1. Introducción
Debido a sus excelentes propiedades integrales y ventajas de costos, el acero 9Ni se usa ampliamente en diversas industrias como la aeroespacial, petrolera, química, construcción naval, ingeniería marina, energía eléctrica, metalurgia, maquinaria, energía nuclear y más.
Este post se centra en la construcción del proyecto del módulo de petróleo y gas ubicado bajo el sal. En este diseño, el acero 9Ni debe poseer no sólo alta resistencia y excelente tenacidad a bajas temperaturas, sino también resistencia SSC (fisuración por corrosión bajo tensión por sulfuro) en condiciones específicas de petróleo y gas. Por lo tanto, se encuentra en estudio el proceso de soldadura del sistema de tuberías de acero 9Ni.
2. Análisis de soldabilidad del acero 9Ni.
El acero 9Ni fue desarrollado por Inco en los Estados Unidos durante la década de 1940. Es un acero de aleación media que contiene un 9% de níquel, lo que le permite exhibir tenacidad a bajas temperaturas de hasta -196 ℃.
En comparación con el acero inoxidable austenítico y la aleación austenítica de hierro y níquel, el acero 9Ni tiene mayor resistencia y menor costo. Además, el acero 9Ni tiene mejores propiedades mecánicas integrales que la aleación de aluminio.
Sin embargo, el material es propenso a magnetizarse y es difícil desmagnetizar. Además, la tecnología de soldadura requiere el cumplimiento estricto de requisitos específicos.
Este artículo analizará la soldabilidad del acero 9Ni.
2.1 Grietas por frío
Es poco probable que se produzca agrietamiento en frío al soldar acero 9Ni con electrodos de níquel alto o medio. Sin embargo, cuando se utilizan electrodos con bajo contenido de níquel y alto contenido de manganeso en condiciones de soldadura inapropiadas, como baja potencia de línea y electrodos húmedos, se pueden producir grietas en frío. La generación de grietas en frío tiene tres aspectos:
2.1.1 Aparición de una capa endurecida en la zona de fusión. Aunque el contenido de carbono del acero 9Ni no es alto (≤ 0,10%), se puede producir una estructura endurecida si se selecciona un material de soldadura con un alto contenido de carbono. Esto se debe a un aumento en el contenido de carbono resultante de la fusión y la difusión.
2.1.2. Presencia de mucho hidrógeno, que se acumula en la capa endurecida debido a impurezas (como aceite y óxido) cerca de la ranura de soldadura.
2.1.3. La concentración de tensiones de uniones soldadas, que incluye tensión estructural, tensión térmica y tensión de restricción.
2.2. Grieta térmica
Al soldar acero 9Ni, pueden producirse grietas en caliente independientemente de si se utiliza un electrodo con alto contenido de níquel, medio níquel o bajo contenido de níquel y alto manganeso. Sin embargo, el uso de un tipo de electrodo con un alto contenido de níquel puede provocar grietas más graves.
Esto se debe al hecho de que la aleación contiene elementos como S y P, que pueden formar fácilmente eutécticos de bajo punto de fusión con níquel. Como resultado, puede ocurrir segregación intergranular. Además, elementos como C y Si también pueden promover la segregación de S y P.
En particular, cuando la estructura está en estado de austenita pura, la distribución de impurezas en el límite de grano puede ser continua.
2.3 Tenacidad reducida a bajas temperaturas
La reducción de la tenacidad a bajas temperaturas está influenciada principalmente por dos factores:
2.3.1 Influencia de los materiales de soldadura:
La composición química del metal de soldadura y de la zona de fusión está relacionada con los materiales de soldadura utilizados. Si los materiales de soldadura tienen un alto contenido de carbono, o si la correspondencia equivalente de Ni Cr de los materiales de soldadura y el metal base después de la fusión cae en el área que contiene martensita en el organigrama del acero inoxidable, se reducirá la tenacidad a baja temperatura.
