In the previous tutorial, different types of SMPS were already discussed. In this series, the following SMPS circuits will be designed –
1. Boost Converters –
a) Open loop boost converter
b) Closed-loop boost converter
c) Open Loop Boost Converter with adjustable output
d) Closed Loop Boost Converter with Adjustable Output
2. Buck Converters –
a) Open Loop Buck Converter
b) Closed-loop Buck Converter
c) Open Loop Buck Converter with Adjustable Output
d) Closed-loop buck converter with adjustable output
3. Buck-Boost Converters
a) Buck Open Loop Inverter – Boost Converter
b) Buck Open Loop Inverter – Boost Converter with Adjustable Output
4. Flyback Converter
5. Push-pull converter
In this tutorial, an SMPS open loop boost converter will be designed. Boost Converter is one of the Switched Mode Power Supply (SMPS) topologies. It has a DC source as input power such as battery, generator or rectifier. In the case of a boost converter, the output power is always greater than the input power. Therefore, the boost converter circuit will increase the power from a DC level to a higher DC level. The method of converting one DC voltage to a different DC voltage is called DC to DC conversion. The boost converter is a DC to DC converter that boosts the input signal to the highest voltage level.
The boost converter can be designed in two ways-
Open Loop Boost Converter – In open loop boost converter, there is no feedback from the output to the input, unlike the closed loop which has a feedback circuit. Therefore, the output of an open-loop boost converter is not regulated.
Closed-loop boost converter – In closed-loop boost converter, there is feedback from the output to the input. Therefore, the output of a closed-loop boost converter is regulated.
There are certain design parameters involved in the design of the boost converter. It is important to understand these design parameters. Any boost converter can operate in any of the two possible operating modes. These modes of operation are as follows –
• Continuous Conduction Mode (CCM) – In CCM, the current in the inductor is continuous throughout the entire switching period cycle. Thus, a regulated voltage at the output is obtained, but the output is regulated only if the current is drawn within the limits of the CCM.
• Discontinuous Conduction Mode (DCM) – In this mode, the current in the inductor is pulsating and becomes zero during a portion of the switching time. Therefore, a regulated voltage is not received at the DCM. However, the voltage can be regulated by connecting a feedback circuit from the output to the input.
In this tutorial, a non-isolated boost converter is designed, which means the input and output share the same ground. The boost converter designed in this project will step up from 12V DC to 24V DC with a tolerance limit of +/-0.5V. Once the circuit has been designed and assembled, the value of the output voltage and current will be observed using a multimeter. These values will indicate the efficiency of the boost converter designed in the project.
Required components –
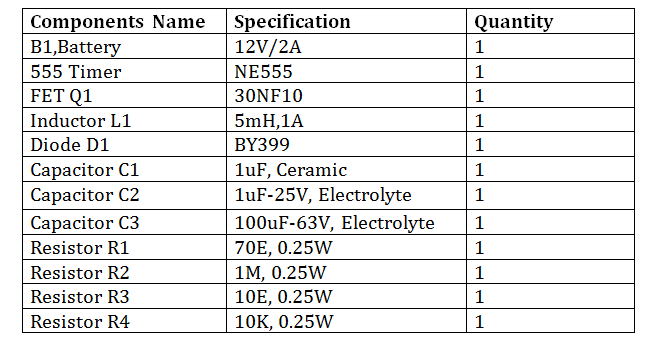
Figure 1: List of components required for Open Loop Boost Converter SMPS
Block diagram –
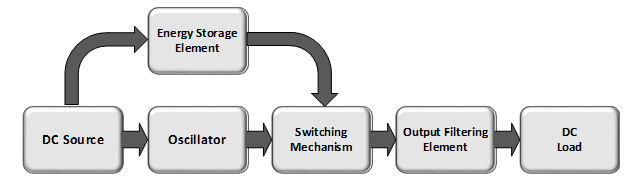
Fig. 2: SMPS Open Loop Boost Converter Block Diagram
Circuit Connections –
In this experiment, an open-loop boost converter operating in CCM mode is designed and component values according to standard CCM equations are calculated for the desired output.
