force F is applied to the surface of the material being tested and, after a designated holding time, the test force is removed, leaving an indentation with diameter d.
The Brinell hardness value is calculated by dividing the test force by the surface area of the indentation. The symbol for the Brinell hardness value is represented as HBS or HBW.
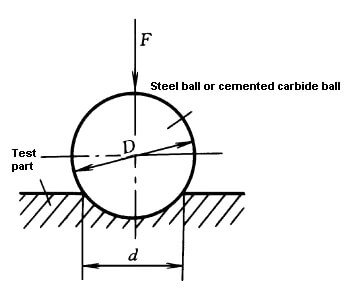
The difference between HBS and HBW is the type of indenter used.
HBS indicates the use of a hardened steel ball as an indenter and is used to determine the Brinell hardness of materials with a value less than 450, such as mild steel, gray cast iron and non-ferrous metals.
HBW, on the other hand, refers to the use of a hard alloy ball as an indenter and is used to measure the Brinell hardness of materials with a value less than 650.
Even when the same material and experimental conditions are used, the results of the two tests may vary, with the HBW value usually being higher than the HBS value, and there is no exact quantitative rule to follow.

In 2003, China adopted international standards and discontinued the use of steel ball indenters in favor of hard alloy ball heads.
As a result, HBS was no longer used and all Brinell hardness values are now represented by HBW.
Although HBW is often referred to simply as HB, references to HBS can still be found in the literature.
The Brinell hardness measurement method is suitable for testing materials such as cast iron, non-ferrous alloys and various steels that have undergone annealing or quenching and tempering processes.
However, it is not suitable for testing samples or workpieces that are too hard, too small, too thin, or that do not allow large indentations in the surface.
Rockwell hardness
The Vickers hardness test uses a diamond cone with a cone apex angle of 120 degrees or a hardened steel ball with a diameter of Ø1.588 mm or Ø3.176 mm as an indenter, together with a specified load.
The sample is subjected to an initial load of 10kgf and a total load of 60, 100 or 150kgf.
After full load is applied, hardness is determined by the difference in indentation depth when the main load is removed while maintaining the initial load and the indentation depth under the initial load.
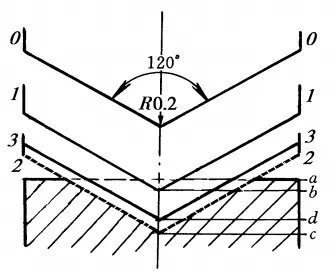
The Rockwell hardness test utilizes three different testing forces and three different indenters, resulting in a total of nine possible combinations and corresponding Rockwell hardness scales.
These nine scales are suitable for a wide variety of commonly used metallic materials.
The three most commonly used Rockwell hardness scales are HRA, HRB and HRC, with HRC being the most widely used.
Table of Commonly Used Rockwell Hardness Test Specifications
Hardness symbol | Penetrator type | Full strength test F/N(kgf) |
Hardness range | Forms |
---|---|---|---|---|
HR | 120° diamond cone | 588.4(60) | 20~88 | Hard alloy, carbide, surface hardening steel and etc. |
HRB | Hardened steel ball Ø1.588mm | 980.7(100) | 20~100 | Annealed or normalized steel, aluminum alloy, copper alloy, cast iron |
CDH | 120° diamond cone | 1471(150) | 20~70 | Hardened steel, quenched and tempered steel, deep hardening steel |
The Rockwell hardness test is suitable for hardness values ranging from 20-70HRC. If the sample hardness is less than 20HRC, it is recommended to use the HRB scale, as the sensitivity of the indenter decreases with increasing pressure in the conical part.
However, if the sample hardness is greater than 67HRC, it is advisable to use the HRA scale, as the pressure at the indenter tip may become too high and result in damage to the diamond and reduced indenter life.
The Rockwell hardness test is known for its ease, speed, and minimal recoil, making it ideal for testing the surface of finished products and harder, thinner workpieces.
However, due to the small indentation, the hardness value may fluctuate greatly for materials with irregular structures and hardness, making it less accurate than the Brinell hardness test.
The Rockwell hardness test is commonly used to determine the hardness of materials such as steel, non-ferrous metals, and cemented carbides.
Vickers hardness
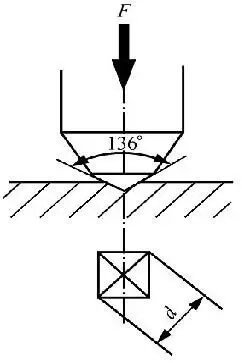
The principle behind Vickers hardness measurement is similar to that of the Brinell hardness test.
A pyramid-shaped diamond indenter with an angle of 136° is used to apply a specific testing force, F, to the surface of the material being tested.
After a specified holding time, the testing force is removed and the hardness value is calculated as the average pressure on the unit surface area of the regular pyramid-shaped indentation, with the symbol HV.

Vickers hardness measurement has a wide range and can measure materials with hardness ranging from 10 to 1000 HV. The recoil is small.
This measurement method is commonly used to measure thin materials and hardened surface layers created through carburizing and nitriding.
Leeb Hardness
The Leeb Hardness Test uses a device equipped with a tungsten carbide ball to impact the surface of the test piece, which then rebounds. The speed of rebound is affected by the hardness of the material being tested.
