Austenitic stainless steel is one of the main materials used in nuclear reactor structures, which contain a large number of welded parts.
A small amount of δ ferrite in stainless steel welds can improve the strength and intergranular corrosion resistance of the weld and prevent hot cracking in welding. However, too much δ ferrite will cause embrittlement in the σ phase and selective corrosion in the δ phase.
δ-ferrite content is one of the important technical indexes for the development and application performance evaluation of austenitic stainless steel welding materials.
At present, the commonly used methods to determine the δ ferrite content in austenitic stainless steel welds are metallographic method, chemical method and magnetic method.
The metallographic method calculates the area ratio by directly observing the δ ferrite in the metallographic sample and then calculates the volume fraction. This method is destructive and requires a sufficient number of measurement points to obtain data with high reliability, which increases the detection cost.
The chemical method can indirectly obtain the ferrite content δ (mass fraction) by calculating the nickel equivalent and chromium equivalent in the material and comparing the empirical diagram. The Schaeffer diagram, the Delong diagram, and the WRC-92 diagram are three diagrams commonly used in chemical methods today. The Schaeffer diagram was the first applied, but it did not consider the influence of nitrogen and copper. The Delong diagram includes nitrogen as the austenite-forming element and improves the accuracy of the curve. The WRC-92 diagram also considers nitrogen and copper.
The chemical method also has some problems, such as the accuracy of the alloying element content, which directly affects the calculation accuracy of the ferrite content δ, and the nonlinearity of the effect of alloying elements on the ferrite content δ, which leads to a certain deviation between the measured value and the actual value.
The magnetic method determines the δ ferrite content by measuring a certain magnetic physical quantity related to the δ ferrite content. However, this method is greatly affected by the principle of the measuring instrument, and if the content or morphology of δ ferrite in the material is uneven, the reproducibility and accuracy of the results will be poor.
The magnetic method is easy to operate and can carry out on-site non-destructive testing, which is commonly used. In actual detection, one or two methods are generally selected for measurement.
Researchers from the Key Laboratory of Reactor Fuels and Materials of China Institute of Nuclear Energy Research and Design simultaneously used the above three methods to measure the δ ferrite content of the surface layer of austenitic stainless steel for nuclear power, and compared and analyzed the differences in measurement results obtained by different detection methods.
1. Test content
1.1 Test materials
The research object is a 308 stainless steel cover with a sample size of 50mm × 25mm × 10mm. Its chemical composition meets the specifications described in ASTM A276-2006 for stainless steel bars and profiles.
1.2 Test patterns
Metallographic tests were carried out in accordance with standards GB/T 1954-2008 for measuring the ferrite content of chromium-nickel austenitic stainless steel welds and GB/T 15749-2008 for quantitative metallography.
In addition to existing detection methods, an analysis of the chemical composition was carried out using the Schaeffler and WRC-1992 diagrams to calculate the δ-ferrite content.
To measure the number of ferrite in the weld metal of chrome-nickel austenitic stainless steel, the magnetic method was used following the guidelines of GB/T 1954-2008 and JB/T 7853-1995.
1.3 Test equipment
The metallographic method used for detection and analysis used the Olympus GX71 metallographic microscope and its TIGER3000 metallographic image analysis system.
In terms of chemical analysis, a carbon/sulfur analyzer was used to detect carbon and sulfur, a spectrophotometer was used to detect silicon, phosphorus and boron, and an inductively coupled atomic emission spectrometer was used to detect other metallic elements.
As for the measurement of ferrite content δ, it was read directly by the ferrite measuring instrument during the magnetic method.
2. Testing process and results
2.1 Metallographic method
There are two main metallographic methods used to measure δ-ferrite content: the standard sample atlas contrast method and the measurement method. Both methods can be used to measure the δ ferrite content in the surface layer of 308 stainless steel.
2.1.1 Map comparison method
According to the GB/T 1954-2008 standard, the metallographic sample is prepared and observed under a microscope. A relatively uniform area of ferrite distribution δ is then selected for photography, as shown in Figure 1.