The boost converter has the following circuit blocks –
1. DC Source – A 12V battery is used as the input power source in the circuit.
2. 2. Oscillator and switching mechanism – An oscillator is used to generate a pulse width modulated (PWM) signal of a desired frequency. In this boost converter, 555 IC is used to generate the PWM signal, therefore, 555 IC acts as an oscillator. The PWM signal is a pulse train used to turn the MOSFET on and off. MOSFET is used as switching transistor in the circuit. The 555 is configured in Astable mode with some modifications to the basic circuit. To learn how the 555 IC generates PWM signal, read the 'Generating Square Wave' tutorial.
Care must be taken that the input voltage of 555 does not exceed the specified limit mentioned in its technical data sheet. A pulled-down capacitor should always be used on the control pin of the 555 IC to avoid unwanted ambient noise.
For switching purposes, a transistor and a diode are used as the switching component. For transistor selection, MOSFET is chosen as FETs are known for their fast switching speed and low RDS (ON) (drain to source resistance in ON state). Therefore, an N-channel 30NF10 MOSFET (shown as Q1 in the circuit diagram) is connected in parallel to the input DC source which acts as a switch in the circuit. The switching time of the MOSFET and diode must be less than the rise and fall time of the PWM wave. The diode must offer low voltage drop in the forward bias and the RDS (ON) of the MOSFET must be low.
A gate-to-source resistance must be used to prevent any unwanted triggering of the MOSFET by external noise. It also helps to quickly turn off the MOSFET by discharging its parasitic capacitance. A low resistor value (10E to 500E) should be connected to the MOSFET gate. This will solve the ringing (eddy oscillations) and spike current problem in the MOSFET. The PWM signal voltage level must be greater than the MOSFET threshold voltage. So that the MOSFET can be turned ON completely with minimum RDS (ON).
Another switching component used in the circuit is a diode. The diode switching time must be less than the rise and fall time of the PWM wave. The IC 555 used generates a PWM wave with a rise time of 110ns and a fall time of 90ns. The forward voltage drop of the diode must also be very low, otherwise it will dissipate power, which will further reduce the efficiency of the circuit. Therefore, in this experiment, a BY399 diode that best suits the circuit design is selected.
Before generating the PWM signal, the switching frequency of the circuit needs to be decided. For this boost converter, a switching frequency of 10kHz is selected, which will work well in this converter design.
The duty cycle of the generated PWM signal is another important consideration as it will decide the active state of the MOSFET. The duty cycle can be calculated as follows –
D% = 1- (Vin/Vo)*100
Vo=Desired output voltage, 24V
Vin =Input voltage, 12V
Putting all the values in the above equation, the desired duty cycle is –
D = 50%
A capacitor and resistor of appropriate value should be used to generate the 10kHz frequency and 50% duty cycle. The higher the frequency selected for the switching components, the greater the switching losses. This decreases the efficiency of the SMPS. But the high switching frequency reduces the size of the energy storage element and improves the transient response of the output.
3. Energy storage element
An inductor is used to store electrical energy in the form of a magnetic field. Therefore, the inductor acts as an energy storage element. The value of the inductor can be calculated using the standard CCM equation which is as follows –
Lmin>= Vo /(16* Fs*Io (min))
where, Lmin = minimum value of the inductor
F = 10kHz
Io (min) = Critical value of the output current to maintain a regulated voltage at the output.