A permanent magnetic material is installed in the impact device, which produces an electromagnetic signal proportional to the speed of movement of the impact body. This signal is then converted into a Leeb hardness value by an electronic circuit, represented by the symbol HL.
The Leeb hardness tester is a portable device that does not require a workbench. Its hardness sensor is compact and can be easily operated by hand, making it suitable for testing large, heavy or complex geometries.
One of the main benefits of the Leeb Hardness Test is that it only results in light surface damage, making it an ideal option for non-destructive testing. It also provides a unique hardness test for all directions, narrow spaces and special parts.
Hardness Test
The Brinell hardness test measures the hardness of a sample by pressing a steel ball or diamond cone into the surface of the sample and measuring the depth of the indentation. This method is suitable for determining the hardness of materials such as annealed, normalized, quenched and tempered steel, cast iron and non-ferrous metals.
The Rockwell hardness test uses specific procedures and smaller indenters, such as diamonds, to measure hardness, making it suitable for a wide range of materials.
The Vickers hardness test maintains the advantages of the Brinell and Rockwell tests, capable of measuring materials ranging from extremely soft to extremely hard, and their results can be compared.
The specifics of the advantages and disadvantages of the Knoop hardness test are not detailed in the information I found, but it is one of the static testing methods, on par with Brinell, Rockwell, and Vickers.
Webster hardness tester is mainly used to check the mechanical properties of aluminum alloy profiles, but it is also suitable for materials such as copper, brass and carbon steel.
Barcol hardness tester is a kind of indentation hardness tester. The specifics of its advantages and disadvantages are not explicitly stated in the information I found.
Each hardness testing method has its characteristics and range of applications:
- The Brinell hardness test is suitable for various materials, especially annealed, normalized, quenched and tempered steel, cast iron and non-ferrous metals.
- The Rockwell hardness test is suitable for a wide variety of materials, utilizing a smaller indenter for measurements.
- The Vickers hardness test combines the advantages of Brinell and Rockwell tests, suitable for materials from extremely soft to extremely hard, and its results can be compared.
- Knoop hardness test, as one of the static testing methods, is suitable for various materials, but a greater understanding of their specifics is required.
- The Webster hardness tester is particularly suitable for checking the mechanical properties of aluminum alloy profiles, but can also be used for other materials.
- The Barcol hardness tester, as an indentation hardness tester, has a place in material hardness testing.
Hardness Testers
- Micro Vickers Hardness Testing Machine
HM Series:
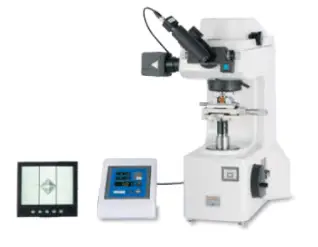
- Vickers Hardness Testing Machine
HV Series:
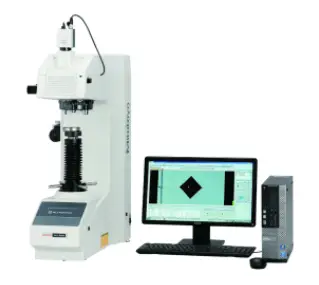
- Rockwell Hardness Testing Machine
HR Series:
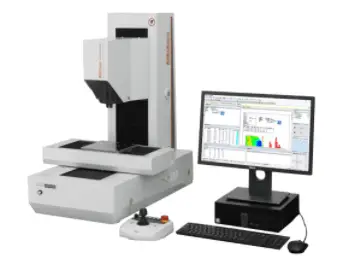
- Portable Leeb Hardness Tester
HH Series:
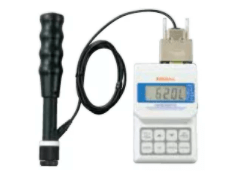
How can the hardness of metal materials be improved through heat treatment?
The hardness of metallic materials can be increased through heat treatment using various methods, including:
Carburizing and Nitriding: These chemical heat treatment methods involve the infusion of carbon atoms (carburizing) or active nitrogen atoms (nitriding) into the surface layer of the metal. This increases the carbon content or abrasion resistance of the surface layer of the metal, thereby increasing hardness and wear resistance. The commonly used carburizing medium is charcoal, while nitriding uses active nitrogen atoms decomposed from ammonia gas when heated.
Quenching: For medium carbon steels and high carbon steels in general, hardness can be improved through quenching. Quenching is a common heat treatment method that involves heating steel to an appropriate temperature and then rapidly cooling it to obtain greater hardness.
Changing grain size and phase composition: Heat treatment affects hardness by changing the grain size and phase composition of the metallic material. This can be achieved through mechanisms such as grain boundary solution strengthening, crystal solution strengthening, and phase transformation strengthening.
Coating technology: The use of coating technology during the heat treatment process of metal materials can prevent significant damage to the metal structure while achieving optimal hardness, ensuring a significant improvement in application results.
Reorganizing Organizational Structure: Heat treatment processing can improve material uniformity and hardness, reorganizing organizational structure and reducing or eliminating non-uniformity. This method can be implemented in several ways depending on specific needs.
Forming a protective layer: The formation of a thin protective layer on the surface of metallic materials changes the original structure of the metal. Compared with traditional quenching methods, this approach effectively increases the surface hardness of the metal and offers the advantage of easy operation.