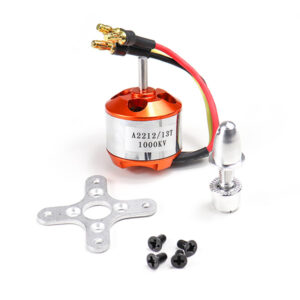
Figure 1. Drone engine
The electric motor, electronic speed controller, and flight controller are the three main components that make up the propulsion system of any drone. It is now quite common to get a flight controller-ESC combination for building FPV drones, making electric motor selection often an independent affair. However, it is really necessary to have a compatible combination of all three components – electric motors, flight controller and ESC to get the desired performance from the drone. A compatible combination of all three main components is automatically obtained when they are selected according to specific drone size and weight criteria.
It is now common for electronics manufacturers and enthusiasts to try their hand at building FPV drones. With advances in battery technology and other drone electronics, it's much easier to build a drone now than ever before. First, the manufacturer must decide the size of the drone. The size of the drone can be estimated by calculating the expected weight of the drone. The weight of the drone is calculated by adding the weight of all the components and accessories to be assembled as in a drone. Alternatively, the size of a drone could be decided and selected according to the other compatible components within an estimated weight constraint.
Either way, with the drone size selected, the manufacturer can focus on the drone's structure. Since the drone structure and propeller size are related, the appropriate propeller size can be calculated from the drone size. The diagonal length of the drone structure must be at least 3 times the size of the propellers. According to the size and weight of the propeller, the lifting thrust and speed of the drone are calculated. These factors are most important when selecting drone motors. Although there are several other specifications that must be considered and taken care of when finalizing the drone motors. In this article, we will take a look at all the factors that should be considered before purchasing a set of drone motors. Let's start.
How do drone engines work?
Drones can be built using brushed or brushless motors. Brushed motors are generally only used in toy drones and mini-drones. All commercial drones use brushless motors. Brushless motors are also common in DIY drone projects; they are preferred due to minimal friction and energy loss in the engine. Whether it is a brushless or brushed motor, the operation of both types is based on the same principle of electromagnetism. In both types, electromagnets and permanent magnets are used. When electromagnets are charged by current, a temporary magnetic field is formed, which interacts with the magnetic field of permanent magnets. The repulsive and attractive forces between the permanent magnets and the electromagnets cause the motor shaft to rotate.
Brushless vs. brushless motors brushed motors
The first thing to consider is selecting between brushed and brushless motors. Brushed motors are only suitable for small drones. These engines are not very energy efficient. Nowadays, for all types of drones, brushless motors are preferred. Brushed motors are only used where drone performance can be compromised to reduce costs, such as in the case of toy drones. Unless there is a tight budget constraint, you should use brushless motors for your drone project.
Key Factors in Engine Selection
Once you have completed your engine type selection, you will need to evaluate the purchasing options available on several factors. Some of the most important factors to consider include:
- Drone weight and structure
- Thrust Requirement
- Engine Size
- Mounting pattern
- KV classification
- Current and voltage ratings
- Poles and magnets
- Engine torque
- KV vs. torque constant
- Consequence
- Motor winding
Drone weight and structure
The first thing now is to calculate the weight of the drone. Consider all the components that will make up or be attached to the drone – the drone frame, flight controller, ESCs, motors, propellers, battery, camera, antenna, etc. You should also take into account 10 to 20% extra weight (it would be better to overestimate than underestimate). With an estimated drone weight, you can determine the frame size. The chassis size will provide the maximum allowable propeller size. Ideally, the maximum propeller size is one-third of the chassis dimensions.
Determining thrust requirements
You now have an estimated weight of the drone and have selected a frame size. Next, you need to decide the thrust requirements of the drone. The maximum thrust of all engines must be at least twice the weight of the drone. If the weight of the drone is 1Kg, all motors must produce a thrust of at least 2Kg. If it is a quadcopter, this means that each engine must produce at least a maximum thrust of 500 grams. This is almost essential. Otherwise, the drone will not be able to get up into the air. Ideally, for a normal drone, the thrust-to-weight ratio should be 3:1 or 4:1. This is the ideal ratio for normal drones, where the drone can be easily maneuvered and also has the capacity to carry extra payloads.
The ideal thrust-to-weight ratio is different for different types of drones. For normal drones, the aspect ratio should be 3:1 or 4:1. For freestyle drones, the desired aspect ratio is 5:1. For racing drones, the ratio of 10:1 and 14:1 is preferred. The higher the thrust-to-weight ratio of the drone, the more difficult it will be for the pilot to maneuver it. A drone with a high thrust-to-weight ratio can bounce even with a light touch of the accelerator.
