1. Laser cutting machine
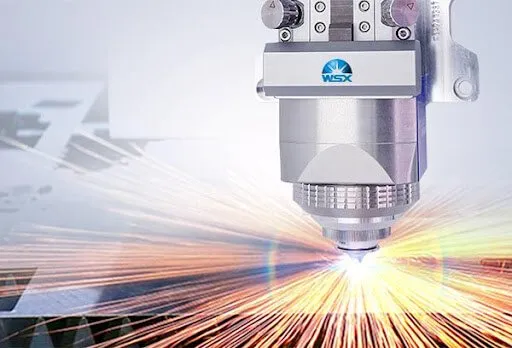
A laser is a type of light generated through the transition of atoms, molecules or ions. Unlike typical light sources, laser light is mainly based on stimulated emission, resulting in highly pure color, intense luminosity and high coherence.
In laser cutting machines, the beam is focused to a small point through the lens in the cutting head. This point has high power density and the cutting head is positioned along the z axis.
During the cutting process, the heat input from the beam exceeds the heat reflected, conducted or diffused by the material, causing it to quickly heat up to the melting and vaporization temperature.
A high-velocity airflow then removes the molten and vaporized material, either in the coaxial or non-coaxial direction, creating cuts in the material.
With the relative movement between the focus and the material, a continuous and narrow gap is formed, completing the material cutting process.
Process parameters (such as cutting speed, laser power and gas pressure) and motion path are controlled by a numerical control system during slot cutting. The slag in the gap is also removed by a pressurized auxiliary gas.
However, the laser beam has a certain divergence angle and has a “conical” shape, which means that its height can change (equivalent to the change in the optical path length of the laser cutter). This results in a change in the cross-sectional area of the beam at the surface of the focusing lens.
Furthermore, light has wave properties, leading to diffraction. Diffraction causes the beam to expand laterally as it travels, which is a common phenomenon in all optical systems and limits their performance.
The tapering of the Gaussian beam and the diffraction of the light wave cause the beam diameter at the surface of the lens to change as the optical path length changes. This leads to changes in focus size and depth, but has little effect on focus position.
During continuous processing, if the focus size and depth change, it may have a significant impact on the processing result. For example, it may result in inconsistent cutting seam width, incomplete cutting, or material ablation under the same cutting power.
This is a disadvantage of the laser cutting machine principle.
2. CNC servo turret punch
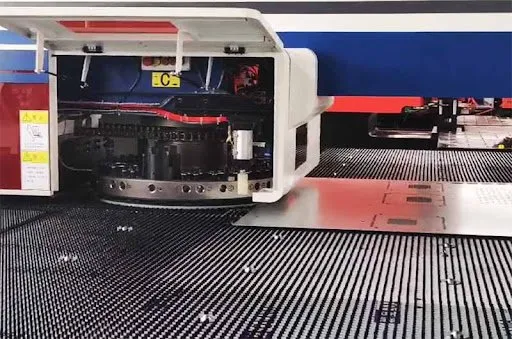
A CNC turret punch can be used to process all types of sheet metal parts and can automatically complete complex holes and shallow elongations in a single operation.
Based on requirements, holes of various shapes, sizes and spacing can be processed automatically.
Large round, square, waist holes and a variety of curved contours can also be drilled with small dies in steps.
Special processes such as louvers, surface stretching, counterbores, flange holes, reinforcements and embossing can also be carried out.
Through simple die combination, compared to traditional stamping:
The CNC turret punch has high machining precision and stable machining quality.
It has a large processing format, with the capacity to complete a 1.5m x 5m format in a single operation.
It can perform multi-coordinate bonding and process parts with complex shapes, and can also be used for shearing and forming.
When machining parts need to be changed, only the NC program needs to be changed, which saves time in production preparation.
The punch itself has high precision and rigidity, allowing for optimal processing conditions and high productivity.
The punch has a high level of automation, reducing labor intensity.
It is simple to operate and with basic computer skills, 2 to 3 days training is sufficient.
CNC turret punch saves mold costs and enables low-cost, short-cycle processing of small batches and diverse products.
It has a wide range and processing capacity, adapting in a timely manner to market and product changes.
Servo turret CNC punch processing mode:
(1) Single Punching: The punching process is completed in one operation, including linear distribution, arc distribution, circumferential distribution and grid hole drilling.
(2) Continuous cutting in the same direction: The partial overlap processing method using a rectangular die can be used to produce long holes and trimming.
(3) Multi-directional continuous blanking: The process of machining large holes using small molds.
(4) Nibbling: Continuous punching of arcs using small round dies in small steps.
(5) Single forming: A unique surface stretching process based on the shape of the mold.
(6) Continuous Forming: Forming processes larger than the size of the die, such as large shutters, rolling ribs and rolling steps.
(7) Array Forming: Machining of multiple identical or different parts on a large plate.
3. Laser cutting versus CNC punching
Both laser cutting and CNC punching are essential processing methods in production and processing.
To choose the most efficient and economical method, it is important to understand the unique characteristics of each one.
Based on my experience, the two methods have the following characteristics and differences:
CNC punch
CNC punching mainly cuts straight lines, square holes, round holes and oblong holes, with a simple and fixed pattern.
It is mainly used to process carbon steel plates and aluminum plates with a thickness of less than 6mm.
CNC punching is not recommended for stainless steel sheets thicker than 2 mm, as the material has high viscosity and hardness, leading to frequent material skipping and tool jamming, as well as high mold consumption.
Overall, CNC punching has a fast processing speed with fixed dies. If a new mold is needed, the development cycle is at least three weeks and the cost is high.
The degree of flexibility is low, removing burrs at the connection point is challenging and the razor joint mark is noticeable.
For parts with a length of less than 500 mm, the machining accuracy is approximately +/- 0.10 mm.
Laser cut
Laser cutting is more flexible and has faster cutting speed and higher production efficiency.
It has a shorter production cycle, no deformation during processing and no need for a mold.
Any shape can be formed accurately in one operation. For parts with a length of less than 500 mm, the machining accuracy is approximately +/- 0.05 mm.
However, the cost of simple laser graphic cutting is higher compared to punching. Slag around the cutting line affects the surface quality.
Special three-dimensional shapes such as rolling ribs, hollow holes and shutters cannot be produced using a laser cutting machine.
Conclusion
In actual production, it is necessary to choose the appropriate processing method based on the part design to obtain the best results.