What are the dangers when using multiple gases? What should I do in case of an emergency?
- Avoid having flammable and explosive materials near any cylinders.
- Stay away from open flames and do not work with gas at temperatures above 60 degrees Celsius. The use of gas from unapproved sources is strictly prohibited.
- The Dewar tank should not be tilted more than 45 degrees to avoid frostbite. Protective glasses and gloves must be worn during operation. Ventilation with high gas concentrations is strictly prohibited. If the Dewar tank falls to the ground, it must be raised within two minutes.
- Secure the cylinder using a bracket.
The main components of the laser cutting machine and their respective functions?
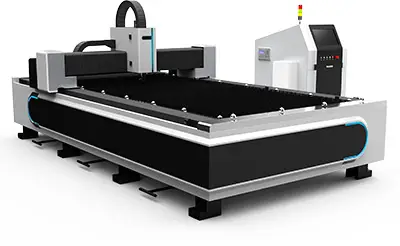
Laser source: Generates the laser beam.
Laser cutting machine: Used for computer numerical control (CNC) machining.
Chiller: Cooling system for the laser beam, reflective lens and cutting head.
Air Compressor: Provides air to the laser cutting machine and machining auxiliary gases.
Dryer: Filters water, oil and other contaminants from the air to maintain dry air conditions.
Dust collector: Removes dust and waste gases.
Regulator: Maintains a stable operating voltage for the device.
The meaning of the following code
G00: | Quick positioning | M00: | Unconditional suspension |
G01: | Linear interpolation | M36: | Turn off followers |
G02: | Clockwise circular interpolation | M31: | Choose the air |
G03: | Circular interpolation counterclockwise | M35: | Activate followers |
G04: | Break | M10: | Open mechanical shutter |
G10: | Empty stack | M30: | The program ends and returns to the program header |
G50: | Climb by | M11: | Turn off the mechanical shutter |
G09: | Read the program in advance | M06: | Turn off the electronic shutter |
G51: | Part rotation | M07: | Turn on the electronic shutter |
G71: | Metric programming | M14: | Turn off the auxiliary gas |
G91: | Incremental programming | ||
G90: | Absolute coordinates |
Why recalibrate when changing different cutting materials and different nozzle types? What should you do if the automatic calibration is not successful?
The height is monitored using a capacitive sensor, which is influenced by the material, the surface area in contact and the distance between the sensor and the material.
Different nozzles have varying contact areas, so changing nozzle types requires recalibration.
If automatic calibration fails, perform manual calibration by running the M70 command in manual data entry (MDI) mode or switch to manual calibration.
External light path and Z-axis coaxial adjustment method
The X-axis is adjusted by turning the upper and lower left and right adjustment screws on the laser bracket. The Y axis and Z axis are adjusted using three adjustment nuts on the lens mount.
Typically, coarse adjustments are made with a red light, followed by fine adjustments with a cross light fork, to ensure that the front and rear points are centered.
Method and precautions for finding focus
To prepare the flat board, place it on the end of the laser cutting machine at a 30 to 45 degree angle.
Then remove the nozzle and adjust the scale to -5. Set the drilling delay (P199) to 0 and move the cutting head to the highest point on the board.
Open the program to focus the laser, turn on the air manually and run the program. Find the place where the burn marks on the plate are thinnest and install the nozzle. Move the shaving head manually above this thinnest point.
Then unscrew the scale until the nozzle is 0.5 mm away from the surface of the board. Record the scale value at this point, which is known as the “zero focus scale.”
Precautions:
Before running the program, it is important to verify that the direction of movement of the focus adjustment in the program matches the orientation of the plate to avoid reverse collisions.
It is also essential to turn on the air manually before and after running the program to prevent smoke from affecting the lenses.
Once the program has finished, it is essential to avoid moving the Z axis until focus is reestablished and the plate is not bumped or shaken.
Write a coaxial program and tell the meaning of each sentence
% | Program header |
P900002 | Program name |
N1010 | Program annotation |
N1020M10 | Turn on the mechanical shutter |
N1030M21 | Select the laser pulse frequency |
N1040M15 | Select continuous wave mode |
N1040G4F30 | Pause 0.03 seconds |
N1050G111V100 | Laser power |
N1060U1 | Determine the power |
N1070M91 | Cancel laser aperture limit |
N1080M7 | Open electronic shutter |
N1090G4F10 | Pause 0.01 seconds |
N1100M6 | Electronic shutter |
N1110U0 | Cancel power setting |
N1120M11 | Turn off the mechanical shutter |
N1130M30 | The program ends and returns to the program header |
What are the factors that affect laser cutting?
