NASA's $2.5 billion rover Curiosity is ready to capture the finest details of the planet Mars. The rover is designed to be highly accurate in observing environmental conditions, including atmospheric pressure and gravitational force. To this end, its Instrumental Control Unit or ICU was equipped with pressure sensors. These sensors will help detect the Dust Devils that are a feature of the planet and will also detail the concentration of different gases in the atmosphere at different points. Let's take a look at what makes a pressure sensor capable enough to perform such specific tasks and where else it can be used.
A pressure sensor is a device that detects pressure and converts it into an analog electrical signal whose magnitude depends on the pressure applied. As they convert pressure into an electrical signal, they are also called pressure transducers.
Need for pressure sensors
Since a long time, pressure sensors have been widely used in areas such as automobile, manufacturing, aviation, biomedical measurements, air conditioning, hydraulic measurements, etc. Some prominent areas where the use of pressure sensors is inevitable are:
1. Touch Screen Devices: Computer devices and smartphones that have touch screens come with pressure sensors. Whenever slight pressure is applied to the touchscreen using a finger or stylus, the sensor determines where it was applied and, consequently, generates an electrical signal that informs the processor. Typically, these sensors are located in the corners of the screen. Therefore, when pressure is applied, usually two or more sensors act to provide accurate location information.
2. Automotive Industry: In the automotive industry, pressure sensors are an integral part of the engine and its safety. In the engine, these sensors monitor oil and coolant pressure and regulate the power the engine must deliver to reach appropriate speeds whenever the accelerator is pressed or the brakes are applied to the car.
For safety purposes, pressure sensors form an important part of the anti-lock braking system (ABS). This system adapts to the road terrain and ensures that, when braking at high speeds, the tires do not lock and the vehicle does not skid. Pressure sensors in the ABS inform the processor of road conditions as well as the speed at which the vehicle is moving.
Airbag systems also use pressure sensors so that the airbags are activated to ensure passenger safety whenever the vehicle feels great pressure.
3. Biomedical Instrumentation: In instruments like digital blood pressure monitors and ventilators, pressure sensors are required to optimize them according to the patient's health and needs.
4. Industrial Uses: Pressure sensors are used to monitor gases and their partial pressures in industrial units so that large chemical reactions can occur under precisely controlled environmental conditions. In the oil industry, sensors detail the depth that the oil rig has reached during exploration.
5. Aviation: In airplanes, these sensors are necessary to maintain a balance between atmospheric pressure and the airplane's control systems. This not only protects the aircraft's circuits and various internal components, but also provides the system with accurate data about the external environment. Additionally, specific air pressure levels need to be maintained in the cabin and passenger lobby to provide nominal breathing conditions.
6. Marine Industry: For ships and submarines, pressure sensors are needed to estimate the depth at which they are operating and to detail marine conditions so that electronic systems can remain safe. The oxygen requirements of underwater projects are also regulated by pressure sensors.
Types of pressure measurements
Pressure measurement can be relative to a reference value or on an absolute scale.
1. Absolute pressure measurement: The pressure measured in relation to perfect vacuum is called
as absolute pressure. Perfect vacuum is a condition in which there is no matter present in the atmosphere and, therefore, there is no air pressure in that region. Absolute pressure sensors have limited use because it is impossible to achieve a perfect vacuum state. Consequently, sensors based on absolute pressure measurement require stringent specifications for accurate results. Sensors based on this type of measurement are used in barometric or altitude-related pressure measurements.
two. Differential pressure measurement: In differential pressure measurement, pressures from two different positions are compared. For example, the pressure difference calculated by measuring it on different floors of a tall building will give us the differential pressure. Differential pressure measurements, typically done in pounds per square inch differential (psid), are applied when a large amount of pressure must be measured. These types of measurements are used for supply pressure monitoring purposes, where the pressure at which fluid is flowing in a medium is monitored, so that homogeneity in flow can be maintained.
Differential pressure measurements find an important application in monitoring filters in various types of purification systems. They take as a reference the normal pressure at which the filters clean the fluid. Whenever the filters face the problem of clogging due to contaminants, these pressure sensors provide a reading relative to the normal pressure. This helps keep the filter clean and operational.
3. Gauge pressure measurement: It can be defined as a subtype of differential pressure measurement where we compare the pressure at any point with the current atmospheric pressure. Gauge pressure measurement is used in applications such as tire pressure or blood pressure measurement. There is no consistency in gauge pressure measurements because atmospheric pressure varies with altitude and therefore its applications are limited to non-critical measurements.
Types of pressure sensors
Types of pressure sensors
Based on the type of applications they are used in, pressure sensors can be categorized into various types. However, the following are the most common types of pressure sensors that have been widely used:
1. Strain Meter Type: These sensors are similar to a wheat stone bridge in their functioning. In the wheat stone bridge, the ratio of resistances of two adjacent arms connected to one end of the battery must be equal to that of the other two arms connected to the other end of the battery. When the two proportions are equal, no production is generated by the wheat stone bridge. In the case of an extensometer, a wheat stone bridge arm is connected to a diaphragm. The diaphragm compresses and expands due to the applied pressure. This variation in the diaphragm causes the output at the bridge to vary. A voltage would be generated proportional to each deviation from the normal equilibrium condition, so that each compression or expansion movement of the diaphragm will produce an output indicating a change in pressure conditions. Since the change in resistance is the main cause of the potential difference, these sensors are also called piezo-resistive type pressure sensors.
