What is Springback?
Springback is defined as a partial restoration of the shape of deformed parts after removal of the load.
The shape and size of the parts do not align with the shape and size of the working surface of the stamping die, causing the parts to fall outside the tolerance range and affecting the assembly accuracy of products.
In engineering, it is crucial to resolve errors in the product caused by springback.
Stamping not only results in plastic deformation, but also in elastic deformation. When the forming load is released, springback occurs in the parts.
Springback is the deformation that inevitably occurs after the sheet metal has been formed and the molded part has been removed from the mold, impacting the final shape of the part.
The magnitude of springback directly impacts the geometric precision of the part and is a forming defect that is difficult to overcome in the engineering field.
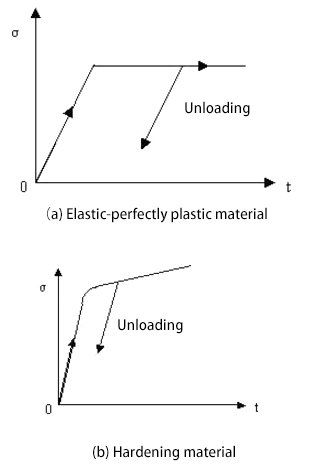
Voltage change curve after charge discharge
Factors that influence the springback of printed parts
Material property
The yield strength of sheet metal varies between common plates and high-strength plates.
The higher the yield strength of the sheet metal, the greater the probability of recovery.
Thick plate parts are typically made of hot-rolled carbon steel or low-alloy, high-strength hot-rolled steel.
Compared with cold-rolled sheet materials, hot-rolled sheet materials have poor surface quality, large thickness tolerance, unstable mechanical properties and low elongation rate.

Stress changes before and after springback
Material thickness
In the forming process, the thickness of the sheet material significantly impacts its bending performance. As plate thickness increases, the occurrence of rebound decreases.
This is due to the fact that as the sheet thickness increases, the amount of plastic deformation involved also increases, leading to an increase in elastic recovery deformation. As a result, resilience decreases.
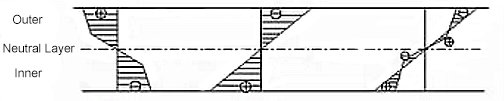
Sheet metal interface tangential stress
As the strength level of thick plate parts continues to improve, the problem of dimensional accuracy caused by shoulder becomes more and more serious.
Both mold design and subsequent technology commissioning require knowledge of the nature and magnitude of part resilience in order to implement appropriate countermeasures and corrective actions.
For thick sheet parts, the relationship between the radius of curvature and sheet thickness is usually small, and the stress and its changes in the direction of sheet thickness cannot be neglected.
Part format
The elastic return of parts with different shapes varies greatly. Parts with complex shapes typically require an additional forming process to avoid springback resulting from an incomplete forming process.
However, certain specialized shapes, such as U-shaped pieces, are more prone to ricocheting. Therefore, springback compensation must be taken into account during the forming process.
Central angle flexion
The greater the central bending angle, the greater the cumulative springback value, which can result in significant springback.
The deformation length of stamped parts increases as the central bending angle increases.
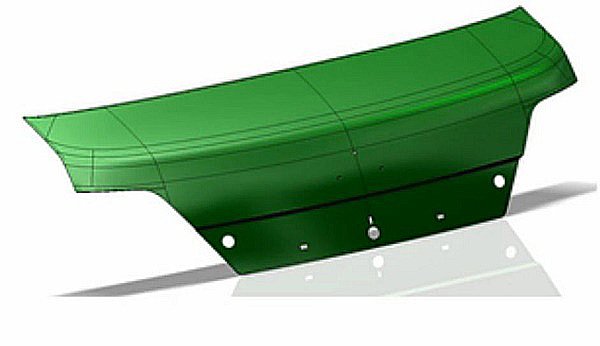
Corresponding condition of mold clearance
The die must be designed with a gap equal to twice the thickness of the material in the corresponding workpiece, and the product must fit into this gap.
To facilitate better material flow, mold parts should be developed after mold processing is completed, especially in the case of bending molds. The greater the gap in the workpiece, the greater the springback.
If the error tolerance range for plate thickness is greater, the overhang will also be greater, making it difficult to accurately determine the mold clearance.
Relative radius of curvature
The relative radius of curvature is proportional to the value of springback. As a result, the more curved the stamped parts are, the less likely they are to bend.
Training Technique
The forming process is a crucial factor in determining the value of springback.
