
When you explore the area of V/F Control of induction motors, you will discover that balancing the voltage-frequency relationship is not just about maintaining efficiency - it is important to the longevity and performance of your motors. With this technique you can adapt power supply parameters to load conditions, optimize power consumption and reduce wear. But remember: as simple as V/F control may seem, the real challenge lies in its implementation. Are standard methods sufficient for the different requirements of modern industries or are more needed? Innovative approaches handle complex applications? Let's decipher the nuances that make this topic so important and exciting for anyone involved in engine management.
The central theses
- V/F control optimizes induction motor efficiency by adjusting the voltage-frequency relationship.
- Provides consistent torque delivery at different engine speeds, improving performance.
- It includes components such as microcontrollers and inverters to dynamically control engine operation.
- It simplifies control and allows easy configurations and adaptation to different operating conditions.
- Reduces energy consumption and operating costs and extends engine life.
Understanding Induction Motors
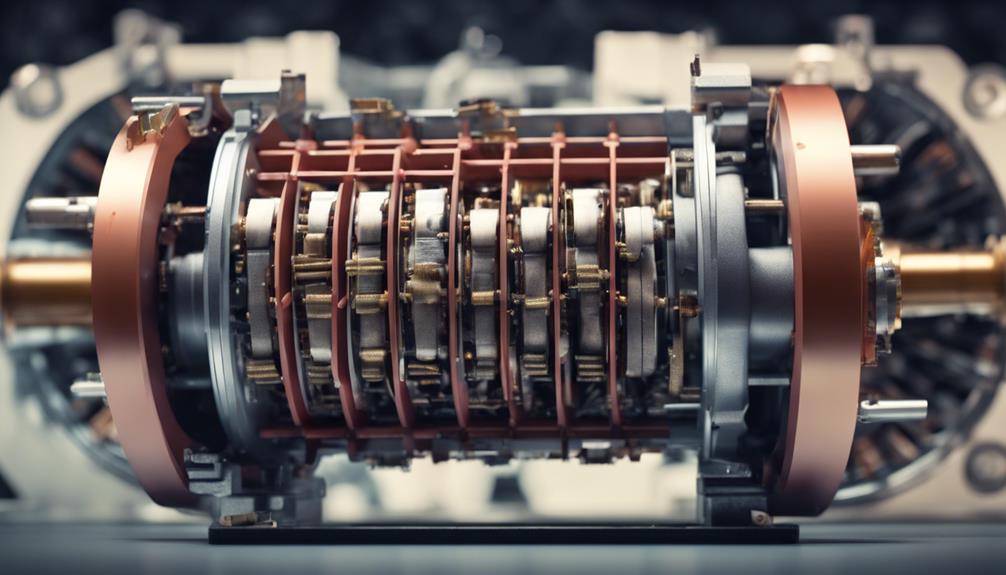
To understand how induction motors work, you need to understand that electromagnetic induction converts electrical energy into mechanical energy. This process creates a rotating magnetic field driven by alternating current (AC) in the stator windings, which then induces a current in the rotor and rotates it.
Engine efficiency is an important aspect to consider. It measures how effectively a motor electrical energy it consumes into mechanical force . Higher efficiency means less energy lost as heat, making the engine more economical and environmentally friendly in the long run. Several factors, including engine design, quality of materials used and operating conditions, affect this efficiency.
Induction motor starting methods are also important because they help minimize the load on the power supply during motor starting. Common methods include direct starting, star-delta starting, and autotransformer starting, each of which provides different levels of current reduction to protect the motor and electrical grid. Very High Starting Currents Understanding these methods will help you optimize performance and extend engine life.
V/F Control Basics
Now let's explore the basics of V/F control, a method that optimizes the speed and torque of an induction motor by adjusting the voltage-frequency relationship. By mastering these control principles, you can not only optimize the numbers, but also improve performance and maximize efficiency.
V/F control isn't just about keeping the engine running, it's about making it run better than ever. Here's why you should care:
- Constant torque output: You get strong, stable torque throughout the entire engine speed range, ensuring smooth, reliable operation.