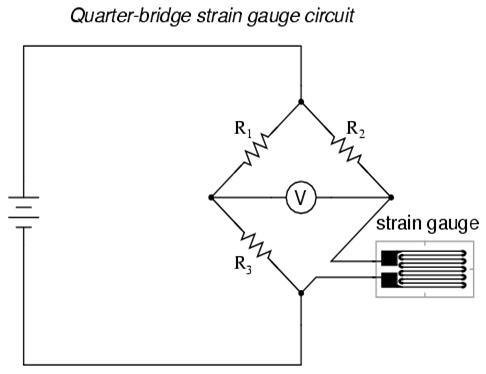
Figure 1: Quarter Bridge Extensometer Pressure Sensor Circuit Diagram
two. Capacitive pressure sensor: A capacitor has two metal plates and a dielectric sandwiched between them. In capacitive pressure sensor, one of these metal plates is allowed to move in and out so that the capacitance between them changes due to the variation in the distance between the plates. The moving plate is connected to a diaphragm that senses pressure and then expands or compresses accordingly. The movement of the diaphragm would affect the position of the fixed metal plate and the capacitance could vary.
These sensors, although very ineffective at high temperatures, are widely used in the ambient temperature range due to their linear output.
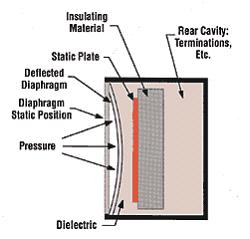
Figure 2: Diagram showing the internal structure of the capacitive pressure sensor
3. Piezoelectric Pressure Sensor: Piezoelectric crystals develop a potential difference (i.e. voltage is induced on the surfaces) whenever they are subjected to any mechanical pressure. These sensors have the crystal mounted on a dielectric base so that there is no current leakage. Attached to the crystal is a horizontal shaft to which a diaphragm is connected. Whenever the diaphragm senses pressure, it pushes the shaft down, which pressurizes the crystal and voltage is produced.
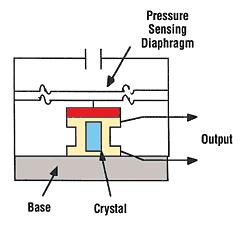
Figure 3: Image showing details of the piezoelectric pressure sensor
Specification, limitations and challenges
Pressure sensor specifications
As pressure sensors have diverse applications, it has certain specifications that are adopted so that they function optimally in a particular environment. Some of the main settings are listed below:
1. Measuring range: This defines the minimum and maximum pressure between which the sensor is designed to operate without being damaged. This criterion is most essential for differential and gauge sensors, as their measurements are relative and if the magnitude of the reference pressure is outside their range, they will not work.
two. Operating temperature: It is the temperature range under which the sensor functions optimally. It is always necessary to run the sensor within the set temperature range for the output to be consistent. In extremely hot or cold environmental conditions, the sensors may not function properly. This is especially applied in the case of electronic pressure sensors that are used in touchscreen computers and other devices.
3. Sensor Dimensions: Based on the application, the sensor size varies depending on the type of area where pressure needs to be detected. Consequently, sensor dimensions are an important consideration during sensor design. Typically, small size sensors are preferred as they can be easily installed in difficult locations such as air filters.
4. Type of measurement: It is also important that the user knows which type of pressure measurement is being made by the sensor: absolute, gauge or differential. This is because different measurement techniques are followed by different processing methods and therefore the results vary accordingly.
5. Accuracy: Differential pressure measurements are the best way to make a sensor as accurate as possible. This is because the reference pressure is more under the user's control than the atmosphere, which is the case when measuring gauge pressure.
6. Repeatability: This can be defined as the ability of the sensor to produce the same result when a specific amount of pressure is applied repeatedly. Repeatability is one of the most important specifications of a sensor. Because the sensors are range specific, the likelihood that they will be calibrated at the same pressure is high; therefore, the results must be reproduced by the sensor for the same amount of pressure, repeatedly.
7. Type of output generated: The electrical output generated by the sensor can be of several types depending on its design and what the final output device is. Some known formats in which output is being generated are analog voltage; analog current, digital signal (TTL), RS232 Interface and HART protocol based on frequency switching.
8. Response Time: This denotes the time taken between inputs applied and output achieved. Pressure sensors are expected to have a short response time so that instantaneous outputs can be generated and, in the case of rapid pressure variations, the system can also respond quickly.
9. Offset voltage: Offset voltage can be termed as the output voltage generated when no input is applied. In the case of differential sensors, displacement voltages are generated when there is no reference pressure, and in the case of gauge pressure, they are generated when ambient pressure is applied to the sensor. The offset voltages are necessary to reduce the error in the output and the final outputs are calculated after subtracting the offset voltages from them.
Limitations and Challenges:
Pressure sensors have several limitations that restrict their use in different areas. High temperature dependence, hysteresis, inability to deduce rapid and dynamic pressure variations, sensitivity to external vibrations, irreparability of the electronic board assembly, sensitivity to electric, magnetic and RF fields, incompatibilities with external devices are some challenges that a sensor can face. general pressure faces. In some applications, pressure sensors have limited accuracy. For example, in a touch screen, the sensitivity of the sensor when multiple touches are affected, while in the aviation sector high pressure can limit the functioning of the sensor.
Pressure sensors are essentially required to make a device respond to its environmental conditions optimally. Their types and uses are many and will continue to evolve as sensor technology matures. Extensive use of pressure sensors, such as in touch screens or automobiles, degrades their efficiency quickly, and therefore the robustness of pressure sensors is also a growing industrial research priority. However, pressure sensor tools, and as with all other tools, must be used with care and constantly checked to ensure quality results.