Assuming Io (min) = 30mA
Putting all the values in the above equation, the inductor value is obtained as follows –
Lmin>= 5mH
The inductor value must be in accordance with the calculation and its nominal current must be greater than the inductor peak current (standard CCM equation, peak current, Ipk = (Vin*D*Ts)/L)
4. Output filtering element
As a filtering element, a capacitor (shown as C3 in the circuit diagram) is used at the output of the circuit. In normal operation of the Boost circuit, transistor Q1 turns on and off according to the frequency of the oscillator circuit. This generates a pulse train in inductor L1 and capacitor C3, as well as transistor Q1. Since the capacitor is connected to the inductor only in the negative cycle of the PWM signal, this forms an LC filter that filters the pulse train to produce a smooth DC at the output. The capacitor value can be calculated using the following CCM equation – Cmin>= (Io (max) * D)/ (Fs*dVo)
Where, Cmin = minimum value of the capacitor
Maximum output current, Io (max) = 100mA
Duty cycle, D = 0.5
Desired output ripple voltage, dVo
Assuming dVo = 100mV
Putting all the values in the above equation, the capacitance value is obtained as follows –
Cmin>= (0.01 * 0.5)/ 10000*0.01
Cmin>= 50uF
C >= (0.01 * 0.5)/ 10000*0.01
C >= 50uF
As it is the minimum value of capacitor required, so in the circuit a standard value capacitor is used which can be easily available, hence a capacitor of 100 uF is used.
C3 = 100uF
The capacitors used in the circuit must have a higher voltage rating than the input supply voltage. Otherwise, the capacitors will start leaking current due to excess voltage on their plates and will explode. All capacitors must be discharged before working on a DC power supply application. To do this, the capacitors can be short-circuited with a screwdriver and insulated gloves.
How the circuit works –
Any SMPS has some switching components that turn on and off at high frequency and has some storage component that stores the electrical energy while the switching components are in the conducting state and discharges the stored energy to the output device while the switching components are in state no. -driving status.
A simple boost converter consists of the inductor (L), a diode (D), a capacitor (C) and a transistor where the transistor acts as a switch. In the boost circuit, when the switch is closed, i.e., the switching component is in a conducting state, the inductor starts generating a magnetic field and stores energy. The energy stored in the inductor increases the output voltage compared to the input voltage.
When current begins to flow through the switching component, as its path is less resistive compared to the parallel path containing the capacitor and output load, the inductor generates a positive polarity at its left terminal and negative at its right terminal. . Due to the change in polarity, the diode becomes reverse biased. In this condition, the capacitor, which was charged in the previous cycle, supplies current to the load while the switching component goes into a non-conducting state or opens between ground.
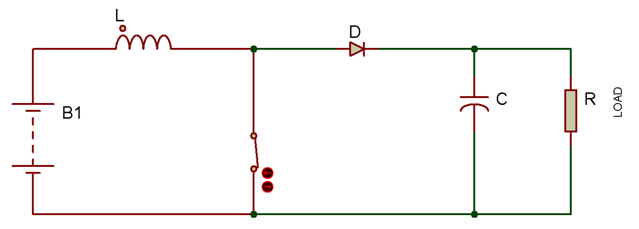
Fig. 3: Circuit diagram showing the ON state of the switching component in the Boost converter
When the switch is open, the current is reduced as the impedance increases, so the magnetic field generated in the inductor begins to collapse and the polarity of the inductor reverses. This makes the diode forward biased and the capacitor now starts charging with a voltage higher than the input voltage. Since the input now has two sources in series, one is the inductor and the other is the battery. Therefore, the output voltage is always greater than the input voltage.

Fig. 4: Circuit diagram showing the OFF state of the switching component in the Boost converter
Therefore, in the ON state, the Diode was in Blocking Mode (OFF) and the Transistor was ON. In the OFF state, the Diode was in conduction mode (ON) and the Transistor was OFF.
So, it can be said that the Boost Converter has two switching components – one is the transistor and the other is the diode. At a time, only one of the switching components conducts, that is, it is in the ON state, while the other enters the non-conducting state, that is, it enters the OFF state.