- Improved motor efficiency: By optimizing voltage and frequency, energy is saved and motor life is extended, resulting in fewer breakdowns and lower maintenance costs.
- Simplified control mechanism: Forget complex algorithms. V/F control simplifies the process and makes it easy to manage and adjust settings as needed.
- Adaptability: Whether it's load changes or different operating conditions, V/F control adapts seamlessly, giving you peace of mind knowing your engine can handle whatever comes your way.
Importance of the voltage-frequency relationship
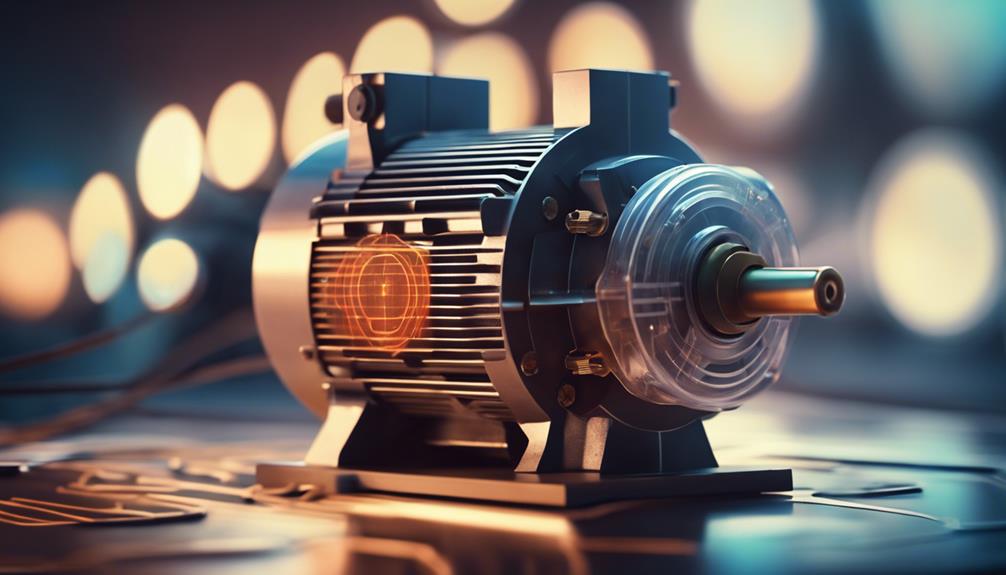
Understanding the voltage-frequency relationship is crucial because it has a direct impact on the efficiency and performance of your induction motor. If you examine the operation of these motors, you will find that maintaining the correct voltage-frequency (V/F) ratio for torque stability and efficiency optimization.
This is why it is important: the V/F ratio determines the magnetic river in the motor's air gap. If this ratio is too high, the engine will saturate, wasting energy and potentially overheating. On the other hand, if it is too low, the engine will not produce enough torque, resulting in a loss of performance.
Components in V/F control systems
The V/F control systems that control the performance of induction motors consist of several main components. Understanding these elements is critical to optimizing engine control. They form the backbone of effective control strategies and help you adapt system parameters to your needs.
Here's a breakdown of the main components:
Microcontroller or programmable logic controller (PLC)
This is the brains of the operation. It processes input signals and executes control strategies that adjust the voltage and frequency applied to the motor, ensuring maximum performance.
converter
The inverter plays a fundamental role in converting the source's direct current into alternating current with variable frequency and voltage, and directly affects the speed and torque characteristics of the motor.
Feedback Sensors
These sensors provide real-time data on motor speed, voltage and current. This feedback is critical for adjusting control strategies to maintain desired engine performance.
Human-machine interface (HMI)
The human-machine interface (HMI) allows you to interact with the control system and monitor and adjust system parameters in an easy-to-use manner based on real-time data and performance metrics.
Each component ensures that the induction motor works efficiently and reliably under different operating conditions.