2.3.2 Energía de la línea de soldadura y temperatura de la capa intermedia:
La energía de la línea de soldadura y la temperatura de la capa intermedia pueden cambiar el valor máximo y la temperatura del ciclo térmico de soldadura, afectando así la estructura metalográfica de la zona afectada por el calor. Si la temperatura máxima es demasiado alta, puede provocar una reducción de la austenita inversa y la formación de bainita gruesa, lo que puede dar lugar a una reducción de la tenacidad a bajas temperaturas.
2.4 Golpe magnético parcial
El soplado magnético parcial puede provocar una fusión deficiente de la soldadura y afectar significativamente la calidad de la soldadura.
El acero 9Ni tiene alta permeabilidad e intensidad de inducción de remanencia, lo que lo hace susceptible a golpes magnéticos parciales durante la soldadura.
Generalmente, cuando se utiliza el método DC (soldadura manual por arco DC, soldadura manual por arco DC de argón, etc.) para soldadura de soporte de tubería magnética, el soplado magnético parcial es común en la posición inicial de soldadura de soporte, pero normalmente no está presente durante la soldadura de tapa. llenado y soldadura.
3. Medidas preventivas para problemas de soldadura de acero 9Ni.
3.1 Prevenir la tendencia al agrietamiento en frío y en caliente
Las causas de las grietas por frío en la soldadura son la tensión, la estructura endurecida y el contenido de hidrógeno por difusión del metal de soldadura. La generación de grietas térmicas está relacionada con tensiones, impurezas y composición química. Por lo tanto, seleccionar los materiales de soldadura adecuados es fundamental.
Después de analizar las propiedades de diferentes materiales de soldadura, se descubrió que el material de soldadura nicrmo-3 es muy ventajoso para soldar acero 9Ni.
3.1.1 El coeficiente de expansión lineal de la aleación de níquel en el material de soldadura nicrmo-3 es similar al del acero 9Ni tanto a temperatura ambiente como a alta temperatura. Esta similitud ayuda a prevenir el estrés térmico causado por la expansión y contracción desiguales.
3.1.2 El contenido de Ni del material de soldadura nicrmo-3 es alto, oscilando entre el 55% y el 65%, y el contenido de carbono es similar al del acero 9Ni. Ambos materiales pertenecen al tipo bajo en carbono. Incluso con el efecto de dilución del metal base, todavía hay una estructura de austenita lo suficientemente alta como para evitar la formación de una correa de martensita dura y quebradiza en la línea de fusión.
3.1.3 El material de soldadura Nicrmo-3 tiene las siguientes características: bajo contenido de carbono (contenido de carbono ≤ 0,1%), un pequeño "rango de temperatura frágil" en el diagrama de fases de la aleación FC, alta pureza (S ≤ 0,03%, P ≤ 0,02%) y bajo contenido de hidrógeno. Por lo tanto, el uso del material de soldadura Nicrmo-3 puede proporcionar las condiciones básicas necesarias para reducir la tendencia al agrietamiento en frío y en caliente en las soldaduras de acero 9Ni.
Por lo tanto, bajo el estricto control del contenido de difusión de hidrógeno, la selección del material de soldadura nicrmo-3 puede evitar eficazmente la tendencia al agrietamiento en frío y en caliente al soldar acero 9Ni.
3.2 Garantía de tenacidad a bajas temperaturas de uniones soldadas
Las uniones soldadas constan de la soldadura, la línea de fusión y la zona afectada por el calor.
La tenacidad a baja temperatura de las uniones soldadas generalmente se produce en el metal de soldadura, la zona de fusión y la zona de grano grueso.
La tenacidad del metal soldado a bajas temperaturas depende principalmente del tipo de material de soldadura utilizado.
Al soldar acero 9Ni con materiales que tienen la misma composición que el acero 9Ni, la tenacidad del metal de soldadura a bajas temperaturas normalmente es baja, principalmente debido al alto contenido de oxígeno en el metal de soldadura.
Por lo tanto, los electrodos basados en Ni y Fe-Ni se emplean generalmente para soldar acero 9Ni.
