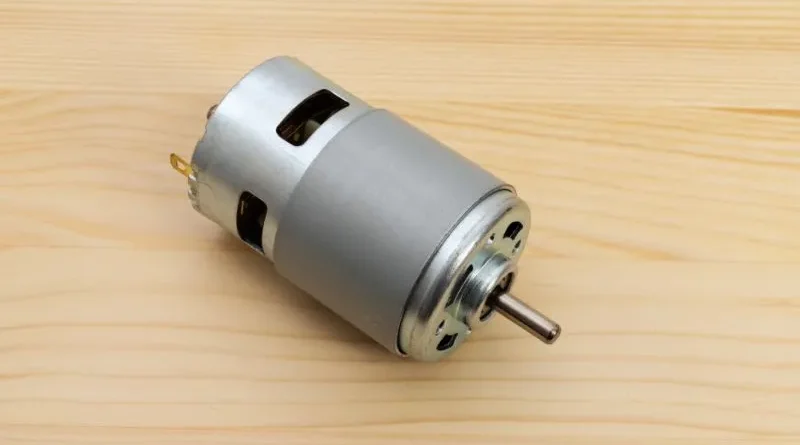
The introduction of DC compound motors reveals a cornerstone of electrical engineering that embodies innovation and versatility. These motors, which combine the properties of series and parallel wound DC motors, are considered performance pillars in numerous industries. From industrial machinery to automotive applications and renewable energy systems, DC compound motors play a central role, providing a unique balance between torque and speed control. Understanding the intricacies of these motors is essential for engineers, technicians and enthusiasts who want to delve deeper into the heart of electrical machines. In this guide, we embark on a journey to unlock the secrets of DC compound motors. We explore its components, types, applications, benefits and maintenance tips, highlighting their importance in the current technological scenario.
Understanding DC Compound Motors
Understanding DC compound motors is crucial to understanding their operation and application. These motors combine the characteristics of both series and shunt DC motors, resulting in a unique combination of characteristics. With components such as armature, field windings, brushes and commutator, these motors offer high starting torque and excellent speed control. This versatility makes them suitable for various industrial applications.
Components of a DC compound motor
To understand how a DC compound motor works, it is important to familiarize yourself with its main components:
- anchor : The rotating part where electrical energy is converted into mechanical energy.
- Field windings : Generates the magnetic field in the motor. In a compound motor there are series and shunt field windings.
- Brushes and commutator : The brushes maintain contact with the commutator and ensure current flow to the armature.
- Housing and Bearings : The housing surrounds the engine components while the bearings allow for smooth rotation.
Types of DC Compound Motors
Compound DC motors can be divided into two main types based on the connection of their field windings:
Cumulative compound engines
Cumulative compound motors have a series of field windings connected in such a way that the flux produced by the shunt field winding is amplified. This configuration increases torque and makes it suitable for high starting torque applications. Cumulative compound motors are widely used in heavy machinery such as cranes, elevators and conveyor belts. Their rugged construction and ability to deliver significant torque during starting make them essential in industries that rely on powerful equipment for efficient operation.
Differential compound engines
Differential compound motors have a series field winding that opposes the flux produced by the shunt field winding. Although they offer better speed control than cumulative compound engines, they typically have lower starting torque. Differential compound motors are ideal for applications where precise speed control is of utmost importance, such as: For example, machine tools, printing machines and textile machines. Their constant speed under different loads makes them ideal for processes that require precision and reliability.
DC Compound Motor Applications
Due to their versatility, DC compound motors are indispensable in numerous industries:
Industrial machines
DC compound motors are widely used in industrial machinery, powering conveyors, elevators, cranes and other heavy equipment. Their robust construction and high torque capacity make them suitable for demanding applications in manufacturing and logistics.
Specific applications
- Conveyor systems
- material handling equipment
- Hydraulic pumps
Auto Industry
In the automotive sector, DC compound motors play an important role in various components and systems. They are used in electric vehicles, power windows, windshield wipers and other automotive applications that require precise speed control and reliable performance.
