Concrete structures are protected by waterproofing to prevent them from coming into contact with or absorbing water. Water penetration can cause corrosion of the reinforcement.
There are two main types of waterproofing.
- type of application
- Weldable membranes
- Sealing Additives
Application Type Seals
Impregnation can also be applied by spraying.
However, they are usually applied with brushes. First, the area to be treated must be completely clean and free of all foreign substances. If there is damage or unevenness on the concrete surface, they must be leveled with a mixture of cement and sand.
Furthermore, the corners must be adjusted by attaching angled strips to avoid sharp edges. The seal must then be applied.
Typically, two coats are applied in vertical directions .
The thickness must be controlled taking into account the amount of waterproofing applied to the area.
Furthermore, the uniform thickness of the waterproofing membrane must be maintained.
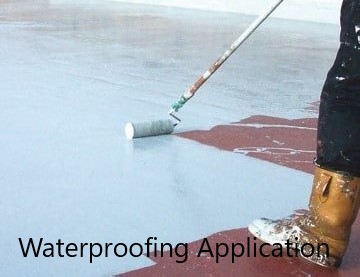
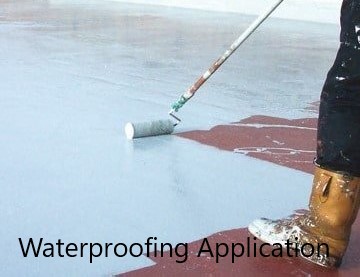
In general, sealants are cement compounds that are applied laterally with positive pressure.
Recent developments in this field have changed the types of materials used in construction.
Crystalline seals are seals that penetrate concrete and form a crystalline structure after reacting with the concrete. This type of material can also withstand negative pressure.
For example, if these types are installed inside an underground tank, it is not essential to seal from the outside to prevent water from entering the tank.
However, if it is necessary to prevent water from entering the wall, external waterproofing can be done in these projects.
Weldable Membrane Seal
Torchon membranes are applied to the outer surface of concrete to protect it from water penetration. The membrane is made of bituminous material that can be overlaid/bonded by heating.
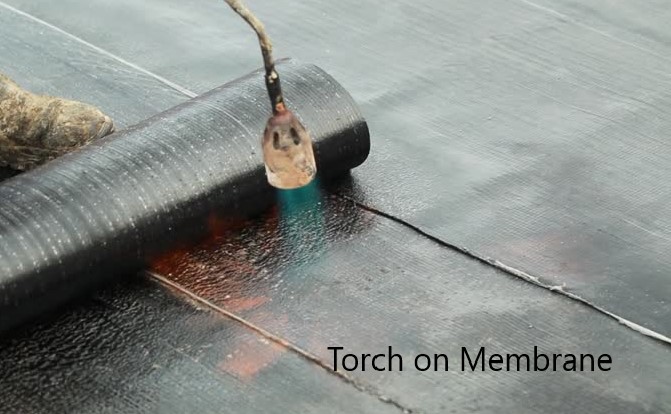
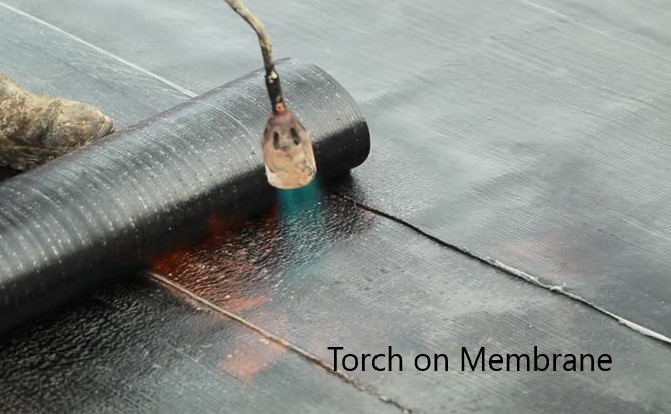
The application must comply with product specifications. Technically qualified people must be hired for this purpose. This type of seal is mainly used in civil construction of foundations and terraces.
Most waterproofing suppliers offer a 10-year waterproofing warranty . However, this is not enough compared to the service life of the structure.
For example, cement-based waterproofing is commonly used, which has a warranty period of 10 years. Do we have to renew/replace the seal every ten years?
This is a controversial topic in the construction industry. The best solution to these problems is to carry out the concreting perfectly and ensure that there are no water leaks before applying the waterproofing.
Pond tests are carried out to check for water leakage. It is recommended to perform a pond test before applying the membrane to ensure there are no panel leaks.
Once the waterproofing has been applied, there is no need to perform a pond test if water leaks are not identified prior to application. If water leaks are found before applying the membrane film, the pond test (after applying the waterproofing) must be carried out very carefully.
To do so, the project specification or corresponding documentation must be consulted.
Visual observations are generally made to check for water leaks where there is access.
However, if visual control is not possible, water levels are monitored and the drop in water height is checked. The water level is monitored, mainly in underground structures.
Additionally, as the reservoir expands, measurements need to be taken.
The article typical building sealing details provide other useful information that designers should consider.
Impregnation additives
Here we are discussing concrete additives that make it impossible for water to penetrate concrete.
The addition of additives reduces the porosity of concrete and also reduces permeability. This effect is caused by calcium hydroxide formed during the hydration process, which reacts with the additives.
Additives can be added to concrete at the concrete mixing plant or on site.
These chemicals react with the concrete and form a barrier that prevents water from moving through the concrete section. It's a kind of self-barrier because there is no external protection.
If cracks form during hydration or subsequently Factors affecting the durability of concrete can lead to water ingress. Such defects cannot be corrected with sealing additives.
Depending on the type of structure and the different parts of the structure, these materials can be used. For example, underground floors, floor beams, underground tanks, etc., where applying or burning the membrane is very difficult, protection with additives makes more sense.
However, unlike other waterproofing methods, there are more advantages .
- Legal construction costs.
- Less effort and fewer mistakes
- Easy to use
- The consistency of the mixture offers greater benefits
- In general, most waterproofing systems offer a warranty of around 10 years. However, as it is made of concrete, it lasts longer than the useful life of the structure.
- The normal properties of concrete are not affected by the use of additives.
- Reduces maintenance costs
Although these additives are new to the construction industry, their use is increasing rapidly as they offer more benefits compared to other materials.
Crystalline types can also be considered as additives or other types of applications. Let's see how this works.
Crystal clear sealing
Male, there are two types.
- Application type (external application)
- Fully crystal clear
The application method is conventional and can be done with a brush or by spraying.
Integral Crystalline adds the chemical as an additive as described above.
When added or applied to concrete, it reacts with the concrete to form a crystalline structure that is not soluble in water.
As shown in the figure above, crystals form in concrete when there is moisture.
This waterproofing can be used for underground structures: basement slabs, floor beams, basement walls, bridges, dams, water retention structures, marine structures.
The following advantages can be highlighted:
- The work required for complete sealing is almost zero because mixing occurs in the initial phase.
- This reduces costs.
- Easy to use
- Reduces the time required for sealing work.
- High resistance to water movement due to the formation of crystals in concrete
- As the porosity and permeability of concrete are reduced, durability is improved.
- Crystalline materials can seal cracks. They could even seal cracks with widths in the range of 0.4 to 0.5 mm.
- External factors have no influence on performance
- The application can be inside or outside the structure. Furthermore, it can withstand negative pressure .