The wire mesh weight calculation method can be determined in several ways depending on the material, the structure of the wire mesh and the specific parameters required for the calculation. We can summarize several different calculation methods and factors to consider.
Firstly, a basic weight calculation method involves estimating by dividing the product of wire diameter, mesh count, mesh length and mesh width by 2. This method is applicable for general wire mesh weight calculations, where the unit of wire diameter is millimeters (mm). ), and the units for mesh length and width are meters (m).
Furthermore, for specific types of wire mesh, such as galvanized wire mesh, more detailed calculation methods can be employed. For example, the weight of galvanized wire mesh can be calculated by measuring the length of the wire per square meter (in meters) and the weight of the wire per meter (in kilograms). This method provides a simple way to estimate the weight of wire mesh.
Another method is to calculate the weight through the cross-sectional area and length of the wire, as well as the density of the material. This can be achieved using the formula “Weight (kg) = Cross-sectional area (mm 2 ) × Length (m) × Density (g/cm 3 ) × 1/1000″. This method is suitable for situations where an accurate calculation of the weight of the wire mesh is required, especially when considering the density of different materials.
Wire Mesh Weight Calculation Formula
The following simplified formula can be used to calculate the weight of steel wire mesh.
Of course, if you need a more accurate calculation result, you can use our online calculator.
Weight (kg) = total length of raw material * wire diameter² * coefficient (0.00617)
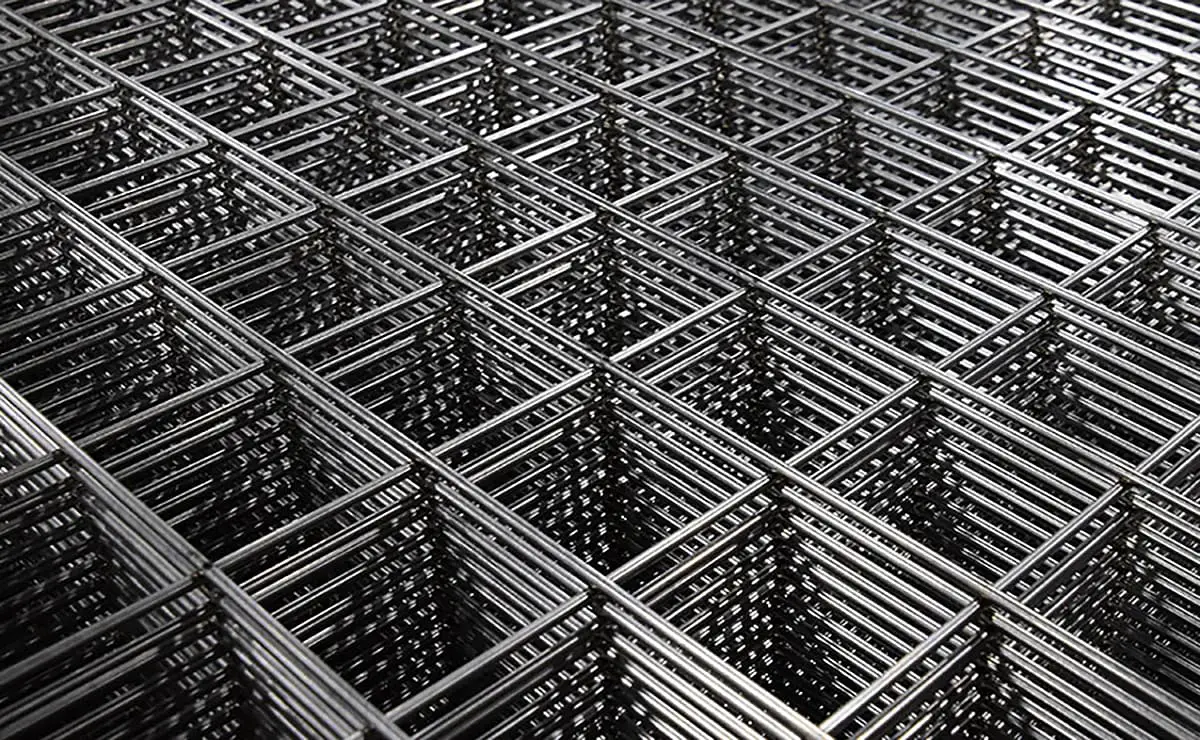
Steel Wire Mesh Weight Table
The following table lists the theoretical weight of steel wire mesh in kg/m². If your steel size is not in the table below, you can use our steel weight calculator to calculate online.
