Observation:
All personnel servicing any part of the press brake must follow safe work practices:
- Make sure all other people are away from the die area (point of operation) while the press brake is being repaired.
- Follow factory machine lockout procedures to prevent operation of the press brake during maintenance or troubleshooting.
- Equipment post-maintenance warning signs.
- Use appropriate personal protective equipment as required by regulatory requirements.
Service personnel may need basic diagnostic tools such as an electrical multimeter to assess electrical control problems and a pressure gauge to assess hydraulic problems.
Maintenance personnel using manual overrides on hydraulic directional valves must proceed with extreme caution to avoid personal injury or damage to dies, limit switches, or hydraulic cylinders due to excessive travel.
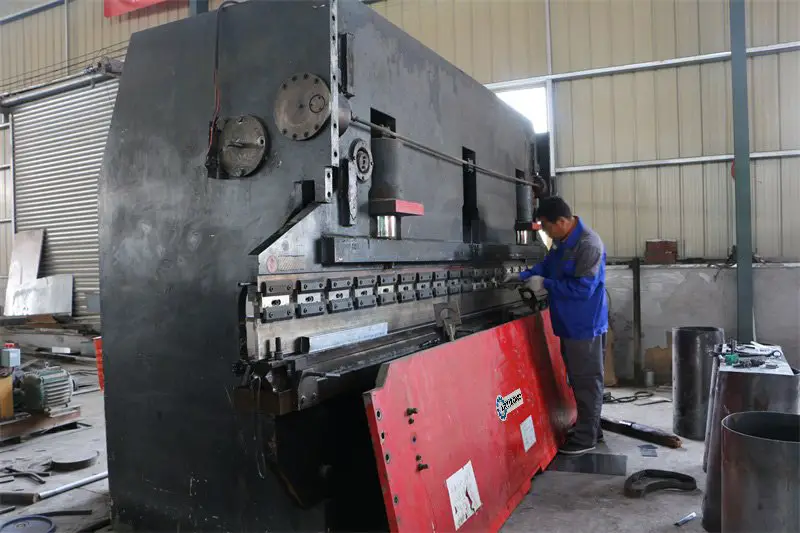
Causes:
The back gauge transmission fails because the drive shaft is disengaged from the timing belt on the timing pulley or the belt is slipping.
Solutions:
This malfunction requires reassembling the chain and timing belt and then checking the electrical part.
55. Excessive parallel misalignment between back gauge crossbeam guide rail and mold centerline.
Solutions:
Such failure requires releasing the synchronous belt from the “X” axis, readjusting it to the parallelism tolerance range, reinstalling the synchronous belt.
56. Loosening of the cylinder and ram connection, causing the bending angle to be inaccurate or the machine to be unable to find the reference point.
Solutions:
This type of failure requires rechecking the tight ram and cylinder connecting nut.
57. The pressureless hydraulic system.
Solutions:
- Check that the proportional relief valve solenoid coil is turned on. If the electromagnetic coil voltage meets the requirements. For the above reasons, please check the relevant electrical parts.
- Check whether the cartridge valve is stuck or the main spool is stuck, as well as whether the wet hole is clogged. If this is the reason, remove the relief valve and clean it.
- three-phase power phase modulation, resulting in motor reversal.
58. Ram speed goes from fast to slow, pause too long.
Solutions:
- Check that the oil surface of the tank is very low, the filler neck has not been flooded. When advancing rapidly, the cylinder chamber fills with liquid and air, which leads to underfilling. For the above reasons, tank oil can be added to the filling tank 5 mm above the filling mouth until it is completely flooded.
- Check whether the rapid forward speed is too fast, causing insufficient filling. For the reasons described above, you can reduce the fast forward speed by modifying system parameters.
- Check whether the filling valve is completely open if it is due to oil pollution, so that the valve spool activity is not flexible and the sticking problem leads to insufficient oil filling. Need to clean the filling valve and reinstall it, make the spool flexible.
59. Ram returns normal, fast forward normal, manual can't slow down, fold weak.
Solutions:
- Check that the reversing valve, which controls the oil circuit, is working properly. In this case, this causes the fill valve to not be closed, so the connected upper chamber and tank fill port cannot create pressure. The reason the valve does not work properly is that it is not energized or stuck.
- Check if the fill valve is stuck, if so, clean the reinstalled fill valve so that the spool becomes flexible.
60. Plunger return speed is too slow.
Causes:
Malfunctions such as high back pressure mainly occur because the filling valve is not open. This phenomenon is exactly contrary to the logic of malfunction 3 above.
Solutions:
This can be resolved by referring to malfunction solution 3.
61. After turning on the CNC press brake pump, the low voltage disconnect switches.
Solutions:
The following checks are required for such faults:
- Check the power outage phenomenon.
- Check whether the blockage of the high pressure filter resulting in the pump motor current is too large.
- Check whether the low voltage switch is too small.
62. After starting CNC press brakes, the reference point cannot be found during return.
Solutions:
- The connecting parts of the grid ruler read head may become loose, causing the read head to not align with the reference point on the grid ruler during the return stroke. In this case, the cylinder has exceeded its stroke and the pump operates under overload. To resolve this issue, press the red stop button on the CNC system to stop the reference point. Reconnect the connector to secure the grid ruler, switch to manual mode and manually lower the ram until it aligns with the bottom die. Then return to the reference point and correct the problem.
- If the operator failed to properly shut down the press brake after the last operation and did not stop the ram in the top dead center position before shutting down the CNC press brake, the ram may be in the upper and lower mold overlapping position during the next startup . This will cause the system to be unable to find the reference point during reference point operation.
- To solve this problem, switch the system to manual mode and manually adjust the ram to the upper and lower mold overlapping position. Then switch to semi-automatic or automatic mode and reposition the reference point.
