The sheet metal bending process is not only crucial for the successful execution of a company's production plan, but also has a significant impact on its economic benefits.
As a result, the safety of this process has attracted increasing attention from both companies and society.
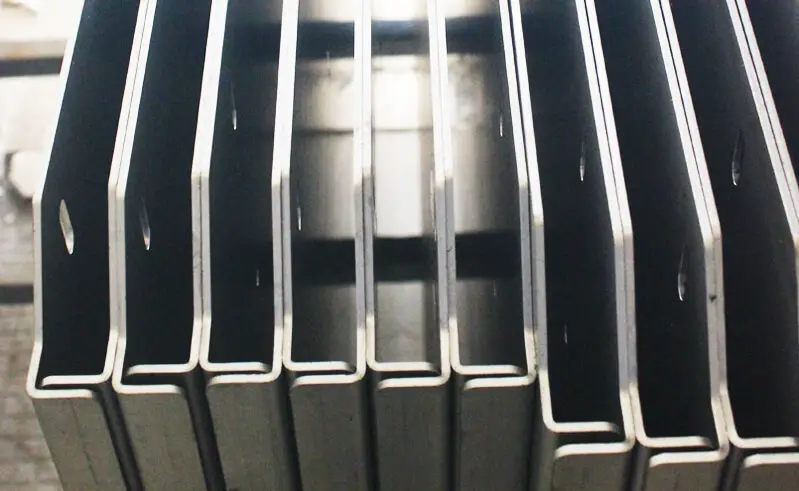
Production management personnel in a company must not only prioritize the safety of operators using the press brake, but also carry out a comprehensive assessment of potential hazards affecting the machine. They must then implement appropriate safety measures to ensure the protection of frontline workers in the workshop.
Dangerous analysis
Throughout the production process, a competent production manager must prioritize employee safety, as it is the most important aspect of production.
Typically, the main sources of hazards during the operation of a bending machine include mechanical and electrical hazards.
Mechanical injury problem
Mechanical injury refers to an accident caused by the unintentional release of mechanical energy. It is one of the most common hazards in the production process and has different origins.
The main sources of mechanical injury include:
(1) The press brake operator should not insert any part of the body between the upper and lower dies, such as placing his hand to adjust the position. This is because the upper die or rear positioning of the press brake may collide with the hand, putting safety at risk.
(2) When bending large or heavy parts, two people need to work together to complete the operation (as shown in Figure 1).
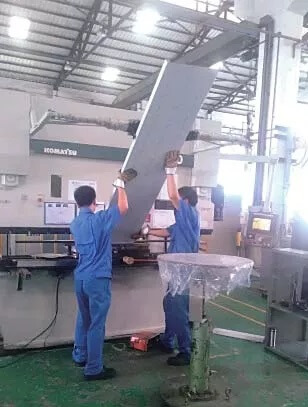
Fig. 1 Parts pushed by two people during bending
At the same time, both operators must simultaneously push the parts to the specified position. When pushing parts, they must work together.
This requires good cooperation skills between operators and between operators and the machine. If not executed correctly, the likelihood of accidents increases and parts could collide with your heads during the descent, threatening your safety.
(3) The press brake operates by pushing the parts manually while stepping on the control switch, which activates hydraulic pressure to move the upper and lower dies, thus bending the parts.
If an operator is not careful when bending a part that is small or smaller than the press brake's upper die, his or her hand may become trapped between the upper die and the part due to incorrect bending techniques.
Figure 2 shows the hand between the upper and lower dies when bending small parts.
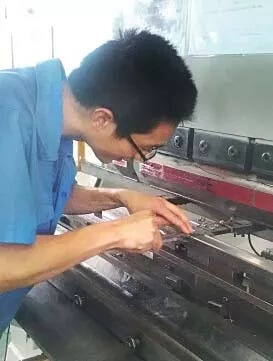
Fig. 2 Hand between upper and lower dies when bending small parts
(4) During the operation of the press brake, it is important to avoid stacking materials too high, which may cause parts to fall and injure workers' legs or feet. Additionally, materials should not be placed too close to the press brake to prevent parts from scratching workers when they turn around.
(5) When two people operate the press brake, if the double pedal is not activated, one person may start stepping on the switch while the other is still adjusting the position of the parts. This can cause parts to scratch the operator or hit the operator's chin.
Additionally, during the process of pushing parts, the sharp edges of some parts can scratch inspectors' hands.
Figure 3 shows the situation of two people stepping on the pedal.
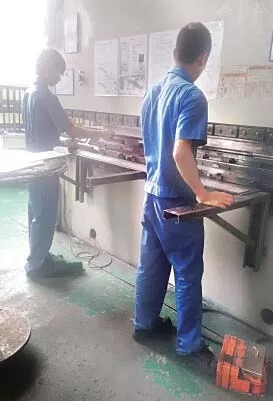
Fig.3 Double foot switch
(6) Bending is an intermediate process that involves cutting and punching sheets in the previous stage and subsequent viscose, welding and assembly processes.