Reinforcement Mesh Weights Table (steel wire mesh)
(1) Longitudinal reinforcement bar weight table
Note | Longitudinal reinforcement bar | Theoretical weight | ||
Day. | Distance | Area per linear meter | ||
(mm) | (mm) | (mm²/m) | (kg/m²) | |
A18 | 18 | 200 | 1273 | 2:43 p.m. |
A16 | 16 | 200 | 1006 | 12:34 |
A14 | 14 | 200 | 770 | 10:49 am |
A12 | 12 | 200 | 566 | 8.88 |
A11 | 11 | 200 | 475 | 7.46 |
A10 | 10 | 200 | 393 | 6.16 |
A9 | 9 | 200 | 318 | 4.99 |
A8 | 8 | 200 | 252 | 3.95 |
A7 | 7 | 200 | 193 | 3.02 |
A6 | 6 | 200 | 142 | 2.22 |
A5 | 5 | 200 | 98 | 1.54 |
B18 | 18 | 100 | 2545 | 24:42 |
B16 | 16 | 100 | 2011 | 18.89 |
B14 | 14 | 100 | 1539 | 15.19 |
B12 | 12 | 100 | 1131 | 10.9 |
B11 | 11 | 100 | 950 | 9.43 |
B10 | 10 | 100 | 785 | 8.14 |
B9 | 9 | 100 | 635 | 6.97 |
B8 | 8 | 100 | 503 | 5.93 |
B7 | 7 | 100 | 385 | 4.53 |
B6 | 6 | 100 | 283 | 3.73 |
B5 | 5 | 100 | 196 | 3.05 |
C18 | 18 | 150 | 1697 | 17.77 |
C16 | 16 | 150 | 1341 | 14.98 |
C14 | 14 | 150 | 1027 | 12.51 |
C12 | 12 | 150 | 754 | 10.36 |
C11 | 11 | 150 | 634 | 8.7 |
C10 | 10 | 150 | 523 | 7.19 |
C9 | 9 | 150 | 423 | 5.82 |
C8 | 8 | 150 | 335 | 4.61 |
C7 | 7 | 150 | 257 | 3.53 |
C6 | 6 | 150 | 189 | 2.6 |
C5 | 5 | 150 | 131 | 1.8 |
D18 | 18 | 100 | 1545 | 28.86 |
D16 | 16 | 100 | 2011 | 24.68 |
D14 | 14 | 100 | 1539 | 20.98 |
D12 | 12 | 100 | 1131 | 5:75 p.m. |
D11 | 11 | 100 | 950 | 14.92 |
D10 | 10 | 100 | 785 | 12:33 p.m. |
D9 | 9 | 100 | 635 | 9.98 |
D8 | 8 | 100 | 503 | 7.9 |
D7 | 7 | 100 | 385 | 6.04 |
D6 | 6 | 100 | 283 | 4.44 |
D5 | 5 | 100 | 196 | 3.08 |
E18 | 18 | 150 | 1697 | 7:25 p.m. |
E16 | 16 | 150 | 1341 | 4:46 p.m. |
E14 | 14 | 150 | 1027 | 13.99 |
E12 | 12 | 150 | 754 | 11.84 |
E11 | 11 | 150 | 634 | 9.95 |
E10 | 10 | 150 | 523 | 8.22 |
E9 | 9 | 150 | 423 | 6.66 |
E8 | 8 | 150 | 335 | 5.26 |
E7 | 7 | 150 | 257 | 4.03 |
E6 | 6 | 150 | 189 | 2.96 |
E5 | 5 | 150 | 131 | 2.05 |
F18 | 18 | 100 | 2545 | 25.9 |
F16 | 16 | 100 | 2011 | 21.7 |
F14 | 14 | 100 | 1539 | 18 |
F12 | 12 | 100 | 1131 | 14.8 |
F11 | 11 | 100 | 950 | 12:43 p.m. |
F10 | 10 | 100 | 785 | 10.28 |
F9 | 9 | 100 | 635 | 8.32 |
F8 | 8 | 100 | 503 | 6.58 |
F7 | 7 | 100 | 385 | 5.03 |
F6 | 6 | 100 | 283 | 3.7 |
F5 | 5 | 100 | 196 | 2.57 |