V/F control implementation
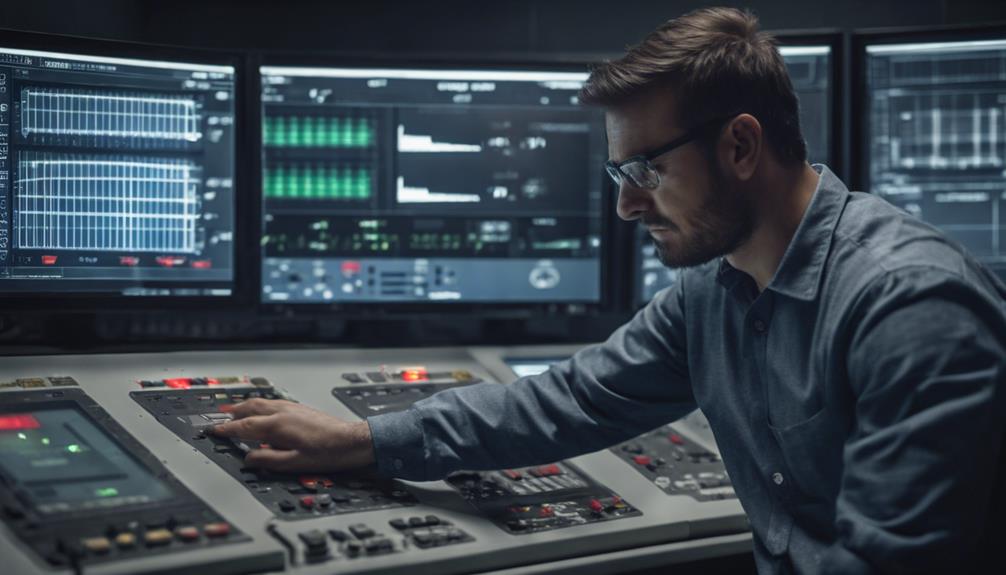
After covering the main components of V/F Control Systems, let's see how this control method can be implemented to optimize the performance of induction motors.
You start by choosing the right hardware. Proper inverter is important to meet the power needs of the motor while providing reliable performance. Remember to consider the inverter's compatibility with other system components.
Next, focus on the Control Algorithms that form the heart of the V/F control system. These algorithms determine how voltage and frequency are adjusted for maximum motor efficiency and torque. You have to Microcontroller or processor in your control system to run these algorithms effectively. Choose a processor that can handle the computing load and perform efficiently under your system's operating conditions.
Configure the Feedback Loop to Monitor Motor Speed and Load Fluctuations . This loop informs its control algorithm and allows dynamic adjustments to the voltage-frequency relationship and thus ensures that the motor runs smoothly.
Advantages of V/F control
The main advantage of V/F control is that it can optimize the energy efficiency of induction motors, saving significant operating costs. Adjusting the voltage-frequency relationship ensures that the motor output power directly matches the load requirements. This precise control not only reduces energy waste, but also improves the life of your motor by preventing stress caused by excessive use.
Here are four compelling reasons why you'll appreciate V/F control:
- Reduced energy costs : Who doesn't want to save costs? V/F control minimizes the energy consumption of your induction motors and results in significantly lower electricity bills.
- Longer device lifespan : Less mechanical and electrical stress means your equipment lasts longer. Imagine not having to replace engines as often – more savings and less effort.
- Simplified Operation : V/F control automates the complex processes of managing engine speed and torque. When you know your engine's performance is optimized, you can focus on other aspects of your operation.
- Improved process efficiency : Better control of motor speed and torque allows your entire production line to run more smoothly, improving overall efficiency and production quality.
Using V/F control increases energy efficiency and improves cost-effectiveness, making it a smart choice for industrial applications.