63. For DNC60 or DNC600 CNC press brake machine, the CNC system did not display, gray-white programming key indicator light flashing.
Causes:
This malfunction is typically caused by the controller operator not immediately and completely clearing unused product programs during the product programming process and instead directly modifying the previous product program.
Repeated occurrences of this behavior can cause the system buffer memory to become full of programs, causing the system program to not function correctly.
Solutions:
To solve the problem, first disconnect the main power to the engine. Then, simultaneously press the “+ +” and “- -” keys on the keyboard. Finally, turn the power back on to return the system to its initial state.
Next, clean the project by entering “1” to indicate the item to be cleaned. After entering the password “817”, press the Enter key to confirm. The screen will display a warning that the operation has been performed. At this point, the steps necessary to complete the project have been completed.
64. “Counting is not accurate” of CNC bending machine grid ruler causes bending angle error.
Causes:
This malfunction mainly results from the cumulative increase in repositioning accuracy errors in the “Y1” and “Y2” axes, leading to an increase in the angular error of the part after bending. This increase in angular error is based on previous errors and is mainly caused by the loss of feedback signal pulses from the grid ruler.
Solutions:
To resolve this issue, remove the ruler from the grid and clean it thoroughly. Implement measures to reduce dust and vibrations. Redesign and reinstall the grid ruler to ensure a reasonable level of installation. If the grid ruler is damaged, it must be returned to the manufacturer for repair or replacement.
65. After programming the product, the safe distance is alarmed for the “X” axis and “R” axis of the rear meter.
Causes:
This type of malfunction occurs mainly because the safety distance settings between the upper and lower molds, as well as the limit positions of the X and R axes, conflict with the programmed positions. To ensure safety, the system will trigger an alarm and prevent operation if these settings are incorrect.
Solutions:
To resolve the issue, reprogram the product or modify the product parameters or mold settings to meet the requirements. This will remove the alarm and allow operation.
66. X-axis and R-axis of the rear meter, an error occurs in the drive motor
Solutions:
To solve this type of fault, first open the electrical box of the CNC press brake. Check the alarm code on the driver display and determine the cause of the alarm by referring to the user manual and immediate alarm code.
Two common alarms are:
- Alarm 16, indicating drive motor overload. Check the flexibility, strength and mechanical limit of the X and Y axis drives. If necessary, resolve any mechanical problems.
- Alarm 22, indicating an encoder feedback signal alarm. This may be caused by poor contact at the “joint”, desoldering or disconnection or signal interference. Check each issue one by one.
67. The computer display location Y1, Y2 does not match the actual location.
Causes:
This type of failure is mainly due to changes in the original reference point of the NC press brake that are not accurate.
Solutions:
To reset the reference point.
68. The positioning of the X, R axis controller does not match the actual positioning.
Causes:
This type of malfunction is caused by a change in the position of the X-axis and R-axis while the machine is turned off. The computer retains memory of the location before shutdown, leading to a discrepancy between the actual and recorded positions of the X-axis and R-axis.
Solutions:
The X axis position of the R axis needs to be reset.
69. The position deviation of Y1 axis and Y2 axis exceeds the allowable synchronization deviation distance, the ram cannot move up and down.
Causes:
This type of failure occurs when the ram is not positioned between the upper and lower mold at the time of stopping, causing the punch to fall. As a result, the actual positions of the Y1 and Y2 axes exceed their limits.
To solve the problem, adjust the actual positions of the Y1 and Y2 axes. The controller must display the current position value. Once the adjustment is made, the press brake can be operated normally.
Solutions:
To solve the problem, increase the data in the CNC press brake controller by 5 mm from its original value. Then switch to manual mode and manually lower the ram. The system will automatically correct the position and return to normal operation.
70. Unequal angle at each end of formed piece
Cause | Solution |
Variation in metal thickness. | Move the ram parallel to compensate for any variation. |
Check the thickness of the material at both ends of the part. Move the ram parallel to compensate for variation in material thickness. | Move the ram parallel to compensate for any tool variation. |
71. Inconsistency in formed parts
Cause | Solution |
The press ram, base and tools are rust-proof coated. | Remove the die set, clean all parts with solvent, reassemble and readjust. |
Tooling does not lie flat on press cover | Check the clearance with feeler gauges. Wedge between press base and tools or mechanically straighten as needed. |
The tools are worn out. | Check the clearance with feeler gauges. Wedge between press base and tools or mechanically straighten as needed. |
72. Each formed part exhibits a consistent angle from end to end, but there is inconsistency from part to part
Cause | Solution |
Press the ram into free fall | Check the fit of the pressure piston forms assembly. |
Disassemble and inspect for damaged or worn landings, spools, springs, or contaminants. | Disassemble and inspect for damaged or worn landings, spools, springs, or contaminants. |
73. Each piece formed exhibits an inconsistent angle from edge to edge
Cause | Solution |
The rocker arm mounting screws are loose. | Locate and retighten. |
The right ram terminal fixing screws are loose. | Locate and retighten. |
The left ram terminal fixing screws are loose. | Locate and, if loose, consult factory service before retightening. |
The connecting rod mounting bolts are loose. | Locate and, if loose, consult factory service before retightening. |
The connecting rod lower self-aligning bearing is worn or damaged. | The lower connecting rod ball bearing is worn or damaged. |
74. Under bending in the middle of the formed part
Cause | Solution |
Remachine tool forming surfaces. Use localized shim practices to compensate for worn areas. | Remachine the forming surfaces of the press base and ram. Use localized shim practices to compensate for worn areas. |
The press base and ram are worn in the center due to the continuous formation of small parts in one location. | The press base and ram are worn in the center due to the continuous formation of small parts in one place. |