Cuando el acero 9Ni se suelda con material de soldadura nicrmo-3, la composición química y la estructura metalográfica de cada área son diferentes.
El metal de soldadura es austenítico y tiene una excelente tenacidad a bajas temperaturas.
En la zona de fusión, el contenido de carbono del material de soldadura es esencialmente el mismo que el del acero 9Ni, con un contenido de Ni superior al 55%, lo que previene eficazmente la migración de carbono y evita una estructura quebradiza en la zona de fusión, asegurando así la baja emisión de carbono. Contenido de la zona de fusión. resistencia a la temperatura.
En la zona afectada por el calor, bajo el ciclo térmico de temperatura máxima superior a 1100 ℃, se generan estructuras gruesas de martensita y bainita, que revierten la reducción de la austenita y disminuyen la tenacidad a bajas temperaturas.
Por lo tanto, la alimentación de la línea debe controlarse tanto como sea posible y se debe utilizar soldadura de múltiples pasadas para minimizar el tiempo de permanencia a alta temperatura.
Por lo tanto, al soldar acero 9Ni con material de soldadura nicrmo-3, la tenacidad de la unión soldada a bajas temperaturas está influenciada en gran medida por la entrada de calor de soldadura y la velocidad de enfriamiento del proceso de cristalización del metal de soldadura.
3.3. Métodos para superar el soplado de polarización magnética
3.3.1. Cambie la posición del cable de tierra del metal base:
Para minimizar el bucle de corriente formado por la corriente en el metal base, el cable de tierra debe pasarse directamente al lado de la ranura o colocarse en la ranura. No debe estar conectado a una distancia larga con el metal base.
3.3.2. Cree temporalmente varios puntos de soldadura sobre la ranura (no en la raíz de la ranura) para cortocircuitar el campo magnético en ambos lados de la ranura. Al cebar en esta posición, utilice una amoladora para eliminar los puntos de soldadura.
4. Materiales y métodos de prueba.
4.1. Materiales de prueba
Acero 9Ni (355,6 mm de diámetro y 50,8 mm de espesor de pared) producido por Hengyang Valin Steel Pipe Co., Ltd.
Consulte la Tabla 1 para conocer la composición química y la Tabla 2 para conocer las propiedades mecánicas.
Tabla 1 Composición química del tubo de acero 9Ni (% en peso)
Tipo | W. | Sí | Minnesota | cr | Mes | Culo | No |
acero 9Ni | 0,05 | 0,21 | 0,57 | 0.045 | 0.056 | 0.035 | 9.24 |
Alabama | s | PAG | |||||
0,02 | 0.004 | 0.006 |
Tabla 2 propiedades mecánicas del tubo de acero 9Ni
Resistencia a la tracción Ri /MPa |
Fuerza de producción Rp0,2 /MPa |
Extensión A/% |
Energía impactante (-195 ℃) KV/J |
Relación de resistencia al rendimiento % |
750 | 698 | 27,5 | 108, 112, 107 | 93 |
4.2 Método de soldadura
Según los requisitos específicos del producto, la soldadura por arco de argón y tungsteno (GTAW) se utiliza para la soldadura de respaldo, mientras que la soldadura por arco manual (SMAW) se emplea para la soldadura de relleno y tapa. Además, durante el proceso de soldadura se utiliza material de soldadura nicrmo-3.
Consulte la Tabla 3 para conocer la composición química específica.
Tabla 3 Composición química de los materiales de soldadura (% en peso)
Tipo | W. | Sí | Minnesota | cr | Mes | Culo | No | Mes |
ERNiCrMo-3 | 0,01 | 0,04 | 0,03 | 0.004 | 0.004 | 22.2 | 64.3 | 9.3 |
ENiCrMo-3 | 0,02 | 0,36 | 0,4 | 0.005 | 0.006 | 22.7 | 63,6 | 8.8 |
5. Calificación del procedimiento de soldadura.
5.1 Preparación antes de soldar
5.1.1 El procesamiento de corte y ranurado de tubos de acero 9Ni debe utilizar preferentemente el método de procesamiento mecánico. Sin embargo, también se puede utilizar el corte con gas o el corte por plasma y la preparación de ranuras.