Challenges and solutions
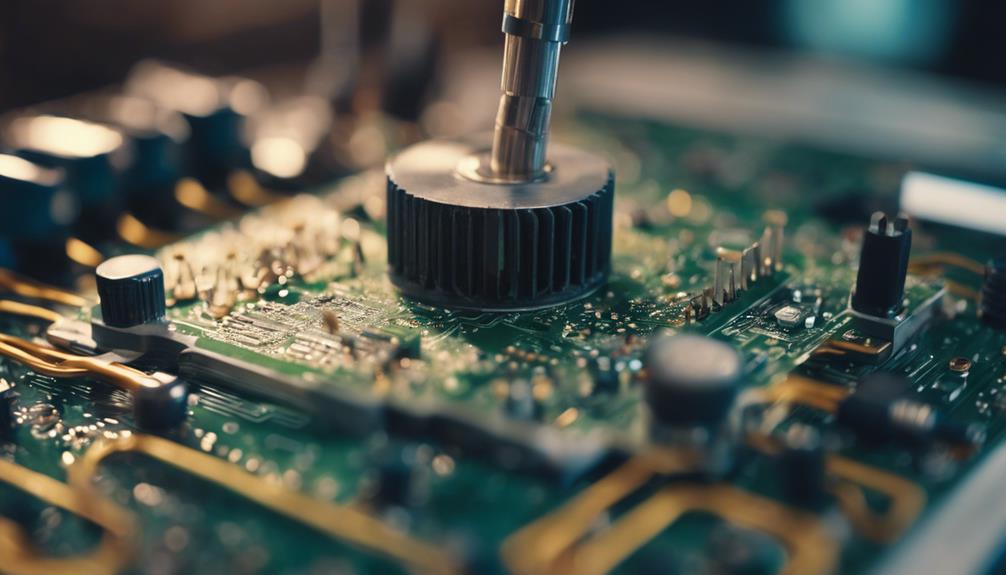
Although V/F control offers numerous benefits, implementing this technology into your systems can present some challenges. The main questions are usually related to torque dynamics and efficiency optimization. Let's examine these challenges and explore practical solutions.
First, controlling torque dynamics can be difficult. With V/F control, as the frequency decreases, it becomes difficult to maintain sufficient torque at low speeds. This problem often results in suboptimal engine performance. To combat this, you can implement an improved V/F curve strategy that more accurately matches voltage to load requirements.
Second, optimizing efficiency is important but also challenging. V/F control tends to be less efficient under partial load conditions. One solution here is to integrate energy-efficient algorithms that dynamically adjust voltage and frequency based on real-time power and load data, ensuring efficient performance under different operating conditions.
Here is a brief overview of the challenges and solutions:
Challenge | Solution |
---|---|
Torque dynamics | Improved V/F Curve Strategy |
Efficiency optimization | Integration of energy efficiency algorithms |
V/F control compared to other methods
Let's compare V/F control to other engine control methods to compare performance and versatility.
When diving into the world of engine controls, V/F control often proves to be an extremely simple yet effective strategy, especially in applications that require consistent torque characteristics and a simplified control architecture. But how does it compare to its competitors? Here's a straightforward breakdown:
- Torque response and stability : V/F control ensures stable torque, which is essential in applications with high loads or when precise speed control is not of paramount importance. This method guarantees smooth operation without the problems that can occur with more complex systems.
- Efficiency analysis : In industrial environments, efficiency is key to selection. V/F control generally provides good efficiency at higher speeds, but can lag at slow operation compared to vector control methods that optimize power delivery over a wide range of speeds.
- Cost effectiveness : If you have your budget under control, V/F control is an excellent solution. It requires less sophisticated hardware and is easier to implement, reducing acquisition and maintenance costs.
- Simplicity and reliability : For many people, the less complex the better. The V/F controller offers a user-friendly interface and simple mechanics, reducing the likelihood of failure and simplifying maintenance.
When considering your options, remember that the best choice will depend on your specific needs and the requirements of your operation.
