What is press brake?
A press brake is a machine that uses a punch and die (general or specialized) to bend cold metal plates into parts with various geometric shapes.
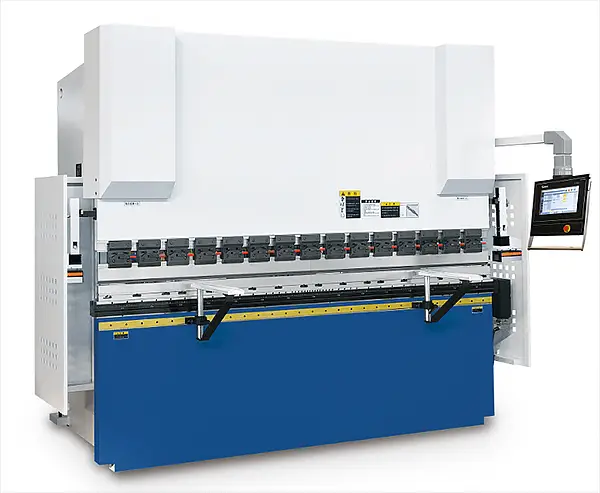
Typically, a press brake employs a specialized CNC system for the press brake.
The coordinate axis of bending machines has evolved from a single axis to up to twelve axes, which are classified based on their functions as follows:
- X-axis: Controls the movement of the backstop in the forward and backward direction
- Y axis: Controls cylinder stroke
- Z axis: Controls the movement of the rear stop in the left and right direction
- R Axis: Controls the movement of the rear stop in the up and down direction
- AP axis: Front support axis
- P-axis: Automatically changes the opening position of the lower die based on the multiple V-mouths of the lower die
- W axis: Mechanical crowning axis.
Related reading: Press brake shaft explained
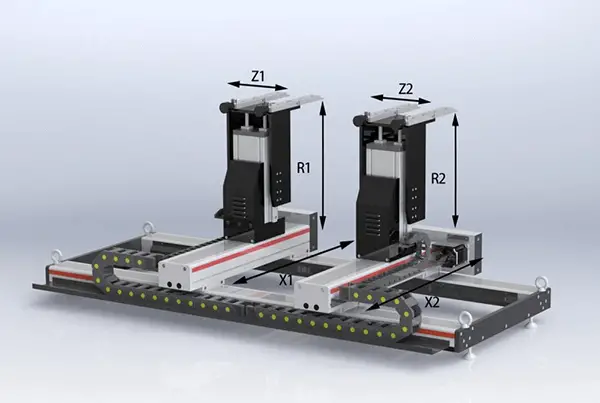
The numerical control system can automatically control the operating depth of the ram, adjust the left and right tilt of the ram, adjust the front and rear and left and right positions of the backstop, control the pressure tonnage, and adjust the speed of the approach of ram.
Related Reading: Press Brake Bending Depth Calculator
The hydraulic press brake can perform effortless actions such as ram downward movement, gradual advance, continuous pressure, return and intermediate stop. It can also complete multiple bends at the same or different angles at the same time.
Hydraulic Press Brake Parts
To knock:
The ram component typically uses hydraulic transmission. It consists of a ram, an oil cylinder and a mechanical stop fine-tuning structure. The numerical control system controls and adjusts the mechanical stop value.
Synchronous System:
The synchronous system mainly uses mechanical design and has a simple structure with stable and reliable performance. Its main components include a torsion shaft, swing arm and knuckle bearing.
Bench section:
The bench section is controlled by a button box and the movement distance is regulated by the numerical control system. It also has travel limit devices installed in the front and rear positions.
Backgauge mechanism:
The backgauge mechanism is normally driven by a motor and its movement is mainly controlled by the NC system.
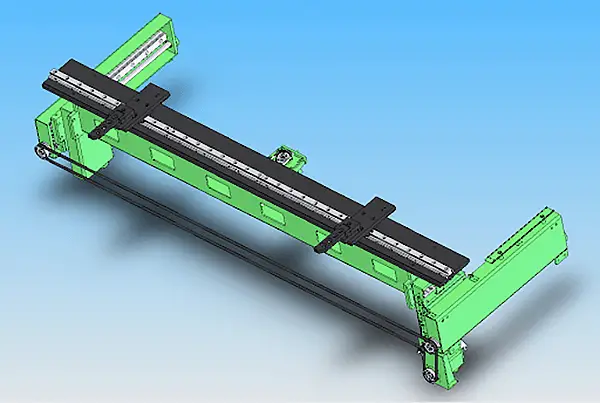
Types of press brake
Press brake mainly refers to a plate bending machine, which is used to bend and shape various metal plates.
