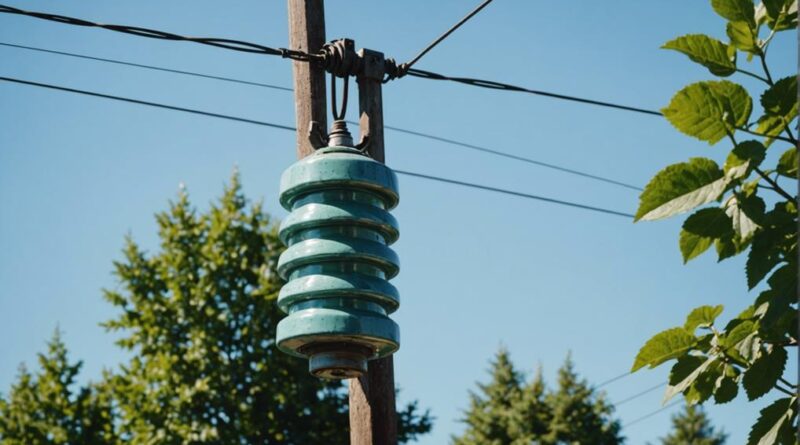
You probably have a support insulator if you've noticed the sturdy components on power poles or in substations. These insulators are essential for managing the precarious balance of high voltage electrical currents . They not only support the physical weight of power lines, but also prevent the catastrophic consequences of electrical grounding. While you may understand its basic function, its nuances are Material composition — whether porcelain, polymer or composite — can have a big impact on its performance and longevity. Each type offers a number of benefits that increase the efficiency and safety of electrical distribution systems . Curious about which materials offer the best protection and why?
The central theses
- Support insulators are essential for supporting and insulating high voltage lines in electrical systems.
- Available in materials such as porcelain, glass and composite polymers, each with different benefits.
- They prevent power outages, ensuring robust electrical isolation and system integrity.
- Regular maintenance and inspections are necessary to maintain performance and safety.
- Types include porcelain, polymer and composite, each suitable for different environmental and operational requirements.
Understanding Support Isolators
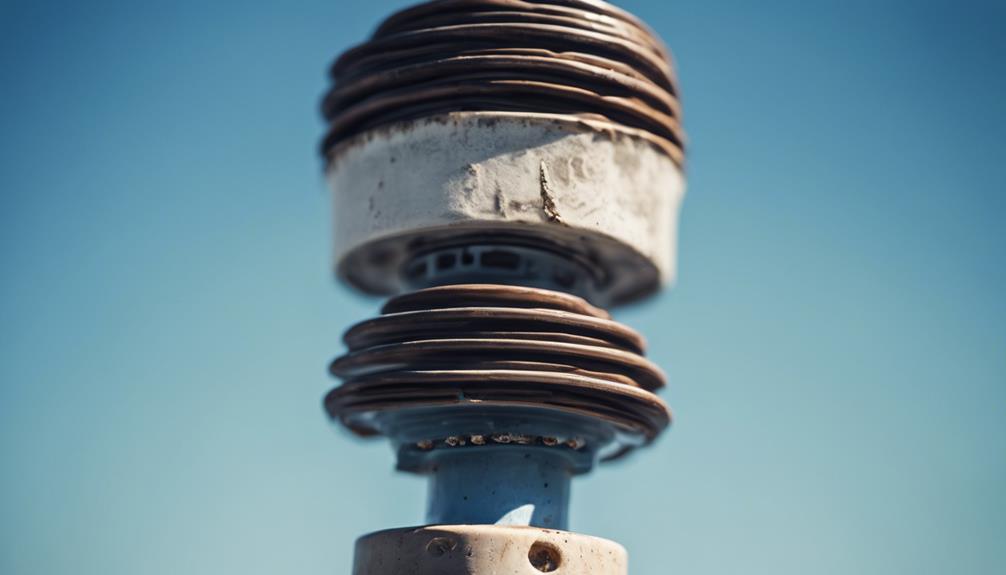
Support insulators are essential components in electrical systems because they support and insulate conductors from the ground and from each other. When installing, it is important to understand proper installation techniques to ensure it works as intended. It is necessary to consider the environment in which the isolator will be used, as this will influence the choice of technique. Each scenario requires specific methods to effectively manage electrical and mechanical loads, whether it be a high-voltage overhead power line or a substation .
Once installed, you can't just assume they will work perfectly. This is the point where Performance Testing comes into play. You need to check your ability to do this electrical voltages and environmental factors that you are exposed to in real-world conditions. The test involves applying a voltage higher than the normal operating level to check for faults or flashovers. This ensures that each insulator meets the required standards and can withstand the pressure.
