A long, narrow part is characterized by its large length-to-width ratio and is positioned using its short edge during bending.
The common problem of out-of-tolerance workpieces is often caused by the limited contact size between the positioning edge of the workpiece and the backstop positioning of the press brake machine.
This post introduces a tooling framework designed to optimize the bending and positioning of narrow and long parts, effectively addressing the challenges of difficult positioning and low accuracy.
With the advancements in sheet metal deformation technology, CNC press brake has become a crucial production equipment for cold deformation processing of sheet metal, widely used in the sheet metal processing industry.
For safety and convenience, most press brakes nowadays use rear stop fingers as a positioning device. After simple programming, back stop articulation, single action and other functions can be achieved, meeting the processing requirements for bending parts of various shapes.
However, the positioning of the back stop used in CNC press brakes also has its limitations. When the width of the positioning edge of the workpiece to be processed is too narrow (such as in the case of a narrow and long workpiece), the limited contact size between the workpiece and the back stop finger leads to problems such as inaccurate positioning size, displaced bend position and design bend line, resulting in poor quality products, frequent rework and repairs, and significant waste of materials, energy and labor.
Bending deformation mechanism
In production, it is often necessary to bend a part (steel plate) at a specific angle, where the bending radius at the bending position is small.
This process is known as bending.
Bending is the process of using a punch and die to apply an external force to sheet metal, shaping it into a specific angle or shape.
The bending deformation of the part is divided into several steps.
Initially, the material is in a state of free bending.
As the upper punch is pressed, the material gradually approaches the surface of the lower die.
Then, as the punch continues to press, the bending area of the material becomes smaller until it contacts the punch at three points.
When the punch reaches the lowest point of its stroke, the material is completely in contact with the punch.
During free bending, the inner fibers of the material shorten due to longitudinal compression and the outer fibers lengthen due to longitudinal tension, resulting in transverse shortening due to constant volume during plastic deformation.
Therefore, for workpieces with narrow width, the cross section will have a slight fan-shaped appearance after bending.
For wide plate parts, the bending cross-section will not show any noticeable deformation.
Curvature positioning
Basic positioning of the press brake
The CNC press brake typically uses stop fingers for positioning the workpiece.
The basic principle is that before bending processing, a bending program is prepared and the shape of the part is entered into the machine controller. The machine then calculates the bend line position of the workpiece, and the CNC system controls the servo motor to move the two rear stops to the required bend positioning position through the high-precision lead screw.
The operator only needs to align the positioning edge of the workpiece with the stop finger of the press brake to complete the positioning process.
At this point, the center line of the press brake's lower die represents the bend line of the part.
The positioning state of the part is illustrated in Figure 1.
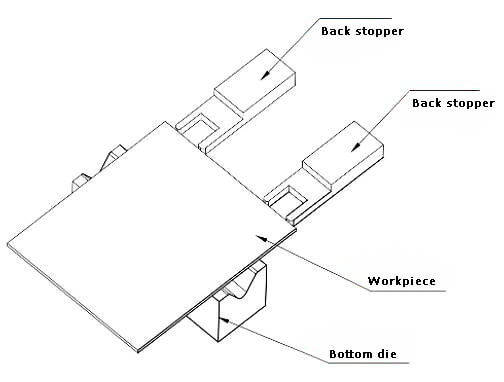
Fig. 1 Positioning of the part
Limitations of the press brake positioning device
During the production process, it was discovered that using the typical backstop positioning employed by today's press brake machine can result in difficulties in aligning the workpiece with the backstop if the size of the positioning edge between the workpiece and the back stop is too short.
As illustrated in Figure 2, a small shift from left to right of the workpiece can cause incorrect positioning, resulting in excessive workpiece discard or an uneven edge size during bending.
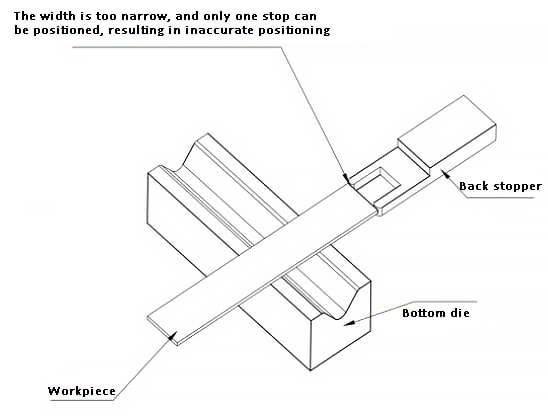
Fig. 2 Positioning of narrow and long parts
Operators are required to repeatedly align the workpiece to achieve the desired primary forming effect; however, this often leads to subpar results and has a significant negative impact on production efficiency and product quality.
Optimization of positioning when machining narrow and long parts
Positioning Optimization Device Structure
Considering the limitations of the positioning device of the CNC press brake, a new positioning optimization device was designed and is shown in Figure 3.
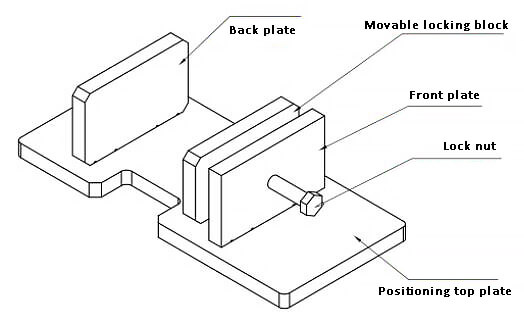
Fig.3 Positioning optimization device
The back plate is used to close the lower die side of the press brake. The movable locking block is used together to securely lock the device to the bottom die of the press brake. The faceplate serves as the location for screw installation, and the locking screw fixes the movable locking block to the bottom die. The upper positioning plate is used to position the workpiece.
Use of positioning optimization device
To use the positioning optimization device mentioned above, it must first be aligned and fixed on the bottom die of the press brake and its condition must be checked using a square.
When positioning the workpiece, the end of the workpiece should be positioned close to the back stop of the press brake, while the side of the workpiece should be positioned using the positioning optimization device, resulting in accurate and stable positioning of the workpiece of work, as illustrated in Figure 4.
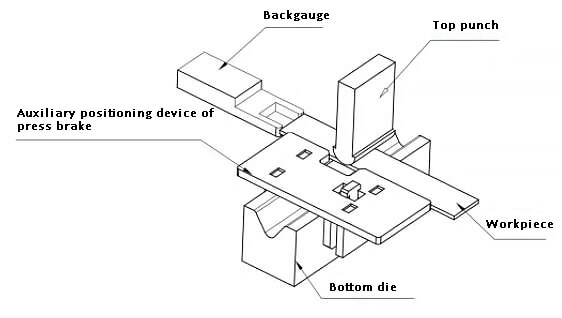
Fig. 4 Combination of rear retention material and positioning aid
Positioning auxiliary device implementation effect
(1) Better production efficiency:
Prior to the use of this device, narrow and long parts often required repeated measurements to ensure accurate positioning, leading to large errors. However, with the use of this device, the operator can easily locate the part to be processed, significantly improving production efficiency and reducing the production and processing time of a single part by more than half.
(2) Better product quality:
Prior to the implementation of these tools, the defect rate of narrow and long parts remained high, and problems such as over-tolerance scrapping and irregular bent edge size were prevalent. However, with the use of the optimization device, these problems caused by inaccurate positioning during bending no longer occur, leading to a significant improvement in product quality.