La ranura procesada o cortada debe pulirse.
5.1.2 Debido al gran espesor de pared de la tubería utilizada en esta evaluación, es necesario diseñar un tipo de canal adecuado.
Considerando la reducción del área de ranura y la deformación de la soldadura, mejorando la eficiencia de la soldadura y reduciendo el costo de consumo de materiales de soldadura a base de Ni, se decidió adoptar el tipo de ranura que se muestra en la Fig. 4mm y un borde romo de 0 2 mm.
5.1.3 Una vez completado el procesamiento de la ranura, se debe inspeccionar la apariencia para garantizar que no haya grietas ni delaminaciones. Si se encuentra alguno de estos defectos, deberá repararse.
5.1.4 Se deben utilizar métodos mecánicos y disolventes orgánicos para limpiar la superficie de la ranura y el área dentro de los 20 mm en ambos lados para eliminar aceite, óxido, virutas de metal, película de óxido y cualquier otra suciedad de la superficie.
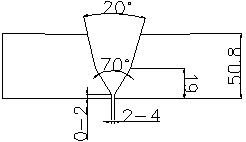
Fig. 1 detalles de la ranura
5.2 Secuencia de soldadura y disposición del cordón de soldadura
La capa de soporte se soldó mediante soldadura por arco de argón.
Para asegurar la formación del cordón de soldadura de raíz y evitar el fenómeno de quemado durante el llenado manual mediante soldadura por arco, se deben aplicar al menos dos capas de soldadura de soporte, con un espesor mínimo de soldadura de 6 mm, y rellenar mediante soldadura por arco manual.
Consulte la Figura 2 para ver la secuencia de disposición de las capas de soldadura.
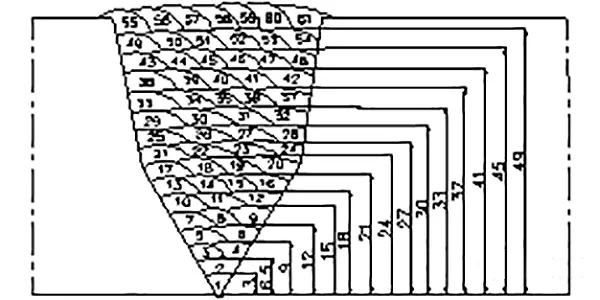
Fig. 2 Disposición del cordón de soldadura
5.3 Parámetros del proceso de soldadura
El aporte de calor se refiere a la cantidad de energía recibida por la soldadura por unidad de longitud y es el principal factor que influye en el ciclo térmico de la soldadura. Por lo tanto, controlar el aporte de calor es esencial para garantizar las propiedades mecánicas y la resistencia al agrietamiento por corrosión bajo tensión por sulfuro (SSC) durante las pruebas.
Consulte la Tabla 4 para conocer los parámetros de soldadura específicos.
Tabla 4 parámetros de soldadura
Cordón de soldadura No | Método de soldadura | Modelo de material de soldadura | Especificación (mm) | Corriente (A) | Voltaje (V) | Velocidad de soldadura (mm/min) |
1~2 | GTAW | ERNiCrMo-3 | 2.4 | 110~130 | 15~16 | 50~70 |
3~61 | SMAW | ENiCrMo-3 | 3.2 | 80~100 | 19~23 | 110~160 |
5.3.1: Debido a que el punto de fusión del metal de soldadura soldado con materiales de soldadura a base de níquel es aproximadamente 100 ℃ más bajo que el del acero 9Ni, puede causar fácilmente defectos como una fusión incompleta entre el borde de la ranura y el cordón de soldadura. Por lo tanto, está prohibido formar un arco al azar durante el proceso de soldadura y el arco no debe golpearse fuera de la ranura para evitar daños al metal base.