1) Beam quality:
- Beam wavelength
- Power
- Energy
- Mode
- Beam angle
- State of polarization
- Beam position
- Stability
- Pulse width and peak power
- Repetition frequency
- Average output power
2) Process parameters:
- Speed
- Power
- air pressure
- cutting height
- Focus position
- Beak size and roundness
3) External light path:
- How good is the focusing mirror?
- Degree of contamination of circular polarizers and reflector
4) External conditions:
- Gas purity
- Sheet quality
What types of gases are needed for the laser to work? What is the purity of each? What is the minimum external pressure?
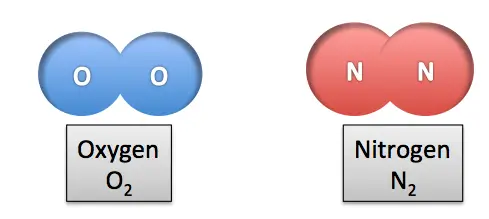
ROFIN: | High purity nitrogen 99.999% 5bar
Mixed gas (carbon dioxide, helium, nitrogen, carbon monoxide, oxygen, helium), designated supplier |
---|---|
RPC | High purity nitrogen 99.999% 5bar
High purity carbon dioxide 99.999% 5bar Pure nitrogen 99.995% 5bar |
T.K. | High purity nitrogen 99.999% 5bar
High purity carbon dioxide 99.999% 5bar Note: The gas blown by the TK laser is deflected by high purity nitrogen inside the laser. |
Precautions before running the program? And what should you pay attention to during processing?
Before starting the machining process, it is important to check that the selection procedure is correct, that the process parameters have been named correctly, that external auxiliary gas is available and that the plate position is correct.
To avoid deformations of the sheet during machining, which could result in collisions, it is essential to avoid any disturbances. When the machine is in operation, the operator must remain alert and not leave the machine, always ensuring personal safety.
What are the various types of lenses used in the machine?
Focusing mirror, circular polarizer, round reflecting mirror.
Stainless steel suspended slag, why can't it be cut and how to solve it?
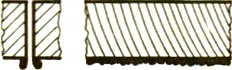
There are two types of slag that can appear on the lower surface of cut material:
- Hard slag: This can usually be resolved by lowering the focus or increasing the air pressure.
- Soft hanging slag: This can typically be resolved by increasing cutting speed, reducing power, and increasing focus position.
If the material isn't cutting, the solution is usually to slow down, increase the power, and adjust the focus position.
What is the relationship between the diameter of the cutting hole and the thickness of the plate? If it is out of range, what should be done ?
For Carbon Steel: The hole diameter should not be less than the plate thickness if less than 8 mm. If the hole diameter is more than 10 mm, it should not be less than 1.2 times the thickness of the plate.
For Stainless Steel: The hole diameter should not be less than the plate thickness if less than 4 mm. If the hole diameter is greater than 5 mm, it should not be less than 1.5 times the thickness of the plate.
If holes exceed these requirements, they can be drilled using marking positioning or slow pulse cutting techniques.
Sudden power outage during processing, how should we continue laser processing?
If the machine is turned off during the machining process, the following steps must be performed after restarting the machine:
- Return the machine to the reference point to reestablish the machine coordinate system.
- Open the NC program that was running before turning off the power and check whether subroutine Q999997 (which calls the part coordinate system memory) was called. If not called, the part zero point can only be located manually.
- If subroutine Q999997 was called, select the part coordinate system using G54.
- Go to X0Y0 to find the part zero point using G00X0Y0.
- Check the values of parameters P8 (line number of the program being executed before turning off the power) and P12 (number of the last line of G00 quick positioning before turning off the power) in the loop parameter. Use FASTPLOT to check the program and verify that the program number is correct.
- Modify the NC program by adding an unconditional pause (M00) after the G09 command (read-ahead, pre-stage function) and increasing the skip command (GO**** with value for memory P12). After the G00 memory command line in P12, add the layer cutting process subroutine such as Q990051 (first layer cutting parameter call).
- Run the program, turn on the auxiliary function and laser power and resume cutting with automatic positioning.
What are the specific reasons for contamination of focusing lenses?
Air or auxiliary gases such as oxygen and nitrogen are not pure and contain contaminants such as moisture, particles, soot and oil.
The external light path is also not clean and can become contaminated with slag during the cutting and drilling processes.
What materials cannot be processed with a laser?
Gold, silver, copper, pure aluminum, hard alloy steel, marble, cast iron, glass, etc.
How many drilling methods are there? Under what circumstances is each method used? What is the cause of burst holes when using common ionic drilling method ? How to deal with this?
There are three drilling methods:
- Conventional drilling
- Progressive drilling
- blast hole
Typically, conventional drilling is used on carbon steel plates that are 10 mm or less thick, while progressive drilling is used on carbon steel plates that are 10 mm or more thick. The use of breakout holes is not common.