Types of Support Insulators
You will find different types of Support Isolators each designed to meet specific operational requirements. One of the most common types is the Porcelain Support Insulator known for its high mechanical strength and excellent insulating properties. They are ideal for high voltage applications where reliability under load is critical.
Another type you may find is this Polymer Support Insulator . These are celebrated for their lightweight and hydrophobic properties making them ideal for areas with high humidity or frequent rainfall. Design innovations in this category often focus on improving the insulator's resistance to environmental and electrical stresses to ensure it meets global standards.
Composite support insulators also play an important role in modern electrical networks. They combine the advantages of porcelain and polymer materials and offer superior performance with reference to Durability and resilience. These are insulators adapted to provide expanded functionality. Adapted to specific environmental conditions, this further pushes the limits of what is possible in insulator technology.
Each type of insulating post offers its own advantages. As technology advances, these insulators continue to evolve, driven by a constant quest for efficiency and compliance with global standards. This ensures they meet current requirements and are prepared for future challenges.
Selection of materials for insulators
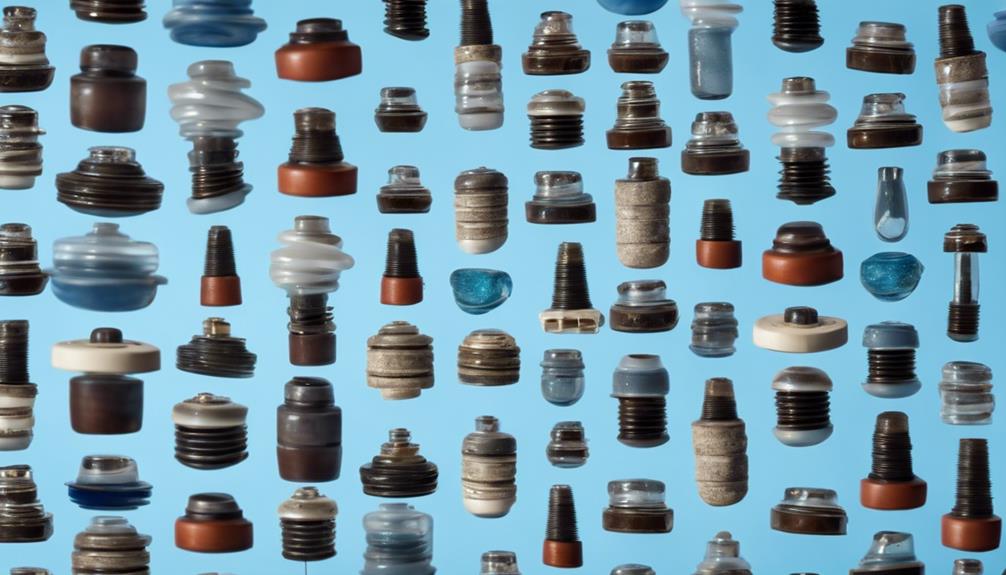
When selecting insulation materials, it is important to evaluate their ability to withstand electrical and environmental stresses. You need to evaluate how these materials will stand up to the challenges they will face over time, especially in relation to insulator aging and its thermal properties .
Materials such as porcelain, glass and composite polymers are common due to their high dielectric strength. Porcelain, for example, is very resistant to wear and aging, making it a reliable choice for long-term use. However, it is also fragile and can break under mechanical stress. Glass has similar properties, but is even more sensitive to shock.
Composite polymers, on the other hand, are more flexible and less prone to breakage. They are also resistant to UV light and corrosion, factors that significantly contribute to the aging of insulators. Their thermal properties are also beneficial, as these materials can withstand a wide range of temperatures without degrading.
It would be helpful if you also considered the specific environmental conditions that the insulators will be exposed to. Areas with extreme temperatures, high humidity or corrosive atmospheres require materials specifically designed to prevent and ensure premature failure Operational safety .
Applications in electrical systems
Understanding the material properties of insulators helps select the right type for various applications in electrical systems. You need to consider how these isolators can handle voltage regulation and ensure effective power distribution to prevent system failures and ensure efficiency.
Here's a quick look at how post-insulators fit into various electrical system applications:
scope of application | Role of support insulators |
---|---|
Power transmission | Support high voltage lines, manage voltages |
substations | Isolate and support electrical components |
Distribution networks | Distribute electricity safely, reduce losses |
Support insulators are indispensable in substations. They separate electrical components, prevent energy losses and stabilize voltage throughout the system. This isolation helps maintain the integrity and performance of sensitive devices.
In power lines, these insulators withstand mechanical stress on wires and cables while regulating voltage levels. This dual function is critical for avoiding power outages and improving energy reliability.
