Introduction to tube bender
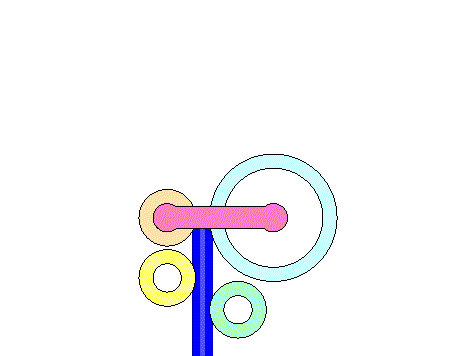
A pipe bender refers to a machine used to bend pipes, which can be classified into numerical control and hydraulic types. These machines are widely used in various industries such as power construction, railway and highway construction, bridges, ships and more.
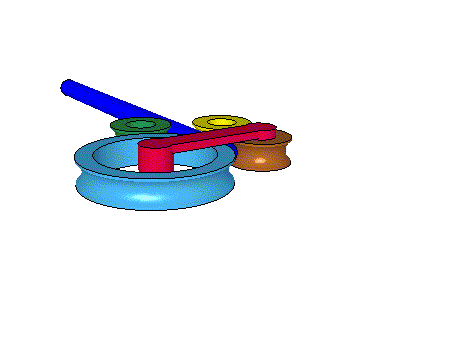
Unlike plate bending machines, tube bending machines are mainly used to bend steel pipes. They are commonly used in power construction, railway construction, boilers, bridges, ships, furniture and decoration, and other pipeline laying and construction applications.
Pipe benders are also considered an important equipment in the pipe machinery industry. They offer multiple functions, have a well-designed structure and are easy to operate.
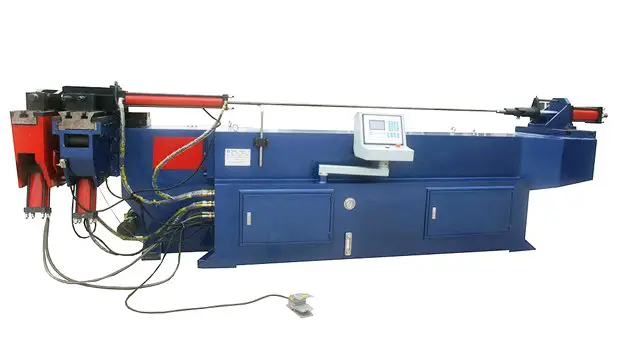
There are two pipe bender bending methods:
1. Cold bending including hydraulic pipe bender, electric pipe bender and three-roll bending machine;
2. Hot bending The representative model is the medium frequency tube bender.
Working principle of tube bending machine
According to the tube bending method, it can be divided into pressure bending, roll bending, press bending and circular bending. Of these, circular bending is relatively easy to automate, so currently, bending machines are mainly designed for this method. The principle of the bending process is illustrated in a diagram.
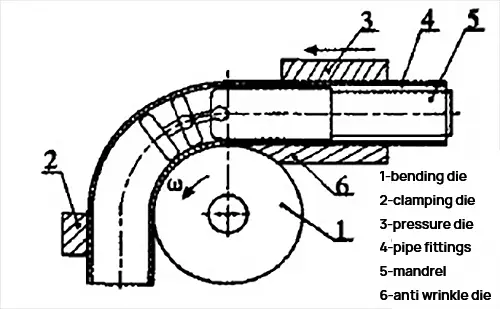
Bending speed of tube bending machine
The main effect of bending forming speed on forming quality is:
If the speed is too fast, it is easy to cause flat spots on the curved parts of the pipelines, and the roundness may not meet the requirements, resulting in pipeline binding and breakage.
If the speed is too slow, it is easy to cause wrinkling of the catheter and slippage of the pressure block, and the large tube may form the channeled part of the sink.
To determine the maximum bending speed of the machine, the best final bending speed should be 20-40% of the pipe bender's maximum bending speed.
The standardization of the bending radius of the tube bender
The radius of curvature must be chosen to achieve “one tube and one die” and “multiple tubes and one die”.
When a tube has only a few bending positions or several bending angles, there can only be one bending radius because the tube bender module cannot be changed during the bending process. This is known as “a tube matching a matrix”.
However, when using “one die for multiple tubes”, tubes with the same diameter must use the same bending radius, and the same modules must be used to bend tubes with different shapes. This helps reduce the number of modules required.
Bent tube mandrel and its position
In the bending process, a mandrel is used to support the inner wall of the pipe's bending radius and prevent its deformation. Without the mandrel, it is difficult to guarantee the quality of tube bending.