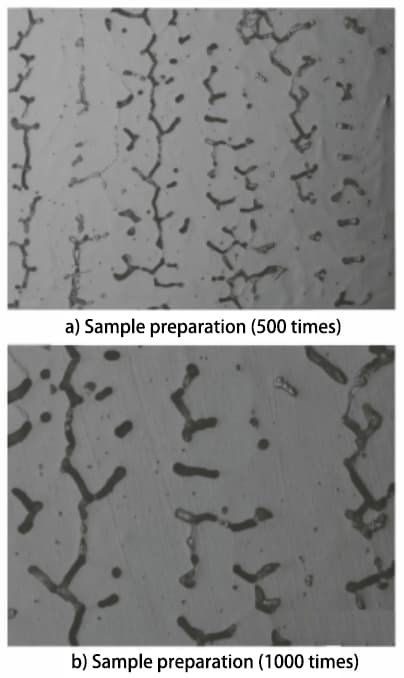
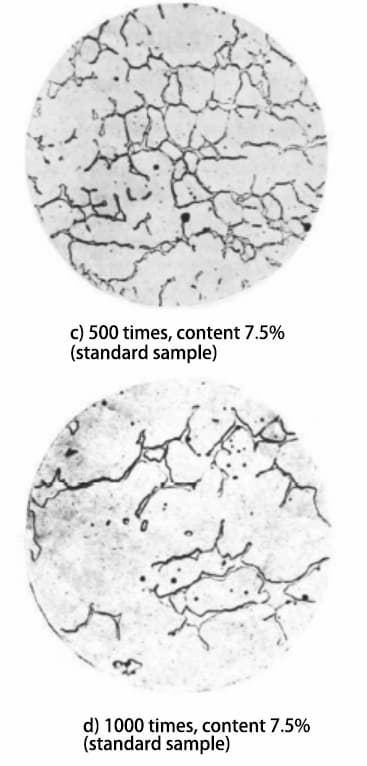
Fig. 1 Microstructural morphology of prepared and standard samples
According to the specifications described in the GB/T 1954-2008 standard, the microstructure of the prepared metallographic sample must be observed with a magnification of no less than 500 times. Microstructures of the prepared sample at 500 and 1000 times magnification were obtained and compared with the microstructures of standard samples at the same magnifications. Based on this comparison, it was determined that the δ ferrite content in the sample is between 7.5% and 10%.
2.1.2 Measurement method
The GB/T 15749-2008 standard is a national standard that applies to the determination of phase volume fraction in various alloy microstructures. It includes a variety of phase content calculation methods, such as grid number point method, grid section method and line segment calibration method (including four-line method, eight-line method, etc.).
Compared with the metallographic secant method in GB/T 1954-2008, the methods described in GB/T 15749-2008 have more dividing lines, a larger coverage area, and greater accuracy.
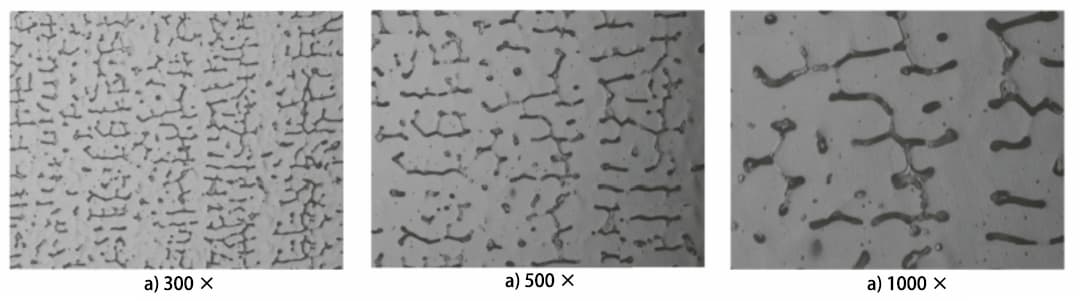
Fig. 2 Microstructure of δFerrite in the Weld in the Same Position
According to the GB/T 15749-2008 standard, the grid section method measures the sample 300 times, 500 times and 1000 times.
Figure 2 shows the microstructure in the same position. The average δ ferrite content measured at different multiples is 11.0%, 7.6% and 9.5%, respectively (see Table 1).