This equipment is commonly used for bending sheets and is considered a large machine.
Press brake selection should be based on factors such as intended use, working environment, degree of curvature required, plate thickness and other relevant conditions. Understanding how to correctly select the right type is crucial knowledge.
Press brakes can be classified into different categories based on their characteristics and working modes.
The following is a comprehensive and in-depth introduction to press brake classification:
There are several types of press brakes, which can generally be divided into manual press brakes, hydraulic press brakes and NC/CNC press brakes.
1. Manual press brake
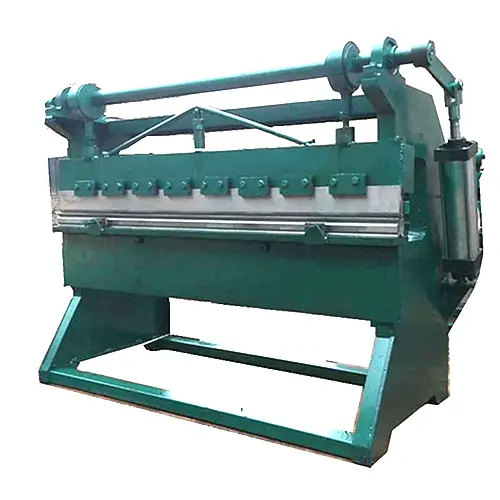
Manual press brakes come in two forms: mechanical manual press brakes and electric manual press brakes.
These types of press brakes are popular both domestically and internationally due to their compact size, low power consumption, high efficiency, large and fast production capacity, wide range of applications and ease of transportation.
The structure of manual press brakes is relatively simple and requires manual labor to operate. They are suitable for processing and manufacturing small parts.
2.H hydraulic press brake
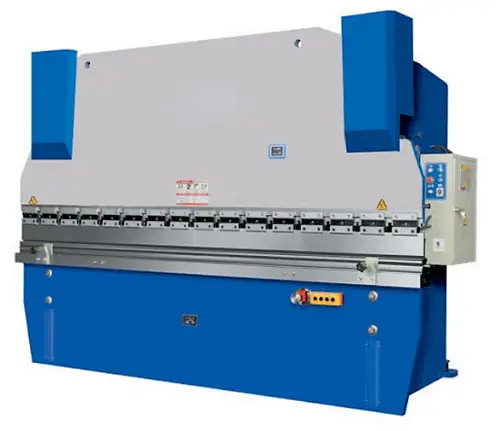
Hydraulic bending machines can be classified into different categories based on their synchronization modes, including torsion shaft synchronous bending machines, mechanical-hydraulic synchronous bending machines and electro-hydraulic synchronous bending machines.
Based on the mode of movement, hydraulic press brakes can be further divided into upward motion press brakes and downward motion press brakes.
Hydraulic press brakes are widely used in the sheet metal industry for applications such as automobiles, doors and windows, steel structures, and V-grooving for sheet metal, among others.
Following are the main features and characteristics of hydraulic press brakes:
- Constructed with fully welded steel frame, with vibration stress relief for high strength and rigidity.
- It employs hydraulic transmission, ensuring stability and reliability.
- Utilizes a mechanical stop and torsion shaft synchronization for high precision.
- The rear stop distance and top slider travel can be adjusted electrically and adjusted manually, with digital displays.
3. NC/CNC press brake
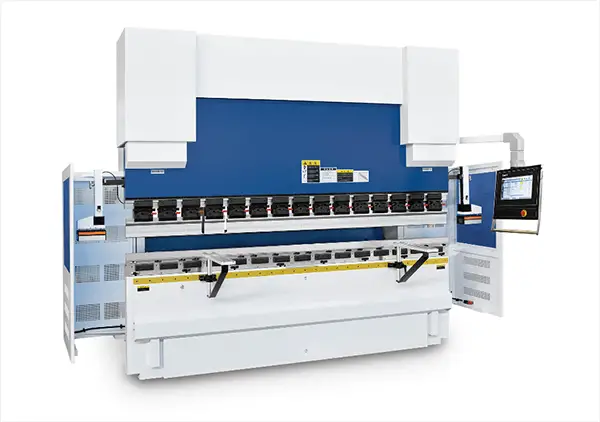
The core of the NC/CNC press brake is the press brake tool used to bend sheets. The tool consists of a support, workbench and clamping plate.
The pressing plate generates force by energizing the coil, thereby trapping the sheet between the pressing plate and the base.