There are many types of chucks, including cylindrical chucks, single-head, double-head, triple-head and four-ball head universal chucks, as well as single-ball and multi-ball orientation head chucks.
The position of the mandrel in the tube forming process has a certain influence. In theory, the tangent of the mandrel should be at the same level as the tangent of the tube bending die. However, a large number of experiments have shown that advancing the mandrel 1-2 mm is better and the bend quality is ideal at this point.
Of course, if the chuck is moved too much, it may cause the so-called “goose head” on the outer wall of the curved part.
How to install the CNC automatic pipe bender mold?
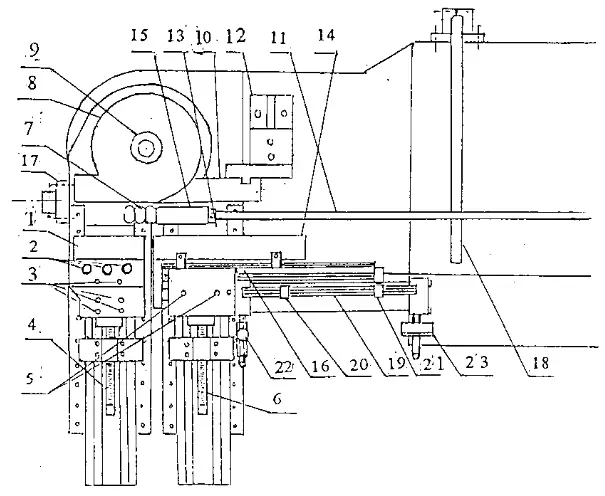
- clamping die adjustment screw
- chuck rod beads
- anti-wrinkle board
- chuck shank fixing nut
- guide mold base
- auxiliary push limit sliding seat groove plate
- auxiliary speed regulating valve
- pressing die sleeve fixing screw
- bending die
- chuck rod
- guide mold
- swing seat
- auxiliary pushing front limit
- auxiliary pressure gauge
- pressure die sleeve adjustment screw
- fold lock and mold cover
- anti-wrinkle board seat
- chuck
- retaining bar
- auxiliary pushback limit
Lock the bending die and cover (9) clockwise, release it and remove it. After replacing the required bending wheel die, lock the bending die and cover.
Installation of the main clamping matrix
To replace the required fixture die, first remove the pin shaft (2) from the main fixture die, replace it with the desired fixture die, and insert the pin shaft. Then loosen the fixing screw (3) of the fixing die base, operate the main clamp fixing using the manual mode screen, turn the fixing die adjusting screw (4) and move it forward until that the clamping die is fixed to the bending die. . Then press the main clamp to loosen it and turn the clamping die adjustment screw forward 1/3 or 1/2 turn. Finally, lock the fixing screws on the base of the fixing matrix.
Installation of the guide clamping matrix
To install the guide die, follow the same method as above, but adjust the clamping force so that it is slightly looser than that of the main clamping die.
If the tube becomes wrinkled during bending, move the pressing die sleeve adjustment screw forward about 1/4 turn and try bending again until there are no wrinkles.
During the bending test, it is important to ensure that the forward speed of the auxiliary push is synchronized with the bending speed.
Installation and adjustment of the chuck rod and chuck cylinder seat
To install the chuck string (7), screw the chuck shank (11) into the chuck shank (15) and connect the chuck to the chuck barrel cross joint.
The general adjustment method is to ensure that the front end of the mandrel shank exceeds the center tangent point of the bending die by 2-5mm (depending on the diameter of the bending die; the larger the diameter, the greater the distance beyond the tangent point , and the smaller the diameter, the opposite).
The chuck cylinder seat must be installed on the chuck cylinder guide rail, and the chuck cylinder guide rail must be equipped with a scale.
The pointer indicates the radius of the bending die, so if the bending die is replaced, the chuck cylinder seat must be adjusted accordingly.
Anti-wrinkle device installation
The wrinkle-resistant plate (10) is fixed to the wrinkle-resistant seat (12), with the arched seat of the wrinkle-resistant plate close to the bending die (8). The front end should be as close to the center of the wheel die as possible, and the rear end of the wrinkle-resistant plate should be parallel to the guide die with a difference of 1-2 degrees to reduce the friction between the wrinkle-resistant plates. plate and workpiece.
Handling and installation of pipe bender
Handling:
The entire machine tool can be lifted by running a steel wire through the bottom of the machine tool.