(2) Transverse reinforcement bar weight table
Note | Transverse reinforcement bar | Theoretical weight | ||
Day. | Distance | Area per linear meter | ||
(mm) | (mm) | (mm²/m) | (kg/m²) | |
A18 | 12 | 200 | 566 | 2:43 p.m. |
A16 | 12 | 200 | 566 | 12:34 |
A14 | 12 | 200 | 566 | 10:49 am |
A12 | 12 | 200 | 566 | 8.88 |
A11 | 11 | 200 | 475 | 7.46 |
A10 | 10 | 200 | 393 | 6.16 |
A9 | 9 | 200 | 318 | 4.99 |
A8 | 8 | 200 | 252 | 3.95 |
A7 | 7 | 200 | 193 | 3.02 |
A6 | 6 | 200 | 142 | 2.22 |
A5 | 5 | 200 | 98 | 1.54 |
B18 | 12 | 200 | 566 | 24:42 |
B16 | 10 | 200 | 393 | 18.89 |
B14 | 10 | 200 | 393 | 15.19 |
B12 | 8 | 200 | 252 | 10.9 |
B11 | 8 | 200 | 252 | 9.43 |
B10 | 8 | 200 | 252 | 8.14 |
B9 | 8 | 200 | 252 | 6.97 |
B8 | 8 | 200 | 252 | 5.93 |
B7 | 7 | 200 | 193 | 4.53 |
B6 | 7 | 200 | 193 | 3.73 |
B5 | 7 | 200 | 193 | 3.05 |
C18 | 12 | 200 | 566 | 17.77 |
C16 | 12 | 200 | 566 | 14.98 |
C14 | 12 | 200 | 566 | 12.51 |
C12 | 12 | 200 | 566 | 10.36 |
C11 | 11 | 200 | 475 | 8.7 |
C10 | 10 | 200 | 393 | 7.19 |
C9 | 9 | 200 | 318 | 5.82 |
C8 | 8 | 200 | 252 | 4.61 |
C7 | 7 | 200 | 193 | 3.53 |
C6 | 6 | 200 | 142 | 2.6 |
C5 | 5 | 200 | 98 | 1.8 |
D18 | 12 | 100 | 1131 | 28.86 |
D16 | 12 | 100 | 1131 | 24.68 |
D14 | 12 | 100 | 1131 | 20.98 |
D12 | 12 | 100 | 1131 | 5:75 p.m. |
D11 | 11 | 100 | 950 | 14.92 |
D10 | 10 | 100 | 785 | 12:33 p.m. |
D9 | 9 | 100 | 635 | 9.98 |
D8 | 8 | 100 | 503 | 7.9 |
D7 | 7 | 100 | 385 | 6.04 |
D6 | 6 | 100 | 283 | 4.44 |
D5 | 5 | 100 | 196 | 3.08 |
E18 | 12 | 150 | 754 | 7:25 p.m. |
E16 | 12 | 150 | 754 | 4:46 p.m. |
E14 | 12 | 150 | 754 | 13.99 |
E12 | 12 | 150 | 754 | 11.84 |
E11 | 11 | 150 | 634 | 9.95 |
E10 | 10 | 150 | 523 | 8.22 |
E9 | 9 | 150 | 423 | 6.66 |
E8 | 8 | 150 | 335 | 5.26 |
E7 | 7 | 150 | 257 | 4.03 |
E6 | 6 | 150 | 189 | 2.96 |
E5 | 5 | 150 | 131 | 2.05 |
F18 | 12 | 150 | 754 | 25.9 |
F16 | 12 | 150 | 754 | 21.7 |
F14 | 12 | 150 | 754 | 18 |
F12 | 12 | 150 | 754 | 14.8 |
F11 | 11 | 150 | 634 | 12:43 p.m. |
F10 | 10 | 150 | 523 | 10.28 |
F9 | 9 | 150 | 423 | 8.32 |
F8 | 8 | 150 | 335 | 6.58 |
F7 | 7 | 150 | 257 | 5.03 |
F6 | 6 | 150 | 189 | 3.7 |
F5 | 5 | 150 | 131 | 2.57 |
What impact does a wire mesh material have on its weight?