As the clamping method is based on electromagnetic force, the pressing plate can be customized according to the specific requirements of the part, making the operation simple and capable of processing parts with sidewalls.
NC/CNC press brakes are modern, large machines, known for their high precision and preferred by many.
They offer flexible modes of operation and can be connected to two press brakes to handle long sheet metal processing or operated as a single machine to improve utilization, reduce energy consumption and automatically adjust compensation via the CNC system for greater convenience.
There are various models of NC/CNC bending machines, such as G type, F type, WC67k type, etc.
Different types of press brakes have unique performance and application fields, so it is essential to choose the appropriate machinery based on the usage situation and operating environment to achieve optimal performance.
Related Reading: Types of Press Brake Bending
NC press brake vs CNC press brake
What is the difference between torsion shaft synchronous press brakes and electro-hydraulic synchronous press brakes (in reference to NC press brakes and CNC press brakes)?
There are numerous press brakes available on the market today, with a wide range of configurations and systems installed.
Torsion shaft press brakes and electro-hydraulic press brakes are often compared due to their similar functions but different strengths in terms of accessories, systems and prices.
So how do you choose a high-performance, economical and easy-to-use press brake from the many options available?
In the following sections, we will compare NC press brakes and CNC press brakes from multiple perspectives.
Different structural principles
The design principles of the two models are distinct, leading to different structures that ensure synchronization on both sides of the ram.
The NC press brake uses a torsion shaft to connect the left and right rocker rods, forming a torsion shaft forced synchronization mechanism that drives the oil cylinders on both sides to move up and down.
As a result, the NC press brake uses a mechanical forced synchronization mode and the ram parallelism cannot be automatically monitored or adjusted.
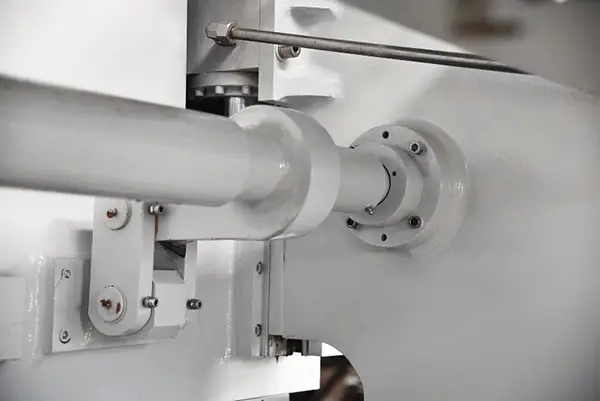
Review the following content and produce the revised content:
“
The CNC press brake is used to install a grid ruler on the ram or base.
The CNC system can analyze the synchronization on both sides of the ram through the information fed back by the grid ruler at any time.
“
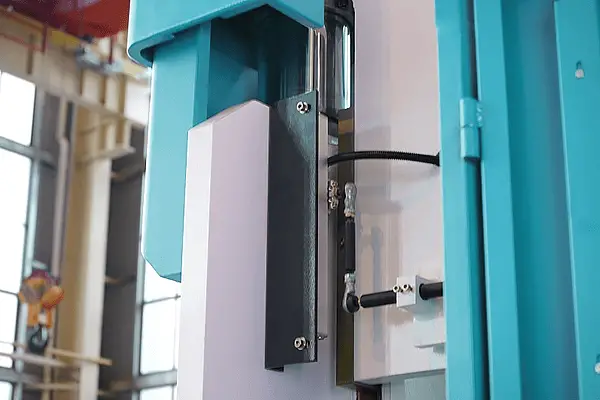
In case of error, the CNC system will make adjustments through the proportional electro-hydraulic servo valve to synchronize the stroke on both sides of the ram.
The numerical control system, hydraulic control valve group and grid ruler form the feedback closed-loop control system of the CNC press brake.
Part accuracy
The parallelism of the ram determines the angle of the workpiece.
The NC press brake maintains ram synchronization by mechanical means, without real-time error feedback and the ability to make automatic corrections, leading to below-average machining accuracy.
Furthermore, it has limited load capacity, as the NC press brake forces the synchronization mechanism to move the oil cylinders on both sides up and down through the torsion shaft, which can deform along the way. time with partial loads.
On the other hand, the CNC press brake controls the timing of the ram through a group of proportional electro-hydraulic valves and receives real-time error feedback from the grid ruler. In case of error, the system adjusts through the proportional valve to maintain ram synchronization and improve machining precision.