Table 1 δ Ferrite content at the same location under different magnification times
Amplified | Mass fraction | |||||||||
1 | two | 3 | 4 | 5 | 6 | 7 | 8 | 9 | Average value | |
300 times | 10 | 9.7 | 11.6 | 11.7 | 12.7 | 10.8 | 11.5 | 10.6 | 10.8 | 11 |
500 times | 8.2 | 10 | 8.8 | 6.1 | 10.1 | 6.4 | 9.3 | 9.8 | 9.3 | 7.6 |
1000 times | 10.6 | 11 | 8.2 | 7.7 | 10 | 7.8 | 10.5 | 10.8 | 9.6 | 9.6 |
Table 1 shows that the δ ferrite content varies greatly at different magnifications.
The lowest δ ferrite content is measured at 500 times magnification, while the content measured at 300 and 1000 times is higher.
Test results indicate that magnification has a significant impact on metallographic analysis results:
In welds, δ ferrite grains are generally very small. At low magnification (300x), the microstructure within the field of view appears very dense, making it difficult to discern the edge of the image segmentation calculation, resulting in generally larger results.
On the other hand, at very high magnification (1000 times), the area of the selected field of view is very small. Because the fabric itself is uneven, you may need to measure more stitches to get accurate results.
GB/T 1954-2008 specifies a minimum magnification of 500 times. Therefore, it is appropriate to select a magnification of 500 times for actual measurements.
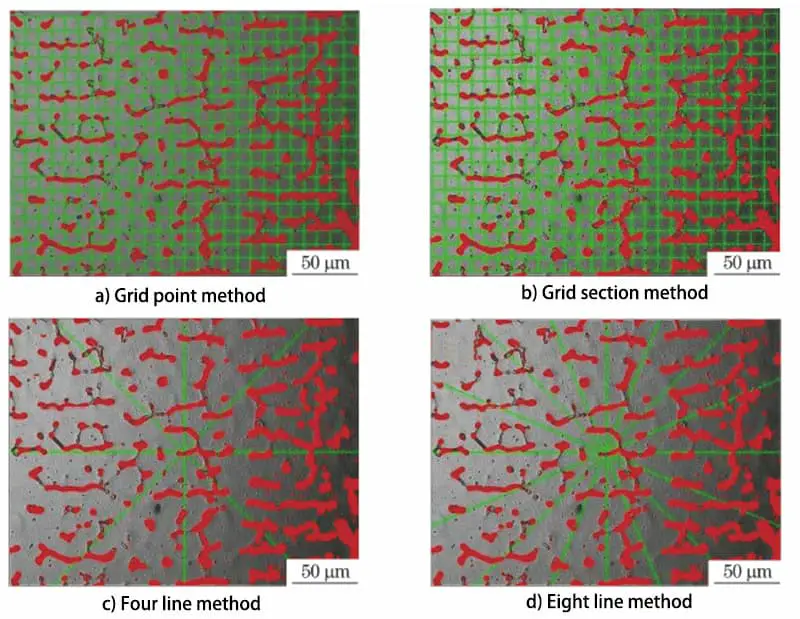
Fig. 3 Schematic diagram of the ferrite content measurement method
In testing, we use the grid number method, grid section method, four-line method and eight-line method respectively. We randomly selected 9 locations under 500 different conditions to measure the δ ferrite content, and the measurement method is shown in Fig. 1.
The results of these measurements were 7.6%, 7.6%, 6.7% and 7.6%, respectively, as shown in Table 2.
Table 2: δ-Ferrite content measured at random locations below 500×
Position and average | Grid number point | Grid Section | Four lines | Eight lines |
1 | 6.9 | 8.2 | 4.1 | 6.9 |
two | 8.2 | 10 | 6.6 | 8.8 |
3 | 9.2 | 8.8 | 5.1 | 5.8 |
4 | 5.6 | 6.1 | 6.5 | 5.9 |
5 | 10.2 | 10.1 | 7.7 | 7.9 |
6 | 4.2 | 6.4 | 5.5 | 6.3 |
7 | 7.9 | 9.3 | 9 | 9.3 |
8 | 8.3 | 9.8 | 5.9 | 8.5 |
9 | 7.5 | 9.3 | 9.6 | 9.2 |
to mean | 7.6 | 7.6 | 6.7 | 7.6 |
According to Table 2, it can be seen that, with the exception of the four-line method, the measurement results of the other three methods are the same.
2.2 Chemical method
The chemical composition of the surface layer of 308 stainless steel is shown in Table 3 and meets the requirements of specified technical indicators.