Distribution networks are fundamental to minimizing energy waste. Better power distribution saves costs and increases the overall efficiency of the electrical grid. This efficient management of power flow ensures that each area receives stable and reliable power, making your grid smarter and able to respond more quickly to changes in demand.
Maintenance and security protocols
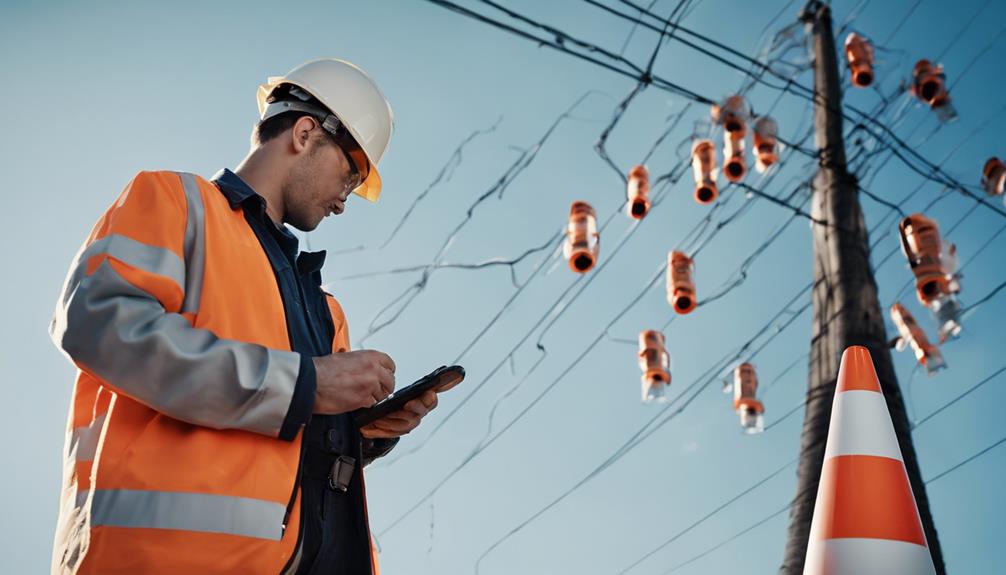
Regular support isolator maintenance is essential for superior performance and safety. Establish a strict inspection frequency schedule to catch potential problems before they escalate. It is generally advisable to inspect these insulators at least once a year, but in areas with high environmental pollution or adverse environmental conditions you may need to do so more frequently.
The effects of contamination are a serious problem for post-insulators. Deposits such as salt, industrial pollutants or bird droppings can significantly reduce its effectiveness. This deposit can lead to accumulations or power outages which disrupt the system. It is advisable to clean insulators regularly, especially after storms or in dirty environments. With a mild, non-abrasive cleaning solution helps prevent damage while cleaning.
Remember that during the inspection you also check for signs of wear, such as cracks or erosion in the insulation material. Don't limit yourself to visual inspections; Testing on electrical integrity is also important. If you are unsure whether you can perform these tests safely, it is best to consult a professional.
Always follow the manufacturer's instructions and safety protocols during maintenance to ensure you do not put yourself in danger. Regular maintenance not only extends the life of insulators, but also maintains the reliability of your electrical system.
Conclusion
You now have the crucial role of Support Insulators in electrical systems, covering their types, materials and applications.
Whether Porcelain, polymer or composite Choosing the right insulator impacts safety and efficiency.
Remember, routine maintenance and the following safety protocols cannot be neglected.
Keeping these insulators in optimal condition can prevent failures and improve network performance.
Therefore, always stay up to date and act proactively to ensure the proper functioning and safety of your electrical systems.
Common questions
What are the main differences between porcelain, polymer and composite post insulators?
Porcelain post insulators are known for their high mechanical strength and are therefore suitable for high voltage applications. Polymer insulators are lightweight and water resistant, ideal for humid environments. Composite insulators combine the benefits of both materials, providing durability and load-bearing capacity.
How often should support insulators be checked and what special attention should be paid during the check?
Support insulators should generally be checked at least once a year. More frequent checks are necessary in dirty or aggressive environments. When inspecting, look for signs of dirt buildup, such as salt or industrial fumes, as well as visual clues, such as cracks or erosion in the insulation material.
What are the consequences of inadequate support isolator maintenance and how can they be mitigated?
Improper maintenance can cause power outages and electrical system malfunctions due to dirt buildup or insulator failure. To mitigate these risks, establish a rigorous maintenance schedule that includes regular cleaning to remove debris and proactive electrical integrity testing.