R incredible speed
During machine operation, three points determine its operating speed:
(1) Ram speed
(2) Rear stopping speed
(3) Bending steps
The 6:1 or 8:1 oil cylinder is selected for the NC press brake, which is slow, while the 13:1 or 15:1 oil cylinder is selected for the CNC press brake, which is fast.
As a result, the rapid descent and return speeds of the CNC press brake are significantly higher than those of the NC press brake.
When the NC press brake ram descends, it has the functions of fast descent and slow descent, but the fast descent and return speeds are only 80 mm/s and the speed transitions are not smooth. The rear stop operates at a speed of just 100 mm/s.
In contrast, the CNC press brake ram has the functions of fast descent and slow descent, with fast descent and return speeds reaching 200mm/s and smooth speed transitions, greatly improving production efficiency. The rear stop operates at a speed of 400 mm/s.
M mechanical strength
Due to its design, the NC press brake is unable to bend under eccentric loads. Prolonged bending under eccentric loads will result in deformation of the torsion axis.
However, the CNC press brake does not have this problem. The Y1 and Y2 axes on the left and right sides operate independently, allowing bending under partial loads.
Practical operation
Most NC press brakes do not have a CNC system and do not have V-axis compensation.
As a result, when processing based on drawings, it is necessary to rely on the experience of veteran workers to make trial bends. If results do not meet standards, additional testing will be required, resulting in waste and a limited pool of potential high-paying operators.
Although it is possible to add a manual crowning system, the CNC press brake is controlled by a professional CNC system with V-axis compensation, making it easier to operate and requiring less experience from the operator.
The CNC press brake can simulate bends without the need for test bends, simply by correcting the drawings, inserting the steps and sizes, and proceeding directly with the bend.
Numerical control axis
The more control axes an NC press brake has, the less effective it becomes. Typically, it only controls the X-axis and Y-axis.
In contrast, the number of control axes for a CNC press brake is not limited. It can have 3+1 axis or more, with automatic program design capable of meeting high requirements, such as 4+1 axis, 5+1 axis, 6+1 axis, 7+1 axis, 8+1 axis and so on .
Good option all components
The NC press brake can be improved by adding better components such as a quick release clamp, manual crowning, lift stop fingers, ball screws, linear guide rail back stop, oil cooler and light curtain guard .
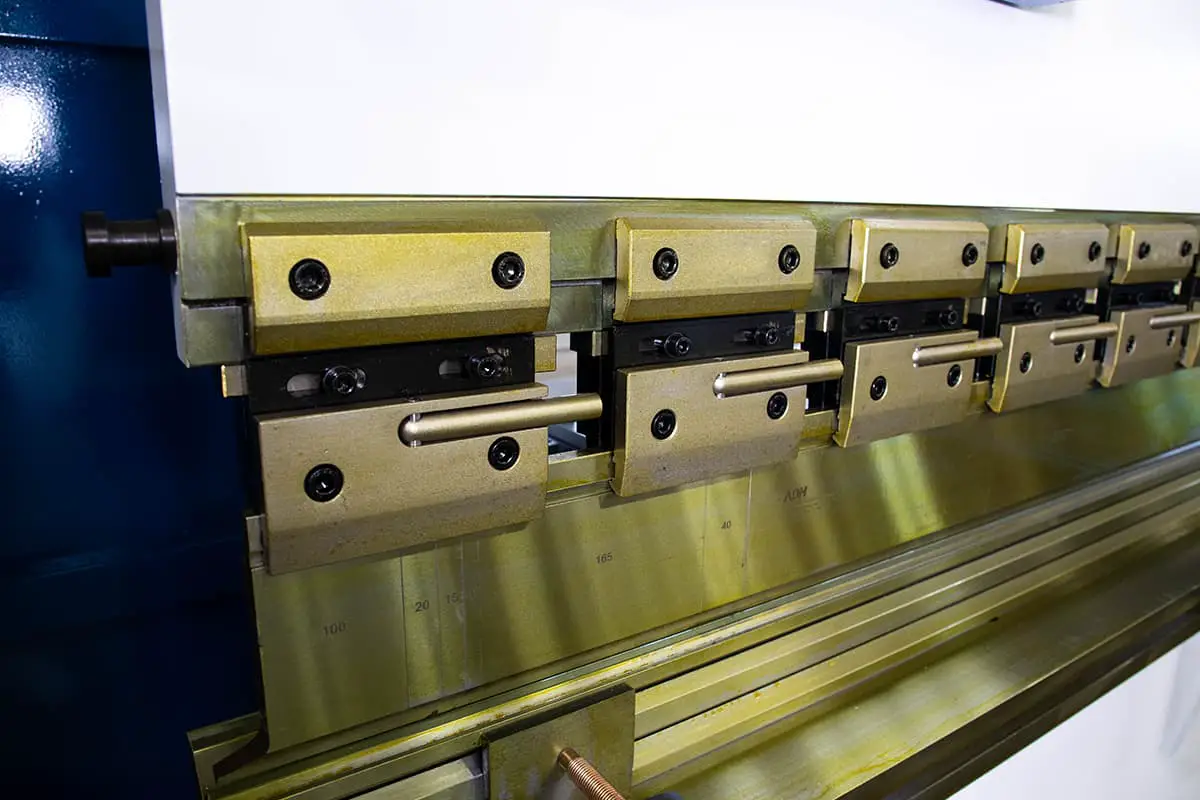
On the other hand, the CNC press brake not only has these basic components, but can also be equipped with a variety of high-quality accessories.