Note that aluminum alloys should not be drilled using progressive drilling, but rather at the focal point.
Reasons for using a blowout hole include:
- Insufficient drilling time
- Excessive drilling pressure
- High drilling focus.
What are the reasons for inconsistent cutting end faces?
- Coaxial misalignment
- Incorrect light path
- No beak
- Poor quality board
- Focusing on mirror pollution
- Initial cutting surface is not good
- Slight opening delay
What are the types and sizes of nozzles? How should nozzles be selected for different material thicknesses?
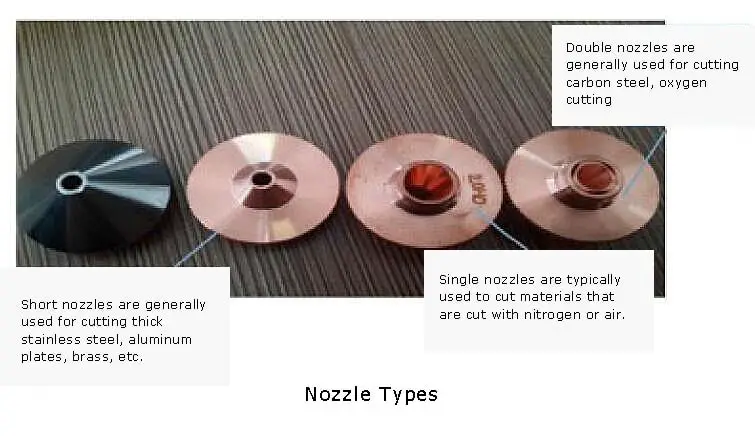
There are two types of nozzles: double-layer high nozzles and single-layer straight-bottom low nozzles. The double-ply high spouts come in sizes 1.4, 2, 2.5, and 3.0, while the single-ply, straight-bottom low spouts come in sizes 1.5, 2.0, 2.5, and 3. 0.
Typically, carbon steel uses double-layer high nozzles. For thicknesses of 8 mm or less, a 1.4 nozzle is used; for thicknesses between 10-12mm, a 2.0 nozzle is used; for thicknesses between 14-18 mm, a 2.5 nozzle is used; and for thicknesses between 20-25 mm, a 3.0 nozzle is used.
Stainless steel and aluminum alloys, on the other hand, generally use a single-ply, straight-bottom low nozzle.
Detailed processing parameters of 10mm-16mm carbon steel oxygen cutting and 8mm stainless steel nitrogen cutting
Type of laser generator | Sheet | Power | Speed | Focus | Nozzle diameter. | cutting height | Cutting Gas | air pressure | Lens |
mm | W | mm/min | mm | mm | mm | Pub | inch | ||
TK2000 | IN 10 | 1800 | 1000-1200 | 1 | two | 1.2 | O2 | 0.8~1.0 | 7.5 |
PRC4000 | MS 16 | 2450 | 800-1000 | two | 2.5 | 1.2 | O2 | 0.6~0.7 | 7.5 |
ROFIN DC030 | SUS 8 | 2950 | 800-1100 | -8 | 2.5 | 0.65 | O2 | 20 | 7.5 |
What are the advantages of the 21.5 and 7.5 inch lenses when cutting sheets?
5 inch lens:
This lens is ideal for cutting thin sheets as it offers fast cutting speed and high quality results.
7.5 inch lens:
This lens is suitable for cutting thick sheets due to its small taper and high-quality cutting results. It is also effective in protecting the lens from damage.
What is the difference between the far end and the near end of the optical path at focus, why does this difference exist? How to resolve the impact of your cut?
The focus at the distal end of the optical path is smaller compared to the focus at the proximal end due to the divergence angle of the laser light, which is not perfectly parallel.
To counteract the effect of different focus during the cutting process, the height of the operation panel can be adjusted by rotating the adjustment knob or adjusting the cutting speed override.
What should you pay attention to when cutting non-metal?
It is imperative to avoid cutting with oxygen and instead use nitrogen or air.
To avoid collisions and lens contamination, the distance between the nozzle and the material must be increased and a small gap must be maintained to prevent dust accumulation.
How to prevent the part from deforming and rotating during the cutting process? What are the causes of dimensional deviation of the cut part?
To avoid deformation and warping during cutting, techniques such as misaligned cutting, microconnection and displacement of the cutting point can be used.
If the size of the workpiece deviates too much due to displacement caused by deformation, it may result in a significant deviation from the desired size.
Why cut a small circle when cutting stainless steel over 4mm, or start with a slow cutting ?
It is important to ensure that the auxiliary airflow is directed downwards at the beginning of the cutting process to effectively prevent slag rollback.
What type of gas is used to cut carbon, what effect does the purity of the gas have on the cut?