5.3.2: Durante la soldadura por arco, es importante llenar el cráter y permanecer en el arco por un tiempo para evitar que se agriete. En el caso de grietas en forma de cráter, es necesario un pulido inmediato.
5.3.3: Para garantizar la tenacidad a baja temperatura y los resultados de las pruebas SSC del acero 9Ni, el control del aporte de calor de soldadura es crucial y la corriente de soldadura no debe ser excesiva. Es aconsejable utilizar soldadura rápida de múltiples pasadas para minimizar el sobrecalentamiento del cordón de soldadura y refinar el grano mediante el efecto de recalentamiento de la soldadura de múltiples pasadas.
Durante la soldadura de múltiples pasadas, se debe regular la temperatura de la capa intermedia y se debe utilizar una pequeña entrada de calor para soldar. La entrada de calor debe controlarse por debajo de 20 KJ/cm. La temperatura entre capas de la soldadura multicapa debe mantenerse por debajo de 100 ℃ para evitar el sobrecalentamiento de la junta.
6. Resultados y análisis de las pruebas.
6.1 Ensayos no destructivos
Después de la soldadura, la pieza de prueba se sometió a una inspección visual, que no reveló cortes, poros superficiales, grietas, inclusiones de escoria u otros defectos ni en la soldadura ni en la zona afectada por el calor.
El refuerzo de soldadura midió entre 0,5 y 1,5 mm, y la soldadura y el metal base exhibieron una transición suave.
La inspección radiográfica no mostró grietas, fusión incompleta, penetración incompleta, inclusiones de escoria u otros defectos en la muestra, lo que confirma que la calidad de la unión soldada cumple con los requisitos de la norma.
6.2 Prueba de tracción
Durante una prueba de tracción, la muestra de tracción se sujeta a una máquina de prueba universal WE-100. Luego se aplica una tensión de tracción a la muestra, provocando un estiramiento axial hasta que alcanza su punto de rotura. Este es el principal indicador utilizado para medir la resistencia de los materiales.
Los resultados de la prueba se muestran en la Tabla 5.
Tabla 5 resultados de la prueba de tracción
Pieza de prueba no. | Resistencia a la tracción (MPA) | Ubicación de la fractura |
1 | 761 | metal común |
dos | 764 | metal común |
Según los resultados de la prueba, es evidente que la prueba de tracción cumple con los requisitos de la especificación.
6.3 Prueba de flexión
El ensayo de flexión evalúa la capacidad de los materiales para resistir la deformación.
Utilizando la máquina de prueba universal WE-100, se prueban muestras de flexión estándar procesadas.
Para realizar el ensayo se recogen cuatro muestras de flexión lateral según las especificaciones y se utiliza un penetrador de 63,5 mm de diámetro. El ángulo de flexión se establece en 180°.
Después de la prueba de flexión, no debe haber grietas ni defectos mayores a 3 mm en ninguna dirección en la superficie de las muestras.
Según los resultados de las pruebas, cumple con los requisitos de la especificación.
6.4 Prueba de impacto
El propósito de las pruebas de impacto es determinar el rendimiento de impacto de una junta soldada midiendo la cantidad de energía de impacto consumida por unidad de área en el punto donde se rompe la ranura en la superficie de la junta. Para realizar esta prueba, se coloca una muestra de impacto en una máquina de prueba de impacto JB-30B, que aplica la carga de impacto requerida para romper la ranura.
Para esta prueba de impacto específica, se utiliza un impacto Charpy a una temperatura de -196 ℃. Las muestras se toman desde una posición de aproximadamente 1 a 2 mm de distancia de la superficie de soldadura.
Las posiciones de las muescas están ubicadas en varios puntos a lo largo de la unión, incluido el centro de soldadura, la línea de fusión, la línea de fusión de 1 mm, la línea de fusión de 2 mm y la línea de fusión de 5 mm.
Los resultados de la prueba se muestran en la Tabla 6.