Table 3 Chemical Composition of 308 Stainless Steel Cover
W | Cr | No | Mo | Mn | co | Ass | V | s | B | P | Yes |
0.028 | 7:25 p.m. | 10.4 | 0.065 | 1.38 | 0.02 | 0.03 | 0.04 | 0.0078 | 0.0006 | 0.013 | 0.73 |
Based on the Schaeffler diagram and its calculation formula, the mass fractions of chromium and nickel in the test material are 20.41% and 10.93%, respectively, indicating a δ ferrite content of about 8.5%.
On the other hand, referring to the WRC-1992 value, the mass fractions of chromium and nickel in the test material are 19.315% and 10.24%, respectively, resulting in a δ-ferrite content of approximately 13%.
It is evident that the calculation results of the chemical method vary when different experiment graphs are used due to the influence of various factors.
Further analysis reveals that the inclusion of copper as a nickel equivalent in the WRC-1992 diagram, together with the 0.03% copper content of 308 stainless steel, leads to a calculated δ-ferrite content considerably higher than the one obtained using the Schaeffler diagram.
2.3 Magnetic method
According to the specifications given in GB/T 1954-2008 for measurement by magnetic method, six points should be randomly selected along the weld bead direction of the 308 stainless steel surface layer. averaging five readings at each point, and the average δ-ferrite content is calculated to be 3.4%.
3 . Analysis and discussion
The α-ferrite content in the surface layer of 308 stainless steel was measured using metallographic, chemical and magnetic methods, as shown in Table 4.
The δ-ferrite content in the weld structure of austenitic stainless steel is normally between 4% and 12%.
It is evident that the magnetic method produced lower measurements, while the WRC-1992 diagram measurement results from the chemical method were higher.
Table 4 Coverage of 308 stainless steel measured by different methods δ Ferrite content
Measurement method | δ - Mass fraction of ferrite | |
Metallography (500 times) | Atlas contrast method | 10.0 |
Measurement method | 7.6 | |
Chemical method | Schaeffler Chart | 8.5 |
WRC-1992 Chart | 13.0 | |
Magnetic method | 3.4 |
When measuring δ-ferrite content using different methods such as grid number method, grid section method, four-line method and eight-line method, the four-line method tends to have less measurement data due to the distribution uneven and to the shape of the δ ferrite. in each field of view, leading to larger deviations.
Although the metallographic method offers a wide and random field of view, the reliability of its results is generally high.
To reduce the adverse effects of measurement methods and improve the reliability of results, the appropriate measurement method should be selected by comprehensively considering factors such as magnification, position of the field of view and differences between the principles of different methods.
At 500x magnification, the average δ ferrite content values obtained from the grid number method, grid section method, and eight-line method are the same, indicating a more reliable result of 7.6% ferrite content. δ ferrite.
The chemical method uses element content detection results to calculate and compare an experiment graph to obtain δ ferrite content. The measurement accuracy of the chemical element directly affects the accuracy of the results.
The chemical method is directly affected by factors such as the accuracy of element measuring instruments and the selection of experiment charts.
The magnetic method tends to produce relatively small measurement results due to differences in the physical quantities measured by different instruments and the measurement errors of the instruments themselves. Furthermore, the morphology and distribution of δ ferrite may be uneven in materials with low δ ferrite content.
Inappropriate sampling locations can lead to poor reproducibility and accuracy of determination results.
During testing and production, it is recommended to avoid relying on a single method to measure the δ ferrite content of welds and to use multiple methods for mutual verification.
4. Conclusion
(1) Each of the three methods has advantages and disadvantages and should be selected according to the specific situation.
The metallographic method is a destructive testing method, but it provides highly reliable measurement results. During testing, it is necessary to consider the magnification, the position of the field of view and the differences between various methods and principles in order to select the appropriate measurement method.
The chemical method can easily and quickly obtain detection values based on the known chemical composition of the material. However, it is important to select an appropriate experience chart and calculation formula.
The magnetic method is a non-destructive inspection method suitable for rapid inspection of large material components on site, but its measured value is low.
(2) The measurement results obtained using the metallographic atlas comparison method and the chemical Schaeffler diagram method are similar. Similarly, the measurement results obtained using the grid number method, grid section method and eight-line method in the metallographic measurement method are also the same. Therefore, these methods can be used as alternative methods in actual detection.