For example, it may have a Tyokko-type or Amada-type quick-release clamp in place of a standard clamp. The lift stop fingers can be operated manually or electrically via an AC motor on the guide rail. The light curtain protection can be replaced with a more sensitive laser protection system.
The CNC press brake can also be equipped with a servo pump control system for energy saving, low noise, faster stamping speed and lower fuel consumption, as well as a manipulator to improve production efficiency, a hydraulic clamping system , a tracking bracket and a laser angle detector.
The main difference between CNC and NC press brakes lies in the existence of a closed feedback loop and CNC crowning system.
See too:
- Open Loop vs. Open Loop Closed Loop
- What is press brake coronation
The distinction between the two should be clear. The NC press brake adjusts cylinder stroke mechanically, while the CNC press brake controls the stroke using hydraulic pressure. The NC press brake is controlled by a balance shaft, while the CNC press brake is synchronized by servo proportional valves on both sides.
The CNC press brake combines the benefits of electrical and hydraulic systems, offering high control precision, fast response speed, large output power, flexible signal processing and the ability to easily monitor multiple parameters. One CNC press brake can have the same working efficiency as two or three NC press brakes.
Advantages of CNC press brake
Left and Right Ram Sync
Synchronization is stable and flexible, and the CNC system includes a function to detect and correct any ram tilt.
Bending angle (depth)
The CNC system can automatically calculate the bending depth based on the selected die angle, opening, R size and sheet metal thickness.
Bending Depth Feedback
The grid ruler, imported from a reliable source, directly measures the positions of both sides of the ram. It also includes a mechanism to compensate for any deformation of the throat, ensuring consistent angles.
Work Table Deflection Compensation
The CNC system can calculate the pressure needed to compensate for the deflection of the work table during the bending process, ensuring uniform angles along the entire length and improving the straightness of the part.
Angle correction
In the case of an error between the programmed and actual forming angles, the user simply needs to enter the error value. The system will compensate and correct automatically.
Stop position
The system can calculate the position of each stop axis based on the bending height and can change steps and correct quickly and easily.
Programming Mode
The system has graphical and data programming options, making program modification and editing quick and convenient.
Expansion length
The CNC system can calculate the unfolding length based on graphical programming and external or internal dimensions.
Interference calculation
The CNC system can automatically determine the best bending process based on programming charts, mold shape and machine tool shape, and will alert the user if there is any bending interference. The user can also manually modify the bending process.
How to choose the hydraulic press brake?
In conclusion, the choice of press brake depends on the specific processing requirements.
The CNC press brake features high precision, real-time error feedback and strong resistance to bias loads on the bending ram. On the other hand, the NC press brake has lower precision, no error feedback and low resistance to deflection loads on the bending ram. Furthermore, the CNC press brake is more complex and expensive compared to the NC press brake.
When making your decision, consider the following factors:
Precision requirements for the workpiece: CNC press brake offers higher precision than NC press brake.
Working hours per day: CNC press brake is more efficient and can reduce working hours and labor costs.
Experience of Machine Operators: NC press brake requires experienced operators, while CNC press brake is easier to operate with its system-controlled operation.
Failure rate: Frequent failures can decrease efficiency and extend construction time. The failure rate of CNC press brake is much lower.
Available Funds: If budget allows, CNC press brake is the best choice. However, if the budget is limited, the NC press brake may be a more viable option.
1 comment
Boa Tarde, você teria o manual do fabricante da dobradeira hidraulica NC PRESS BRAKE MODELO WC67K-125T/3200.
gRATO