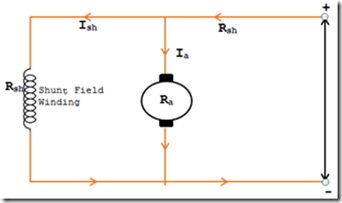
Performance and functionality
The classification of DC motors is based on several factors, including design, electrical configuration, and operating characteristics. Understanding the operating principles behind these classifications is crucial to effectively using DC motors in a variety of applications. Let's delve deeper into how the main types of classified DC motors work.
Similar to generators, DC motors are also divided into three types according to field winding connections. They are
-
Shunt Motor
-
Series wound motor
-
Composite winding motor
- Brushed DC Motors
- Brushless DC Motors
Shunt Motor
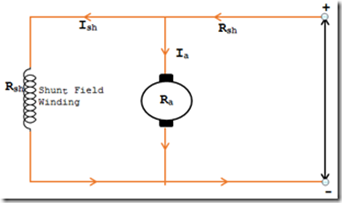
Series wound motor
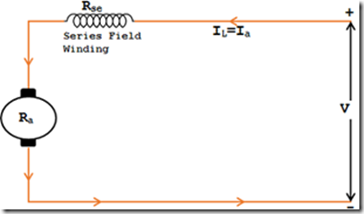
Composite winding motor
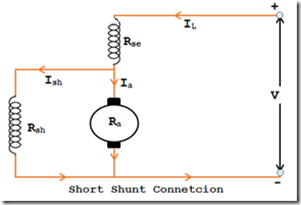
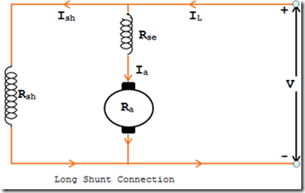
DC motors with brushes
Brushed DC motors consist of a rotating armature (the rotor) and a stationary set of magnets (the stator). The rotor is connected to a commutator and brushes that transmit electrical current to the armature windings. When electric current flows through the armature windings, a magnetic field interacts with the stator magnetic field. This interaction creates torque that turns the rotor and generates mechanical energy.
Brushless Motors
BLDC motors offer precise speed control, making them suitable for applications that require precise and constant speeds. Speed control is achieved using sophisticated electronic switching methods such as sensor-based or sensorless control. Sensorless control uses the motor's back electromotive force (EMF) to determine rotor position, while sensor-based control uses Hall effect sensors or encoders for accurate feedback. BLDC motors have excellent torque-to-weight ratios and power densities, allowing them to deliver high torque despite their compact size. This feature makes them suitable for space-limited applications that require a high power-to-size ratio.
Classification criteria
- Speed control: Some DC motors maintain a constant speed, while others are designed for variable speed applications.
- Starting torque: Motors with high starting torque are essential for applications that require heavy starting loads.
- Control Methods: DC motors can be controlled using various techniques such as armature voltage control, field flux control, or a combination of methods.
- Efficiency and energy consumption: Different types of motors have different efficiencies, which affects energy consumption and operating costs.
Forms
- Due to their simplicity and efficiency, PMDC motors are used in small appliances, tools and toys.
- Series wound motors are suitable for drive systems and cranes that require high torque.
- Due to their constant speed, shunt motors are often used in conveyor belts, lathes and fans.
- Composite winding motors are suitable for applications that require speed and torque.
- Separately excited motors are widely used in industries where precise control is required, such as robotic systems and machine tools.
Conclusion
Each classification offers unique benefits and capabilities, from timeless brushed DC motors to innovative brushless DC motors. Thanks to their simplicity and reliability, brushed DC motors continue to be the workhorse in countless applications. On the other hand, brushless DC motors are gaining popularity in modern industries due to their efficiency, precise speed control and maintenance-free operation. We also look at the characteristics of series, series, and compound DC motors, each with different features and applications. DC shunt motors offer speed control and relatively constant torque-speed factors, while DC series motors offer high starting torque and are used in high load applications. Compound DC motors combine the best of both worlds, offering better speed control and torque characteristics.