Engine Size
As already mentioned, a drone motor, brushed or brushless, consists of electromagnets and permanent magnets. Electromagnets are present in the form of metallic coils. These metallic coils form the motor’s stator. The coil wire is enamelled for insulation and preventing short circuits. The coils are wound on posts with an extremely thin layer of insulation between them. The posts are made of thin laminated metal plates. When current flows through metal coils, a temporary magnetic field is generated, which interacts with the magnetic field of the permanent magnets causing rotation.
Permanent magnets are attached to the inside of the motor bell. The motor bell acts as a protective case for the permanent magnets as well as the metal coils. The motor shaft is connected to the motor bell. When the change in magnetic fields causes rotation, the shaft transfers torque from the engine to the propellers.
The size of a motor is determined by the width and height of the stator. This is indicated on the motor by four numbers – XXYY, where XX indicates the width or diameter of the stator in mm and YY indicates the height of the stator in mm. The larger the size of the engine, the greater the torque generated by it and the greater thrust it will produce. As the engine size increases, however, its responsiveness is reduced. Additionally, large engines are heavier than smaller engines. The engine size must be determined according to the maximum thrust requirement of each engine in a multicopter. Since you should have already determined the required thrust-to-weight ratio, you should have derived the maximum thrust required from each engine. Now, you will need to list the engines that meet the desired thrust requirement and select the smallest engines that meet the given thrust requirement.
Wider vs. larger engines taller
BLDC motors of various sizes will meet the desired thrust requirements. Some of these motors will have wider stators, while others will have taller stators. Motors with a wide stator have greater inertia. Larger motors require more energy to change rotation speed. As a result, these engines are less responsive. Wider engines, however, have greater surface area, allowing for better cooling. The wider stator also allows larger bearings to fit, improving the engine's durability, efficiency and stability.
On the other hand, narrow engines respond better, but may not be as effectively cooled. To decide between wider or taller motors, one must consider the use case of the drone. For drones that need to lift payloads, responsiveness may be somewhat compromised in lieu of better cooling. Therefore, wider engines should be preferred in this case. Drones carrying cargo need to be flown carefully, so less responsiveness is indeed preferable in such drone designs. On the other hand, a racing drone should be as responsive as possible. For a racing drone, a higher engine is suitable. Overall, how you intend to maneuver the drone, i.e. slow or fast, and whether the drone needs to lift payloads or not will be the deciding factors for selecting wider or taller motors.
KV classification
Next, you need to look for the KV rating of the motor. The KV rating is the number of engine revolutions per minute when one volt is applied to the engine at no load. If a drone motor has a KV rating of 920 and is powered by a 3S LiPo battery, i.e. a 12.6V battery, it will spin at 11,592 RPM without a propeller mounted on it. Motors with higher KV ratings have shorter windings and low internal resistance. As a result, these engines tend to heat up prematurely. Heating is obvious as most taller motors have higher KV ratings. Engines with a high KV rating spin at higher speeds and produce more thrust.
It is the norm to combine high KV motors with lighter propellers and low KV motors with heavier propellers. If a high KV rating engine is combined with a heavy propeller, the engine will attempt to turn the propeller at maximum speed. Due to the heavy propeller, more torque will be required and the motor will consume more current. It is possible that too much current drawn by the motor could damage the ESC or the MOSFETs within it. Likewise, if a low horsepower KV engine is combined with a lighter propeller, it may not be able to produce sufficient thrust.
If you have already concluded the use of wider engines considering good maneuverability at slow speeds, a low KV rating engine in combination with heavier propellers should be selected. If your drone is designed to fly without any need to carry a payload, select a taller motor with a high KV rating in combination with lighter propellers.
It should be noted that the KV rating is only a rough estimate of engine speed made by engine manufacturers. The engine may rotate at lower RPM due to air resistance; The KV rating is an estimated engine speed for the engine not mounted with the propeller. Whether a low KV rating engine is combined with a heavier propeller or a high KV rating engine combined with a lighter propeller, the combination must produce the desired thrust-to-weight ratio.
