“10,000 watts” has been a hot topic in the laser industry for the past two years.
Currently, the 10,000 watt laser has been increasingly recognized and accepted by the market.
During this period, we received feedback from some users about the challenges they faced during the commissioning of the 10,000 watt laser cutting process.
To solve these difficulties, we have compiled a list of common problems and provided corresponding solutions for your reference.
Commission c method revealing process of carbon steel thick plate
- To debug the carbon steel cutting process with fiber laser cutting machines with power greater than 10,000 watts, start by referring to the cutting process parameter table to obtain a shiny surface on thicker carbon steel and stabilize the cutting process for thicker carbon steel.
- After adjusting the drilling process parameters, ensure that the cutting efficiency and quality meet your needs.
- After adjusting the cutting and drilling process, perform a small batch cutting to check the consistency of the process and its effect.
Table of common problems and solutions for debugging carbon steel cutting with a 10,000+ watt laser
Thickness and surface | Problem | Solutions |
---|---|---|
25mm glossy surface 30mm glossy surface 40mm matte surface |
Cutting nozzle heating | 1. Increase the nozzle size |
2. Clean the lens if it is dirty | ||
3. Lower the cropping focus | ||
Rough cutting surface | 1. Increase the cropping focus | |
2. Reduce the nozzle size | ||
3. Reduce cutting gas | ||
4. Increase cutting speed | ||
Hanging slag cutting | 1. Inadequate cutting speed | |
2. Increase cutting air pressure | ||
3. Improper cropping focus | ||
Inconsistent cutting surface | 1. The nozzle outlet is not round | |
2. The laser is not in the center of the nozzle |
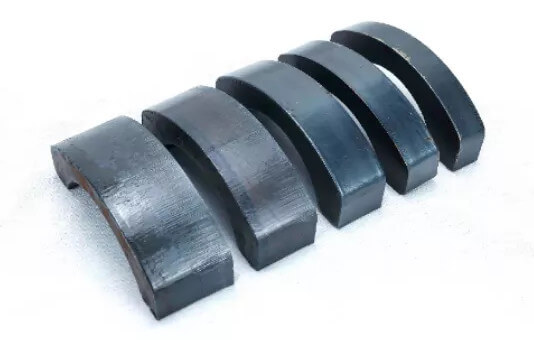
16-40mm carbon steel cutting effect
Commission cutting process method thick stainless steel plate
- For lasers with power greater than 10,000 watts, refer to the laser cutting process parameter table and start debugging the cutting effect on stainless steel with varying thickness.
- After adjusting the drilling process parameters, ensure that the cutting efficiency and quality meet your needs.
- After adjusting the cutting and drilling process, perform cutting in small batches to check the consistency of the process and its effect.
Table of common problems and solutions for debugging stainless steel cutting with lasers over 10,000 watts
Thickness and surface | Problem | Solutions |
---|---|---|
6mm: without slag suspension 20mm: slag point |
Layered cut | 1. Reduce dam cutting speed |
2. Increase the dam cutting pressure | ||
3. Increase the nozzle size | ||
4. Improper cropping focus | ||
hanging slag | 1. Inadequate cutting speed | |
2. Increase cutting air pressure | ||
3. Reduce the negative focus | ||
Slow efficiency | 1. Dirty lens | |
2. Increase cutting air pressure | ||
40mm: small amount of slag hanging | Layered cut | 1. Reduce frequency |
2. Increase positive focus | ||
3. Increase cutting pressure | ||
Yellow cutting surface | 1. Reduce duty cycle | |
2. Increase positive focus | ||
3. Increase cutting air pressure |

10-70mm Stainless Steel Cutting Effect
Test method for cutting stability
To ensure equipment stability during mass production and maintain consistent product quality, stability testing must be performed prior to formal batch processing.

Test Method for 10,000 Watt Laser Cutting Stability
Test material | Stainless steel 6-10mm | Test Charts | Helical line |
---|---|---|---|
Testing time | 5-10min | Test gas | Nitrogen |
Test method | 1. Adjust the stainless steel cutting parameters to ensure that the cutting surface is free from slag and stratification | ||
2. Continuously cut at full power for 5-10 minutes to check whether the cutting surface is consistent; | |||
3. In case of increased slag suspension, blue light after cutting for a period of time, continuous cutting and other problems, it indicates that the cutting focus is displaced. It is necessary to check the cutting head lens (dirty lens, poor quality lens, thermal lens problem) and focus position. |