Testing the circuit –
Firstly, the PWM output of the 555 circuit must be confirmed. The output waveform of the 555 oscillator or timer circuit can be observed on an oscilloscope. The waveform generated in the circuit is obtained as shown in the figure below –
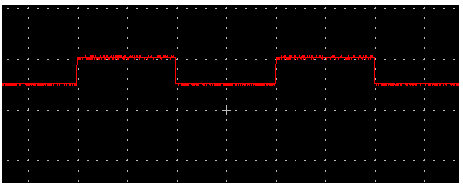
Fig. 5: Graph showing the PWM output of the 555 IC based circuit as observed in a CRO
By measuring voltage and current values with different loads at the output, the following observations were made –
Battery voltage, Vin = 12V
I go
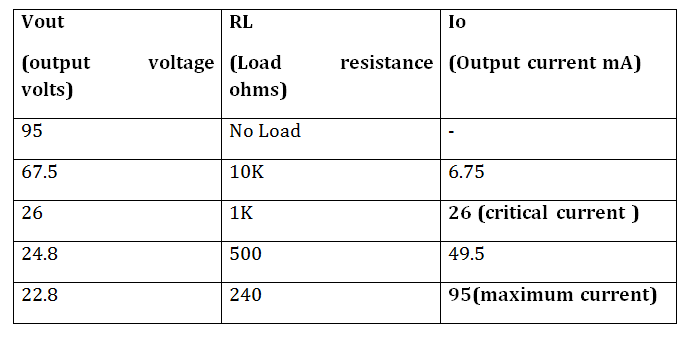
Figure 6: Table listing the Open Loop Boost Converter SMPS output voltage and current for different loads
Thus, it can be seen that within the tolerance limit of +/-0.5V the output current of 49.5mA is obtained.
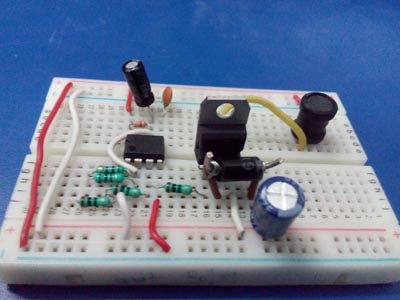
Fig. 7: Open Loop Boost Converter SMPS prototype designed on a breadboard
But as the maximum output current must be 100mA for 24V, there is a voltage drop due to losses in the circuit such as switching and conduction losses of diode and MOSFET, losses in the windings surrounding the inductor core, eddy current losses and hysteresis losses in the inductor, capacitor losses due to ESR (Equivalent Series Resistance) and losses due to Rds(on) of N-MOS. The efficiency of the circuit is maximum when the output current is 49.5mA. The efficiency of the circuit can be calculated as follows –
Efficiency% = (Pout/Pin)*100
(Output power) Pout = Vout*Iout
(Output voltage)Vout = 24.8V
(Output current) Iout = 49.5mA
Pout = 1228mW (approx.)
(Input power) Pin = Vin*Iin
(Input voltage) Vin = 12V
(Input current) Iin = 115mA (measure input current using ammeter)
Pin = 1380mW
Putting all the values,
Efficiency% = 88%
It can be seen that there are certain limitations of this circuit. The output voltage in this circuit is not regulated, it varies for different load resistances. This can be improved by adding a feedback circuit that helps regulate the output voltage. A Boost Converter with feedback circuit is designed in the next tutorial. Secondly, the efficiency of this boost converter design is 88% due to the power losses in the circuit.
This is an open loop boost converter with non-isolated output and operating in CCM mode. It can be used as a switching regulator for LED drivers and as a regulated DC power supply. It can be used to supply power to low-power portable electronic devices. In battery powered applications, when there is space constraint to stack number of batteries in series to achieve high voltage, this boost converter can be used with less number of batteries to supply DC power.
This boost converter is simple to design and uses inexpensive components. It can be easily assembled in a short time. Furthermore, there is no need for control circuits for PWM signal generation in this boost converter design.
Circuit diagrams
Circuit-Diagram-Open-Loop-Boost-Converter-SMPS | ![]() |