After the previous process is completed, the parts must be lifted for bending or placed on a pallet or cart and transported to the next process after bending is complete.
During the placement, lifting and transportation process, parts may fall and cause injuries or crush people.
Electrical injury problem
Electrical injuries are the most direct threat to the human body among accidents caused by press brakes, and the main sources of electrical hazards include:
(1) Poor quality tools and instruments used by personnel while operating the press brake may result in electric shock accidents. The engine and lighting installations can also emit excessive thermal energy after being turned on, causing burns if not handled carefully.
(2) Over time, some wires on the press brake may become damaged, and if a wire is partially exposed, the operator or maintenance personnel may suffer an electric shock due to the damage.
(3) Operators may also suffer electric shocks if they do not follow regulations when operating electrical equipment. Additionally, the continuous movement of air around electrical equipment can generate static electricity, causing sparks and potentially starting a fire.
Analysis of safety protection in the bending process
Mechanical injury protection analysis
(1) To ensure safety, the press brake operator must take protective measures before starting the operation, such as wearing non-slip shoes, gloves and a safety helmet. In addition, operators in the previous process must remove large burrs on the bent parts.
(2) Standardize the press brake safety production process. Develop procedures for the production of the bending process and transportation of parts, including safe operating procedures for mechanical handling and lifting, safe operating procedures for transportation and storage of parts, and operating instructions for the bending process and other guidance documents for machine operation. This will ensure that operators use tools and machines correctly, thus promoting their own safety.
(3) Ensure the safety of the position of the parts to be bent and the finished parts. Operators must pay attention to maintaining a synchronous relationship between the machine and the worker, and the bending work area must be isolated with guardrails.
(4) Visual management is emphasized in the safety management of the bending process. This means that security management states and methods are clearly visible and easy to understand, so that employees can understand, accept and implement security measures independently.
A source of danger information board (Figure 4) is posted above the bending machine at the bending production site, highlighting possible safety hazards in the bending operation area and warning that improper operation of the bending machine may cause injury to operators or other people who handle parts.
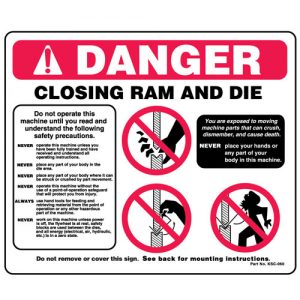
Fig. 4 Kanban of information about the source of danger at the bending production site
Analysis of the sources of danger in the bending operation area highlights that the door panel and other parts are long and heavy, and the speed at which they are lifted and dropped during bending is very fast. The operator's inattention to the presence of people near the press brake is also identified as a contributing factor.
Electrical Injury Protection Analysis
(1) The bending machine operator must wear protective equipment during electrical inspections. Illegal operation is strictly prohibited during inspection. Before carrying out the inspection, it is crucial to carefully check the wires for damage and leaks. If any of these conditions are found, the inspection must be stopped immediately.
(2) When checking the circuit and instrument, make sure the power supply is disconnected. To reduce the risk of inspection, red warning signs should be posted on the surrounding guardrails. During inspection, avoid using temporary power supplies and circuits to prevent leaks and fires.
(3) To increase the effectiveness of visual management, comics and text descriptions of safety precautions for bending operations (Figures 5 and 6) and switch status signs for the photoelectric device of the bending machine should be posted above the machine.
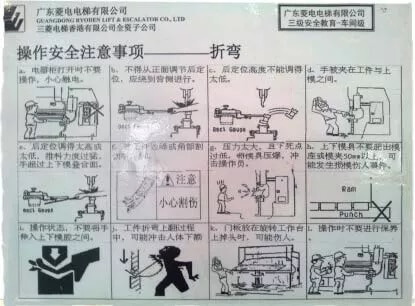
Fig. 5 Safety precautions for bending
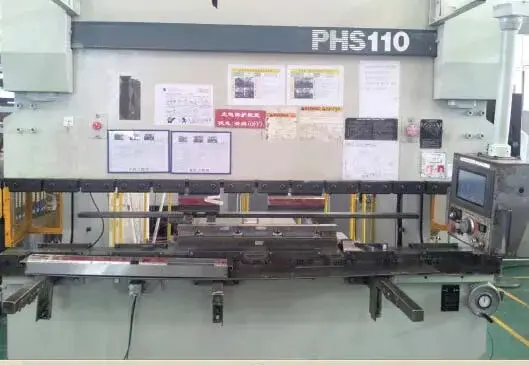
Fig. 6 Gluing position of safety information
Conclusion
In conclusion, there are numerous potential safety risks in the bending production process. It is imperative to have a comprehensive understanding of these sources of danger and take proactive measures to ensure personal safety. Only then can we carry out production and work safely.