Cotton thread or fabric should be placed at the contact point between the wire rope and the machine tool to avoid damaging the surface of the machine body.
During handling, moving parts must be secured to avoid movement and collisions.
Installation:
The machine tool must be installed directly, and the equipment level can be adjusted by adjusting the damping sizing block on the base of the machine tool.
The position of the oil cooler in relation to the machine tool must be determined according to the actual operating position.
Preparation for commissioning:
- Before starting, the operator must carefully read the instructions and be familiar with the safety precautions, performance and operating specifications of the machine tool.
- Connect the cable between the operation box and the host.
- Add hydraulic oil to the hydraulic oil tank up to the center line of the oil level gauge.
- Add No. 20 mechanical oil to the rotating body and gear case to the center line of the oil level indicator.
- Inject lubricating grease into the linear guide rail sliding block and several cups of oil.
- Check whether there are any foreign bodies in and around the moving track of moving parts.
- After the power supply is connected, press the hydraulic motor start button (motor) and quickly press the emergency stop button (fstop), and observe whether the direction of the motor is in accordance with the direction mark. If not, adjust the power wiring and try again.
- Check the pressure of the hydraulic system (after starting the hydraulic motor, press the core of the electromagnetic valve with the help of appropriate tools), and the value indicated on the pressure gauge must be less than 14 MPa (generally adjusted when leaving the factory).
Pipe Bending Machine Applications
Pipe bender application in power generation equipment manufacturing industry:
In a context of an increasingly tight global supply of resources and rising oil prices, the demand for energy production equipment has become increasingly obvious.
In the manufacturing process of power generation equipment, the cost spent on the CNC pipe bender alone is very considerable.
Application of tube bending machine in mold making industry:
In the pipe bender mold manufacturing process, NC pipe bender mold is used in almost every link, such as forming mold, hot mold, cold mold, plastic mold, etc.
In addition, automobiles, tuning trains, general machinery manufacturing and furniture manufacturing have become the main users of the CNC tube bender mold industry.
Pipe bender application in aerospace industry:
In this industry, tube benders are generally used to bend aircraft structural parts; These structural parts are generally large in volume, and aluminum alloy has been widely used in the past.
With the expansion of the application fields of titanium alloys and composite metal materials, the requirements for NC tube bending machines are becoming greater and greater.
What is the price of the tube bender machine?
The configuration of the hydraulic pipe bender plays an important role in determining the price. There is a saying that the price is equal to the commodity. Each price has its own reasons and requirements.
Users who demand high bending precision and efficiency from hydraulic pipe bender are very concerned about quality. Quality is determined by the internal configuration of the equipment.
Some customers are very concerned about price, but they also have certain quality requirements. It is a challenge to balance the trade-offs between them.
At present, most pipe benders on the market range from 3,000 to 100,000 RMB, and the specific quotation depends on the wall thickness and bending radius of the material.
How to use the tube bender machine?
Machine tool adjustment:
To obtain the desired geometric shape for the bent tube, select the mold based on the outer diameter of the tube connection, wall thickness and bending radius, and then adjust the corresponding parts.
- Bending angle:
Enter the required angle on the operation screen according to the user's needs (refer to the manual of the electrical appliance).
- Adjusting the sliding plate clamping and reinforcing mechanism:
The pipe clamping and strengthening of this machine tool adopts a connecting rod force increasing mechanism.
To ensure the self-locking of the clamping state, first loosen the screw rods of the tube clamping mechanism and the reinforcement mechanism. Then, in the manual state, the two mechanisms are in the clamping position, and finally tighten the screw rods.
The speed of the sliding block can be adjusted by the one-way butterfly valve to synchronize it with the main shaft.
- Adjust the rotation part of the cross screw rod based on the selected tube and mold to make the center line of the sleeve coincide with the center of the mold elbow.
- Tailstock adjustment:
First, adjust the tailstock so that the center of the core rod coincides with the center of the die elbow, and then adjust the screw rod on the tailstock piston rod so that the core head extends into position appropriate.
Machine tool idling:
- In manual mode, press the action button to actuate the corresponding oil cylinder and observe whether the action is normal without crawling, pulsation and oil leakage.
- Use the inching mode to move the carriage along the guide rail, rotate the rotating sleeve, and observe its flexibility and accuracy.
- Activate the clamp clamping cylinder to observe the movement of its sliding sleeve and the reliability of the clamping.
- Select several different angles to observe the coordination and consistency of each mechanism's actions in automatic mode. After checking that all items are normal, the equipment can be put into normal use.