Oxygen is commonly used as a cutting gas and its purity is typically 99.5% or higher.
Cut quality improves with greater oxygen purity.
What type of gas is used to cut stainless steel and what effect does the purity of the gas have on the cut?
Nitrogen is typically used as a cutting gas and its purity is generally 99.6% or higher. If the nitrogen purity is low, the cutting edge may appear yellow. On the other hand, if the nitrogen purity is high, the cutting edge will be brighter.
In addition, the use of high-purity nitrogen can also reduce the accumulation of slag at the bottom edge of the cut.
When cutting stainless steel with film, face up or down? Why do that? What should you pay attention to when cutting the film?
When the film is facing downwards, it makes it difficult to discharge the slag, which is why the film must be facing upwards.
When cutting with film, it is important to be careful that the film comes loose and traps the cutting head. A common solution is to first make a mark on the film and then proceed with the cutting process.
What should you pay attention to when installing FASTCAM?
Once the installation is complete, replace the incorrect configuration files PA8000.com and SETUP.DAT in the FASTCAM installation directory with the correct ones.
What are the requirements for the input line for stainless steel /carbon steel with different thicknesses?
For stainless steel with a thickness of 3 mm or less, straight handles can be used. When cutting stainless steel 4 mm or more thick, a combination of straight lines and small arcs is generally used.
For carbon steel, a circular arc is typically used.
What should be done if there is a sudden occurrence of a bad phenomenon during normal processing?
If an undesirable phenomenon occurs, it is important to first pause and then analyze the cause before taking appropriate action to resolve it.
What are the advantages and disadvantages of using bottled gas, Dewar tank and storage tanks?
Use bottled gas:
Although the pressure is well guaranteed, the high cost and short usage time require frequent gas changes.
Use Dewar tank:
With easy ventilation, long service life and low cost, Dewar tanks are suitable for long-term processing. (It is recommended to use high-pressure Dewar tanks, with a gasification gas volume generally not less than 80 cubic meters.)
Use storage tank:
Storage tanks offer significant gas savings and low cost with a long service life. Typically, liquid nitrogen is charged once every half month, making it a one-time investment. It is recommended for use when two machines are in operation and a large amount of nitrogen is required for processing auxiliary gas.
What are the programming steps in FASTCAM and FASTNEST?
The programming steps for FASTCAM are as follows:
- Import the DXF/DWG file and perform CAD cleaning and compression processing.
- Define the processing process and process settings, including tool compensation.
- Generate the program, specify the source, and perform program verification.
The programming steps for FASTNEST are as follows:
- Set the board size and modify machine parameters including file type and FASTPATH.
- Add the processed part pattern to the discharge table and set the number of parts.
- Click on automatic nesting and make fine adjustments, if necessary, through manual adjustment.
- Check the exit program simultaneously.
The meaning of “ LOST CUTTERHEAD NOZZLE ” the reason and solution for this alarm?
- The cutting head sensor nozzle loses alarm;
- Check that the nozzle is turned off;
- Whether the ceramic ring is intact;
- Whether the calibration is correct.
What does the EX CHANGE TABLE ALARM mean and how to resolve this alarm?
Check that the cutting head is raised to the highest point in case of failure on the changing bench.
What is the meaning and solution of AXIS Z MINUS LIMIT ALARM?
Z axis negative hardware limit failure detected. To solve this problem, press the emergency stop button, unscrew the hard limit switch cutting head and return to the zero position.
How to protect ceramic ring from damage?
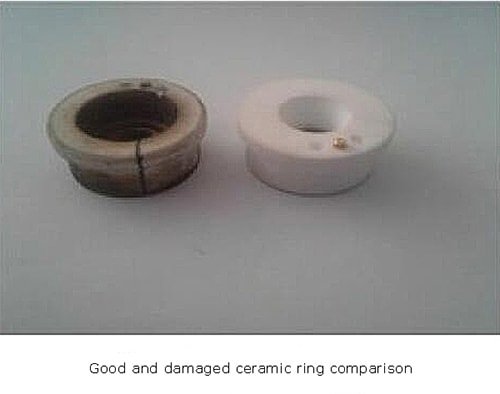
Make sure the ceramic cooling ring gas is working properly. The operator must not move away from the machine while it is in operation and must be alert to the sudden release of tension on the plate and the rotation of the part. If necessary, immediate measures must be taken after pausing the machine to avoid damage to the ceramic rings and cutting heads.
It is strictly prohibited to use high double-layer nozzles when cutting stainless steel or aluminum alloy with high pressure nitrogen.
What are the reasons for slag on the lower surface of the carbon steel sheet?
- Incorrect focus position
- Low air pressure
- Contaminants on the leaf surface (such as rust, oil and glue)