Specific applications
- Drive systems for electric vehicles
- Electric window mechanisms
- Windshield wiper motors
Renewable energy
DC compound motors are also used in renewable energy systems and contribute to the efficient operation of wind turbines and solar tracking systems. Its ability to constantly regulate torque and speed helps optimize energy production and distribution in sustainable energy systems.
Specific applications
- Yaw mechanisms for wind turbines
- Solar module tracking systems
- Dam gates for hydroelectric plants
Marine applications
DC compound motors power various devices on board ships and boats in marine environments. From propulsion systems to winches and pumps, these engines provide reliable performance, even in difficult conditions.
Specific applications
- Drive systems
- Reels
- Sewage Pumps
aerospace industry
DC compound motors are used in the aerospace industry for propulsion, landing gear operations, and cargo handling. Their compact design, high torque and precise speed control make them suitable for the high requirements of aircraft and spacecraft.
Specific applications
- Actuator systems
- Chassis mechanisms
- Cargo handling equipment
Advantages of DC compound motors
- High starting torque : Provide significant starting torque, making them ideal for applications that require high starting loads.
- Speed Regulation : Provides excellent speed control under different loads, ensuring consistent performance.
- versatility : The ability of DC compound motors to operate in series and shunt configurations gives them the versatility they offer to meet different application requirements.
Maintenance Tips for DC Composite Motors
DC compound motor maintenance is critical to ensure optimal performance and longevity. Proper maintenance helps prevent breakdowns, extend engine life and reduce operating costs. Here are important maintenance tips, divided into subheadings:
Brush inspection and replacement
Regularly check brushes for signs of wear. Worn brushes can result in poor electrical contact, resulting in inefficient engine operation and possible damage to other components. Replace brushes as needed to maintain optimal performance.
Bearing lubrication
Make sure bearings are properly lubricated to minimize friction and reduce wear. Inadequate lubrication can lead to increased heat generation and premature bearing failure. Follow the manufacturer's recommendations regarding the type and frequency of lubrication to ensure the engine operates properly.
Cleaning and ventilation
Keep the engine and surrounding area clean to prevent dust and dirt buildup that can impede airflow and cooling. Clean the engine regularly with compressed air or a soft brush to remove accumulated dirt. Provide adequate ventilation to dissipate heat generated during operation to prevent overheating and possible engine damage.
Checking electrical connections
Periodically inspect electrical connections, including terminals and wiring, for signs of corrosion, loose connections, or damage. Faulty electrical connections can cause voltage drops, overheating and engine malfunction. Tighten loose connections and repair or replace damaged wiring to maintain electrical integrity.
Regular testing and monitoring
Perform regular testing and monitoring of engine performance using diagnostic tools such as multimeters or vibration analyzers. Monitor important parameters such as voltage, current, temperature and vibration levels to detect anomalies that indicate potential problems. Regular testing allows for proactive maintenance and early detection of issues before they turn into serious problems.
Conclusion
In summary, DC compound motors are a testament to the ingenuity of electrical engineering, offering a balance of torque, speed control and versatility for many applications. From industrial machines to automotive systems, from renewable energy systems to marine and aviation technologies, these engines play a critical role in powering critical devices around the world. Their ability to provide high starting torque, maintain precise speed control and adapt to diverse operating conditions makes them the preferred choice of engineers and technicians. By understanding their components, benefits and maintenance requirements, users can harness the full potential of DC compound motors, ensuring greater productivity, reliability and efficiency across a wide range of industries and applications.
Common questions
1. What are the main differences between series and shunt field windings in a compound DC motor?
Series field windings are connected in series with the armature and provide high starting torque but limited speed control. Shunt field windings, on the other hand, are connected in parallel with the armature and provide better speed control but lower starting torque.
2. Can DC compound motors be used in both AC and DC systems?
DC compound motors are designed specifically for DC systems and may not work efficiently in AC systems without appropriate conversion mechanisms.
3. How can I determine the appropriate size of a DC compound motor for my application?
Factors such as required torque, speed, duty cycle and environmental conditions are critical in selecting the correct motor size. Advice from a qualified engineer or engine specialist can help ensure that the engine will truly meet your needs.