V/F Control Case Studies
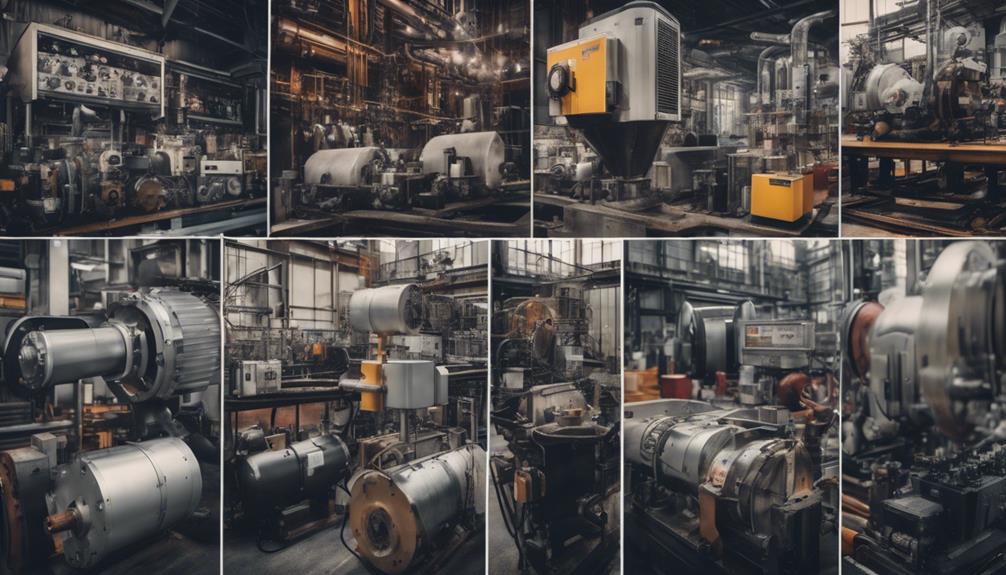
To ensure effective V/F Control consider these real-world applications where operational efficiency has been greatly improved. Implementing V/F control on spindle motors at a large textile mill significantly improved field performance. Before Fluctuations in the power supply caused frequent outages. With V/f control the motors stop at constant speed regardless of load fluctuations, resulting in smoother operation and less component wear.
In another case, a water treatment plant faced different configurations of the different pumps used in the process. The integration of V/F control allowed each pump to operate efficiently at different flow rates and pressures without the need for manual recalibration. This adjustment not only simplified operations, but also saved significant energy costs .
These examples show how V/F control adjusts various industrial environments , thereby improving efficiency and reliability. The ability to automatically adjust frequency and voltage according to changing requirements ensures your machines deliver consistent performance even under varying operating conditions.
Don't you think about how V/F control could optimize your setups? Using this technology can significantly improve your operational performance and savings measures .
Future of V/F Control Technology
Looking to the future, V/F control technology promises even greater advances in efficiency and adaptability for industrial applications. You will witness a transformation that is streamlining operations and having a profound impact on the environmental footprint and operational reliability of industries around the world.
- Smart sensor integration : Imagine a world where every small change in engine performance is monitored in real time. Smart sensors will revolutionize V/F control by providing continuous data resulting in unprecedented accuracy in engine control and energy consumption. It's not just about saving electricity, it's about optimizing every watt.
- Predictive maintenance models : Just imagine – no more unexpected downtime. With predictive maintenance models, you know exactly when a component needs attention, drastically reducing failures and extending useful life. This means less waste, lower costs and more productivity.
- Improved adaptability : As V/F technology advances, so does its ability to adapt seamlessly to varying loads and environmental conditions. This adaptability means that machines operate at maximum efficiency in all circumstances.
- Increased sustainability : Through better control and efficiency, industries can significantly reduce their environmental impact. Not only do they reduce costs, they are also part of a broader movement towards greater sustainability.
This future is not just a possibility – it is on the horizon and will change the way we think about and interact with technology.
Conclusion
You have seen how V/F Control optimizes induction motor performance by controlling the Voltage-Frequency Relationship . This method ensures consistent torque, increases efficiency and extends engine life.
By integrating modern electronics such as inverters and microcontrollers, the implementation of V/F control is uncomplicated and guaranteed energy savings and greater operational efficiency.
As technology advances, we can expect the development of even more sophisticated and efficient V/F control systems. Engine management and performance in a variety of applications.