Engine torque
The torque generated by a motor depends on the volume of the stator, the types of permanent magnets used in the motor, the quality of metal coils, the construction of the motor (such as number of poles and insulation gap), etc. an engine, the heavier it will be. As long as there are two motors with the same stator volume, preference should be given to the lighter motor. The greater the torque of an engine, the more responsive it will be to the pilot's instructions. Too much torque or thrust, however, can cause the drone to jerk, making it difficult for the pilot to control. These sudden movements are accompanied by voltage or current spikes in the motor, which can damage the ESC unit. For a given torque or thrust, a lighter engine should always be selected. Motors with lower torque and lower RPM should be used where the drone needs to fly slowly and smoothly carrying a payload.
KV vs. torque constant
The torque constant of a drone motor is the amount of current consumed by the motor to produce a given torque. The torque constant and KV rating of an engine are theoretically unrelated. Still, it is observed that high KV rating motors have a high torque constant, and low KV rating motors have a low torque constant. This means that a high KV rating motor draws more current to produce the same amount of torque compared to a low KV rating motor. Due to high current consumption, energy efficiency is affected. This is why high KV rating motors end up being less energy efficient compared to low KV rating motors. To ensure energy efficiency, it is important to choose an ideal KV rating so that the torque constant is not too high to impact efficiency. A motor with an exaggerated torque constant can damage the ESC and cause engine heating problems. With this motor, battery life is reduced and there may be more wear on the wires, motor and MOSFETs.
Current voltage and efficiency
Voltage and current ratings are important when selecting a BLDC motor for drone. The higher the motor voltage, the more current it tends to draw from the battery. You must calculate the maximum current drawn by the motor when it operates at the highest voltage and generates maximum thrust. The rated current of the ESC must be greater than the maximum current consumed by the motor. The direct current rating of the ESC may not need to be greater than the maximum current drawn by the motor. But to ensure reliable and safe operation, the rated breakdown current must be greater than the maximum motor current. Even if the direct current rating is on the higher side, this is better.
N&P on engine
Drone motors are marked with N&P ratings such as 12N15P, which indicates the number of electromagnets or poles in the motor's stator and the number of permanent magnets. A motor with fewer poles has greater torque output, while a motor with more poles has smoother operation due to the uniform distribution of the magnetic field. As drone motors are three-phase, the number of poles is always a multiple of 3. For BLDC motors size 22XX and 23XX, the 12N15P configuration is the most common. The number of poles and magnets does not directly impact the motor's performance. It may, however, be necessary to know the number of poles and magnets in the motors to configure certain settings in the flight controllers, such as enabling RPM filters.
Mounting pattern
Size 22XX, 23XX and 24XX drone motors have a 16x16mm or 16x19mm mounting pattern. A drone structure must support both standards. These motors are secured with M3 screws. The length of the screws should be 2 mm longer than the thickness of the drone arm. For example, if the drone arm is 5mm thick, the M3 screws for mounting the motors should be 7mm long.
Motor winding
Just as the number of poles in a motor affects the torque output and smoothness of the motor, the motor winding or turns around a pole also affect the motor's performance. The motor winding is related to the current capacity and torque output of the motor. If the motor uses thick wire to wind, it will be able to handle a larger current through it. Due to the thick wire, the internal resistance of the wire is less likely to result in a high KV rating. Winding the thick copper wire, however, reduces the stator's electromagnetic field, resulting in lower torque.
On the other hand, if a thin wire is used for winding, its tolerance to high current consumption is reduced. The winding produces a good electromagnetic field resulting in high torque, but due to the high internal resistance of the fine wire, the KV rating is reduced.
Motor manufacturers deal with this torque versus KV rating dilemma by increasing the number of windings while using thick copper wire. The thick wire ensures that the motor can withstand high current consumption, and the greater number of windings improves the stator's electromagnetic field, resulting in greater torque.
In fact, motor windings come in two options – single-wire and multi-wire. The winding of the single chain motor consists of a thick copper wire with a smaller number of turns around the pole. Due to the large gap between the thick wires, the number of turns is obviously limited. These motors can handle large current draw and can run on large voltage batteries such as 6S.
The motor's multifilament winding has the same thick wire divided into three thinner wires. These motors produce strong electromagnetic fields and offer high torque. Although large current consumption may damage the winding or cause it to break. The KV rating for multifilament motor windings is obviously lower.
Engine bearing
The engine bearing has a direct impact on the durability and smoothness of the engine. Bearing size is determined by the difference between the inner diameter and outer diameter of the motor. Motors that have large bearings are more durable. Motors that have small bearings are more stable and smoother in operation. The size of the motor shaft is determined by the inner diameter of the bearing. Many engine manufacturers market their engines with ceramic bearings instead of steel bearings. The ceramic bearing is smoother, but can break.