Tips for using tube bender machine
The following points should be noted after purchasing the pipe bender:
Before operating, check whether the machine's lubrication points are lacking oil, whether the safety protection device is reliable, and whether the moving mechanism is loose. A person must confirm before starting the operation.
Connect the elbow oil pump and check that the system pressure is within the specified range. If the pressure is too high, it can damage hydraulic components and waste energy. If it is too low, it will affect the work.
Adjust the required position and angle of the parts and position the parts to the required length.
Adjust the vertical lifting guide rail so that the pressing cylinder can firmly clamp the iron pipe.
Make sure the clamping die pressing cylinder can clamp the iron pipe.
During normal operation, place the workpiece into the bending die, contact and position the front end, and press the foot pedal to complete.
After completing the work, turn off the power and perform proper cleaning and lubrication.
In case of emergency when operating the pipe bender, press the emergency stop button, turn the rotary switch to the manual position and restart it manually. In case of failure, report for repair in a timely manner.
Pipe bending machine maintenance
Eight methods for pipe bender maintenance:
Method 1:
When operating the pipe bender, it must be operated strictly in accordance with the operating regulations (key points).
Regular maintenance of machinery is required. Maintenance personnel must be qualified through education and training.
Method 2:
The pipe bender must be kept clean and unpainted parts must be coated with anti-rust grease.
Check whether the pressure of each oil pressure system is normal.
Method 3:
Before starting the pipe bender, lubricating oil must be added regularly at fixed points and quantitatively in accordance with the requirements of the lubrication table.
The oil must be clean and free of sediment.
The oil pipe and flexible arm line must not touch the ground.
Method 4:
Regularly check and repair the switch, fuse and handle to ensure their reliable operation.
Regularly check whether the hydraulic oil in the oil tank reaches at least 80% of the oil level gauge.
Method 5:
The lubricating oil in the engine bearing must be replaced and topped up regularly, and the engine operation must be checked regularly.
The temperature index of the oil level gauge must not exceed 60°C.
Method 6:
Regularly check the V-belt, handle, button and switch for damage. If they are significantly worn, they must be replaced immediately.
Regularly add lubricating grease to the gear position between the transmission gear and the rack.
Method 7:
It is strictly prohibited for non-designated personnel to operate the equipment. In general, people should get off the machine and stop.
The sliding or rotating part must be lubricated regularly.
Method 8:
Lubricate and clean the pipe bender 10 minutes before work every day.
When operating below 5°C, pay attention to puddles and do not let them freeze.
Do not place magnetic objects near the servo motor or strike them.
When cleaning the LCD, turn off the power first and do not clean it with liquid detergent or liquefied steam.
Do not place the machine in places where rain or moisture leaks.
Tube Bending Machine Troubleshooting
If oil leakage is found in the oil cylinder, confirm the need to replace the sealing ring.
If the machine pressure is insufficient, check whether the oil level in the oil tank is sufficient and whether the oil temperature is too high.
When the proximity switch is not detected, the screen will show the corresponding cause of the failure. Use the displayed fault information to locate the problem for maintenance and troubleshooting.
In the case of an inaccurate angle, check whether the gripper cylinder moves forward and is in place, or check whether the corresponding gripper is too large.
If the servo does not rotate or the servo motor does not power during operation, check the servo driver for a fault code. The most common failure is a momentary low voltage. If the above conditions occur, turn off the main power supply first and restart it after 30 seconds. If this cannot be resolved, notify the company. Do not disassemble and repair without authorization, as you will be responsible for the consequences.
If the bend angle is not correct, check that the encoder coupling fixing screw is loose and that the final slow bend has a lead-in angle.
If any oil pressure action does not respond, check whether the corresponding solenoid valve is abnormal.
Best tube bending machine suppliers/manufacturers
You can read Top 16 Tube Bending Machine Manufacturers to know more details.
How to choose the right tube bending machine?
First, the diameter range of the elbow pipe should be determined according to the actual production situation.
Some hardware processing factories use tube benders for various tube fittings, but each tube bender has its own limitations, and its bending capacity is limited by its own parameters.
Secondly, it is necessary to determine the bending parameters of the largest pipe connection that falls within the scope of bending, including:
- Pipe fittings material (steel pipe, stainless steel pipe, aluminum pipe, etc.)
- Pipe section (round pipe, square pipe, angle iron, etc.)
- Tube outer diameter
- Tube wall thickness
- Radius of curvature (referring to the primitive diameter of the tube) and other parameters.
Finally, provide these parameters to manufacturers. They will typically recommend the model you need based on your parameters.