Tabla 6 resultados de la prueba de impacto
Ubicación de la muesca | Valor de impacto único (J) | Valor medio de impacto (J) |
centro de soldadura | 89, 78, 76 | 81 |
Línea de fusión | 80, 82, 76 | 79 |
Línea de fusión+1mm | 104, 91, 111 | 104 |
Línea de fusión+2mm | 78, 99, 85 | 87 |
Línea de fusión+5mm | 112, 98, 104 | 104 |
Según los resultados del impacto, se puede ver que los valores de impacto cumplen con los requisitos de especificación de (-196°C ≥ 41J).
6.5 Macro y prueba de dureza
Después de realizar una macroinspección de la sección de soldadura, se determinó que la soldadura está completamente soldada sin grietas ni otros defectos. La Figura 3 muestra la muestra macro.
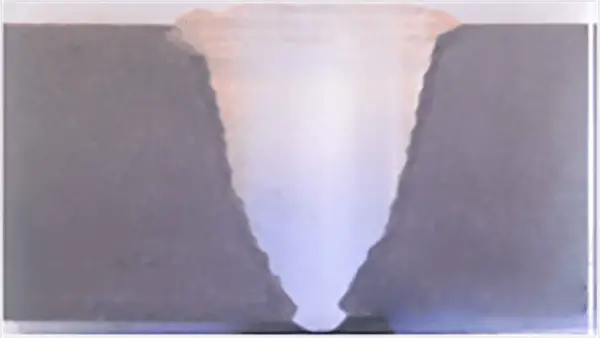
Fig. 3 fotografía de muestra macro
6.5.2 Medir la dureza del metal de soldadura, la zona afectada por el calor y el metal base de las uniones soldadas, respectivamente.
Los valores de dureza se muestran en la Tabla 7.
Tabla 7 resultados de la prueba de dureza
Posición de muestreo | Valor de dureza (HV10) |
metal de soldadura | 219~247 |
Zona afectada por el calor | 253~290 |
Metal base | 230~256 |
6.6. Prueba SSC (corrosión por tensión por sulfuro)
Se recogieron tres muestras estándar en forma de placa y se llenaron continuamente con una solución de 99,2 % de CO2 , 0,8 % de H2S y ácido acético (pH inicial = 3) a 25 ℃. Luego, las muestras se cargaron hasta un límite elástico del 80 % utilizando flexión de 4 puntos (σS = 698 MPa) y se remojaron durante 720 horas. Se observó que las muestras no se rompieron.
Al examinar las muestras con una lupa de 10x, no se detectaron grietas. Además, la prueba de fisuración por corrosión bajo tensión por sulfuro de este lote de muestras cumplió con los estándares especificados (ver Figura 4).
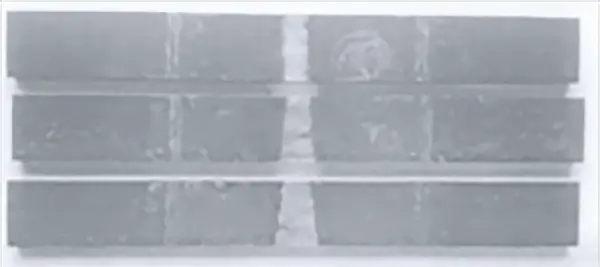
Fig. 4 Morfología de la superficie de la muestra de tensión de compresión después de la corrosión por inmersión.
7. Conclusión
7.1 Con el uso de soldadura por arco de argón y tungsteno para soporte, soldadura por arco manual para relleno y recubrimiento y soldadura de acero 9Ni con alambre de soldadura ERNiCrMo-3 y varilla de soldadura ERNiCrMo-3, se pueden lograr uniones de soldadura de alta calidad en condiciones apropiadas del proceso de soldadura. .
7.2 La prueba de calificación del procedimiento de soldadura cumplió con todos los índices de desempeño y requisitos técnicos. Hemos adquirido dominio en soporte TIG, llenado manual de soldadura por arco y tecnología de soldadura de sistemas de tuberías para acero 9Ni, lo que brindará una experiencia valiosa para guiar la producción futura.