Motor movements
The drone's motors are rotated in opposite directions to stabilize the drone in the air. If all the motors were rotating in the same direction, it would be very difficult for the drone to get up into the air and maintain proper orientation. This is why some motors rotate clockwise, while others rotate counterclockwise. Motors mounted diagonally opposite each other always rotate in opposite directions, that is, one motor rotates clockwise and the other rotates counterclockwise. Figure 2 demonstrates common engine rotation patterns for different multicopters.
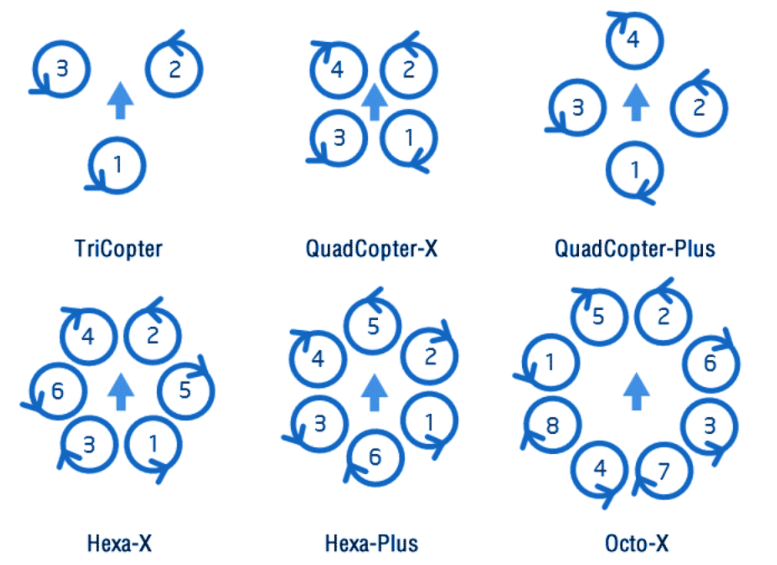
Figure 2. Drone motor rotation directions in different multicopters.
Engine Connections
The drone's motors can be rotated clockwise or counterclockwise. Brushed DC motors have only two wires. Brushless DC motors have three wires. These wires connect to the ESC. When connected one way, the motor rotates clockwise or counterclockwise. To reverse the direction of rotation, any two connections to the ESC can be swapped. The direction of rotation of the engines can also be changed by the flight controller.
Conclusion
There are several factors that must be considered when selecting a BLDC motor for a drone. First, you need to decide the weight and size of the drone’s frame. From there, you get the necessary boost from the engine. According to the thrust requirement, you can select an engine size. Depending on the desired nature of the flight, i.e. whether the drone should fly slowly and smoothly carrying a payload or should fly fast and responsive without a payload, you can decide on the nature of the engine – wider or taller, KV rating, torque and constant torque. The maximum current draw and voltage rating of the drone's motor can then be used to determine a suitable ESC for the drone. In addition to these factors, other specifications such as number of poles, motor winding type, bearing and mounting pattern can be considered to further refine motor performance. Motors are connected in a drone to rotate clockwise and counterclockwise. Diagonally opposite pairs of motors rotate in opposite directions to keep the drone's flight stable in the air. The direction and rotation of the engines can also be changed by the flight controller. Table 1 summarizes the expected specifications of a drone motor according to the desired performance of the drone.

Table 1.
Table 2 provides a rough estimate of suitable propeller size, engine size and KV rating according to chassis size.
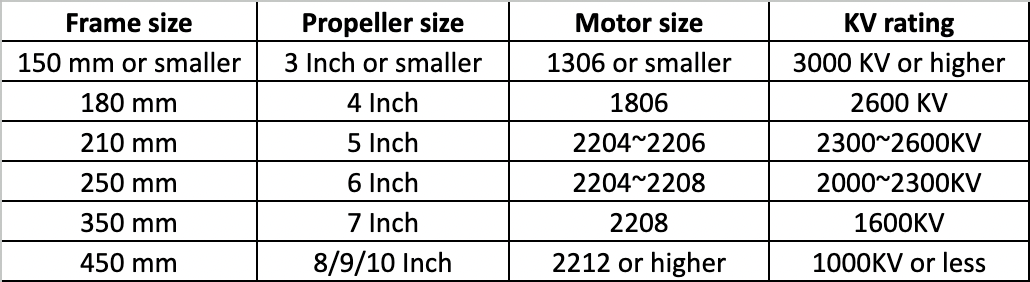
Table 2.