The influence of the material of a wire mesh on its weight is mainly manifested in the density of the different materials. The materials of cables and wire mesh can be divided into steel wire, nickel-chromium steel, alloy steel, stainless steel, etc. These materials have different densities, thus affecting their weight.
For example, wire mesh made of steel wire, featuring excellent strength and durability, is suitable for withstanding considerable stress and pressure, widely applied in the construction industry.
In addition, the materials of protective meshes generally include steel wire, aluminum alloy, stainless steel, etc. The difference in density of these materials would also result in different weights. Therefore, it can be concluded that the impact of the material of a wire mesh on its weight is mainly due to the differences in density of the different materials.
How to choose the appropriate calculation method based on different types of wire mesh (such as galvanized wire mesh, stainless steel wire mesh, etc.)?
The selection of the appropriate calculation method depends on the type of wire mesh, such as galvanized wire mesh, stainless steel wire mesh, etc. We can summarize the following points:
For different types of wire mesh, their weight calculation formulas may vary. This indicates that the specific properties of wire meshes of different materials need to be considered in the calculations.
The calculation of wire mesh parts can be done by software, automatically calculating the length according to the material and multiplying by the width specified in the project. This method is applicable to wire mesh of various materials, including, but not limited to, galvanized wire mesh and stainless steel wire mesh.
In terms of construction welding, the calculation method for wire mesh parts specifications reflects the production of multiple models, sizes and style types. This means that when selecting the calculation method, the specific specifications and application requirements of the wire mesh need to be considered.
Choosing the appropriate calculation method first requires understanding the type and characteristics of the wire mesh. For galvanized wire mesh and stainless steel wire mesh, etc., the software method that automatically calculates the length and multiplies the width can be used for calculation. This ensures the accuracy and applicability of the calculation results.
In practical applications, how to choose the most suitable method for calculating the weight of wire mesh based on its usage?
In real-world applications, choosing the most appropriate method for calculating wire mesh weight requires first considering the specific type of mesh and its use. We can see that different types of mesh have different calculation formulas. For example, the weight calculation formulas for copper mesh and stainless steel mesh are as follows:
Weight calculation formula for copper mesh: Wire Diameter × Wire Diameter × Mesh Count × Length × Width ÷ 2 × 1.07 = kg.
Weight calculation formula for stainless steel mesh: Wire Diameter × Wire Diameter × Mesh Count × Length × Width ÷ 2 × 1.07 = kg.
This shows that the calculation methods for copper mesh and stainless steel mesh are similar, the main difference being the difference in density (1.07) caused by different materials.
For steel and aluminum plate mesh, its weight calculation formula is: Mesh weight (kg): Mesh length ÷ 1/2 short section rectangle × Rod thickness × Rod width × Mesh width × 7, 85. This formula involves several parameters such as mesh length, short section rectangle (hole width), rod thickness, rod width and mesh width, and is suitable for accurately calculating larger areas or complex wire mesh structures.
Therefore, when choosing the most appropriate weight calculation method, you must decide according to the specific type of wire mesh and its use. If it is copper mesh or stainless steel mesh, the general calculation formula mentioned above can be used. For special types of mesh, such as steel and aluminum plate mesh, a calculation formula designed specifically for that type of mesh must be used. In addition, cost calculation considerations such as cost:= mesh weight × plate price + labor cost + circulation cost are also one of the factors to be considered when choosing a calculation method.