Generally, flexion correction has a better springback effect than free flexion.
If the same machining result is desired for the production of a batch of stamped parts, the bending force required to correct the bending is significantly greater than that required for free bending.
As a result, even if the same bending force is used in both methods, the end result will be different.
The greater the correction force required to correct the bending, the lower the elastic return of the stamped parts. This correction force stretches the inner and outer fibers in the deformation zone, resulting in the desired forming effect.
When the bending force is released, the inner and outer fibers shorten, but the springback direction of the inner and outer fibers is opposite, reducing the springback of printed parts to a certain extent.
The springback stamping solution
Product design
First of all, in terms of materials, it is advisable to choose materials with low yield strength or increase the thickness of the material and still meet the product requirements.
Secondly, in terms of the design of printed parts, the shape of the part also plays a significant role in determining its springback. In the case of complex stamped parts with a curved shape, it is difficult to eliminate springback due to complex tension in all directions and other factors such as friction.
Therefore, the product shape can be designed by combining several parts to solve the problem of springback in complex printed parts.
An elastic anti-return cord can also be added, which is an effective solution for springback defects. The shape of the product can be changed by increasing the number of anti-return balls as required by the product and the springback value.
Finally, the springback defect can be solved by reducing the value of the angle R of the bent part.
Technical Project
- Adding a preforming process into the die design. By incorporating a preforming process, the one-time forming of stamped parts can be divided into different stages, and the internal stress in the forming process can be reduced to a certain extent, thereby solving the springback defect.
- Reducing the gap between concave and convex molds. This gap can be adjusted to approximately twice the thickness of the material to maximize the bond between the material and the mold.
- Die hardening treatment can also help reduce stretching of stamped parts and decrease die wear.
- Product modeling can be employed. If the product design cannot be changed, reshaping the stamped parts at the end is another option.
- Other methods to solve the springback defect include the use of hydraulic stamping equipment, which can offer some relief from the springback problem.
Strength of blank parts support
Using the support force of the blank in the forming process is a crucial technology. By continuously optimizing the support force of the blank, the material flow direction can be adjusted and the internal stress distribution of the material can be improved.
Increasing the support force of the blank causes the parts to extend more fully, particularly at the sidewall and R-angle position. If it is fully formed, the difference in internal and external stress will decrease, leading to a reduction in resilience.
Cords
The use of beads is common in modern technology. Proper positioning of the drawing beads can effectively change the material flow direction and distribute the feeding resistance evenly on the pressing surface, thereby increasing the formability of the material.
Placing draw cords on parts prone to springback will result in fuller forming and more even stress distribution, reducing springback.
The springback flexion solution
Flexion correction
Correcting the bending forces concentrates the impact pressure in the bending deformation zone, causing the inner metal to be compressed. After adjustment, both the inner and outer layers are stretched, and the springback tendency of the two areas after unloading can compensate for each other, reducing the springback.
Heat treatment
Annealing before bending can reduce hardness and yield stress, which not only decreases springback but also reduces bending strength. After bending, carry out a hardening process.
Excessive bending
In the bending production process, the deformation angle and radius of the sheet metal will increase due to elastic recovery. To reduce springback, the deformation of the plate may exceed the theoretical degree of deformation.
Warming Fold
Use hot bending, selecting the appropriate temperature so that the material has enough time to soften, which will decrease the amount of springback.
Stretch flexion
The method involves applying tangential stress during bending of the sheet metal, changing the stress state and distribution within the sheet metal, causing the entire section to undergo tensile plastic deformation. After unloading, the internal and external springback compensate each other, reducing the springback.
Local Compression
The local compression technique involves increasing the length of the outer plate by decreasing its thickness, so that the elastic return of the inner and outer layers compensate each other.
Multiple Flexion
Bending is divided into several times to eliminate springback.
Inner Canthus Passivation
Compress from the inside of the folded piece to eliminate springback. When the plate is U-shaped, the effect is better because both sides are symmetrical.
Adopt partial flexion in stretching training
The method of partially forming a part by bending and then stretching reduces springback. This method is effective for products with a simple two-dimensional shape.
Control residual stress
During the stretching process, a local convex hull shape is first added to the tool surface and then eliminated in a later process to change the residual stress balance in the material, thus eliminating springback.
Negative return
When machining the tool surface, try to make the sheet material have negative springback. After the return of the upper die, the parts will achieve the desired shape through springback.
Electromagnetic Method
Shape and size errors caused by springback can be corrected by using electromagnetic pulses to impact the surface of the material.